Introduction to PCB Assembly Guidelines for RF and Microwave Circuits
Printed Circuit Board (PCB) assembly for RF and microwave circuits requires careful consideration of various factors to ensure optimal performance, reliability, and manufacturability. As the demand for high-frequency applications continues to grow, it is crucial for engineers and designers to follow best practices when designing and assembling PCBs for these critical applications.
In this comprehensive article, we will explore the top design guidelines for RF and microwave PCB assembly, covering essential aspects such as material selection, layout techniques, component placement, and manufacturing considerations. By adhering to these guidelines, you can minimize signal integrity issues, reduce electromagnetic interference (EMI), and achieve robust and reliable PCB assemblies for your RF and microwave projects.
Key Considerations for RF and Microwave PCB Material Selection
Substrate Materials
Choosing the right substrate material is critical for RF and microwave PCB assembly. The substrate material should have the following properties:
- Low dielectric constant (Dk) to minimize signal delay and attenuation
- Low dissipation factor (Df) to reduce signal loss
- Stable Dk and Df over the operating frequency range and temperature
- Smooth surface finish to minimize conductor loss and signal distortion
Some commonly used substrate materials for RF and microwave PCBs include:
Material | Dielectric Constant (Dk) | Dissipation Factor (Df) | Typical Applications |
---|---|---|---|
Rogers RO4003C | 3.38 | 0.0027 | Wireless communications, radar, satellite |
Rogers RT/duroid 5880 | 2.20 | 0.0009 | High-frequency applications, military, aerospace |
Isola I-Tera MT40 | 3.45 | 0.0031 | 5G, automotive radar, high-speed digital |
Taconic RF-35 | 3.50 | 0.0018 | Broadband applications, RF amplifiers, filters |
Copper Foil Thickness
The choice of copper foil thickness is important for RF and microwave PCBs. Thinner copper foils (e.g., 0.5 oz or 17 µm) are preferred for high-frequency applications because they:
- Reduce skin effect losses
- Minimize conductor surface roughness
- Allow for finer trace widths and spacing
However, thicker copper foils (e.g., 1 oz or 35 µm) may be necessary for high-power applications or to improve thermal management.
PCB Layout Techniques for RF and Microwave Circuits
Transmission Line Design
Proper transmission line design is essential for maintaining signal integrity in RF and microwave PCBs. The two most common types of transmission lines used are:
-
Microstrip: Consists of a conductor trace on top of a dielectric substrate with a ground plane on the bottom. Microstrip is easier to fabricate but is more susceptible to EMI.
-
Stripline: Consists of a conductor trace embedded between two dielectric layers, with ground planes on top and bottom. Stripline offers better EMI shielding but is more challenging to fabricate.
When designing transmission lines, consider the following:
-
Characteristic impedance: Match the impedance of the transmission line to the source and load impedances (typically 50Ω) to minimize reflections and signal distortion.
-
Trace width and spacing: Use appropriate trace widths and spacing to achieve the desired characteristic impedance and minimize crosstalk.
-
Bends and transitions: Use smooth bends (e.g., chamfered or mitered) and gradual transitions to minimize discontinuities and reflections.
Ground Planes and Shielding
Proper grounding and shielding techniques are crucial for RF and microwave PCB assembly to minimize EMI and ensure signal integrity. Some best practices include:
-
Use continuous ground planes on adjacent layers to provide a low-impedance return path for high-frequency signals.
-
Implement ground stitching vias to connect ground planes on different layers and minimize ground bounce.
-
Use via fencing around sensitive signals to provide additional shielding and reduce crosstalk.
-
Incorporate electromagnetic bandgap (EBG) structures or defected ground structures (DGS) to suppress unwanted surface waves and improve isolation.
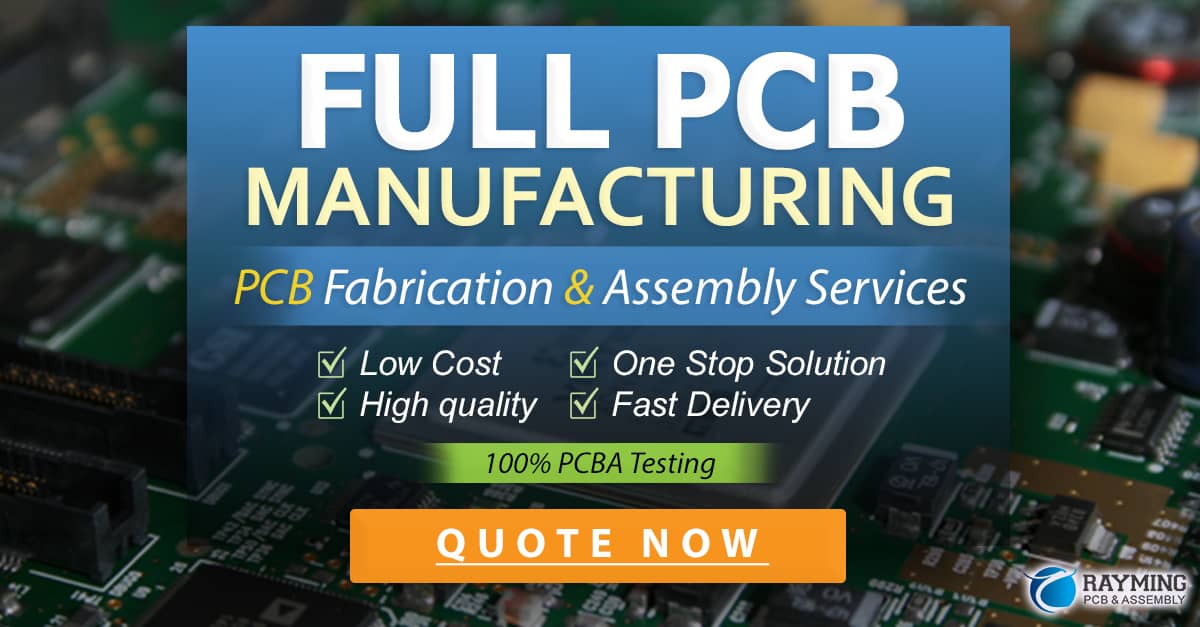
Component Placement and Routing Guidelines
Component Placement
Proper component placement is critical for RF and microwave PCB assembly to minimize signal path lengths, reduce parasitic effects, and improve manufacturability. Consider the following guidelines:
-
Place components as close as possible to their associated transmission lines and connectors to minimize signal path lengths and reflections.
-
Orient components to minimize coupling and crosstalk between adjacent signals.
-
Use symmetrical placement for differential signals to maintain signal balance and reduce common-mode noise.
-
Provide adequate spacing between components to facilitate assembly and rework processes.
Routing Guidelines
When routing RF and microwave PCBs, follow these guidelines to ensure signal integrity and manufacturability:
-
Route high-frequency signals on the top layer whenever possible to minimize via transitions and signal degradation.
-
Avoid routing high-frequency signals parallel to each other for extended distances to minimize crosstalk.
-
Use serpentine routing techniques to match signal path lengths for critical signals and maintain timing relationships.
-
Provide sufficient clearance around components and connectors to accommodate assembly tolerances and avoid signal interference.
Manufacturing Considerations for RF and Microwave PCB Assembly
Fabrication Tolerances
RF and microwave PCBs require tighter fabrication tolerances compared to standard PCBs to ensure consistent performance and reliability. Work closely with your PCB fabricator to specify the following tolerances:
- Trace width and spacing tolerances
- Dielectric thickness and uniformity tolerances
- Hole size and positioning tolerances
- Solder mask and silkscreen registration tolerances
Assembly Process
The assembly process for RF and microwave PCBs requires special attention to minimize signal degradation and ensure proper component attachment. Consider the following:
-
Use specialized soldering techniques, such as reflow soldering with a nitrogen atmosphere or vacuum soldering, to minimize oxidation and improve joint quality.
-
Implement automatic optical inspection (AOI) and X-ray inspection to detect assembly defects, such as misaligned components, bridging, or insufficient solder joints.
-
Perform thorough cleaning processes to remove flux residues and contaminants that can affect high-frequency performance.
-
Conduct rigorous testing and validation, including functional testing, RF parameter measurements, and environmental stress testing, to ensure the PCB assembly meets the required specifications.
Frequently Asked Questions (FAQ)
-
Q: What are the most critical factors to consider when selecting materials for RF and microwave PCB assembly?
A: The most critical factors include the dielectric constant (Dk), dissipation factor (Df), and their stability over the operating frequency range and temperature. It is also important to consider the surface finish and copper foil thickness to minimize losses and signal distortion. -
Q: How can I minimize crosstalk between high-frequency signals on my PCB?
A: To minimize crosstalk, use proper shielding techniques such as ground planes, via fencing, and electromagnetic bandgap (EBG) structures. Additionally, avoid routing high-frequency signals parallel to each other for extended distances and maintain sufficient spacing between components. -
Q: What are the benefits of using stripline transmission lines compared to microstrip?
A: Stripline transmission lines offer better EMI shielding and isolation compared to microstrip because the signal is embedded between two ground planes. However, stripline is more challenging to fabricate and may require additional design considerations. -
Q: Why is component placement critical for RF and microwave PCB assembly?
A: Proper component placement is essential to minimize signal path lengths, reduce parasitic effects, and improve manufacturability. By placing components close to their associated transmission lines and connectors, you can minimize reflections and signal degradation. -
Q: What specialized assembly processes are used for RF and microwave PCBs?
A: RF and microwave PCBs often require specialized soldering techniques, such as reflow soldering with a nitrogen atmosphere or vacuum soldering, to minimize oxidation and improve joint quality. Additionally, thorough cleaning processes and rigorous testing and validation are necessary to ensure the PCB assembly meets the required specifications.
Conclusion
Designing and assembling PCBs for RF and microwave applications requires careful consideration of various factors, including material selection, layout techniques, component placement, and manufacturing processes. By following the top design guidelines outlined in this article, you can ensure optimal performance, reliability, and manufacturability for your RF and microwave PCB assemblies.
Remember to work closely with your PCB fabricator and assembly partner to communicate your requirements and specifications clearly. Staying up-to-date with the latest industry standards and best practices will help you navigate the complexities of RF and microwave PCB design and assembly successfully.
By adhering to these guidelines and collaborating with experienced professionals, you can unlock the full potential of your RF and microwave applications and drive innovation in this rapidly evolving field.
0 Comments