What is a PCB Pad?
A PCB pad, also known as a solder pad or a contact pad, is a small, flat area on a printed circuit board (PCB) designed to provide a connection point for electronic components. These pads are typically made of copper and are coated with a layer of solder mask, which helps protect the copper from oxidation and prevents accidental short circuits.
PCB pads come in various shapes and sizes, depending on the component they are intended to accommodate. Some common pad shapes include:
- Circular pads
- Rectangular pads
- Oval pads
- Teardrop pads
The size of the pad is determined by the size of the component lead or pin that will be soldered to it. It is essential to ensure that the pad is large enough to provide a secure connection but not so large that it interferes with other components or traces on the PCB.
The Importance of PCB Pads
PCB pads play a crucial role in the overall functionality and reliability of a printed circuit board. Some of the key reasons why PCB pads are important include:
-
Providing a secure connection: PCB pads ensure that components are securely connected to the board, preventing them from becoming loose or disconnected due to vibration or mechanical stress.
-
Enabling proper soldering: The size and shape of a PCB pad can affect the quality of the solder joint. A well-designed pad allows for the formation of a strong, reliable solder joint between the component and the board.
-
Facilitating heat dissipation: PCB pads can help dissipate heat generated by components during operation. This is particularly important for power-hungry components, such as voltage regulators or power transistors.
-
Maintaining signal integrity: Properly designed PCB pads can help maintain signal integrity by minimizing impedance mismatches and reducing the risk of signal reflections.
Types of PCB Pads
There are several types of PCB pads, each designed for specific purposes or components. Some of the most common types include:
Surface Mount Pads
Surface mount pads are designed for use with surface mount devices (SMDs), which are components that are soldered directly onto the surface of the PCB. These pads are typically smaller than through-hole pads and are often rectangular or oval in shape.
Surface mount pads can be further categorized based on the type of SMD they are intended for:
-
Passive component pads: These pads are used for resistors, capacitors, and inductors. They are typically rectangular and have a size that corresponds to the component’s footprint.
-
Integrated circuit (IC) pads: IC pads are designed to accommodate the leads of surface mount ICs. They are often arranged in a grid pattern, with the spacing between pads determined by the IC’s package type (e.g., SOIC, QFP, BGA).
-
Leadless component pads: Leadless components, such as chip resistors and capacitors, require special pads that allow for proper soldering and heat dissipation. These pads often have a larger surface area to ensure a secure connection.
Through-Hole Pads
Through-hole pads are used for components that have leads that pass through holes in the PCB and are soldered on the opposite side. These pads are typically larger than surface mount pads and are often circular in shape.
Through-hole pads can be further classified based on their specific design:
-
Annular ring pads: Annular ring pads have a circular copper area surrounding the hole, which helps to strengthen the solder joint and improve mechanical stability.
-
Thermal relief pads: Thermal relief pads have a special design that helps to dissipate heat during the soldering process. They feature a series of thin copper traces that connect the pad to the surrounding copper pour, allowing heat to flow away from the pad more easily.
Specialty Pads
In addition to surface mount and through-hole pads, there are several specialty pads designed for specific applications or components:
-
Connector pads: These pads are designed to accommodate the pins of various types of connectors, such as headers, edge connectors, or USB connectors. The size and shape of the pad will depend on the specific connector being used.
-
Test point pads: Test point pads are small, circular pads that provide access to specific signals or voltages on the PCB for testing and debugging purposes. They are typically not used for component mounting.
-
Fiducial pads: Fiducial pads are small, circular pads placed on the PCB to serve as reference points for automated assembly equipment. They help ensure precise component placement and alignment during the manufacturing process.
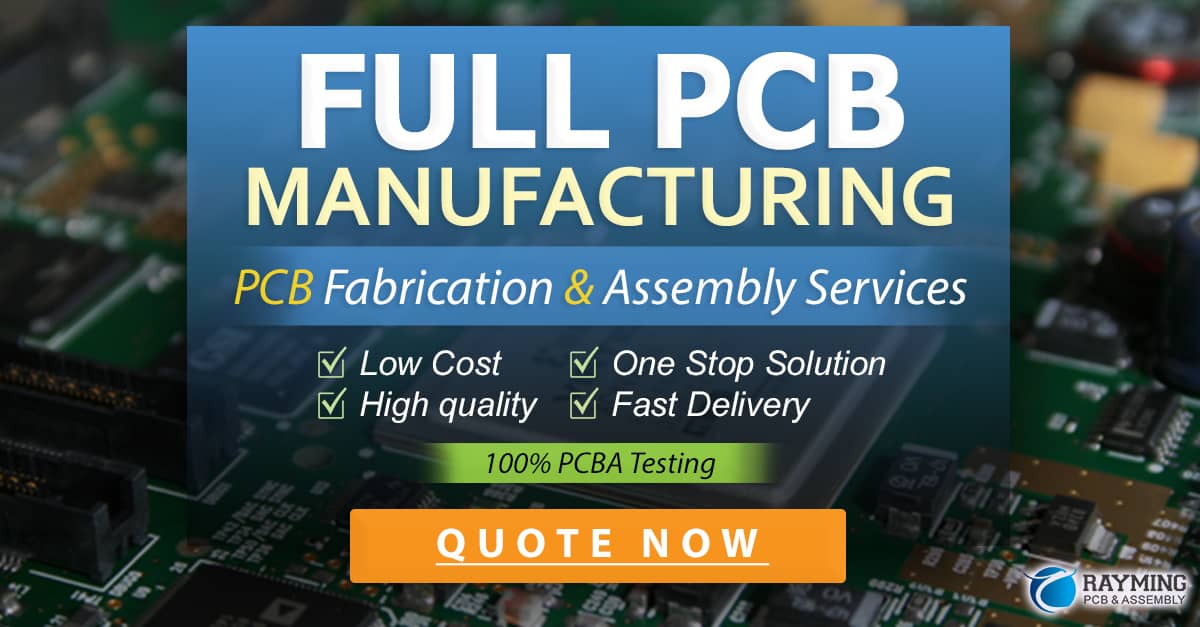
Designing PCB Pads
When designing PCB pads, there are several factors to consider to ensure optimal performance and reliability:
Pad Size and Shape
The size and shape of a PCB pad should be determined based on the specific component it is intended to accommodate. Some key considerations include:
-
Component lead size: The pad should be large enough to provide a secure connection to the component lead or pin, with enough space for a strong solder joint to form.
-
Soldering process: The pad size and shape may need to be adjusted based on the soldering process being used (e.g., wave soldering, reflow soldering, hand soldering).
-
Mechanical stability: For components subject to high mechanical stress, such as connectors, larger pads or additional anchor points may be necessary to ensure a stable connection.
Pad Spacing
The spacing between pads is another critical factor in PCB design. Pads should be spaced far enough apart to prevent accidental short circuits or signal crosstalk, but close enough to minimize the overall size of the PCB.
Some factors that can influence pad spacing include:
-
Voltage and current levels: Higher voltage or current applications may require greater pad spacing to prevent arcing or excessive heat buildup.
-
Signal frequency: High-frequency signals may require greater pad spacing to minimize crosstalk and maintain signal integrity.
-
Manufacturing capabilities: The minimum pad spacing will be determined by the capabilities of the PCB manufacturer and the specific fabrication process being used.
Solder Mask and Paste Openings
Solder mask and paste openings are important considerations when designing PCB pads. The solder mask opening should be slightly larger than the pad itself to allow for proper solder flow and to prevent the mask from interfering with the solder joint.
The solder paste opening, which is used in the stencil printing process for surface mount assembly, should be carefully designed to ensure the right amount of solder paste is deposited on the pad. Too much solder paste can lead to bridging or short circuits, while too little can result in weak or incomplete solder joints.
Thermal Considerations
For components that generate significant amounts of heat, such as power transistors or voltage regulators, thermal management is a critical concern in PCB pad design. In these cases, the pad size and shape may need to be optimized to promote heat dissipation and prevent overheating.
Some strategies for improving thermal performance include:
-
Increasing pad size: Larger pads can help to spread heat more effectively and reduce thermal resistance.
-
Using thermal relief pads: As mentioned earlier, thermal relief pads feature a special design that helps to dissipate heat away from the pad and into the surrounding copper pour.
-
Adding thermal vias: Thermal vias are small, plated holes that are placed in or around the pad to provide an additional path for heat to flow through the PCB and into the ground plane or other heat-sinking structures.
PCB Pad Materials
PCB pads are typically made of copper, which is an excellent conductor of electricity and heat. However, the copper is usually coated with additional materials to protect it from oxidation and improve solderability.
Some common pad surface finishes include:
-
Hot Air Solder Leveling (HASL): HASL is a process in which the pads are coated with a thin layer of solder using a hot air knife. This provides a solderable surface and helps to protect the copper from oxidation.
-
Organic Solderability Preservative (OSP): OSP is a thin, organic coating that is applied to the pads to prevent oxidation and maintain solderability. It is a popular choice for lead-free soldering processes.
-
Electroless Nickel Immersion Gold (ENIG): ENIG is a two-layer surface finish that consists of a layer of nickel and a thin layer of gold. The nickel provides a barrier against copper migration, while the gold ensures excellent solderability and shelf life.
-
Immersion Silver: Immersion silver is a thin, silver-based coating that provides good solderability and is often used as a more cost-effective alternative to ENIG.
The choice of pad surface finish will depend on factors such as the soldering process being used, the shelf life requirements, and the specific environmental conditions the PCB will be exposed to.
PCB Pad Fabrication
PCB pads are typically fabricated as part of the overall PCB manufacturing process. The basic steps involved in creating PCB pads include:
-
Copper etching: The PCB starts as a blank board with a layer of copper on one or both sides. The desired pad layout is etched into the copper layer using a photolithographic process, which involves applying a light-sensitive resist, exposing it to a pattern of light, and then chemically etching away the unwanted copper.
-
Drill holes: For through-hole pads, holes are drilled through the board at the locations of the pads. The size of the hole will depend on the specific component lead size and the requirements of the soldering process.
-
Plating: After drilling, the holes are plated with copper to create a conductive path from one side of the board to the other. This step also helps to reinforce the mechanical strength of the hole.
-
Surface finish application: Once the pads are etched and plated, the desired surface finish (e.g., HASL, OSP, ENIG) is applied to protect the copper and improve solderability.
-
Solder mask application: A layer of solder mask is applied over the entire board, with openings left for the pads and other exposed copper areas. This helps to protect the copper from oxidation and prevents accidental short circuits.
Throughout the fabrication process, strict quality control measures are employed to ensure that the pads meet the required specifications for size, shape, and spacing. This includes visual inspections, automated optical inspections (AOI), and electrical testing to verify continuity and isolation.
Common PCB Pad Defects and Issues
Despite advances in PCB manufacturing technology, defects and issues can still occur with PCB pads. Some common problems include:
-
Pad lifting: Pad lifting occurs when the pad separates from the PCB surface, often due to poor adhesion or mechanical stress. This can lead to broken solder joints and component failures.
-
Pad corrosion: Over time, exposed copper pads can corrode due to exposure to moisture, air, or other environmental factors. This can lead to increased resistance and potential signal integrity issues.
-
Solder bridging: Solder bridging occurs when excess solder flows between adjacent pads, creating an unintended short circuit. This can be caused by improper pad spacing, excessive solder paste application, or incorrect reflow profiles.
-
Insufficient solder joint strength: If the pad size or shape is incorrect, or if there is not enough solder paste applied, the resulting solder joint may be weak or incomplete. This can lead to intermittent connections or component failures.
-
Pad contamination: Contaminants such as dirt, grease, or flux residue on the pad surface can interfere with the formation of a strong solder joint, leading to connection issues.
To minimize the risk of these defects and issues, it is important to follow best practices in PCB design, fabrication, and assembly. This includes careful pad layout and sizing, proper surface finish selection, and strict process controls during manufacturing and assembly.
FAQ
1. What is the difference between a surface mount pad and a through-hole pad?
A: Surface mount pads are designed for components that are soldered directly onto the surface of the PCB, while through-hole pads are used for components with leads that pass through holes in the board and are soldered on the opposite side.
2. How do I choose the right size and shape for my PCB pads?
A: The size and shape of a PCB pad should be based on the specific component it is intended to accommodate, taking into account factors such as lead size, soldering process, and mechanical stability requirements. Consult component datasheets and PCB design guidelines for recommendations.
3. What is the purpose of a solder mask opening on a PCB pad?
A: The solder mask opening is a small area around the pad where the solder mask has been removed to expose the underlying copper. This opening allows for proper solder flow and helps to prevent the mask from interfering with the formation of a strong solder joint.
4. How can I improve the thermal performance of my PCB pads?
A: To improve thermal performance, you can increase pad size, use thermal relief pads, or add thermal vias to provide additional paths for heat to dissipate through the PCB and into heat-sinking structures.
5. What are some common issues that can occur with PCB pads?
A: Common issues include pad lifting, pad corrosion, solder bridging, insufficient solder joint strength, and pad contamination. These issues can be minimized by following best practices in PCB design, fabrication, and assembly, including careful pad layout, proper surface finish selection, and strict process controls.
0 Comments