What is BGA Rework?
BGA (Ball Grid Array) rework refers to the process of removing and replacing BGA components from printed circuit boards (PCBs). BGA components are integrated circuits or chips that have an array of solder balls on the bottom for connection to the PCB, rather than pins. BGA rework is often necessary to replace defective components, upgrade chips, or modify circuit boards.
BGA rework requires specialized equipment and expertise due to the complex nature of removing and resoldering hundreds of tiny solder joints without damaging the PCB or surrounding components. The BGA component must be precisely aligned when resoldered to ensure proper connections. Careful temperature control is also critical to melt the solder balls without overheating the PCB or components.
Why Use a BGA Rework Company?
While it is possible to perform BGA rework in-house with the right equipment and training, many companies outsource this service to specialized BGA rework companies. There are several advantages to using a dedicated BGA rework service provider:
Expertise and Experience
BGA rework companies have extensive experience performing this intricate process on a daily basis across a wide range of PCB and component types. Their technicians are highly skilled in BGA removal and replacement techniques. An experienced BGA rework company will have a thorough understanding of the common challenges and pitfalls and know how to troubleshoot issues that arise.
Specialized Equipment
Proper BGA rework requires expensive specialized equipment such as rework stations with precision temperature control, x-ray inspection systems, and soldering tools. BGA rework companies invest in high-end, industrial grade equipment to handle any job. Most companies can’t justify the capital expense of purchasing this equipment and training staff on how to use it for occasional in-house BGA rework needs.
Quality and Reliability
BGA rework companies have quality control processes in place to ensure a consistent, reliable result. They will perform visual inspections and often x-ray analysis to verify that the solder joints are correctly formed with no shorts, opens, or other defects. Many are ISO certified and follow industry standards. Attempting BGA rework without the proper expertise significantly increases the risk of defects and damage to expensive PCBs and components.
Quick Turnaround Time
Outsourcing to a BGA rework company is often faster than attempting it in-house. They can usually offer quick turnaround times since they are dedicated to this service and have streamlined processes in place. The rework is performed in parallel to a company’s in-house operations so there is no disruption or lost productivity from staff performing the rework.
Cost Effective
For companies that only have occasional BGA rework needs, outsourcing to a specialized service provider is more cost effective than investing in the equipment, training, and labor to perform it in-house. The cost per board is typically very reasonable, especially considering the quality and speed of service.
BGA Rework Process
While the exact process may vary somewhat between BGA rework companies, the general steps are as follows:
-
PCB Preparation – The PCB is cleaned to remove any dirt or residue. For double-sided PCBs, the side opposite the BGA is masked to protect it during heating. The area around the BGA is also masked to prevent solder bridging to adjacent components.
-
BGA Removal – The existing BGA component is removed by heating to melt the solder joints. Typically a rework station with hot air nozzles is used to apply heat from above, while the underside of the PCB is supported by a preheater. Careful temperature control is critical – enough heat must be applied to melt the solder but not so much that the PCB or adjacent components are damaged. Once the solder reflows, the BGA is lifted off the PCB.
-
Site Redressing – After the old BGA is removed, the rework site is cleaned and prepared for the new component. Any residual solder is removed from the PCB pads, usually with a solder wick and flux. The pads are inspected for any damage or lifted pads. If the PCB is being reused with a new BGA, new solder paste is applied to the pads by stenciling or dispensing.
-
New BGA Placement – The new BGA component is carefully positioned on the PCB, aligning the solder balls with the PCB pads. Precise placement is critical for a good connection. Most rework systems have optical alignment features to assist with this. The component is held in place by tape or a holding fixture.
-
Reflow Soldering – The new BGA component is soldered to the PCB using a similar process as removal, by heating to reflow the solder paste. Again, precise temperature control is key to achieve good solder joints without damage. The solder is allowed to cool and solidify.
-
Inspection and Cleaning – After soldering, the reworked PCB is inspected visually and often by x-ray to verify joint integrity with no bridging, opens, or voids. Any residual flux is cleaned off. In some cases, other testing may be performed such as in-circuit tests or functional circuit tests.
Throughout the process, BGA rework companies take ESD (electrostatic discharge) precautions to protect sensitive components. The reworked PCBs are typically packaged for safe return shipping to the client.
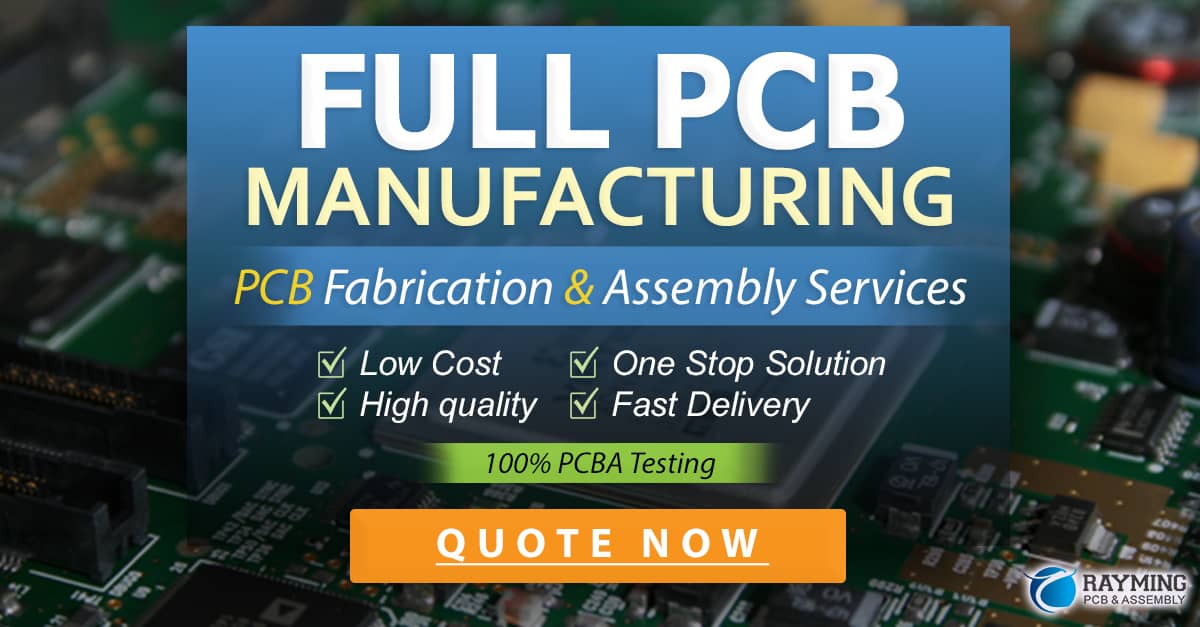
Choosing a BGA Rework Company
With many BGA rework service providers to choose from, how can you determine which company is the best fit for your needs? Here are some key factors to consider:
Industry Experience
Look for a company with extensive experience in BGA rework, ideally in your specific industry. Have they handled boards and components similar to yours? Do they have experience across of a range of PCB types (e.g. flex circuits, high density interconnect, chip-scale packages)?
Equipment and Capabilities
Verify that the company has modern, well-maintained equipment to handle your BGA rework needs. Some key equipment to ask about:
- Rework stations with precision temperature controls
- Vision systems and x-ray for placement and inspection
- Reballing equipment for installing new solder balls
- Stenciling systems for solder paste application
- Microscopes and other inspection aids
In addition to standard BGA rework capabilities, some companies offer additional services such as RoHS conversion, obsolete component sourcing, ball conversion (e.g. lead to lead-free), and reballing services which can be valuable for certain applications.
Quality Systems
Quality is paramount for BGA rework. The company should have well-documented quality processes and be able to discuss their quality standards and metrics with you. Industry certifications such as ISO reflect a commitment to quality. Ask about their rework yields, defect rates, and how they handle any quality issues that arise.
Technical Expertise
BGA rework requires a high level of technical skill. Look for a company whose technicians have solder certifications such IPC-7711/7721 and preferably specific BGA repair certifications. Assess their knowledge by discussing your technical requirements in detail. Do they ask insightful questions and provide helpful recommendations? A skilled BGA rework company can be a valuable technical partner.
Capacity and Turnaround Time
Make sure the provider has the capacity to handle your production volumes within your timeline requirements. Some companies specialize in quick turns for prototypes or small batches, while others are equipped for higher volume production. Look for a company that will give you a clear commitment on turnaround time.
Customer Service and Support
Evaluate the company’s communication and customer service during your initial interactions. Are they responsive and proactive in addressing your questions and requirements? Will they provide regular progress updates? Who will be your main point of contact? Good customer service can make a big difference in your overall experience.
Location and Logistics
Consider the company’s location and your logistics requirements. If you need fast turnaround, a local provider may be preferable to minimize shipping time. For higher volume production, you may want to consider providers in lower cost regions. Make sure the company has experience with your shipping and packaging requirements to ensure your boards will be protected in transit.
Cost
Of course, cost is a consideration in choosing a BGA rework partner. Get detailed quotes from multiple providers and make sure you understand what is included. However, don’t choose on cost alone. The lowest cost provider may not have the capabilities and quality you need. Look for the best overall value in terms of quality, reliability, service, and technical expertise for the price.
Benefits of BGA Rework
BGA rework provides several key benefits for PCB assembly and repair:
Cost Savings
BGA rework can save costs compared to scrapping boards with defective components. Expensive PCBs with complex circuitry can often be salvaged by replacing one or more BGAs at a fraction of the cost of a new board. This is especially valuable for costly boards such as motherboards, telecom boards, and advanced SOCs (systems-on-chip).
Improved Reliability
BGAs tend to be more reliable than other SMT packages due to their inherent design with many redundant solder joints. However, when issues do arise, BGA rework allows defective components to be replaced to restore reliable operation of the circuit board and end product. Skipping BGA rework and leaving a partially functional board in an assembly jeopardizes overall product quality and reliability.
Faster Time-to-Market
For new product introductions, BGA rework can significantly accelerate development and time-to-market by enabling changes to prototype boards without a full redesign and new board spin. Engineering changes can be implemented by simply replacing a BGA rather than waiting for updated bare boards. Faster prototypes mean faster testing, validation, and ultimately getting the product in customers’ hands sooner.
Extending Product Life
BGA rework can extend the life of older products by enabling upgrades to more advanced components and replacement of obsolete or discontinued parts. This is particularly important in industries with long product life cycles such as aerospace, defense, and medical equipment where systems may be in service for many years. With component obsolescence a frequent challenge, BGA rework provides a means to extend support and maintainability.
Environmental Benefits
Reworking boards rather than scrapping them reduces electronic waste. PCBs contain hazardous materials such as lead, cadmium, and brominated flame retardants which can contaminate soil and groundwater if not disposed of properly. Many components also contain valuable metals such as gold, silver, and palladium which are lost if boards are simply discarded. BGA rework allows these materials to be recovered and reused.
Common BGA Rework Applications
BGA rework is used across a wide range of industries and applications, such as:
-
Consumer Electronics – Reworking defects in products such as smartphones, tablets, laptops, gaming systems, and wearables. Performing engineering changes and upgrades to prototype boards.
-
Computer and Networking Equipment – Replacing defective ASICs, processors, FPGAs and other high-density BGAs in servers, routers, switches, and telecom equipment.
-
Automotive Electronics – Reworking engine control units, infotainment systems, sensors, and other electronic control modules.
-
Aerospace and Defense – Replacing obsolete BGAs in avionics, flight controls, radars, and other mil-aero electronic systems. Reworking high-reliability boards for space applications.
-
Medical Devices – Reworking BGAs in equipment such as patient monitors, imaging systems, and diagnostic instruments. Upgrading boards to extend the life of expensive medical systems.
-
Industrial Controls – Troubleshooting and repairing BGA-based circuit boards in PLCs, HMIs, motor drives, and other industrial control systems.
Risks and Challenges of BGA Rework
While BGA rework provides many benefits, it does pose some risks and challenges that must be carefully managed:
Thermal Stress
The heat applied during BGA removal and replacement can cause thermal stress on the PCB and components. Repeated thermal cycles, overheating, or improper cooling can result in damaged boards, lifted pads, and compromised solder joints. Following proper thermal profiles is critical.
Mechanical Stress
The force applied during BGA removal can cause mechanical stress. Improper technique or excessive force can result in pad lifting, board warpage, or trace damage, especially on thinner or more flexible circuit boards.
Solder Defects
Several types of solder defects can occur during BGA rework if the process is not well controlled. These include:
-
Bridging – Solder bridges form between adjacent balls causing an unintended short circuit. This is often due to too much solder, improper ball placement, or inadequate flux coverage.
-
Open Joints – A solder joint fails to form between the ball and PCB pad. Causes include poor wetting due to contamination or oxidation, insufficient Solder volume, or incomplete reflow.
-
Voids – Gaps or air pockets within the solder joint. Small voids are common and may be acceptable, but large voids weaken the joint and can lead to intermittent connections or fractures.
-
Head-in-Pillow – An open caused by the BGA ball and solder paste not combining properly. The ball rests on the paste but doesn’t collapse during reflow.
Proper process controls, solder paste selection, and inspection can mitigate these risks. However, some level of rework fallout is to be expected, especially on high-density boards.
Electrostatic Discharge (ESD) Damage
Many BGA components such as processors and FPGAs are highly sensitive to ESD. Improper handling can cause invisible ESD damage resulting in latent failures in the field. Robust ESD controls are essential for successful BGA rework.
Moisture Sensitivity
Many BGAs are moisture sensitive devices (MSD) prone to damage if exposed to ambient humidity. If not properly baked prior to reflow, moisture turns into steam and can cause interfacial fractures known as “popcorning”. Following proper MSD handling procedures including bake-out is critical.
While there are inherent risks with BGA rework, an experienced rework provider will have processes to mitigate these challenges. Choosing a company with a proven track record and asking about their controls around these issues can considerably reduce rework risks.
Future BGA Rework Trends
As electronics continue to evolve, BGA rework processes and equipment must advance to keep pace. Some key trends shaping the future of BGA rework include:
Smaller Pitches and Higher Densities
BGA components continue to shrink in size while increasing in I/O density. Pitches of 0.3mm and below are becoming more common. Smaller, more tightly spaced solder joints present placement and process control challenges for rework. Advanced rework equipment with finer placement accuracy and more precise heating will be required.
New Materials
New solder alloys, ball compositions, and underfill materials are being developed for enhanced reliability, RoHS compliance, and high-temperature applications. Rework processes must be adapted and requalified for these new materials.
Package-on-Package (PoP)
PoP and other multi-chip packages present unique rework challenges due to multiple layers of stacked components. Reworking an individual layer without damaging the entire stack requires skilled techniques and specialized heating profiles.
Increased Automation
Semi-automated and automated BGA rework systems are becoming more sophisticated, with features such as auto-alignment, profile optimization, and advanced vision systems. Automation can improve rework speed and consistency while reducing operator dependency. However, skilled technicians will still be needed to program and oversee these systems.
Environmental Trends
The trend toward lead-free electronics and restrictions on hazardous substances will continue to impact BGA rework. Lead-free solders require tighter process controls and have a higher melting point, making rework more challenging. New environmental regulations may restrict certain fluxes and cleaning agents commonly used in rework.
Staying abreast of these trends will be important for BGA rework companies to remain competitive in the future. Close collaboration between rework providers, equipment suppliers, and component manufacturers will be needed to develop new processes and best practices.
FAQ
Q: How much does BGA rework cost?
A: BGA rework costs can vary widely depending on factors such as the size and complexity of the board, the number and type of BGAs, and turnaround time. Typical prices can range from $100 to $200 per BGA for simple rework up to $1000 or more for large, complex boards. Many companies have a minimum charge of a few hundred dollars. It’s best to get detailed quotes from multiple providers based on your specific board.
Q: How long does BGA rework take?
A: Turnaround time depends on the complexity of the rework and the provider’s workload. Simple rework on a few BGAs can often be completed in 2-3 days. More complex rework can take a week or more. Rush services are available from some companies at an additional cost. Expect to add shipping time on top of the actual rework time.
Q: What are the most common BGA rework defects?
A: The most common defects are opens due to incomplete solder joints, shorts from solder bridging, and solder voids. Head-in-pillow defects and pad lifting also occur. Many of these can be prevented with proper process controls and are often caught in post-rework inspection. However, some level of fallout is to be expected with BGA rework.
Q: Can I rework BGAs myself?
A: While it is possible to rework BGAs yourself with the right equipment and training, it is very challenging to achieve professional results without significant experience. Proper BGA rework requires investing tens of thousands of dollars in equipment and extensive training
0 Comments