Introduction to PCB Additive Manufacturing
Printed Circuit Board (PCB) manufacturing has come a long way since its inception in the early 20th century. With the advent of new technologies and processes, PCB manufacturing has evolved to meet the ever-increasing demands of the electronics industry. One such technology that has gained significant attention in recent years is additive manufacturing, also known as 3D printing.
What is Additive Manufacturing?
Additive manufacturing is a process of creating objects by adding material layer by layer. This is in contrast to traditional manufacturing methods, such as subtractive manufacturing, where material is removed from a larger piece to create the desired object. Additive manufacturing has been used in various industries, including aerospace, automotive, and medical, and has now found its way into the electronics industry.
Benefits of Additive Manufacturing for PCB Assembly
Additive manufacturing offers several benefits over traditional PCB manufacturing methods. Some of these benefits include:
- Faster prototyping: Additive manufacturing allows for rapid prototyping of PCBs, reducing the time and cost associated with traditional prototyping methods.
- Increased design flexibility: With additive manufacturing, designers have more freedom to create complex geometries and shapes that would be difficult or impossible to achieve with traditional manufacturing methods.
- Reduced waste: Additive manufacturing produces less waste compared to subtractive manufacturing methods, as material is only added where needed.
- Lower costs: Additive manufacturing can be more cost-effective than traditional manufacturing methods, especially for low-volume production runs.
PCB Additive Manufacturing Techniques
There are several additive manufacturing techniques that can be used for PCB manufacturing. Some of the most common techniques include:
Stereolithography (SLA)
Stereolithography is a 3D printing technique that uses a laser to cure and harden liquid resin layer by layer. This technique is well-suited for creating high-resolution PCBs with fine features and smooth surfaces.
Fused Deposition Modeling (FDM)
Fused Deposition Modeling is a 3D printing technique that uses a heated nozzle to extrude molten plastic onto a build platform. This technique is commonly used for creating structural components of PCBs, such as enclosures and housings.
Selective Laser Sintering (SLS)
Selective Laser Sintering is a 3D printing technique that uses a laser to sinter powdered material into a solid object. This technique is well-suited for creating complex geometries and can be used with a variety of materials, including metals and ceramics.
Inkjet Printing
Inkjet printing is a 2D printing technique that uses a printer to deposit conductive ink onto a substrate to create PCB traces and pads. This technique is well-suited for creating flexible and stretchable PCBs.
Advantages of PCB Additive Manufacturing
Faster Time-to-Market
One of the main advantages of PCB additive manufacturing is faster time-to-market. With traditional PCB manufacturing methods, prototyping and testing can be a time-consuming and expensive process. Additive manufacturing allows for rapid prototyping, reducing the time and cost associated with bringing a new product to market.
Traditional PCB Manufacturing | PCB Additive Manufacturing |
---|---|
Prototyping can take weeks or months | Prototyping can be done in days |
Tooling and setup costs can be high | No tooling or setup costs |
Limited design flexibility | High design flexibility |
Increased Design Flexibility
Another advantage of PCB additive manufacturing is increased design flexibility. With traditional PCB manufacturing methods, designers are limited by the capabilities of the manufacturing process. Additive manufacturing allows for the creation of complex geometries and shapes that would be difficult or impossible to achieve with traditional methods.
Traditional PCB Manufacturing | PCB Additive Manufacturing |
---|---|
Limited to 2D designs | Can create 3D designs |
Limited to standard materials | Can use a variety of materials |
Limited to standard trace and pad sizes | Can create custom trace and pad sizes |
Reduced Waste and Environmental Impact
PCB additive manufacturing also offers environmental benefits over traditional manufacturing methods. Additive manufacturing produces less waste, as material is only added where needed. This reduces the amount of material that ends up in landfills and the environmental impact of PCB manufacturing.
Traditional PCB Manufacturing | PCB Additive Manufacturing |
---|---|
Subtractive process produces waste material | Additive process only uses material where needed |
Uses hazardous chemicals for etching | Can use environmentally friendly materials |
Produces greenhouse gases during manufacturing | Reduced greenhouse gas emissions |
Cost Savings
PCB additive manufacturing can also offer cost savings over traditional manufacturing methods, especially for low-volume production runs. With traditional PCB manufacturing, there are often high setup and tooling costs that can make low-volume production runs cost-prohibitive. Additive manufacturing eliminates these costs, making it more cost-effective for low-volume production.
Traditional PCB Manufacturing | PCB Additive Manufacturing |
---|---|
High setup and tooling costs | No setup or tooling costs |
Cost-effective for high-volume production | Cost-effective for low-volume production |
Economies of scale decrease cost per unit | Cost per unit remains constant |
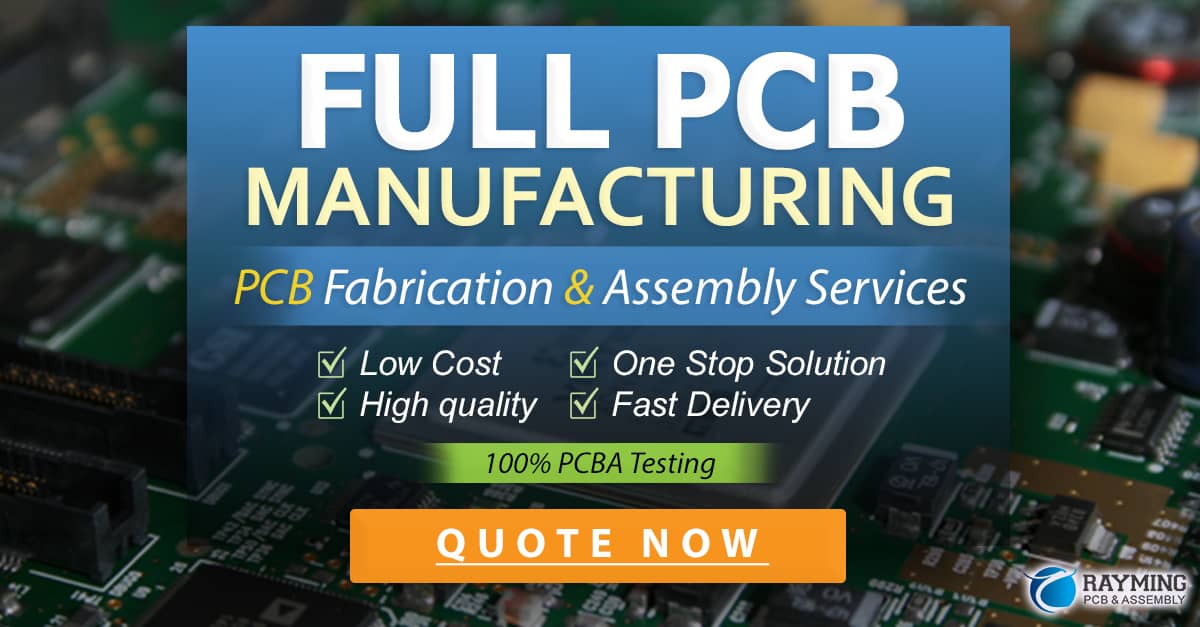
Challenges and Limitations of PCB Additive Manufacturing
While PCB additive manufacturing offers many benefits, there are also some challenges and limitations to consider.
Material Limitations
One of the main limitations of PCB additive manufacturing is the limited range of materials that can be used. Traditional PCB manufacturing can use a wide range of materials, including exotic materials like gold and silver. Additive manufacturing is currently limited to a smaller range of materials, although this is expected to improve as the technology advances.
Resolution and Accuracy
Another challenge with PCB additive manufacturing is achieving the same level of resolution and accuracy as traditional manufacturing methods. While additive manufacturing techniques like SLA can achieve high resolutions, they may not be able to match the resolution and accuracy of traditional methods for all applications.
Post-Processing Requirements
PCB additive manufacturing often requires post-processing steps to achieve the desired level of functionality and reliability. This can include cleaning, curing, and surface finishing, which can add time and cost to the manufacturing process.
Future of PCB Additive Manufacturing
Despite the challenges and limitations, PCB additive manufacturing is expected to continue to grow and evolve in the coming years. Some of the trends and developments to watch include:
Multi-Material Printing
One area of development in PCB additive manufacturing is multi-material printing. This involves using multiple materials in a single print job to create PCBs with embedded components and functionalities.
Hybrid Manufacturing
Hybrid manufacturing combines additive and subtractive manufacturing techniques to create PCBs with the benefits of both processes. This can involve using additive manufacturing to create complex geometries and then using subtractive manufacturing to achieve the desired level of accuracy and resolution.
Increased Adoption
As the technology continues to improve and the cost of equipment and materials decreases, it is expected that more companies will adopt PCB additive manufacturing for their electronics assembly needs. This will likely lead to further advancements and innovations in the field.
Frequently Asked Questions (FAQ)
-
What is PCB additive manufacturing?
PCB additive manufacturing is a process of creating printed circuit boards using 3D printing techniques, such as stereolithography (SLA), fused deposition modeling (FDM), and selective laser sintering (SLS). -
What are the benefits of PCB additive manufacturing?
The benefits of PCB additive manufacturing include faster prototyping, increased design flexibility, reduced waste and environmental impact, and cost savings for low-volume production runs. -
What materials can be used in PCB additive manufacturing?
PCB additive manufacturing currently has a limited range of materials compared to traditional PCB manufacturing methods. However, this is expected to improve as the technology advances. -
Can PCB additive manufacturing achieve the same level of resolution and accuracy as traditional methods?
While PCB additive manufacturing techniques like SLA can achieve high resolutions, they may not be able to match the resolution and accuracy of traditional methods for all applications. -
What is the future of PCB additive manufacturing?
The future of PCB additive manufacturing is expected to include developments in multi-material printing, hybrid manufacturing, and increased adoption as the technology improves and costs decrease.
Conclusion
PCB additive manufacturing is a promising technology that offers many benefits over traditional PCB manufacturing methods. From faster prototyping and increased design flexibility to reduced waste and cost savings, additive manufacturing has the potential to revolutionize the electronics industry.
While there are still challenges and limitations to overcome, the future of PCB additive manufacturing looks bright. As the technology continues to evolve and improve, it is likely that more and more companies will adopt additive manufacturing for their PCB assembly needs.
If you are considering PCB additive manufacturing for your electronics assembly, it is important to weigh the benefits and limitations and determine if it is the right choice for your specific application. With the right approach and expertise, PCB additive manufacturing can help you bring your products to market faster, more efficiently, and more cost-effectively.
0 Comments