Introduction to PCB environmental testing
Printed Circuit Boards (PCBs) are essential components in modern electronic devices, ranging from smartphones and computers to industrial equipment and aerospace systems. To ensure the reliability and longevity of these devices, PCBs must undergo rigorous testing to verify their ability to withstand various environmental conditions. This is where PCB environmental testing comes into play.
PCB environmental testing is a crucial process in the manufacturing of printed circuit boards. It involves subjecting PCBs to a series of tests that simulate real-world environmental conditions to assess their performance and durability. These tests are designed to identify potential issues and failures that may occur during the operational life of the PCB.
Importance of PCB Environmental Testing
PCB environmental testing is essential for several reasons:
-
Ensuring product reliability: By subjecting PCBs to various environmental stresses, manufacturers can identify and address potential weaknesses or defects that may affect the overall reliability of the final product.
-
Meeting industry standards: Many industries have specific standards and regulations that PCBs must meet to be deemed suitable for use. Environmental testing helps manufacturers ensure compliance with these standards.
-
Reducing warranty claims and recalls: By identifying and addressing potential issues during the testing phase, manufacturers can minimize the risk of product failures, warranty claims, and costly recalls.
-
Enhancing customer satisfaction: Reliable and durable products that can withstand real-world environmental conditions lead to increased customer satisfaction and brand loyalty.
Types of PCB Environmental Tests
There are several types of environmental tests that PCBs may undergo, depending on the intended application and industry standards. Some of the most common tests include:
1. Temperature Cycling Test
Temperature cycling tests expose PCBs to alternating high and low temperature extremes to simulate the thermal stresses experienced during normal operation. This test helps identify issues such as component failures, solder joint cracking, and delamination.
Parameter | Value |
---|---|
Temperature Range | -40°C to +125°C |
Number of Cycles | 100 to 1000 |
Dwell Time | 10 to 30 minutes |
2. Thermal Shock Test
Thermal shock tests subject PCBs to rapid temperature changes, typically by moving them between hot and cold chambers. This test is more severe than temperature cycling and helps identify issues related to thermal stress and material compatibility.
Parameter | Value |
---|---|
Temperature Range | -55°C to +125°C |
Transfer Time | 10 seconds or less |
Dwell Time | 30 minutes or more |
3. Humidity Test
Humidity tests expose PCBs to high humidity levels to assess their ability to withstand moisture-related issues such as corrosion, electrical shorts, and fungal growth.
Parameter | Value |
---|---|
Relative Humidity | 85% to 95% |
Temperature | 25°C to 65°C |
Duration | 96 hours or more |
4. Vibration Test
Vibration tests simulate the mechanical stresses that PCBs may experience during transportation or operation in environments with high vibration levels, such as vehicles or industrial equipment. This test helps identify issues such as component loosening, solder joint failures, and mechanical damage.
Parameter | Value |
---|---|
Frequency Range | 10 Hz to 2000 Hz |
Acceleration | 2 G to 20 G |
Duration | 1 hour to 24 hours |
5. Salt Spray Test
Salt spray tests expose PCBs to a corrosive salt solution to assess their resistance to corrosion and electrical shorting in harsh environments, such as coastal areas or marine applications.
Parameter | Value |
---|---|
Salt Concentration | 5% NaCl solution |
Temperature | 35°C |
Duration | 24 hours to 1000 hours |
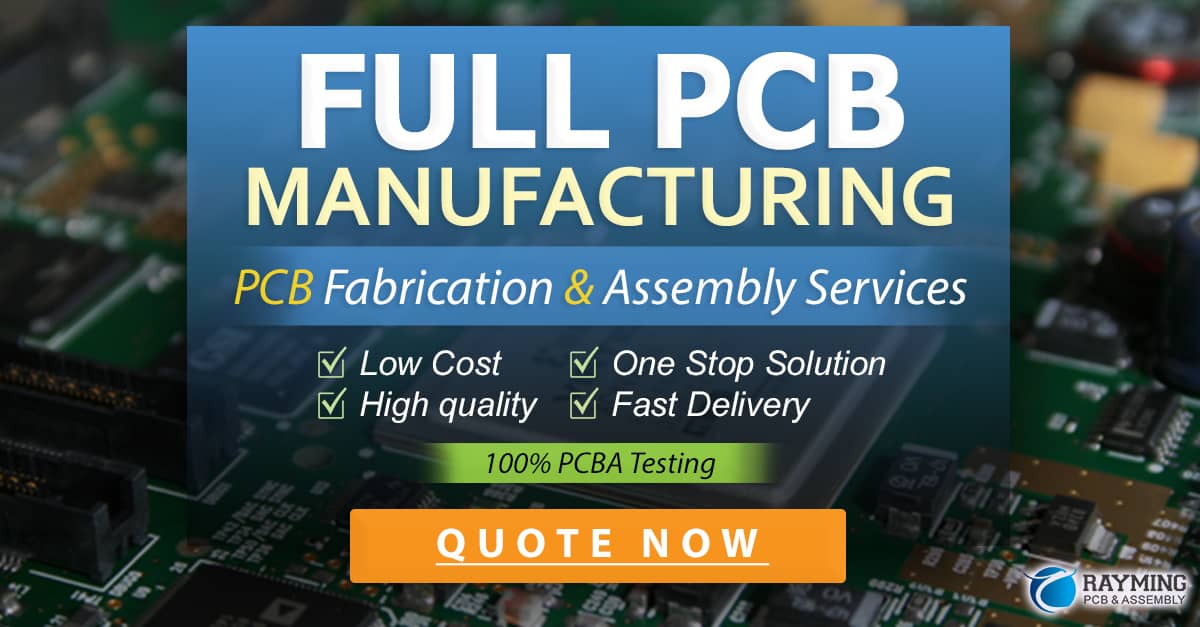
PCB Environmental Testing Process
The PCB environmental testing process typically involves the following steps:
-
Test planning: The manufacturer determines the appropriate environmental tests based on the intended application, industry standards, and customer requirements.
-
Sample preparation: A representative sample of PCBs is selected for testing. The sample size depends on the test requirements and statistical confidence levels.
-
Test setup: The test equipment and chambers are prepared according to the test specifications, and the PCBs are mounted or connected as required.
-
Test execution: The PCBs are subjected to the specified environmental conditions for the required duration, with continuous monitoring of the test parameters.
-
Post-test analysis: After the test, the PCBs are visually inspected and functionally tested to identify any defects or failures. The results are recorded and analyzed to determine if the PCBs meet the required performance criteria.
-
Reporting: A comprehensive test report is prepared, detailing the test conditions, results, and any observed failures or issues. This report is used to make decisions on product improvements or acceptance.
Benefits of PCB Environmental Testing
Investing in PCB environmental testing offers several benefits for manufacturers and end-users:
-
Improved product quality: By identifying and addressing potential issues early in the manufacturing process, environmental testing helps improve the overall quality and reliability of the final product.
-
Reduced development time and costs: Identifying and resolving issues during the testing phase can help reduce the time and costs associated with product development and redesign.
-
Enhanced market competitiveness: Products that have undergone rigorous environmental testing and meet industry standards are more likely to be competitive in the market and gain customer trust.
-
Compliance with regulations: Environmental testing helps manufacturers ensure compliance with industry-specific regulations and standards, avoiding potential legal and financial consequences.
Challenges in PCB Environmental Testing
While PCB environmental testing is essential, it also presents some challenges:
-
Cost: Environmental testing can be expensive, requiring specialized equipment, facilities, and trained personnel. Manufacturers must balance the cost of testing with the potential benefits and risks.
-
Time: Environmental tests can be time-consuming, especially for long-duration tests such as humidity or salt spray. This can impact product development timelines and time-to-market.
-
Interpretation of results: Analyzing and interpreting test results requires expertise and experience. Manufacturers must have skilled personnel who can properly assess the test data and make informed decisions.
-
Simulation limitations: While environmental tests aim to simulate real-world conditions, they may not perfectly replicate all possible scenarios. Manufacturers must consider the limitations of the tests and use appropriate safety factors in their designs.
Future Trends in PCB Environmental Testing
As technology advances and new applications emerge, PCB environmental testing is evolving to keep pace:
-
Accelerated testing: Techniques such as highly accelerated life testing (HALT) and highly accelerated stress screening (HASS) are gaining popularity as they allow for faster identification of potential issues and reduced testing time.
-
Simulation and modeling: Advances in computer-aided engineering (CAE) and finite element analysis (FEA) are enabling manufacturers to simulate environmental stresses and predict PCB performance, complementing physical testing.
-
In-situ monitoring: The integration of sensors and monitoring systems into PCBs allows for real-time monitoring of environmental conditions and performance during operation, providing valuable data for product improvement and maintenance.
-
Standardization: Efforts are being made to develop and harmonize international standards for PCB environmental testing, facilitating global trade and ensuring consistent product quality across different markets.
Conclusion
PCB environmental testing is a critical process in the manufacturing of printed circuit boards, ensuring their reliability, durability, and compliance with industry standards. By subjecting PCBs to various environmental stresses, manufacturers can identify and address potential issues early in the development cycle, leading to improved product quality, reduced warranty claims, and enhanced customer satisfaction.
As technology continues to evolve, PCB environmental testing must adapt to new challenges and opportunities. By embracing advanced testing techniques, simulation tools, and in-situ monitoring, manufacturers can stay ahead of the curve and deliver high-quality, reliable products that meet the demands of increasingly complex applications.
Frequently Asked Questions (FAQ)
-
What is the purpose of PCB environmental testing?
The purpose of PCB environmental testing is to assess the performance and durability of printed circuit boards under various environmental conditions, ensuring their reliability and compliance with industry standards. -
What are the most common types of PCB environmental tests?
The most common types of PCB environmental tests include temperature cycling, thermal shock, humidity, vibration, and salt spray tests. -
How long does PCB environmental testing take?
The duration of PCB environmental testing depends on the specific tests being performed and the required test conditions. Some tests, like vibration, may take a few hours, while others, like humidity or salt spray, can take several days or even weeks. -
Is PCB environmental testing mandatory?
While not always mandatory, PCB environmental testing is often required to meet industry standards and customer requirements. In some industries, such as aerospace or automotive, environmental testing is a critical part of the product validation process. -
How can manufacturers balance the cost and benefits of PCB environmental testing?
Manufacturers can balance the cost and benefits of PCB environmental testing by carefully selecting the most relevant tests based on the intended application and industry standards, optimizing sample sizes, and leveraging advanced testing techniques and simulation tools to reduce testing time and costs while ensuring product quality and reliability.
0 Comments