What is a Castellated PCB?
A castellated PCB, also known as a castellated circuit board or castellated hole PCB, is a type of printed circuit board (PCB) that features small, semi-circular cutouts or “castellations” along the edges of the board. These castellations serve as a unique method for connecting and mounting the PCB to other components or boards in an electronic device.
The term “castellated” derives from the resemblance of these cutouts to the architectural features of a castle’s battlements. The castellations are typically plated with a conductive material, such as copper, which allows for electrical connectivity between the PCB and other components when soldered together.
Advantages of Castellated PCBs
Castellated PCBs offer several advantages over traditional PCB designs:
- Simplified assembly process: Castellations allow for easy and precise alignment of the PCB with other components, reducing the complexity of the assembly process.
- Reduced board space: By utilizing castellations for connections, designers can minimize the amount of board space required for connectors or headers.
- Improved mechanical strength: The castellated edges provide additional mechanical support, making the PCB more resistant to vibration and physical stress.
- Enhanced signal integrity: Castellations can help maintain signal integrity by reducing the distance between connected components, minimizing signal loss and interference.
Applications of Castellated PCBs
Castellated PCBs find applications in various industries and products, including:
- Internet of Things (IoT) devices: Castellated PCBs are commonly used in IoT devices, such as sensors and wearables, where compact size and reliable connections are crucial.
- Modular electronics: Castellations enable the creation of modular electronic systems, allowing for easy swapping and upgrading of components.
- Automotive electronics: The enhanced mechanical strength and vibration resistance of castellated PCBs make them suitable for use in automotive electronic systems.
- Consumer electronics: Many consumer electronic devices, such as smartphones and tablets, utilize castellated PCBs to achieve slim designs and robust connections.
Designing a Castellated PCB
When designing a castellated PCB, several factors must be considered to ensure optimal performance and manufacturability.
PCB Material Selection
The choice of PCB material is crucial for the overall performance and reliability of the castellated PCB. Factors to consider when selecting the PCB material include:
- Dielectric constant: The dielectric constant of the material affects the impedance and signal propagation properties of the PCB.
- Thermal conductivity: Adequate thermal conductivity is necessary to dissipate heat generated by components on the PCB.
- Mechanical strength: The PCB material should provide sufficient mechanical strength to withstand the stresses associated with the castellated design.
Some common PCB materials used for castellated designs include FR-4, Rogers, and Isola.
Castellation Design Considerations
When designing the castellations on a PCB, several key aspects should be taken into account:
- Castellation size and spacing: The size and spacing of the castellations must be carefully designed to ensure proper alignment and soldering with mating components. Typical castellation sizes range from 0.5mm to 1.5mm in diameter, with a pitch (center-to-center distance) of 1.0mm to 2.54mm.
- Plating thickness: The castellations should have sufficient plating thickness to provide reliable electrical connections and withstand the soldering process. A minimum plating thickness of 25μm is generally recommended.
- Solder mask design: The solder mask should be designed to expose the castellations while protecting the rest of the PCB. Proper solder mask design helps prevent solder bridging and ensures reliable connections.
Layout and Routing Considerations
When laying out and routing a castellated PCB, designers should follow best practices to optimize signal integrity and manufacturability:
- Signal trace routing: Signal traces should be routed with controlled impedance and minimized length to reduce signal loss and reflections. The use of differential pairs and proper trace spacing can further enhance signal integrity.
- Ground plane design: A solid ground plane should be incorporated into the PCB design to provide a low-impedance return path for signals and reduce electromagnetic interference (EMI).
- Via placement: Vias should be strategically placed to minimize signal path length and provide efficient connections between layers. The use of microvias and Buried Vias can help optimize routing in dense designs.
- Component placement: Components should be placed to minimize the distance between connected castellations, reducing signal path length and improving overall performance.
Manufacturing Castellated PCBs
The manufacturing process for castellated PCBs involves several specialized steps to ensure accurate and reliable creation of the castellations.
PCB Fabrication Process
The fabrication process for a castellated PCB typically includes the following steps:
- Board layout and design: The PCB layout is designed using CAD software, incorporating the castellations and other necessary features.
- Material selection and lamination: The selected PCB material is cut and laminated to create the base board.
- Drilling and plating: Holes are drilled into the board, including the castellation locations, and then plated with a conductive material (usually copper) to create electrical connections.
- Patterning and etching: The desired circuit pattern is transferred onto the board using photoresist and then etched to remove unwanted copper.
- Solder mask application: A solder mask is applied to the board, exposing the castellations and protecting the rest of the circuitry.
- Surface finish application: A surface finish, such as ENIG (Electroless Nickel Immersion Gold) or HASL (Hot Air Solder Leveling), is applied to the exposed copper to prevent oxidation and enhance solderability.
Castellation Creation Methods
There are two primary methods for creating castellations on a PCB:
- Routing method: In this method, a specialized router is used to create the semi-circular cutouts along the edges of the PCB. This method is suitable for low-volume production and prototyping.
- Punch method: For high-volume production, a punch tool is used to create the castellations. This method is faster and more cost-effective than the routing method but requires a higher initial tooling investment.
Quality Control and Inspection
To ensure the quality and reliability of the manufactured castellated PCBs, several inspection and testing procedures are performed:
- Visual inspection: The PCBs are visually inspected for any defects, such as misaligned castellations, solder mask irregularities, or surface finish issues.
- Electrical testing: Continuity and isolation tests are conducted to verify the electrical integrity of the PCB and ensure proper connections between the castellations and the circuitry.
- Mechanical testing: The mechanical strength of the castellations is tested by subjecting the PCB to various stress tests, such as vibration and bend tests, to ensure the reliability of the connections under real-world conditions.
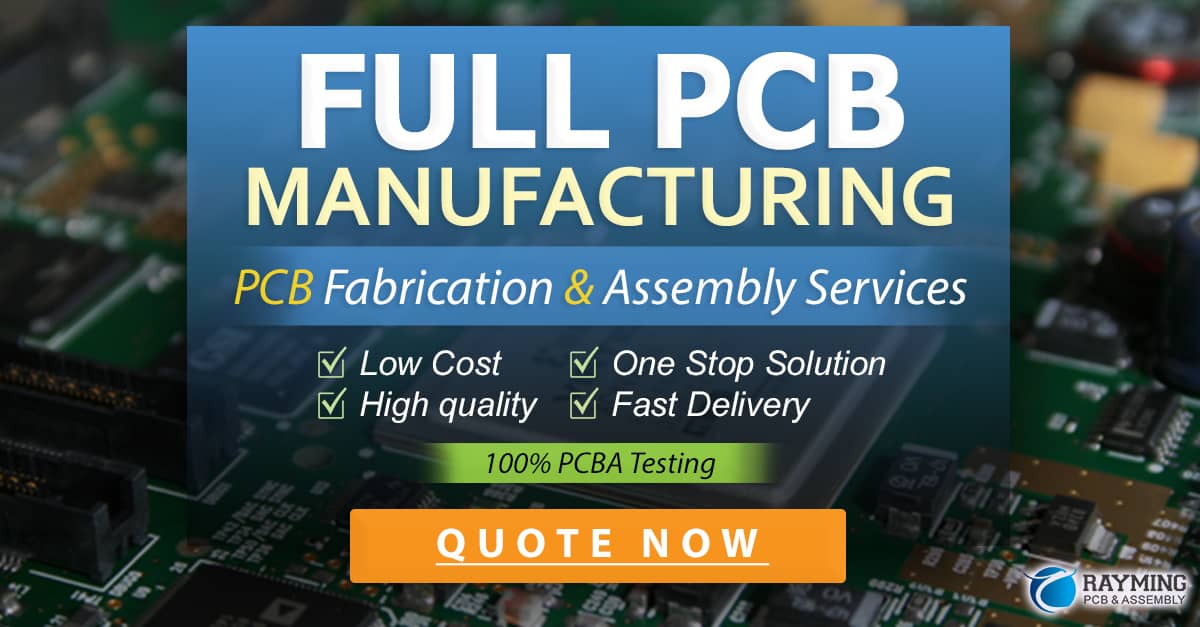
Assembling Castellated PCBs
The assembly process for castellated PCBs involves soldering the castellations to the corresponding components or boards.
Soldering Techniques
There are two primary soldering techniques used for assembling castellated PCBs:
- Reflow Soldering: In this method, Solder Paste is applied to the castellations, and the components are placed on top. The assembly is then heated in a reflow oven, melting the solder and creating the electrical and mechanical connections.
- Hand soldering: For low-volume assembly or rework, hand soldering can be used. A soldering iron is used to apply heat to the castellation and the component lead, melting the solder and creating the connection.
Design for Manufacturing (DFM) Considerations
To ensure a smooth and reliable assembly process, designers should follow DFM guidelines when creating castellated PCBs:
- Castellation size and pitch: The castellation size and pitch should be compatible with the mating components and the assembly process capabilities.
- Solder paste stencil design: The solder paste stencil should be designed to ensure the proper amount of solder is deposited on the castellations, avoiding insufficient or excessive solder.
- Component placement accuracy: The placement accuracy of the components on the castellations should be within the acceptable tolerance range to ensure proper alignment and soldering.
Advantages and Disadvantages of Castellated PCBs
While castellated PCBs offer several benefits, they also have some limitations that should be considered when deciding whether to use them in a design.
Advantages
- Compact size: Castellations allow for smaller PCB designs by eliminating the need for traditional connectors or headers.
- Improved signal integrity: The shorter signal paths enabled by castellations can enhance signal integrity and reduce noise and interference.
- Simplified assembly: Castellations provide a simple and reliable method for connecting PCBs to other components or boards, reducing assembly complexity.
- Enhanced mechanical strength: The castellated edges offer additional mechanical support, making the PCB more resistant to vibration and physical stress.
Disadvantages
- Limited connector options: Castellated PCBs may not be compatible with all types of connectors, limiting the design options available.
- Higher manufacturing costs: The specialized fabrication and assembly processes required for castellated PCBs can increase manufacturing costs compared to traditional PCB designs.
- Reduced repair and rework capabilities: Reworking or repairing a castellated PCB can be more challenging due to the small size and spacing of the castellations.
- Design complexity: Designing a castellated PCB requires careful consideration of various factors, such as castellation size, spacing, and alignment, which can add complexity to the design process.
Frequently Asked Questions (FAQ)
-
Q: What is the difference between a castellated PCB and a traditional PCB?
A: A castellated PCB features small, semi-circular cutouts (castellations) along the edges of the board, which serve as connection points for other components or boards. Traditional PCBs use connectors or headers for these connections. -
Q: What are the typical sizes and pitches for castellations on a PCB?
A: Typical castellation sizes range from 0.5mm to 1.5mm in diameter, with a pitch (center-to-center distance) of 1.0mm to 2.54mm. The specific size and pitch chosen depends on the design requirements and the mating components. -
Q: Can castellated PCBs be used with any type of connector?
A: No, castellated PCBs may not be compatible with all types of connectors. The castellation size, pitch, and layout must be designed to match the specific connector or component being used. -
Q: How does the manufacturing process differ for castellated PCBs compared to traditional PCBs?
A: The manufacturing process for castellated PCBs includes additional steps to create the castellations, such as routing or punching the semi-circular cutouts along the board edges. The plating, solder mask application, and surface finish processes must also account for the castellations. -
Q: Are castellated PCBs more expensive to manufacture than traditional PCBs?
A: Yes, castellated PCBs can be more expensive to manufacture compared to traditional PCBs due to the specialized fabrication and assembly processes required. However, the benefits of using castellations, such as reduced board space and improved signal integrity, can outweigh the increased costs in many applications.
Conclusion
Castellated PCBs offer a unique and advantageous solution for connecting and mounting PCBs in electronic devices. By featuring semi-circular cutouts along the board edges, castellations provide a compact, reliable, and mechanically robust method for creating electrical connections between components.
When designing and manufacturing castellated PCBs, careful consideration must be given to various factors, such as material selection, castellation size and spacing, layout and routing, and assembly processes. By following best practices and DFM guidelines, designers can create castellated PCBs that deliver optimal performance and reliability in a wide range of applications, from IoT devices to automotive electronics.
While castellated PCBs present some limitations and challenges, such as higher manufacturing costs and reduced repair capabilities, their benefits in terms of size reduction, signal integrity, and simplified assembly make them an attractive option for many electronic designs.
As technology continues to advance and the demand for compact, high-performance electronic devices grows, castellated PCBs will likely play an increasingly important role in the electronics industry, enabling the development of innovative and reliable products across various sectors.
0 Comments