Introduction to Trace Length Calculation in High Speed PCB Design
In high speed PCB design, calculating the trace length from the time delay value is a crucial step to ensure proper signal integrity and timing. As signal frequencies continue to increase, the importance of accurate trace length calculation becomes even more critical. This article will delve into the methods and considerations for calculating trace length based on time delay values in high speed PCB designs.
Understanding Time Delay in PCB Traces
Time delay, also known as propagation delay, is the amount of time it takes for a signal to travel from one point to another along a PCB trace. This delay is influenced by several factors, including the dielectric constant of the PCB material, the thickness of the dielectric layer, and the geometry of the trace itself. Understanding how these factors impact time delay is essential for accurate trace length calculation.
Dielectric Constant and Its Impact on Time Delay
The dielectric constant, also known as relative permittivity (εr), is a measure of a material’s ability to store electrical energy. In PCBs, the dielectric constant of the insulating material between the conductive layers directly affects the propagation velocity of signals. Materials with higher dielectric constants will result in slower signal propagation and longer time delays compared to materials with lower dielectric constants.
Common PCB dielectric materials and their typical dielectric constants:
Material | Dielectric Constant (εr) |
---|---|
FR-4 | 4.2 – 4.5 |
Rogers RO4003C | 3.38 |
Rogers RO4350B | 3.48 |
Isola IS410 | 3.96 |
Nelco N4000-13SI | 3.7 |
Dielectric Thickness and Its Impact on Time Delay
The thickness of the dielectric layer between the conductive layers in a PCB also plays a role in determining the time delay. A thicker dielectric layer will result in a longer time delay, as the signal has to travel a greater distance through the insulating material. This is an important consideration when designing Multilayer PCBs, as the dielectric thickness can vary between layers.
Calculating Trace Length from Time Delay
To calculate the trace length from a given time delay value, we need to understand the relationship between propagation velocity, time delay, and trace length. The propagation velocity of a signal in a PCB trace is determined by the dielectric constant of the material and the speed of light in a vacuum.
Propagation Velocity Formula
The propagation velocity (vp) of a signal in a PCB trace can be calculated using the following formula:
vp = c / √εr
Where:
– c is the speed of light in a vacuum (approximately 3 × 108 m/s)
– εr is the dielectric constant of the PCB material
Trace Length Calculation Formula
Once we have the propagation velocity, we can calculate the trace length (L) using the time delay (td) value:
L = vp × td
Where:
– L is the trace length in meters (m)
– vp is the propagation velocity in meters per second (m/s)
– td is the time delay in seconds (s)
Example Trace Length Calculation
Let’s consider an example to illustrate the trace length calculation process. Suppose we have a high speed PCB design using FR-4 material with a dielectric constant of 4.3, and we need to calculate the trace length for a signal with a time delay of 1 nanosecond (ns).
Step 1: Calculate the propagation velocity
vp = c / √εr
vp = (3 × 108 m/s) / √4.3
vp ≈ 1.44 × 108 m/s
Step 2: Calculate the trace length
L = vp × td
L = (1.44 × 108 m/s) × (1 × 10-9 s)
L = 0.144 m or 144 mm
In this example, the trace length required to achieve a time delay of 1 ns on an FR-4 PCB with a dielectric constant of 4.3 is approximately 144 mm.
Considerations for Accurate Trace Length Calculation
While the basic trace length calculation formula provides a starting point, several other factors must be considered to ensure accurate results in high speed PCB designs.
Frequency-Dependent Losses
As signal frequencies increase, the impact of frequency-dependent losses on trace length calculations becomes more significant. These losses, which include skin effect and dielectric losses, can cause the propagation velocity to vary with frequency. To account for these losses, designers may need to use more advanced simulation tools or employ mathematical models that consider the frequency-dependent behavior of the materials.
Impedance Matching
Proper impedance matching is crucial for maintaining signal integrity in high speed PCB designs. Trace lengths must be carefully controlled to ensure that the characteristic impedance of the trace matches the impedance of the source and load. Mismatched impedances can lead to reflections, signal distortions, and degraded performance.
To achieve proper impedance matching, designers must consider factors such as trace width, dielectric thickness, and the presence of ground planes. Specialized tools and calculators are available to help determine the appropriate trace geometries for a given target impedance.
Length Matching
In high speed digital systems, it is often necessary to match the lengths of traces carrying related signals to ensure proper timing and synchronization. This is particularly important for buses, differential pairs, and other groups of signals that must arrive at their destinations simultaneously.
Length matching can be achieved by adjusting trace routing, adding serpentine sections, or using delay lines. The trace length calculation techniques discussed earlier can be applied to ensure that the matched traces have the desired time delay and synchronization.
Simulation and Verification
While trace length calculations provide a valuable starting point, it is essential to simulate and verify the design using specialized tools to ensure accurate results. High speed PCB design software often includes integrated signal integrity and timing analysis tools that can help designers optimize trace lengths, impedance matching, and overall performance.
These tools can take into account the complex interactions between traces, vias, and other components, providing a more comprehensive view of the design’s behavior. Simulations can also help identify potential issues, such as crosstalk, reflections, and electromagnetic interference (EMI), allowing designers to make informed decisions and optimize the layout accordingly.
Frequently Asked Questions (FAQ)
-
What is the impact of dielectric constant on trace length calculations?
The dielectric constant of the PCB material directly affects the propagation velocity of signals and, consequently, the trace length required to achieve a given time delay. Materials with higher dielectric constants will result in slower signal propagation and longer trace lengths compared to materials with lower dielectric constants. -
How does dielectric thickness influence time delay in PCB traces?
The thickness of the dielectric layer between the conductive layers in a PCB impacts the time delay. A thicker dielectric layer will result in a longer time delay, as the signal has to travel a greater distance through the insulating material. This is an important consideration when designing multilayer PCBs, as the dielectric thickness can vary between layers. -
What are frequency-dependent losses, and how do they affect trace length calculations?
Frequency-dependent losses, such as skin effect and dielectric losses, can cause the propagation velocity to vary with frequency. As signal frequencies increase, the impact of these losses on trace length calculations becomes more significant. To account for these losses, designers may need to use advanced simulation tools or employ mathematical models that consider the frequency-dependent behavior of the materials. -
Why is impedance matching important in high speed PCB designs?
Proper impedance matching is crucial for maintaining signal integrity in high speed PCB designs. Trace lengths must be carefully controlled to ensure that the characteristic impedance of the trace matches the impedance of the source and load. Mismatched impedances can lead to reflections, signal distortions, and degraded performance. Designers must consider factors such as trace width, dielectric thickness, and the presence of ground planes to achieve proper impedance matching. -
How can designers verify the accuracy of trace length calculations?
While trace length calculations provide a valuable starting point, it is essential to simulate and verify the design using specialized tools to ensure accurate results. High speed PCB design software often includes integrated signal integrity and timing analysis tools that can help designers optimize trace lengths, impedance matching, and overall performance. These tools can take into account the complex interactions between traces, vias, and other components, providing a more comprehensive view of the design’s behavior and helping identify potential issues.
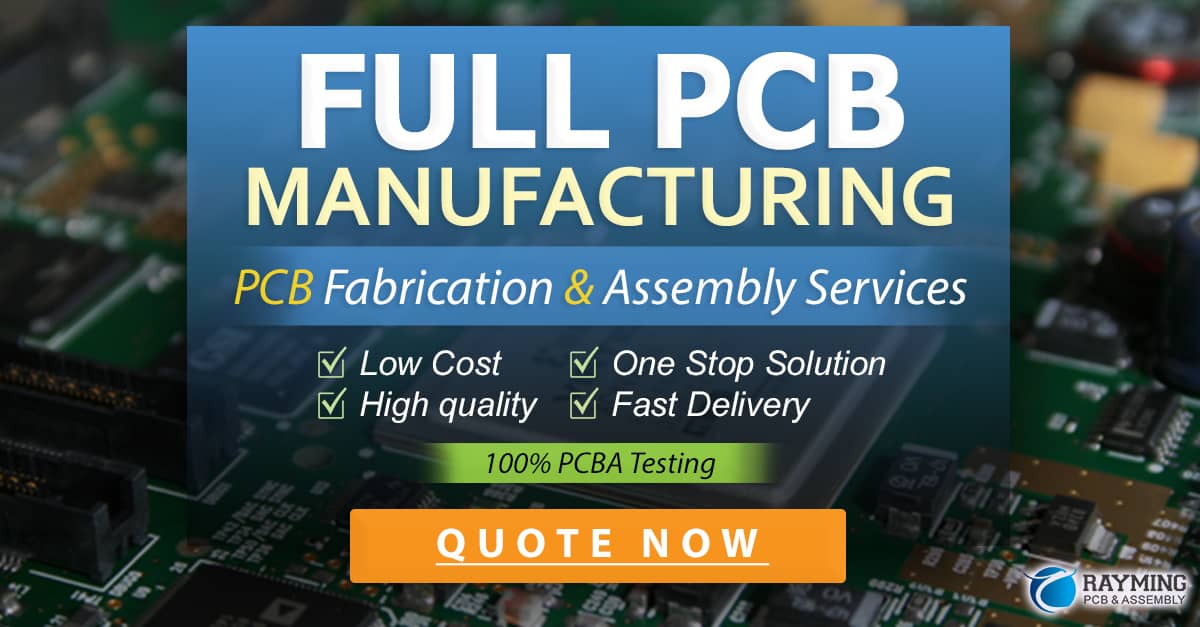
Conclusion
Calculating trace length from time delay values is a critical aspect of high speed PCB design. By understanding the relationship between propagation velocity, time delay, and trace length, designers can ensure proper signal integrity and timing in their designs. However, accurate trace length calculation requires considering various factors, such as dielectric constant, dielectric thickness, frequency-dependent losses, impedance matching, and length matching.
To achieve optimal results, designers should use specialized tools and simulations to verify their calculations and optimize the PCB layout. By following best practices and carefully considering the factors influencing trace length, designers can create high speed PCBs that deliver reliable, high-performance operation in demanding applications.
0 Comments