Introduction to NPI Manufacturing
New Product Introduction (NPI) is a critical process for electronics contract manufacturers to launch new products efficiently and cost-effectively. NPI involves taking a new product design and ramping up production to full volume while ensuring quality, reliability, and manufacturability.
Effective NPI manufacturing practices are essential for electronics contract manufacturers to:
– Meet customer requirements and expectations
– Minimize time-to-market for new products
– Control costs and maximize profitability
– Establish scalable and repeatable manufacturing processes
– Ensure a smooth transition to volume production
This article will cover best practices and key considerations for NPI manufacturing, including design for manufacturability (DFM), prototyping, testing, supply chain management, and volume production ramp-up.
The NPI Manufacturing Process
The typical NPI manufacturing process for an electronics contract manufacturer involves the following key stages:
1. Design for Manufacturability (DFM) Review
- Evaluate the product design from a manufacturing perspective
- Identify potential issues that could impact production efficiency, quality, reliability or cost
- Provide feedback and recommendations to the customer for design improvements
- Ensure the design is optimized for the CM’s specific manufacturing capabilities and processes
2. Prototyping
- Build initial prototypes based on the product design
- Evaluate form, fit and function of the prototypes
- Identify any issues with the design, components, or assembly processes
- Provide feedback to the customer and implement any necessary design changes
3. Testing and Validation
- Perform thorough testing and validation of the prototype units
- Conduct functional testing, environmental testing, reliability testing, etc. as required
- Ensure the product meets all customer requirements and industry standards
- Identify any issues and implement corrective actions
4. Pre-Production and Pilot Runs
- Produce pre-production units using the final design and manufacturing processes
- Validate the manufacturing processes, equipment, and tools
- Train operators and technicians on the specific build processes
- Conduct pilot production runs to evaluate quality, efficiency, and capacity
5. Supply Chain Readiness
- Evaluate long-lead time and critical components
- Identify and qualify multiple sources for key components
- Place orders for components and ensure sufficient inventory for production ramp
- Establish supply chain risk management and business continuity plans
6. Volume Production Ramp-Up
- Transition from pilot production to volume manufacturing
- Continuously monitor and optimize processes for efficiency and quality
- Conduct ongoing reliability testing and quality assurance
- Manage the supply chain to ensure continuity of supply
- Implement corrective actions and process improvements as needed
Key Considerations for NPI Manufacturing
To ensure a successful NPI process, electronics contract manufacturers should focus on the following key areas:
Design for Manufacturability
Design for Manufacturability (DFM) is the practice of designing products with manufacturing in mind from the outset. Effective DFM can help to:
- Reduce manufacturing costs
- Improve production efficiency
- Minimize defects and quality issues
- Enhance product reliability
- Speed up time-to-market
Some key DFM considerations for PCB assemblies include:
Design Factor | DFM Considerations |
---|---|
Component selection | Use standard, readily available components when possible. Avoid obsolete or hard-to-find parts. |
Component placement | Ensure adequate spacing between components. Place components in a way that facilitates automated assembly. |
Soldering | Design for manufacturability with the selected soldering process (wave, reflow, etc). Ensure adequate pad sizes and clearances. |
Test points | Include test points for in-circuit testing and troubleshooting. Ensure test points are accessible. |
PCB Panelization | Design panels to maximize manufacturing efficiency and minimize waste. Consider depanelization methods. |
Supply Chain Management
Effective supply chain management is critical for NPI success. Electronics CMs need to:
- Select reliable suppliers who can provide high-quality components and materials
- Establish strong supplier relationships and effective communication channels
- Implement robust inventory management practices to ensure material availability
- Continuously monitor supplier performance and mitigate supply chain risks
- Develop alternative sources and business continuity plans to avoid disruptions
Some best practices for NPI supply chain management include:
- Early supplier involvement in the NPI process
- Thorough supplier qualification and auditing processes
- Automated inventory tracking and management systems
- Regular supplier performance reviews and scorecards
- Buffer stock and safety stock policies to mitigate supply risks
Testing and Quality Assurance
Thorough testing and quality assurance are essential to ensure that new products meet all requirements and perform reliably in the field. Electronics CMs should establish a comprehensive quality management system that includes:
- Incoming quality control (IQC) for components and materials
- In-process quality checks and statistical process control (SPC)
- Post-assembly testing, including in-circuit testing (ICT), functional testing, and burn-in
- Outgoing quality control (OQC) and final inspection
- Failure analysis and corrective action processes
Best practices for NPI testing and quality assurance include:
- Developing a detailed test plan based on customer requirements and industry standards
- Investing in automated test equipment and systems for efficiency and accuracy
- Conducting thorough first article inspections (FAI) and process capability studies
- Implementing traceability and serialization for effective quality control and root cause analysis
- Continuous improvement through data analysis and corrective actions
Communication and Collaboration
Effective communication and collaboration between the electronics CM and the customer are critical for NPI success. Some best practices include:
- Establishing clear roles, responsibilities, and expectations from the outset
- Having regular project status meetings and progress reports
- Using collaborative project management tools and secure data sharing platforms
- Involving key stakeholders from both sides in design reviews, testing, and problem-solving
- Maintaining open lines of communication and escalation paths to quickly resolve issues
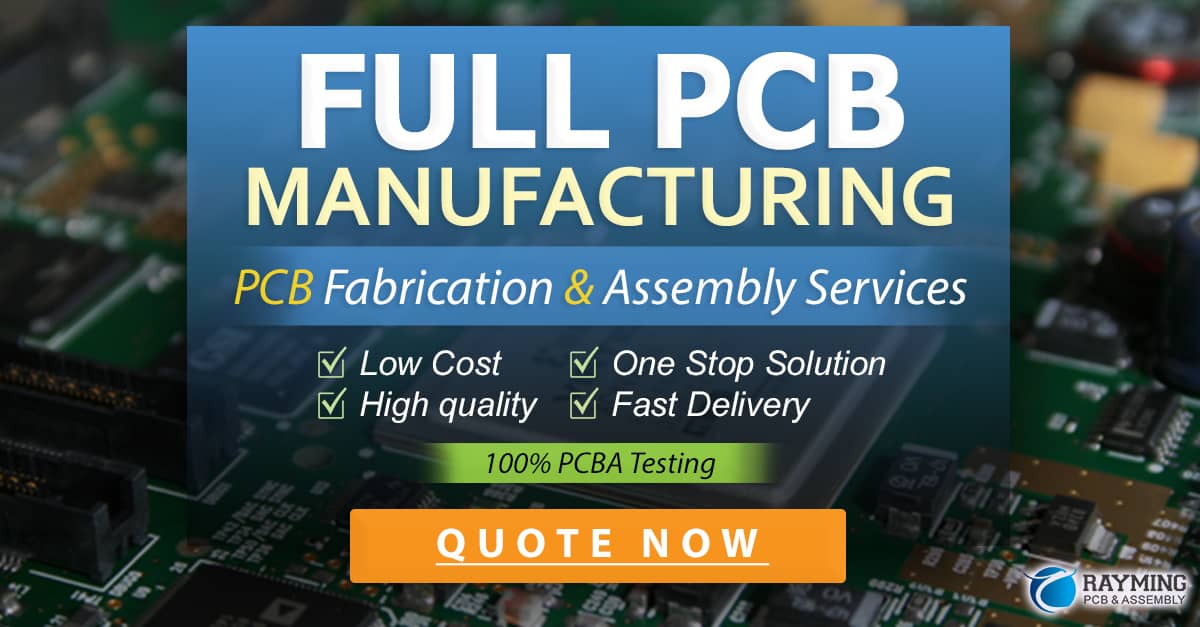
Conclusion
NPI manufacturing is a complex and critical process for electronics contract manufacturers. By following best practices in areas such as design for manufacturability, supply chain management, testing and quality assurance, and communication, CMs can ensure a smooth and successful transition from concept to volume production.
Effective NPI can help electronics CMs to:
- Launch new products quickly and efficiently
- Meet customer requirements and exceed expectations
- Control costs and maximize profitability
- Establish scalable and repeatable manufacturing processes
- Build long-term partnerships with customers
As the electronics industry continues to evolve and innovate, the importance of effective NPI manufacturing will only continue to grow. By staying at the forefront of best practices and continuously improving their processes, electronics contract manufacturers can position themselves for success in an increasingly competitive market.
Frequently Asked Questions (FAQ)
1. What is NPI in electronics manufacturing?
NPI stands for New Product Introduction. It refers to the process of taking a new product design from concept to full-scale production, including design review, prototyping, testing, and volume manufacturing ramp-up.
2. Why is Design for Manufacturability (DFM) important in NPI?
DFM is critical in NPI because it helps to ensure that the product design is optimized for manufacturing from the outset. Effective DFM can reduce costs, improve quality, and speed up time-to-market by identifying and addressing potential manufacturing issues early in the design process.
3. What are some key supply chain considerations in NPI?
Some key supply chain considerations in NPI include selecting reliable suppliers, establishing strong supplier relationships, implementing effective inventory management practices, monitoring supplier performance, and developing risk mitigation and business continuity plans.
4. What types of testing are typically involved in NPI?
NPI testing typically includes incoming quality control (IQC) for components, in-process quality checks, post-assembly testing such as in-circuit testing (ICT) and functional testing, outgoing quality control (OQC), and reliability testing such as burn-in and environmental stress testing.
5. How can electronics contract manufacturers ensure effective communication and collaboration with customers during NPI?
Effective communication and collaboration during NPI require establishing clear roles and expectations, having regular project status meetings, using collaborative project management tools, involving key stakeholders in design reviews and problem-solving, and maintaining open lines of communication to quickly resolve any issues that arise.
0 Comments