Introduction to BGA in PCB Assembly
Ball Grid Array (BGA) is a surface-mount packaging technology used for integrated circuits (ICs) in printed circuit board (PCB) assembly. BGA Packages have become increasingly popular due to their ability to provide high-density interconnections, improved electrical and thermal performance, and reduced package size compared to traditional through-hole and quad flat pack (QFP) packages.
In this article, we will explore the various types of BGA packages, their benefits in PCB assembly, and the inspection techniques used to ensure the quality and reliability of BGA-PCB assemblies.
Types of BGA Packages
There are several types of BGA packages used in PCB assembly, each with its own specific features and applications. Some of the most common types include:
Plastic BGA (PBGA)
PBGA packages are the most widely used type of BGA. They consist of a plastIC Substrate with a die attached to the top and solder balls on the bottom. PBGAs offer a cost-effective solution for high-density applications and are suitable for a wide range of devices, such as microprocessors, ASICs, and memory chips.
Ceramic BGA (CBGA)
CBGA packages use a ceramic substrate instead of plastic. They offer better thermal and electrical performance compared to PBGAs, making them suitable for high-power and high-frequency applications. However, CBGAs are more expensive and have a higher coefficient of thermal expansion (CTE) mismatch with the PCB, which can lead to reliability issues.
Tape BGA (TBGA)
TBGA packages use a flexible tape substrate, which is typically made of polyimide. They offer a thinner profile and better CTE match with the PCB compared to PBGAs and CBGAs. TBGAs are commonly used in mobile devices and other space-constrained applications.
Flip Chip BGA (FCBGA)
FCBGA packages eliminate the need for Wire Bonding by directly attaching the die to the substrate using solder bumps. This results in improved electrical performance, reduced package size, and better thermal dissipation. FCBGAs are used in high-performance applications, such as graphics processors and network switches.
Benefits of BGA in PCB Assembly
BGA packages offer several advantages over traditional through-hole and surface-mount packages in PCB assembly:
-
High-density interconnections: BGA packages allow for a large number of interconnections in a small footprint, enabling the design of compact and complex PCBs.
-
Improved electrical performance: The shorter lead lengths and lower inductance of BGA packages result in better signal integrity and reduced noise compared to other package types.
-
Enhanced thermal performance: BGA packages provide a low thermal resistance path between the die and the PCB, allowing for better heat dissipation and improved reliability.
-
Reduced package size: BGA packages enable the design of smaller and lighter PCBs, which is particularly important in mobile and portable devices.
-
Increased routing flexibility: The array configuration of BGA packages allows for more efficient routing of traces on the PCB, reducing the number of layers required and simplifying the design process.
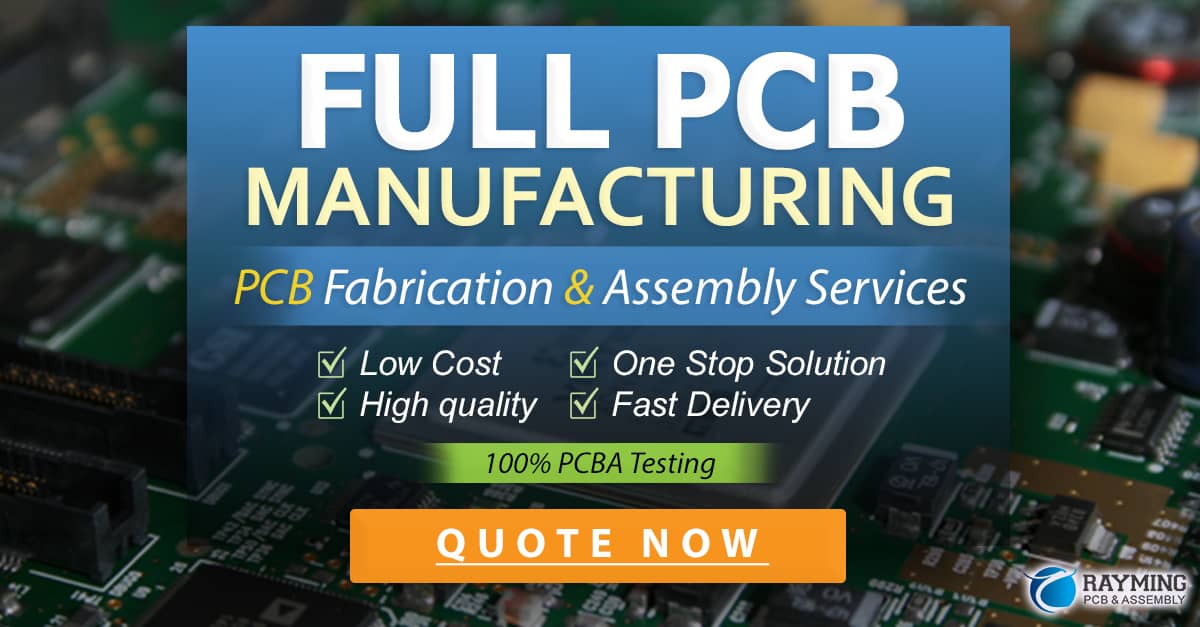
BGA Inspection Techniques
Ensuring the quality and reliability of BGA-PCB assemblies requires careful inspection at various stages of the manufacturing process. Some of the most common BGA inspection techniques include:
X-ray Inspection
X-ray inspection is a non-destructive technique that allows for the visualization of solder joints and other internal features of BGA packages. There are two main types of X-ray inspection:
-
2D X-ray: This technique provides a top-down view of the BGA package and can detect issues such as bridging, voids, and missing balls. However, it cannot provide information about the quality of the solder joints.
-
3D X-ray (CT): Computed tomography (CT) X-ray inspection provides a three-dimensional view of the BGA package, allowing for the detection of more subtle defects, such as partial cracks and head-in-pillow (HIP) defects.
Automated Optical Inspection (AOI)
AOI uses computer vision and image processing techniques to inspect the surface of the PCB and detect defects such as missing components, incorrect polarity, and solder bridging. While AOI cannot directly inspect the solder joints of BGA packages, it can detect issues with the placement and alignment of the package on the PCB.
Boundary Scan Testing (BST)
BST is a functional testing method that uses the JTAG (Joint Test Action Group) interface to test the interconnections between BGA packages and the PCB. BST can detect open and short circuits, as well as stuck-at faults, without requiring physical access to the solder joints.
Thermal Imaging
Thermal imaging can be used to detect hot spots and thermal anomalies in BGA-PCB assemblies, which may indicate issues with the solder joints or the thermal management of the system. This technique is particularly useful for identifying problems that may not be visible through other inspection methods.
Frequently Asked Questions (FAQ)
-
Q: What is the difference between BGA and QFP packages?
A: BGA packages have solder balls arranged in a grid pattern on the bottom of the package, while QFP packages have leads extending from all four sides. BGA packages offer higher density interconnections and better electrical and thermal performance compared to QFP packages. -
Q: Can BGA packages be reworked?
A: Yes, BGA packages can be reworked using specialized equipment and techniques. However, the rework process is more complex and time-consuming compared to other package types, and it may affect the reliability of the assembly if not performed properly. -
Q: What is the most common defect in BGA-PCB assemblies?
A: One of the most common defects in BGA-PCB assemblies is head-in-pillow (HIP), which occurs when the solder ball on the package and the solder paste on the PCB do not fully merge during the reflow process, resulting in an open or high-resistance connection. -
Q: How can BGA defects be prevented?
A: BGA defects can be prevented by ensuring proper design, material selection, and process control. This includes using appropriate solder paste and stencil thickness, optimizing the reflow profile, and maintaining good alignment between the package and the PCB during placement. -
Q: What is the role of underfill in BGA-PCB assemblies?
A: Underfill is an epoxy material that is applied between the BGA package and the PCB after the reflow process. It helps to distribute stress, improve thermal dissipation, and enhance the mechanical strength of the solder joints, thereby improving the reliability of the assembly.
Conclusion
BGA packages have become an essential part of modern PCB assembly, offering high-density interconnections, improved electrical and thermal performance, and reduced package size. Understanding the different types of BGA packages, their benefits, and the inspection techniques used to ensure quality and reliability is crucial for designers, manufacturers, and quality control professionals involved in BGA-PCB assembly.
By selecting the appropriate BGA package type, implementing robust design and process controls, and utilizing advanced inspection techniques, such as X-ray, AOI, BST, and thermal imaging, the electronics industry can continue to push the boundaries of PCB assembly and deliver innovative, high-performance products to meet the ever-increasing demands of the market.
0 Comments