How AOI Works
AOI systems typically consist of the following components:
-
High-resolution cameras: AOI machines are equipped with one or more high-resolution cameras that capture detailed images of the inspected object from various angles.
-
Lighting system: Proper illumination is essential for accurate image capture. AOI systems employ advanced lighting techniques, such as multi-angle lighting or structured light, to enhance the visibility of defects.
-
Image processing software: The captured images are processed using sophisticated image processing algorithms and computer vision techniques to identify and classify defects.
-
Machine learning algorithms: Advanced AOI systems incorporate machine learning algorithms that can learn from historical data and adapt to new defect patterns, improving the accuracy and efficiency of the inspection process.
The AOI Inspection process generally follows these steps:
- The object to be inspected, such as a PCB, is placed in the AOI machine.
- The cameras capture high-resolution images of the object from various angles.
- The image processing software analyzes the captured images, comparing them to a reference model or pre-defined criteria.
- Any deviations or anomalies detected during the analysis are classified as defects.
- The AOI system generates a report detailing the location and type of defects found.
Benefits of AOI
Implementing AOI in the manufacturing process offers several significant benefits:
-
Improved quality control: AOI systems can detect a wide range of defects, including solder joint defects, component placement errors, and missing or incorrect components, ensuring higher product quality and reliability.
-
Increased efficiency: Automated Inspection is much faster than manual inspection, allowing for higher throughput and reduced production time.
-
Reduced human error: AOI eliminates the subjectivity and fatigue associated with manual inspection, minimizing the risk of human error and ensuring consistent inspection results.
-
Cost savings: By detecting defects early in the manufacturing process, AOI helps reduce scrap, rework, and warranty costs, ultimately leading to cost savings for the manufacturer.
-
Traceability and data collection: AOI systems generate detailed inspection reports and collect valuable data that can be used for process improvement, quality trend analysis, and traceability purposes.
Types of AOI Systems
There are several types of AOI systems designed to cater to different inspection requirements:
-
2D AOI: 2D AOI systems use top-down imaging to inspect the surface of the object. They are suitable for detecting defects such as missing components, incorrect component placement, and solder joint defects.
-
3D AOI: 3D AOI systems employ multiple cameras or structured light techniques to capture three-dimensional images of the inspected object. They can detect defects related to component height, coplanarity, and other three-dimensional aspects.
-
Inline AOI: Inline AOI systems are integrated directly into the production line, inspecting objects as they move along the conveyor. They provide real-time feedback and enable immediate correction of defects.
-
Offline AOI: Offline AOI systems are standalone machines that inspect objects outside the production line. They are typically used for batch inspection or for more detailed analysis of defects detected by inline systems.
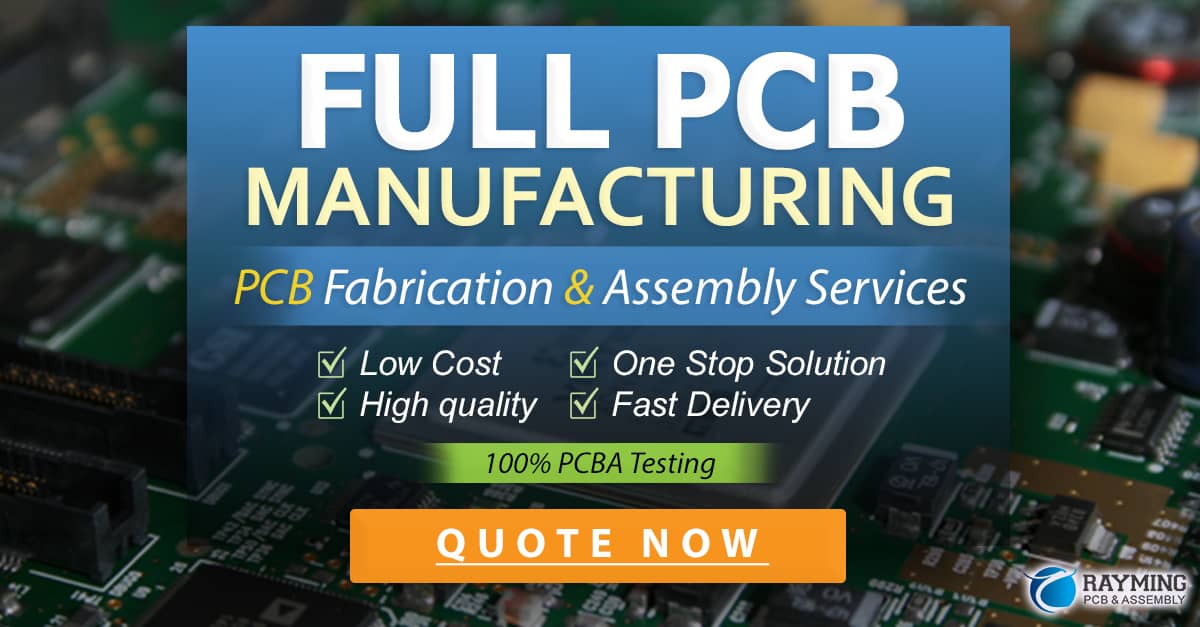
Applications of AOI
AOI technology finds applications in various industries and manufacturing processes:
-
Electronics manufacturing: AOI is widely used in the electronics industry for inspecting PCBs, solder joints, and electronic components. It is an essential tool for ensuring the quality and reliability of electronic products.
-
Automotive industry: AOI systems are used to inspect various automotive components, such as connectors, sensors, and printed circuit assemblies, to ensure they meet the stringent quality requirements of the automotive industry.
-
Medical device manufacturing: AOI is employed in the production of medical devices to inspect critical components, such as implants and surgical instruments, ensuring their quality and safety.
-
Aerospace and defense: AOI systems are used to inspect high-reliability components and assemblies used in aerospace and defense applications, where quality and reliability are of utmost importance.
-
Packaging and printing: AOI is used to inspect packaging materials, labels, and printed products for defects such as color variations, misalignments, and incorrect barcodes.
Challenges and Limitations of AOI
While AOI offers numerous benefits, there are some challenges and limitations to consider:
-
False positives and false negatives: AOI systems may occasionally generate false positive results, identifying non-defective areas as defects, or false negative results, failing to detect actual defects. Careful tuning and optimization of the system are necessary to minimize these occurrences.
-
Limited depth perception: 2D AOI systems may have limitations in detecting defects related to component height or coplanarity. 3D AOI systems can address this issue but may be more expensive and complex.
-
Reflective surfaces: Highly reflective surfaces, such as those found on certain electronic components, can pose challenges for AOI systems. Special lighting techniques or image processing algorithms may be required to accurately inspect these surfaces.
-
Training and expertise: Implementing and maintaining an AOI system requires specialized knowledge and expertise. Operators need to be trained in using the system effectively, and engineers must be able to fine-tune the system to adapt to new products or defect types.
-
Cost: AOI systems can be expensive, especially for small and medium-sized manufacturers. However, the long-term benefits in terms of quality improvement and cost savings often outweigh the initial investment.
Best Practices for Implementing AOI
To maximize the benefits of AOI and ensure successful implementation, consider the following best practices:
-
Define clear inspection criteria: Establish well-defined inspection criteria and acceptance standards based on product requirements and quality goals.
-
Optimize lighting and image capture: Ensure that the lighting setup and camera parameters are optimized for the specific product being inspected to enhance defect visibility and minimize false results.
-
Regular calibration and maintenance: Perform regular calibration and maintenance of the AOI system to ensure consistent performance and accuracy.
-
Continuous improvement: Analyze inspection data and use it for continuous process improvement. Identify recurring defect patterns and take corrective actions to prevent their occurrence.
-
Integration with other systems: Integrate the AOI system with other quality control and traceability systems, such as manufacturing execution systems (MES) or statistical process control (SPC) tools, to enable seamless data exchange and analysis.
The Future of AOI
As technology continues to advance, the future of AOI looks promising. Some of the trends and developments shaping the future of AOI include:
-
Deep learning and artificial intelligence: The integration of deep learning algorithms and artificial intelligence techniques into AOI systems will enable more accurate and adaptive defect detection, reducing false results and improving overall inspection performance.
-
Hyperspectral imaging: Hyperspectral imaging technology, which captures images across a wide range of electromagnetic spectrum bands, has the potential to enhance defect detection capabilities, particularly for materials with distinct spectral signatures.
-
Inline 3D AOI: The development of high-speed, inline 3D AOI systems will enable real-time, three-dimensional inspection of objects, providing more comprehensive defect detection and analysis.
-
Cloud-based AOI: Cloud-based AOI solutions will allow manufacturers to leverage the power of cloud computing for data storage, analysis, and remote access to inspection results, enabling better collaboration and decision-making.
-
Integration with Industry 4.0: As the manufacturing industry embraces Industry 4.0 and the Industrial Internet of Things (IIoT), AOI systems will become more integrated with other smart manufacturing technologies, enabling real-time process monitoring, predictive maintenance, and autonomous quality control.
Frequently Asked Questions (FAQ)
-
What is the difference between AOI and visual inspection?
AOI is an automated process that uses cameras, image processing software, and machine learning algorithms to inspect objects for defects, while visual inspection is a manual process performed by human operators. AOI is faster, more consistent, and less prone to human error compared to visual inspection. -
Can AOI completely replace human inspection?
While AOI can significantly reduce the need for human inspection, it may not completely replace it in all cases. Some complex or subjective defects may still require human expertise for final verification. AOI is often used in combination with human inspection for optimal results. -
How does AOI handle different product variants?
AOI systems can be programmed to inspect different product variants by using CAD data or golden sample comparisons. The inspection criteria and algorithms can be adapted to accommodate variations in product design or specifications. -
What types of defects can AOI detect?
AOI can detect a wide range of defects, including: - Solder joint defects (bridging, Insufficient Solder, tombstoning)
- Component placement errors (missing, misaligned, or rotated components)
- Dimensional defects (size, shape, or height variations)
- Surface defects (scratches, contamination, or discoloration)
-
Assembly defects (incorrect or missing parts)
-
How do I choose the right AOI system for my manufacturing process?
When selecting an AOI system, consider factors such as: - The types of products to be inspected and their complexity
- The required inspection speed and throughput
- The level of defect detection accuracy and reliability needed
- The available budget and return on investment (ROI)
- The ease of integration with existing manufacturing processes and systems
It is recommended to consult with AOI system providers and conduct a thorough evaluation of different options to find the best fit for your specific requirements.
Conclusion
Automated Optical Inspection (AOI) is a powerful technology that revolutionizes quality control in manufacturing. By leveraging advanced imaging techniques, computer vision, and machine learning, AOI systems can detect a wide range of defects with high speed and accuracy, ensuring the production of high-quality products while reducing costs and improving efficiency.
As the manufacturing industry continues to evolve and embrace digital transformation, AOI will play an increasingly critical role in enabling smart, connected, and autonomous quality control processes. By staying informed about the latest developments in AOI technology and implementing best practices, manufacturers can harness the full potential of AOI to drive quality, innovation, and competitiveness in their operations.
0 Comments