Understanding PCB Surface Finishes
A PCB surface finish is a coating applied to the exposed copper traces and pads on a printed circuit board. Its primary purpose is to prevent oxidation and contamination of the copper, which can lead to poor solderability and reduced reliability. Additionally, surface finishes can improve the electrical conductivity, enhance the aesthetic appearance, and provide a suitable surface for component assembly.
Common PCB Surface Finishes
There are several PCB surface finishes available in the market, each with its unique properties and benefits. Some of the most commonly used surface finishes include:
- Hot Air Solder Leveling (HASL)
- Electroless Nickel Immersion Gold (ENIG)
- Immersion Silver (IAg)
- Immersion Tin (ISn)
- Organic Solderability Preservative (OSP)
Let’s take a closer look at each of these surface finishes:
1. Hot Air Solder Leveling (HASL)
HASL is one of the most widely used and cost-effective PCB surface finishes. In this process, the PCB is dipped into a molten solder bath, and then hot air is used to blow off the excess solder, leaving a thin layer of solder on the copper traces and pads. HASL provides excellent solderability and is compatible with a wide range of components.
Advantages:
– Cost-effective
– Good solderability
– Suitable for most applications
– Widely available
Disadvantages:
– Uneven surface due to solder buildup
– Limited flatness, which can affect fine-pitch components
– Not suitable for high-frequency applications
2. Electroless Nickel Immersion Gold (ENIG)
ENIG is a two-layer surface finish that consists of a thin layer of gold over a nickel barrier. The nickel layer provides a diffusion barrier, preventing the copper from migrating into the gold layer, while the gold layer offers excellent oxidation resistance and solderability. ENIG is suitable for high-reliability applications and is compatible with fine-pitch components.
Advantages:
– Excellent solderability
– Flat and uniform surface
– Suitable for fine-pitch components
– Good shelf life
– Suitable for high-frequency applications
Disadvantages:
– More expensive than HASL
– Potential for “black pad” defect due to improper process control
– Not suitable for press-fit connectors
3. Immersion Silver (IAg)
Immersion silver is a single-layer surface finish that involves depositing a thin layer of silver directly onto the copper surface. It offers good solderability, electrical conductivity, and a relatively low cost compared to ENIG. IAg is often used as a more economical alternative to ENIG.
Advantages:
– Good solderability
– Flat and uniform surface
– Suitable for fine-pitch components
– Lower cost than ENIG
Disadvantages:
– Limited shelf life due to silver tarnishing
– Not suitable for high-sulfur environments
– Potential for silver migration
4. Immersion Tin (ISn)
Immersion tin is another single-layer surface finish that involves depositing a thin layer of tin directly onto the copper surface. It provides good solderability and is often used as a lead-free alternative to HASL. ISn is compatible with most assembly processes and is relatively cost-effective.
Advantages:
– Good solderability
– Lead-free and RoHS compliant
– Suitable for most assembly processes
– Cost-effective
Disadvantages:
– Limited shelf life due to tin oxidation
– Potential for Tin Whiskers, which can cause short circuits
– Not suitable for high-temperature applications
5. Organic Solderability Preservative (OSP)
OSP is a organic compound that is applied to the copper surface to prevent oxidation. It is a thin, transparent layer that provides a solderable surface without adding significant thickness to the PCB. OSP is a cost-effective option and is suitable for applications with short storage times.
Advantages:
– Cost-effective
– Thin and uniform coating
– Suitable for fine-pitch components
– Environmentally friendly
Disadvantages:
– Limited shelf life
– Requires careful handling and storage
– Not suitable for multiple reflow cycles
Factors to Consider When Choosing a PCB Surface Finish
When selecting a surface finish for your PCB project, there are several factors to consider, including:
- Application requirements
- Component compatibility
- Shelf life and storage conditions
- Assembly processes
- Cost and availability
Application Requirements
The first factor to consider is the specific requirements of your application. Different surface finishes have varying properties that may be more suitable for certain applications. For example, if your PCB will be exposed to harsh environments or require high reliability, ENIG might be a better choice due to its excellent oxidation resistance and durability. On the other hand, if your application is cost-sensitive and has shorter storage times, OSP or HASL might be more appropriate.
Component Compatibility
Another important factor is the compatibility of the surface finish with the components used in your PCB. Some surface finishes are better suited for fine-pitch components, while others may not provide the necessary flatness or coplanarity. For instance, ENIG and immersion silver offer flat and uniform surfaces that are ideal for fine-pitch components, while HASL may not be suitable due to its uneven surface.
Shelf Life and Storage Conditions
The shelf life and storage conditions of your PCB should also be considered when choosing a surface finish. Some surface finishes, such as immersion silver and OSP, have limited shelf lives due to tarnishing or degradation over time. If your PCB needs to be stored for extended periods or exposed to harsh storage conditions, a surface finish with a longer shelf life, such as ENIG, might be a better choice.
Assembly Processes
The assembly processes used for your PCB can also influence the choice of surface finish. Some surface finishes are more compatible with certain assembly processes than others. For example, HASL is widely used and compatible with most assembly processes, while OSP may require more careful handling and is not suitable for multiple reflow cycles.
Cost and Availability
Finally, cost and availability are essential factors to consider when selecting a PCB surface finish. Some surface finishes, such as ENIG, are more expensive than others due to the materials and processes involved. Additionally, the availability of certain surface finishes may vary depending on the PCB Manufacturer and their capabilities. It’s important to balance the cost and availability with the performance and reliability requirements of your application.
PCB Surface Finish Comparison Table
To help summarize the characteristics, advantages, and disadvantages of each PCB surface finish, we’ve created a comparison table:
Surface Finish | Solderability | Flatness | Fine-Pitch Compatibility | Shelf Life | Cost |
---|---|---|---|---|---|
HASL | Good | Poor | Limited | Long | Low |
ENIG | Excellent | Excellent | Excellent | Long | High |
Immersion Silver | Good | Good | Good | Limited | Moderate |
Immersion Tin | Good | Good | Good | Limited | Moderate |
OSP | Good | Excellent | Excellent | Limited | Low |
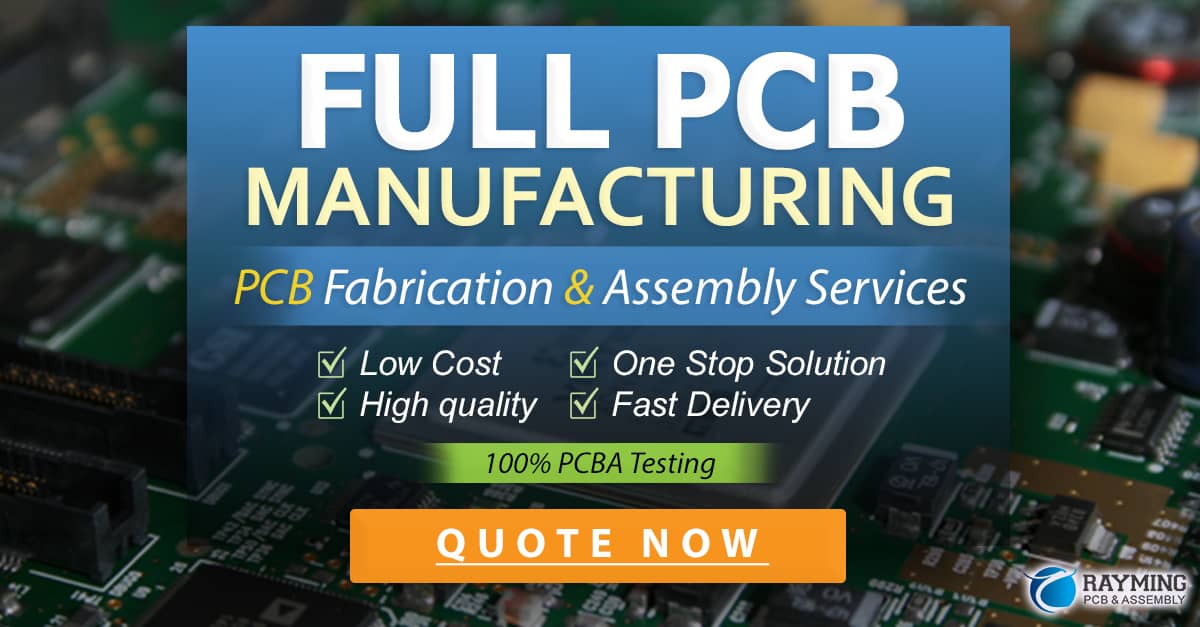
Frequently Asked Questions (FAQ)
-
Q: What is the most cost-effective PCB surface finish?
A: HASL and OSP are generally the most cost-effective PCB surface finishes, as they involve simpler processes and materials compared to other options like ENIG or immersion silver. -
Q: Which surface finish is best for high-reliability applications?
A: ENIG is often the preferred choice for high-reliability applications due to its excellent oxidation resistance, durability, and compatibility with fine-pitch components. -
Q: Can I use HASL for fine-pitch components?
A: While HASL is compatible with most components, it may not be suitable for fine-pitch components due to its uneven surface and limited flatness. ENIG, immersion silver, or OSP are better options for fine-pitch applications. -
Q: How long can I store PCBs with immersion silver or OSP surface finishes?
A: Immersion silver and OSP have limited shelf lives compared to other surface finishes. It’s recommended to use PCBs with these surface finishes within 6 to 12 months of manufacturing to ensure optimal solderability and performance. -
Q: Is ENIG a lead-free surface finish?
A: Yes, ENIG is a lead-free surface finish and is RoHS compliant, making it suitable for applications that require lead-free assembly processes.
Conclusion
Choosing the right surface finish for your PCB project is a critical decision that requires careful consideration of various factors, including application requirements, component compatibility, shelf life, assembly processes, and cost. By understanding the characteristics, advantages, and disadvantages of each surface finish option, you can make an informed decision that balances performance, reliability, and cost-effectiveness for your specific project.
Remember to work closely with your PCB manufacturer and assembly partners to ensure that the chosen surface finish is compatible with their processes and capabilities. With the right surface finish, your PCB will be well-protected against oxidation and contamination, ensuring optimal solderability, reliability, and longevity for your electronic device.
0 Comments