What is a Blind Via PCB?
A blind via is a type of interconnect used in printed circuit boards (PCBs) where the via starts on an outer layer and terminates on an inner layer, without going through the entire thickness of the board. Blind vias are commonly used in high-density interconnect (HDI) PCBs to increase routing density and reduce board size.
Blind Via vs. Buried Via vs. Through Via
There are three main types of vias used in PCBs:
Via Type | Description |
---|---|
Blind Via | Starts on an outer layer and terminates on an inner layer |
Buried Via | Starts and ends on inner layers, not visible on the surface |
Through Via | Goes through the entire thickness of the board, visible on both sides |
Blind vias offer several advantages over through vias, such as:
- Increased routing density
- Reduced board size
- Improved signal integrity
- Enhanced thermal management
Key Elements of Blind Via PCBs
1. Design Considerations
When designing a PCB with blind vias, several factors must be considered:
- Via size and pitch
- Aspect ratio (depth-to-diameter ratio)
- Pad size and shape
- Drill tolerance
- Copper plating thickness
- Dielectric material properties
These design parameters affect the manufacturability, reliability, and performance of the blind via PCB.
2. Manufacturing Process
The manufacturing process for blind via PCBs involves several steps:
- Drilling the blind vias using laser or mechanical drilling
- Electroless copper deposition to make the vias conductive
- Copper electroplating to increase the via wall thickness
- Lamination of additional layers
- Patterning and etching of the outer layers
- Solder mask application and surface finish
Each step must be carefully controlled to ensure the quality and reliability of the finished product.
3. Material Selection
The choice of materials for a blind via PCB is critical for its performance and reliability. The key materials include:
- Dielectric substrate (e.g., FR-4, polyimide, PTFE)
- Copper foil
- Solder mask
- Surface finish (e.g., ENIG, HASL, OSP)
The dielectric material must have good thermal stability, low dielectric constant and loss tangent, and good adhesion to copper. The copper foil thickness and type (electrodeposited or rolled annealed) affect the via formation and signal integrity.
4. Signal Integrity
Blind vias can improve signal integrity compared to through vias by:
- Reducing via stubs that cause reflections and impedance discontinuities
- Minimizing crosstalk between adjacent vias
- Shortening signal paths and reducing propagation delay
- Enabling better impedance control and matching
However, blind vias can also introduce challenges such as increased capacitance and inductance, which must be carefully managed through proper design and simulation.
5. Thermal Management
Blind vias can play a role in thermal management of PCBs by:
- Providing a thermal path for heat dissipation from components to inner layers or heatsinks
- Reducing thermal resistance compared to through vias
- Enabling more efficient use of board space for thermal vias
Thermal simulations should be performed to optimize the placement and size of thermal vias for effective heat transfer.
6. Reliability
The reliability of blind via PCBs depends on several factors:
- Via formation quality (e.g., plating uniformity, via wall roughness)
- Thermal cycling performance (e.g., via cracking, delamination)
- Mechanical stress (e.g., via crushing during lamination)
- Moisture resistance (e.g., via corrosion, CAF formation)
Accelerated life testing and failure analysis should be conducted to assess the reliability of blind via PCBs under various environmental conditions.
7. Cost Considerations
Blind via PCBs generally have higher manufacturing costs compared to standard Through-hole PCBs due to:
- Additional processing steps (e.g., laser drilling, electroplating)
- Higher material costs (e.g., high-performance dielectrics, thin copper foils)
- Tighter tolerances and quality control requirements
- Lower yield and longer cycle times
However, the overall system cost may be lower due to reduced board size, layer count, and improved performance. A cost-benefit analysis should be performed to determine the viability of using blind vias for a given application.
Frequently Asked Questions (FAQ)
1. What is the minimum blind via size that can be manufactured?
The minimum blind via size depends on the PCB manufacturer’s capabilities and the aspect ratio (depth-to-diameter ratio) of the via. Typically, the minimum diameter is around 0.1 mm (4 mils) for laser-drilled vias and 0.2 mm (8 mils) for mechanically drilled vias.
2. Can blind vias be used for high-current applications?
Yes, blind vias can be used for high-current applications by increasing the via diameter and plating thickness to reduce the current density and thermal resistance. However, thermal simulations should be performed to ensure adequate heat dissipation and avoid via failure.
3. How do blind vias affect the impedance of a transmission line?
Blind vias can affect the impedance of a transmission line by introducing capacitance and inductance discontinuities. The via geometry (diameter, pad size, pitch) and dielectric properties influence the via impedance. Proper design and simulation can help minimize the impact of blind vias on signal integrity.
4. What is the typical aspect ratio limit for blind vias?
The typical aspect ratio limit for blind vias is around 1:1 (depth-to-diameter ratio) for laser-drilled vias and 0.75:1 for mechanically drilled vias. Higher aspect ratios can be achieved with specialized processes such as plasma etching or direct metallization, but they may increase the manufacturing cost and complexity.
5. How do blind vias compare to microvias in terms of size and performance?
Microvias are a type of blind via with a diameter less than 0.15 mm (6 mils) and are typically laser-drilled. Microvias offer higher routing density and smaller pad size compared to standard blind vias, enabling finer pitch components and more compact designs. However, microvias may have lower current carrying capacity and higher manufacturing costs.
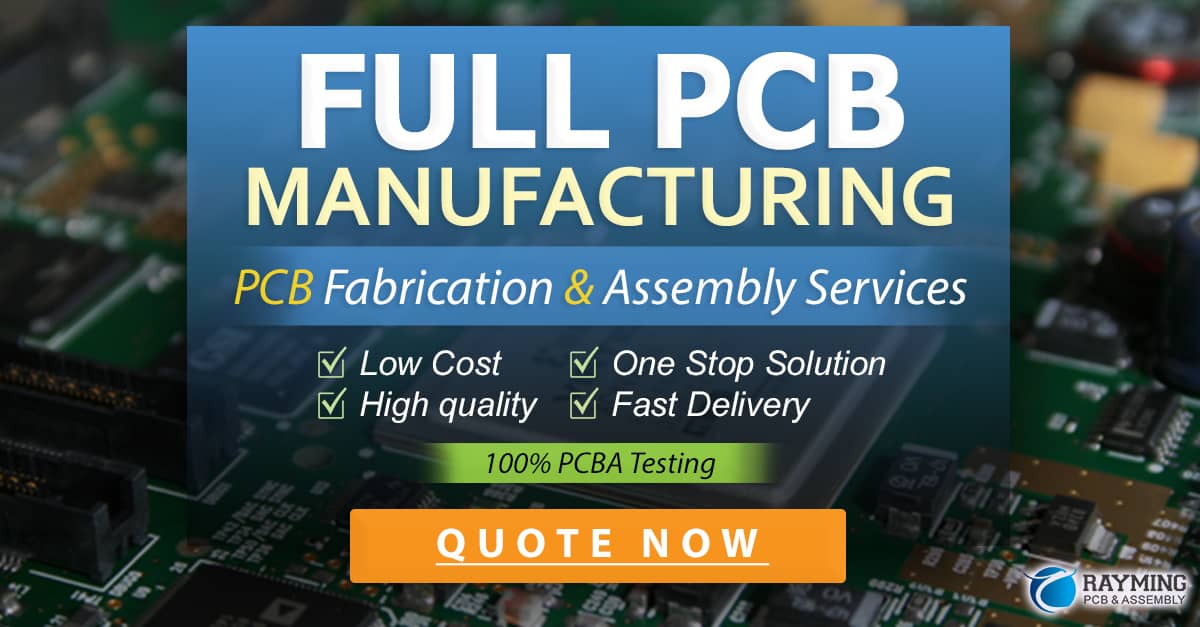
Conclusion
Blind via PCBs offer several advantages over standard through-hole PCBs, such as increased routing density, reduced board size, and improved signal integrity. However, designing and manufacturing blind via PCBs requires careful consideration of various factors such as via geometry, material selection, signal integrity, thermal management, reliability, and cost.
By understanding the key elements of blind via PCBs and following best design practices, engineers can leverage the benefits of this technology to create high-performance, reliable, and cost-effective electronic products. As the demand for miniaturization and functionality continues to grow, blind via PCBs will play an increasingly important role in the future of electronic packaging.
0 Comments