Introduction to Aluminium PCBs and PCB Fabricators
Aluminium PCBs (Printed Circuit Boards) have gained significant popularity in recent years due to their unique properties and advantages over traditional PCBs. These PCBs utilize aluminium as the base material instead of the commonly used FR-4 substrate. Aluminium PCBs offer excellent thermal conductivity, improved heat dissipation, and enhanced mechanical stability, making them ideal for applications that generate substantial heat or require robust performance.
PCB fabricators play a crucial role in the manufacturing process of aluminium PCBs. These specialized companies possess the expertise, equipment, and knowledge necessary to design, prototype, and mass-produce high-quality aluminium PCBs. They work closely with clients to understand their specific requirements and provide customized solutions that meet the desired specifications.
In this comprehensive article, we will delve into the world of aluminium PCBs and PCB fabricators. We will explore the benefits and applications of aluminium PCBs, the manufacturing process, key considerations when choosing a PCB fabricator, and address frequently asked questions to provide a thorough understanding of this technology.
Benefits and Applications of Aluminium PCBs
Thermal Management
One of the primary advantages of aluminium PCBs is their exceptional thermal management capabilities. Aluminium has a high thermal conductivity, which means it can effectively dissipate heat generated by electronic components. This property is particularly valuable in applications that involve high-power devices, such as LED lighting, power electronics, and automotive systems.
By using aluminium as the base material, PCB fabricators can design boards that efficiently transfer heat away from critical components, preventing overheating and ensuring optimal performance. The improved thermal management also contributes to the longevity and reliability of the electronic devices.
Mechanical Stability and Durability
Aluminium PCBs offer superior mechanical stability and durability compared to traditional PCBs. The aluminium substrate provides a rigid and sturdy foundation for the electronic components, reducing the risk of physical damage caused by vibrations, shocks, or impacts.
This enhanced mechanical stability is especially beneficial in applications that are subjected to harsh environments or demanding operating conditions. Aluminium PCBs are commonly used in industrial equipment, aerospace systems, and military devices, where reliability and robustness are paramount.
Weight Reduction
In certain applications, such as aerospace and automotive industries, weight reduction is a critical factor. Aluminium PCBs can contribute to overall weight savings due to the lower density of aluminium compared to other PCB materials.
By incorporating aluminium PCBs into the design, manufacturers can create lighter and more compact electronic devices without compromising performance or functionality. This weight reduction can lead to improved fuel efficiency, increased payload capacity, and enhanced overall system performance.
Electromagnetic Shielding
Aluminium PCBs offer inherent electromagnetic shielding properties. The aluminium substrate acts as a natural barrier against electromagnetic interference (EMI) and radio frequency interference (RFI). This shielding capability is valuable in sensitive electronic applications where signal integrity and protection from external interference are crucial.
PCB fabricators can leverage the shielding properties of aluminium to design boards that minimize electromagnetic compatibility issues and ensure reliable operation in environments with potential interference sources.
Manufacturing Process of Aluminium PCBs
The manufacturing process of aluminium PCBs involves several key steps that require specialized equipment and expertise. PCB fabricators follow a meticulous process to ensure the highest quality and reliability of the final product.
Substrate Preparation
The first step in the manufacturing process is the preparation of the aluminium substrate. The aluminium sheet is cleaned and treated to remove any impurities or contaminants that could affect the adhesion of the subsequent layers.
Insulation Layer Application
To electrically isolate the aluminium substrate from the conductive copper traces, an insulation layer is applied. This layer is typically a thin dielectric material, such as polyimide or epoxy resin. The insulation layer is carefully deposited onto the aluminium substrate using precise coating techniques.
Circuit Pattern Imaging
Once the insulation layer is in place, the desired circuit pattern is imaged onto the surface. This is typically done using photolithography, where a photoresist material is applied, exposed to light through a patterned mask, and developed to create the desired circuit layout.
Copper Deposition
After the circuit pattern is imaged, a layer of copper is deposited onto the insulation layer. This is typically done using electroplating or electroless plating techniques. The copper layer forms the conductive traces and pads that make up the electrical connections on the PCB.
Etching and Resist Removal
The excess copper is then etched away, leaving only the desired circuit pattern. The remaining photoresist material is also removed, revealing the final circuit layout on the aluminium substrate.
Surface Finishing
To protect the copper traces and improve solderability, a surface finish is applied to the PCB. Common surface finishes include HASL (Hot Air Solder Leveling), ENIG (Electroless Nickel Immersion Gold), and OSP (Organic Solderability Preservative).
Drilling and Cutting
Holes are drilled through the aluminium PCB to accommodate through-hole components or create vias for interconnections between layers. The PCB is then cut to its final shape and size using precise cutting techniques.
Quality Control and Testing
Throughout the manufacturing process, PCB fabricators implement strict quality control measures to ensure the consistency and reliability of the aluminium PCBs. Visual inspections, electrical testing, and other quality assurance procedures are performed to detect and rectify any defects or anomalies.
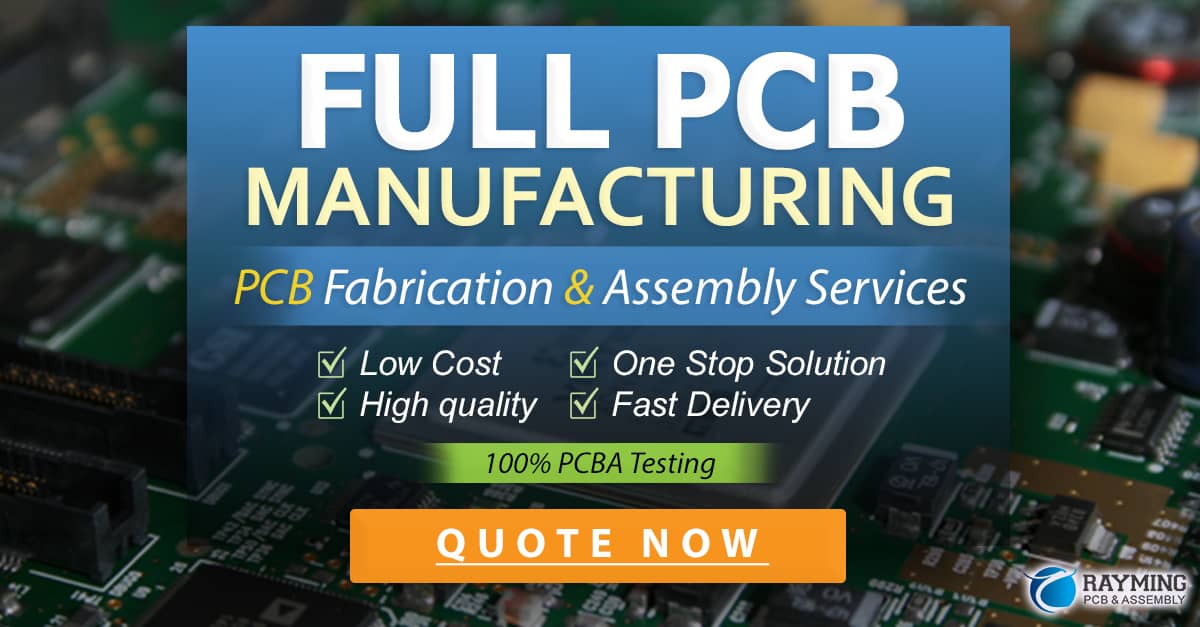
Choosing the Right Aluminium PCB Fabricator
When selecting an aluminium PCB fabricator, several key factors should be considered to ensure a successful partnership and high-quality end products.
Technical Expertise and Experience
Look for a PCB fabricator with extensive experience in manufacturing aluminium PCBs. They should have a deep understanding of the unique properties and challenges associated with aluminium substrates and possess the necessary technical expertise to design and fabricate boards that meet your specific requirements.
Manufacturing Capabilities
Assess the manufacturing capabilities of the PCB fabricator. They should have state-of-the-art equipment and facilities capable of handling the specific requirements of aluminium PCBs. Consider their capacity to accommodate your production volume, lead times, and any specialized manufacturing processes you may require.
Quality Standards and Certifications
Choose a PCB fabricator that adheres to strict quality standards and holds relevant certifications. ISO 9001 certification is a widely recognized quality management system standard that ensures consistent and reliable manufacturing processes. Other certifications, such as UL (Underwriters Laboratories) or IPC (Association Connecting Electronics Industries) standards, demonstrate the fabricator’s commitment to producing high-quality and compliant products.
Customer Support and Communication
Effective communication and responsive customer support are essential when working with a PCB fabricator. Look for a company that provides clear and timely communication throughout the manufacturing process. They should be willing to answer your questions, provide updates, and address any concerns you may have.
Cost and Lead Time
Cost and lead time are important considerations when selecting a PCB fabricator. While price is a factor, it should not be the sole determining criteria. Strike a balance between cost, quality, and delivery time to ensure you receive the best value for your investment. Discuss your budget and timeline requirements with potential fabricators to find a solution that aligns with your needs.
Frequently Asked Questions (FAQ)
-
Q: What are the advantages of using aluminium PCBs over traditional FR-4 PCBs?
A: Aluminium PCBs offer several advantages, including excellent thermal conductivity for improved heat dissipation, enhanced mechanical stability and durability, potential for weight reduction, and inherent electromagnetic shielding properties. -
Q: Can aluminium PCBs be used for high-frequency applications?
A: Yes, aluminium PCBs can be suitable for high-frequency applications. The aluminium substrate provides a stable and low-loss dielectric material that can support high-frequency signal transmission. However, careful design considerations and proper material selection are necessary to optimize performance. -
Q: Are there any limitations or challenges associated with aluminium PCBs?
A: One challenge with aluminium PCBs is the requirement for a dielectric insulation layer between the aluminium substrate and the conductive copper traces. This additional layer adds complexity to the manufacturing process and may impact the overall thickness of the PCB. Additionally, aluminium PCBs may have different thermal expansion properties compared to other components, which needs to be considered during the design phase. -
Q: How do I determine the appropriate thickness of the aluminium substrate for my application?
A: The thickness of the aluminium substrate depends on various factors, including the power dissipation requirements, mechanical stability needs, and overall design constraints. PCB fabricators can provide guidance and recommendations based on your specific application and requirements. They can help you select the optimal aluminium thickness that balances thermal management, mechanical integrity, and manufacturability. -
Q: Can aluminium PCBs be manufactured with multiple layers?
A: Yes, aluminium PCBs can be fabricated with multiple layers. Multi-layer aluminium PCBs offer the benefits of increased circuit density and more complex routing capabilities. The manufacturing process involves laminating multiple layers of insulation and conductive materials onto the aluminium substrate. However, the fabrication of multi-layer aluminium PCBs requires specialized expertise and equipment, so it’s important to choose a PCB fabricator with experience in this area.
Conclusion
Aluminium PCBs have emerged as a valuable solution for applications demanding superior thermal management, mechanical stability, and lightweight construction. With their unique properties and benefits, aluminium PCBs have found widespread use in industries such as automotive, aerospace, industrial equipment, and high-power electronics.
PCB fabricators play a vital role in bringing aluminium PCBs from concept to reality. Their expertise, manufacturing capabilities, and commitment to quality ensure the successful production of high-performance aluminium PCBs.
When selecting an aluminium PCB fabricator, consider factors such as technical expertise, manufacturing capabilities, quality standards, customer support, and cost-effectiveness. By partnering with a reputable and experienced PCB fabricator, you can leverage the benefits of aluminium PCBs and achieve optimal results for your specific application.
As technology continues to advance, the demand for innovative and reliable PCB solutions will only grow. Aluminium PCBs, with their distinct advantages, are poised to meet the evolving needs of industries and contribute to the development of cutting-edge electronic devices.
By understanding the benefits, manufacturing process, and key considerations associated with aluminium PCBs and PCB fabricators, you can make informed decisions and unlock the potential of this technology for your projects.
0 Comments