Introduction
Printed Circuit Board (PCB) layout is a crucial step in the design and manufacturing of electronic devices. The placement of components on the PCB can greatly affect the performance, reliability, and manufacturability of the final product. In this comprehensive guide, we will walk you through the best practices and techniques for PCB component placement, helping you create high-quality designs that meet your project requirements.
Understanding the Importance of PCB Component Placement
Proper PCB component placement is essential for several reasons:
-
Signal Integrity: The placement of components can impact the signal integrity of your design. By carefully positioning critical components and routing traces, you can minimize signal distortion, crosstalk, and electromagnetic interference (EMI).
-
Thermal Management: Heat Dissipation is a critical factor in PCB design. Strategic component placement can help distribute heat evenly across the board, preventing hotspots and ensuring optimal thermal performance.
-
Manufacturing Feasibility: The arrangement of components on the PCB affects the manufacturing process. Proper placement can facilitate automated assembly, reduce manufacturing costs, and improve overall production efficiency.
-
Mechanical Considerations: Component placement must take into account mechanical constraints such as board size, mounting holes, and connector locations. Careful planning can ensure a robust and reliable final product.
PCB Layout Guidelines for Component Placement
To achieve optimal PCB layout, follow these guidelines when placing your components:
1. Start with a Schematic
Before diving into the PCB layout, ensure that you have a well-designed schematic. The schematic serves as a blueprint for your PCB, defining the connections between components and the overall circuit functionality. A clear and accurate schematic will make the layout process smoother and help avoid potential issues.
2. Consider the Board Stackup
The board stackup refers to the arrangement of copper layers and dielectric materials in your PCB. When placing components, consider the stackup and the location of power and ground planes. Proper utilization of the stackup can enhance signal integrity, reduce EMI, and improve power distribution.
3. Group Related Components
Organize components on the PCB based on their functional relationships. Group components that work together or share common signals in close proximity. This approach minimizes the length of traces, reduces signal integrity issues, and simplifies the routing process.
4. Prioritize Critical Components
Identify the critical components in your design, such as high-speed devices, sensitive analog circuits, or power regulation modules. Give priority to the placement of these components, ensuring they have optimal positioning for signal integrity and thermal management.
5. Minimize Trace Lengths
Strive to minimize the length of traces between components, especially for high-speed signals. Shorter traces reduce signal attenuation, minimize parasitic effects, and improve overall signal quality. Consider the use of direct connections or via-in-pad techniques when appropriate.
6. Avoid Crossing Sensitive Signals
When placing components, aim to avoid crossing sensitive signals, such as high-speed traces or analog signals, with other traces or power planes. Crossing signals can introduce crosstalk and degrade signal integrity. If crossings are unavoidable, use techniques like ground shielding or stitching vias to mitigate the impact.
7. Provide Adequate Clearances
Ensure sufficient clearances between components, traces, and board edges. Adequate clearances are essential for manufacturing reliability and to prevent short circuits or mechanical issues. Consult your PCB Manufacturer’s design guidelines for recommended clearance values.
8. Consider Mechanical Requirements
Take into account the mechanical requirements of your design when placing components. Consider factors such as board dimensions, mounting holes, connectors, and any enclosure constraints. Ensure that components do not interfere with mechanical features and have sufficient space for assembly and maintenance.
9. Optimize for Manufacturing
Design your PCB layout with manufacturing in mind. Follow the design for manufacturability (DFM) guidelines provided by your PCB Fabrication and assembly partners. Consider factors such as component orientation, solder mask clearances, and pick-and-place machine capabilities to streamline the manufacturing process.
10. Perform Design Reviews
Conduct thorough design reviews at various stages of the PCB layout process. Involve relevant stakeholders, such as electrical engineers, mechanical engineers, and manufacturing experts, to gather feedback and identify potential issues early on. Design reviews can help catch errors, optimize the layout, and ensure compliance with project requirements.
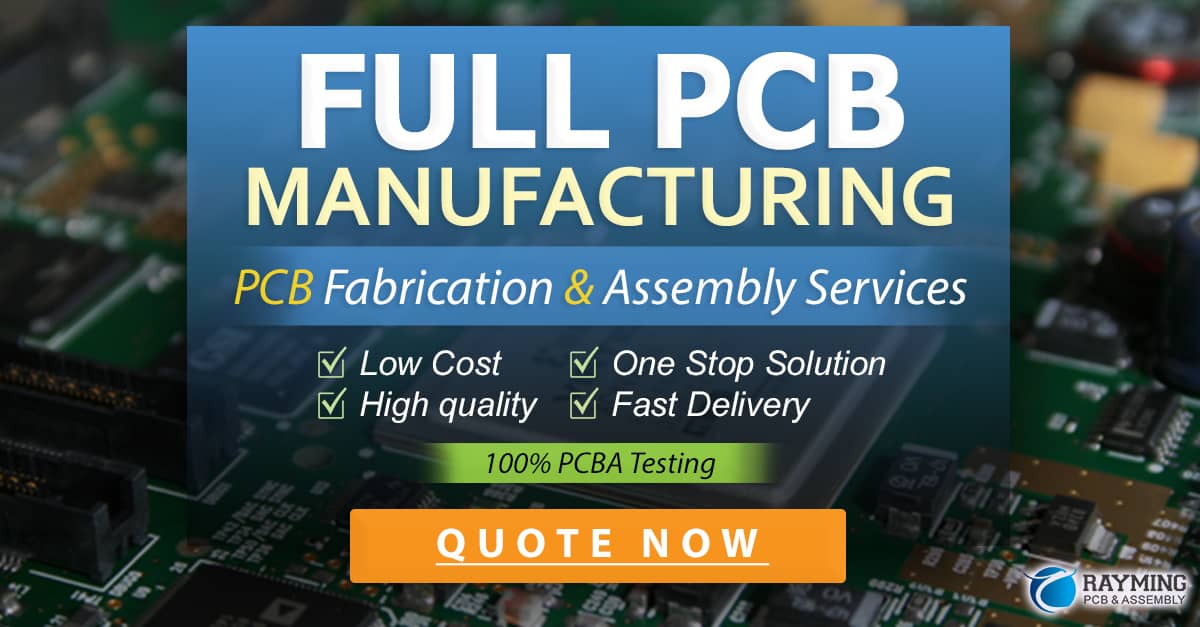
Common Pitfalls to Avoid in PCB Component Placement
To ensure a successful PCB layout, be aware of these common pitfalls and take steps to avoid them:
-
Overcrowding Components: Avoid placing components too close together, as it can lead to manufacturing difficulties, thermal issues, and signal integrity problems. Maintain appropriate spacing between components based on their size, power dissipation, and signal characteristics.
-
Neglecting Thermal Considerations: Don’t overlook the thermal aspects of your design. Identify components that generate significant heat and ensure they have adequate thermal relief. Use thermal vias, heat sinks, or other thermal management techniques when necessary.
-
Ignoring High-Speed Signal Routing: High-speed signals require special attention during component placement and routing. Neglecting high-speed signal integrity can lead to signal distortion, reflections, and EMI issues. Follow best practices for high-speed PCB design, such as controlled impedance routing and proper termination.
-
Overlooking Power Distribution: Proper power distribution is crucial for the stability and performance of your PCB. Ensure that power and ground planes are adequately sized and strategically placed to minimize voltage drops and provide low-impedance power delivery to components.
-
Skipping Design Rule Checks (DRC): Don’t forget to run DRC throughout the PCB layout process. DRC helps identify violations of design rules, such as insufficient clearances, trace width violations, or missing connections. Regularly running DRC can catch errors early and save time in the long run.
PCB Component Placement Techniques and Tips
Here are some additional techniques and tips to optimize your PCB component placement:
1. Use a Grid System
Utilize a grid system when placing components on the PCB. Aligning components to a grid helps maintain consistency, improves readability, and facilitates automated assembly. Choose a grid size that accommodates the majority of your components and ensures appropriate spacing.
2. Consider Component Orientation
Pay attention to the orientation of components on the PCB. Properly orient components to minimize trace lengths, enhance signal integrity, and facilitate efficient routing. Some components, such as connectors or switches, may have specific orientation requirements based on mechanical or usability considerations.
3. Utilize Symmetry and Patterns
Where applicable, leverage symmetry and patterns in your component placement. Symmetrical layouts can improve signal integrity, reduce electromagnetic interference, and enhance the visual appeal of the PCB. Repeating patterns can also simplify the routing process and make the layout more organized.
4. Optimize for Test Points
Include test points in your PCB layout to facilitate testing and debugging. Strategically place test points near critical components or signals, ensuring they are easily accessible for probing. Consider the use of test pads, vias, or dedicated test connectors to simplify the testing process.
5. Document Your Layout
Maintain clear documentation of your PCB layout, including component placement decisions, design rationale, and any specific requirements. Documentation helps collaborate with team members, facilitates future revisions, and serves as a reference for manufacturing and assembly.
PCB Component Placement Checklist
Use this checklist to ensure you have covered the essential aspects of PCB component placement:
- [ ] Schematic review completed
- [ ] Board stackup defined
- [ ] Critical components identified and prioritized
- [ ] Components grouped based on functionality
- [ ] Trace lengths minimized
- [ ] Sensitive signals isolated and shielded
- [ ] Adequate clearances maintained
- [ ] Mechanical requirements considered
- [ ] Manufacturing guidelines followed
- [ ] Thermal considerations addressed
- [ ] High-speed signals properly routed
- [ ] Power distribution optimized
- [ ] Design rule checks (DRC) passed
- [ ] Test points included
- [ ] Layout documentation updated
Frequently Asked Questions (FAQ)
-
Q: What is the recommended spacing between components on a PCB?
A: The recommended spacing between components depends on various factors, such as component size, signal characteristics, and manufacturing capabilities. As a general guideline, aim for a minimum spacing of 0.1 inches (2.54 mm) between components. However, consult your PCB manufacturer’s design guidelines for specific recommendations. -
Q: How can I minimize electromagnetic interference (EMI) in my PCB layout?
A: To minimize EMI, consider the following techniques: - Separate analog and digital circuits
- Use ground planes to provide shielding
- Route high-speed signals away from sensitive circuits
- Minimize loop areas in signal traces
- Use Decoupling Capacitors near power pins of ICs
-
Implement proper grounding and shielding techniques
-
Q: What are the benefits of using a grid system for component placement?
A: Using a grid system for component placement offers several benefits: - Maintains consistency and organization in the layout
- Facilitates easier routing and trace management
- Enhances readability and visual appeal of the PCB
- Simplifies automated assembly processes
-
Ensures proper spacing and alignment of components
-
Q: How can I optimize my PCB layout for thermal management?
A: To optimize thermal management in your PCB layout: - Identify components that generate significant heat
- Place high-heat components away from temperature-sensitive devices
- Provide adequate spacing between high-heat components
- Use thermal vias to conduct heat away from components
- Implement heat sinks or other cooling techniques when necessary
-
Consider the use of thermal planes or heat spreaders
-
Q: What should I consider when placing connectors on a PCB?
A: When placing connectors on a PCB, consider the following: - Mechanical compatibility with enclosures or mating connectors
- Accessibility for user interaction or cable connections
- Orientation and spacing for ease of use
- Signal integrity and shielding requirements
- Strain relief and mechanical support for connectors
- Manufacturing and assembly constraints
Conclusion
PCB component placement is a critical aspect of PCB design that directly impacts the performance, reliability, and manufacturability of electronic devices. By following the guidelines, techniques, and best practices outlined in this article, you can create high-quality PCB layouts that meet your project requirements and ensure successful manufacturing outcomes.
Remember to prioritize critical components, minimize trace lengths, maintain signal integrity, and consider thermal and mechanical aspects during the placement process. Utilize tools like design rule checks (DRC) and collaborate with your manufacturing partners to identify and resolve any potential issues early in the design cycle.
By mastering the art of PCB component placement, you can streamline your design process, reduce development time, and achieve optimal results in your electronic projects.
0 Comments