Introduction to Circuit-Drilling
Circuit-drilling is a crucial process in the manufacturing of printed circuit boards (PCBs). It involves creating precise holes in the PCB substrate to allow for the insertion of components and the creation of electrical connections. The accuracy and quality of the drilling process directly impact the functionality and reliability of the final PCB.
In this comprehensive guide, we will delve into the various aspects of circuit-drilling, covering the techniques, equipment, and best practices involved in the process.
Types of Drilling Machines
There are several types of drilling machines used in the circuit-drilling process, each with its own advantages and applications. Let’s explore the most common ones:
CNC Drilling Machines
CNC (Computer Numerical Control) drilling machines are the most widely used in the PCB industry. These machines are highly automated and can precisely drill holes based on programmed instructions. They offer high speed, accuracy, and repeatability, making them suitable for high-volume production.
Laser Drilling Machines
Laser drilling machines use focused laser beams to create holes in the PCB substrate. They are particularly useful for drilling micro-vias and creating holes in multi-layer PCBs. Laser drilling offers high precision and the ability to drill holes with smaller diameters compared to traditional mechanical drilling.
Mechanical Drilling Machines
Mechanical drilling machines, also known as manual drilling machines, are operated by skilled technicians. These machines are typically used for low-volume production or prototyping purposes. While they offer flexibility, they require more time and manual intervention compared to automated drilling solutions.
Drilling Machine Type | Advantages | Applications |
---|---|---|
CNC Drilling | High speed, accuracy, and repeatability | High-volume production |
Laser Drilling | High precision, micro-via drilling | Multi-layer PCBs, micro-vias |
Mechanical Drilling | Flexibility, suitable for low-volume production | Prototyping, low-volume production |
Drill Bit Selection
Selecting the right drill bit is crucial for achieving optimal results in circuit-drilling. Drill bits come in various sizes, materials, and geometries to cater to different drilling requirements.
Drill Bit Sizes
The size of the drill bit determines the diameter of the holes drilled in the PCB. Common drill bit sizes range from 0.1 mm to 6.35 mm, with smaller sizes used for intricate designs and larger sizes for component mounting holes.
Drill Bit Materials
Drill bits are typically made from high-speed steel (HSS) or carbide. HSS drill bits are cost-effective and suitable for drilling through standard PCB materials. Carbide drill bits, on the other hand, offer higher durability and are used for drilling through harder materials or for extended production runs.
Drill Bit Geometries
The geometry of the drill bit affects the quality and accuracy of the drilled holes. Some common drill bit geometries include:
- Straight flute: Provides good hole quality and is suitable for most PCB materials.
- Spiral flute: Offers better chip evacuation and is ideal for drilling through thicker PCBs.
- Undercut: Reduces the risk of delamination and is used for drilling multi-layer PCBs.
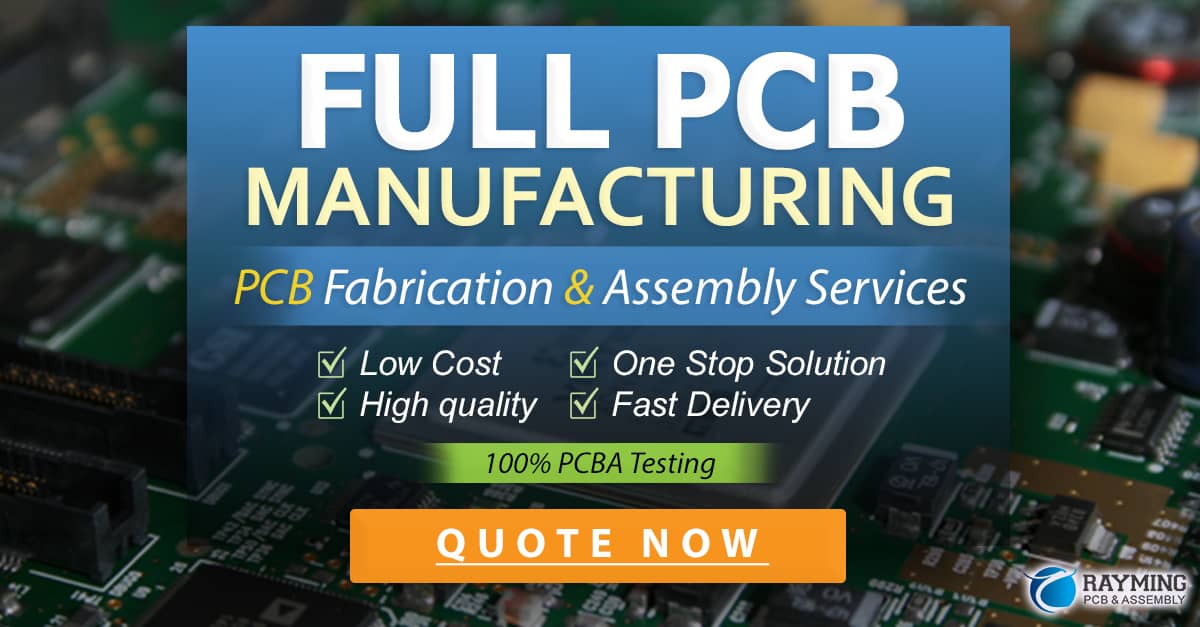
Drilling Parameters
To achieve optimal results in circuit-drilling, it is essential to set the appropriate drilling parameters. These parameters include:
Spindle Speed
The spindle speed refers to the rotational speed of the drill bit, measured in revolutions per minute (RPM). The optimal spindle speed depends on factors such as the drill bit size, material, and the PCB substrate. Higher spindle speeds are generally used for smaller drill bits and softer materials, while lower speeds are used for larger drill bits and harder materials.
Feed Rate
The feed rate represents the speed at which the drill bit advances into the PCB, typically measured in inches per minute (IPM) or millimeters per minute (mm/min). The feed rate should be adjusted based on the drill bit size, material, and the desired hole quality. A slower feed rate allows for cleaner and more precise holes, while a faster feed rate increases productivity but may compromise hole quality.
Peck Drilling
Peck drilling is a technique used to improve hole quality and reduce the risk of drill bit breakage. It involves drilling the hole in multiple steps, with the drill bit retracting and clearing the chips between each step. Peck drilling is particularly useful for drilling deep holes or through harder materials.
Parameter | Description | Factors to Consider |
---|---|---|
Spindle Speed | Rotational speed of the drill bit (RPM) | Drill bit size, material, PCB substrate |
Feed Rate | Speed at which the drill bit advances (IPM/mm/min) | Drill bit size, material, desired hole quality |
Peck Drilling | Drilling in multiple steps with chip clearing | Deep holes, harder materials |
Drilling Challenges and Solutions
During the circuit-drilling process, various challenges may arise that can affect the quality and reliability of the drilled holes. Let’s discuss some common challenges and their solutions:
Drill Wander
Drill wander occurs when the drill bit deviates from its intended path, resulting in misaligned or oversized holes. This can be caused by factors such as worn or damaged drill bits, improper drilling parameters, or machine vibrations.
Solutions:
– Regularly inspect and replace worn or damaged drill bits.
– Optimize drilling parameters, such as spindle speed and feed rate, based on the specific requirements.
– Ensure proper machine maintenance to minimize vibrations and improve stability.
Burrs and Rough Hole Edges
Burrs and rough hole edges can occur when the drill bit exits the PCB, causing raised edges or debris around the hole. This can lead to poor electrical connections and reliability issues.
Solutions:
– Use undercut drill bits to reduce the risk of burrs and delamination.
– Implement a controlled exit strategy, such as reducing the feed rate or using a backing material.
– Perform post-drilling deburring to remove any remaining burrs or rough edges.
Hole Misalignment
Hole misalignment refers to the deviation of drilled holes from their intended positions. This can be caused by factors such as machine calibration issues, material movement, or incorrect drilling data.
Solutions:
– Regularly calibrate the drilling machine to ensure accurate positioning.
– Use proper fixturing and clamping techniques to secure the PCB material during drilling.
– Verify the accuracy of drilling data and make necessary adjustments.
Best Practices for Circuit-Drilling
To optimize the circuit-drilling process and achieve the best results, consider the following best practices:
- Use high-quality drill bits suitable for the specific PCB material and hole requirements.
- Regularly inspect and maintain drilling machines to ensure optimal performance and accuracy.
- Implement proper handling and storage procedures for drill bits to extend their lifespan.
- Monitor and control the drilling environment, including temperature and humidity, to minimize material variations.
- Perform regular quality checks and measurements to identify and address any issues promptly.
Frequently Asked Questions (FAQ)
-
What is the difference between CNC drilling and laser drilling?
CNC drilling uses mechanical drill bits to create holes in the PCB, while laser drilling uses focused laser beams. CNC drilling is suitable for a wide range of hole sizes and is commonly used for high-volume production. Laser drilling, on the other hand, offers high precision and is ideal for drilling micro-vias and holes in multi-layer PCBs. -
How often should I replace my drill bits?
The frequency of drill bit replacement depends on various factors, such as the material being drilled, the drilling parameters, and the overall usage. It is recommended to regularly inspect drill bits for wear, damage, or breakage. Replace the drill bits when they show signs of excessive wear, reduced hole quality, or when they have reached the end of their recommended lifespan. -
What is the importance of hit count in circuit-drilling?
Hit count refers to the number of times a drill bit drills into the PCB material before being replaced. Monitoring the hit count is crucial for maintaining hole quality and preventing drill bit breakage. Each drill bit has a recommended hit count based on the material and hole size. Exceeding the recommended hit count can lead to reduced hole quality, increased wear, and potential drill bit failure. -
How can I minimize drill breakage during the drilling process?
To minimize drill breakage, consider the following tips: - Use drill bits with the appropriate size and geometry for the specific application.
- Ensure proper drill bit installation and alignment in the drilling machine.
- Optimize drilling parameters, such as spindle speed and feed rate, based on the material and hole size.
- Implement peck drilling for deeper holes or harder materials to reduce stress on the drill bit.
-
Regularly inspect and replace worn or damaged drill bits.
-
What are the common causes of hole misalignment, and how can I prevent it?
Hole misalignment can be caused by several factors, including machine calibration issues, material movement, or incorrect drilling data. To prevent hole misalignment: - Regularly calibrate the drilling machine to ensure accurate positioning.
- Use proper fixturing and clamping techniques to secure the PCB material during drilling.
- Verify the accuracy of drilling data and make necessary adjustments.
- Implement a robust quality control process to identify and address any misalignment issues promptly.
Conclusion
Circuit-drilling is a critical process in PCB manufacturing that directly impacts the quality and reliability of the final product. By understanding the various aspects of circuit-drilling, including drilling machines, drill bit selection, drilling parameters, and best practices, manufacturers can optimize the drilling process and achieve superior results.
This ultimate guide has provided a comprehensive overview of circuit-drilling, covering the essential concepts, techniques, and solutions to common challenges. By implementing the knowledge and best practices outlined in this guide, PCB Manufacturers can enhance their drilling processes, improve hole quality, and ultimately deliver high-quality PCBs to their customers.
0 Comments