What is a Blank PCB Board?
A blank PCB (Printed Circuit Board) is a bare board without any components soldered onto it. It consists of a substrate material, typically FR4 (a composite material made of fiberglass and epoxy resin), with copper traces etched on one or both sides. These copper traces form the electrical connections between the various components that will be mounted on the board later in the manufacturing process.
Blank PCBs come in various sizes, thicknesses, and layer counts depending on the specific application requirements. They can be single-sided (copper on one side), double-sided (copper on both sides), or multi-layered (several layers of copper separated by insulating material).
Advantages of Using Blank PCBs
- Customization: Blank PCBs allow for complete customization of the circuit design based on the project’s specific needs.
- Cost-effective: Using blank PCBs can be more cost-effective than purchasing pre-designed boards, especially for large-scale productions.
- Flexibility: Designers have the flexibility to choose the size, shape, and layer count of the PCB based on their requirements.
- Prototyping: Blank PCBs are ideal for prototyping and testing new designs before mass production.
How are Blank PCBs Manufactured?
The manufacturing process of blank PCBs involves several steps:
- Designing: The PCB design is created using specialized software, such as Eagle, KiCad, or Altium Designer.
- Printing: The design is printed onto a transparent film or photomask.
- Copper Lamination: A thin layer of copper is laminated onto the substrate material using heat and pressure.
- Photoresist Application: A light-sensitive photoresist layer is applied to the copper surface.
- Exposure: The photomask is placed on top of the photoresist, and the board is exposed to UV light, hardening the exposed areas of the photoresist.
- Developing: The unexposed photoresist is removed using a chemical developer, leaving behind the desired copper trace pattern.
- Etching: The exposed copper is etched away using a chemical solution, typically ferric chloride or ammonium persulfate.
- Stripping: The remaining photoresist is stripped away, revealing the final copper traces.
- Drilling: Holes are drilled through the board for component leads and vias (connections between layers).
- Finishing: The PCB may undergo additional finishing processes, such as solder mask application, silkscreen printing, and surface finish (e.g., HASL, ENIG, or OSP).
What Materials are Used in Blank PCBs?
The most common materials used in blank PCBs are:
- FR4: A composite material made of fiberglass and epoxy resin, known for its excellent mechanical and electrical properties.
- Copper: Used for creating the conductive traces and pads on the PCB.
- Solder Mask: A protective layer applied to the PCB to prevent short circuits and provide insulation between copper traces.
- Silkscreen: A printed layer on the PCB that provides text, logos, and component outlines for easier assembly and identification.
Other materials, such as aluminum, ceramic, or polyimide, may be used for specific applications that require unique properties, such as high heat dissipation or flexibility.
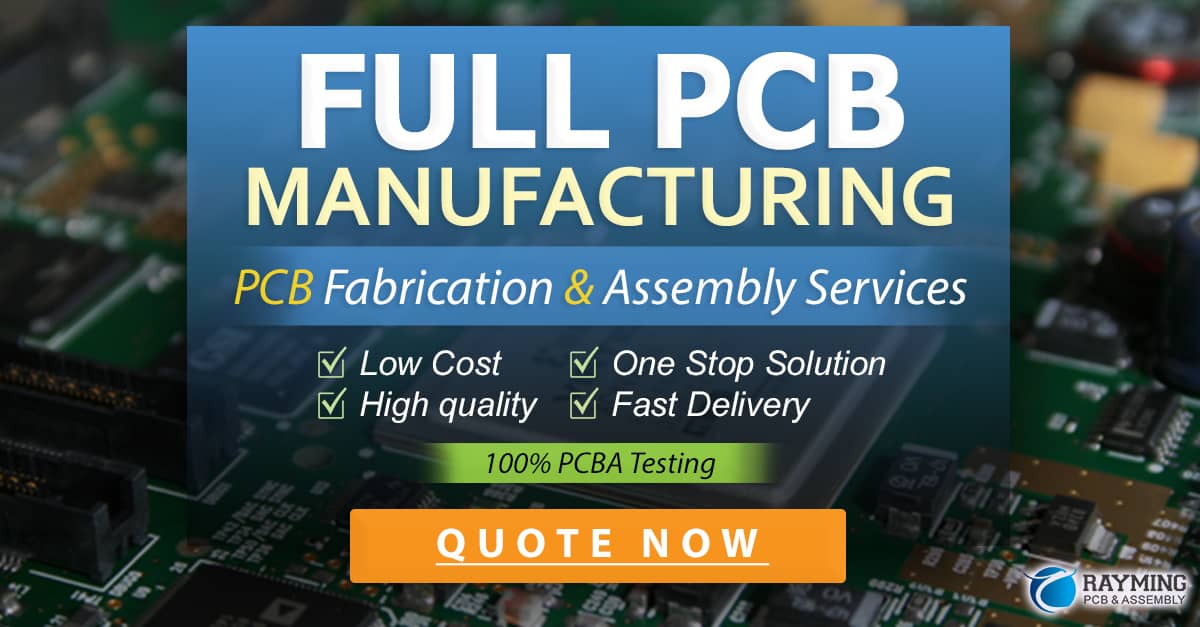
What are the Different Types of Blank PCBs?
Blank PCBs can be classified based on various criteria:
- Number of Layers:
- Single-sided: Copper traces on one side of the substrate.
- Double-sided: Copper traces on both sides of the substrate.
-
Multi-layer: Two or more copper layers separated by insulating material.
-
Rigid vs. Flexible:
- Rigid PCBs: Made using a solid substrate material, such as FR4.
-
Flexible PCBs: Made using a flexible substrate, such as polyimide, allowing the board to bend and conform to various shapes.
-
Substrate Material:
- FR4: The most common substrate material, offering good mechanical and electrical properties.
- Aluminum: Used for applications that require high heat dissipation.
- Ceramic: Used for high-frequency and high-temperature applications.
-
Polyimide: Used for flexible PCBs.
-
Special Features:
- High Density Interconnect (HDI): PCBs with finer traces and smaller vias for compact designs.
- Impedance Controlled: PCBs designed to maintain a specific impedance for high-speed signal integrity.
- Embedded Components: PCBs with components embedded within the substrate layers.
How to Choose the Right Blank PCB for Your Project?
Choosing the right blank PCB for your project involves considering several factors:
-
Application Requirements: Determine the specific requirements of your project, such as size constraints, environmental conditions, and electrical performance.
-
Layer Count: Select the appropriate number of layers based on the complexity of your design and the required connectivity between components.
-
Material Selection: Choose the substrate material based on the project’s requirements, such as temperature range, flexibility, and dielectric properties.
-
Manufacturing Capabilities: Consider the capabilities of your PCB manufacturer, including their minimum trace width and spacing, hole sizes, and available surface finishes.
-
Cost: Evaluate the cost of different blank PCB Options and balance it against your project’s budget and performance requirements.
-
Turnaround Time: Consider the lead time required for manufacturing and delivery of the blank PCBs, especially if your project has tight deadlines.
-
Reliability: Ensure that the selected blank PCB meets the reliability standards required for your application, such as IPC class 2 or class 3.
Comparison of Different Blank PCB Options
PCB Type | Advantages | Disadvantages |
---|---|---|
Single-sided | – Low cost – Simple designs |
– Limited component density – Limited routing options |
Double-sided | – Increased component density – Better signal integrity |
– Higher cost than single-sided – More complex manufacturing |
Multi-layer | – High component density – Excellent signal integrity |
– Higher cost – Complex manufacturing process |
Rigid | – Sturdy and durable – Good for high-density designs |
– Limited flexibility – Higher weight |
Flexible | – Conforms to various shapes – Lightweight |
– Higher cost than rigid PCBs – Limited component density |
FAQ
- What is the difference between a blank PCB and a printed circuit board assembly (PCBA)?
-
A blank PCB is a bare board without any components soldered onto it, while a PCBA is a completed board with all the necessary components mounted and soldered in place.
-
Can I design my own PCB using blank PCBs?
-
Yes, you can design your own PCB using blank PCBs. You will need to use PCB design software to create the schematic and layout, and then send the design files to a PCB manufacturer for fabrication.
-
What is the minimum trace width and spacing I can achieve with blank PCBs?
-
The minimum trace width and spacing depend on the capabilities of your PCB manufacturer. Typically, for standard PCBs, the minimum trace width and spacing range from 0.15mm to 0.20mm (6 to 8 mils). For HDI PCBs, the minimum trace width and spacing can be as low as 0.075mm (3 mils).
-
How long does it take to manufacture blank PCBs?
-
The manufacturing time for blank PCBs depends on the complexity of the design, the chosen materials, and the fabrication options. Standard lead times range from 1 to 3 weeks, but expedited services may be available for faster turnaround times.
-
Can I use blank PCBs for high-frequency applications?
- Yes, blank PCBs can be used for high-frequency applications. However, you need to choose the appropriate substrate material, such as Rogers or Teflon, which have better high-frequency performance than standard FR4. Additionally, the PCB design must be optimized for high-frequency signal integrity, considering factors such as impedance control and signal routing.
In conclusion, blank PCBs are an essential component in electronic product development, offering designers the flexibility to create custom circuit boards tailored to their specific project requirements. By understanding the manufacturing process, materials, types, and selection criteria for blank PCBs, you can make informed decisions when designing and manufacturing your electronic devices. With the right blank PCB choice and a well-executed design, you can ensure the optimal performance, reliability, and cost-effectiveness of your electronic products.
0 Comments