Understanding Cable and Wire Harness Assembly
A cable and wire harness assembly is a group of cables or wires that are bundled together to transmit signals or electrical power. These assemblies are designed to simplify the installation process, reduce the risk of electrical failures, and improve the overall organization of the electrical system.
Components of a Cable and Wire Harness Assembly
A typical cable and wire harness assembly consists of the following components:
- Wires and cables
- Connectors
- Terminals
- Insulation materials
- Protective sleeves or conduits
- Labeling and identification tags
Key Considerations for Selecting Cable and Wire Harness Assembly
When selecting a cable and wire harness assembly for your final product, consider the following factors:
1. Application Requirements
The first step in selecting the right cable and wire harness assembly is to understand your application requirements. Consider the following aspects:
- Operating environment (temperature, humidity, vibration, etc.)
- Electrical requirements (voltage, current, frequency, etc.)
- Size and weight constraints
- Flexibility and bend radius requirements
- Shielding requirements (EMI/RFI protection)
2. Material Selection
The materials used in the cable and wire harness assembly play a crucial role in its performance and durability. Consider the following material properties:
- Conductor material (copper, aluminum, etc.)
- Insulation material (PVC, PE, PTFE, etc.)
- Jacket material (PVC, TPE, PUR, etc.)
- Flammability ratings (UL94V-0, UL94HB, etc.)
- Environmental resistance (UV, oil, chemicals, etc.)
Comparison of Common Insulation Materials
Material | Temperature Range | Dielectric Strength | Flexibility |
---|---|---|---|
PVC | -40°C to 105°C | Good | Good |
PE | -70°C to 90°C | Excellent | Excellent |
PTFE | -90°C to 260°C | Excellent | Fair |
3. Electrical Performance
Ensure that the cable and wire harness assembly meets your electrical performance requirements:
- Current carrying capacity (ampacity)
- Voltage rating
- Insulation resistance
- Dielectric strength
- Capacitance and inductance
4. Mechanical Performance
Consider the mechanical performance of the cable and wire harness assembly:
- Tensile strength
- Flexural strength
- Abrasion resistance
- Crush resistance
- Vibration and shock resistance
5. Connector Selection
Select connectors that are compatible with your application requirements:
- Connector type (circular, rectangular, etc.)
- Number of pins or contacts
- Contact material and plating
- Locking mechanism
- Sealing (IP rating)
6. Standards and Certifications
Ensure that the cable and wire harness assembly complies with relevant industry standards and certifications:
- UL, CSA, CE, RoHS, REACH, etc.
- Military specifications (MIL-SPEC)
- Automotive standards (USCAR, SAE, etc.)
- Aerospace standards (AS, EN, etc.)
7. Manufacturing Process
Consider the manufacturing process of the cable and wire harness assembly:
- Automated or manual assembly
- Crimping, soldering, or welding techniques
- Quality control and testing procedures
- Lead time and production capacity
8. Cost and Supplier Selection
Finally, consider the cost and supplier selection:
- Material and component costs
- Tooling and setup costs
- Minimum order quantity (MOQ)
- Supplier reputation and experience
- Delivery time and logistics
- After-sales support and warranty
Best Practices for Cable and Wire Harness Assembly Design
To optimize the performance of your cable and wire harness assembly, follow these best practices:
- Conduct a thorough application analysis
- Use appropriate wire gauges and insulation materials
- Minimize the number of connectors and splices
- Ensure proper strain relief and bend radius
- Use appropriate shielding and grounding techniques
- Implement proper labeling and identification
- Perform rigorous testing and quality control
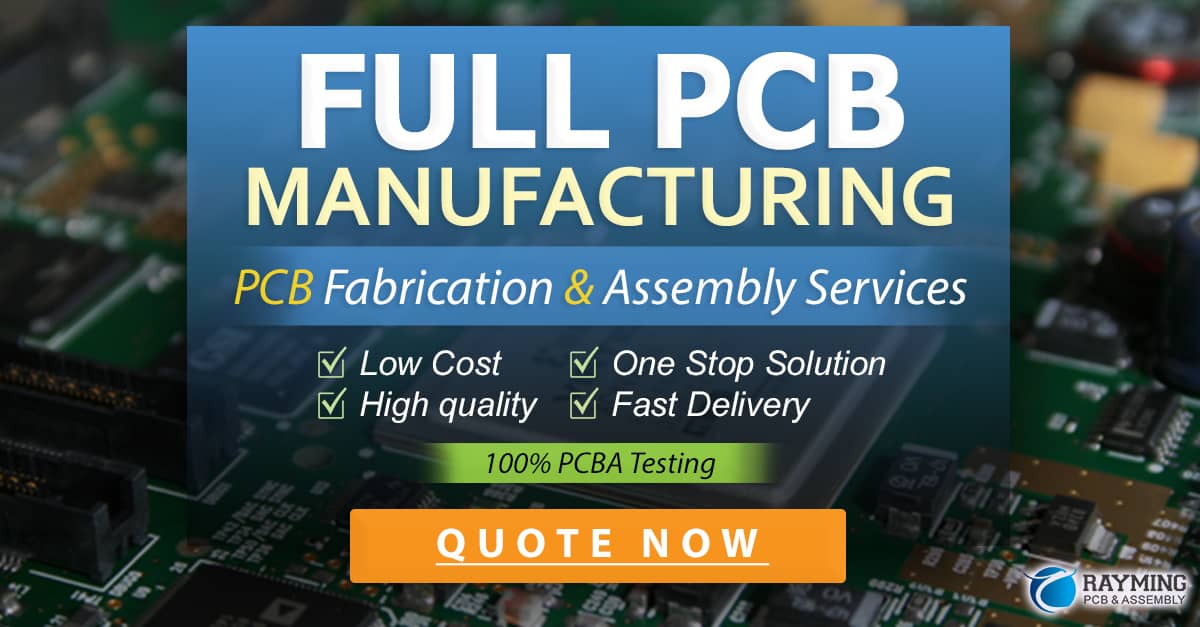
Frequently Asked Questions (FAQ)
- What is the difference between a cable and a wire harness assembly?
-
A cable typically refers to a single insulated conductor or a group of insulated conductors bundled together. A wire harness assembly is a more complex assembly that includes multiple cables, wires, connectors, and other components designed for a specific application.
-
How do I determine the appropriate wire gauge for my application?
-
The appropriate wire gauge depends on factors such as the required current carrying capacity (ampacity), voltage drop, and mechanical strength. Refer to industry standards and charts, such as the American Wire Gauge (AWG) chart, to select the suitable wire gauge for your application.
-
What is the purpose of shielding in a cable and wire harness assembly?
-
Shielding is used to protect the cable and wire harness assembly from electromagnetic interference (EMI) and radio frequency interference (RFI). It helps to minimize signal distortion, crosstalk, and noise, ensuring the integrity of the transmitted signals.
-
How can I ensure the reliability and durability of my cable and wire harness assembly?
-
To ensure reliability and durability, select high-quality materials, use appropriate manufacturing techniques (e.g., crimping, soldering), implement proper strain relief and bend radius, and perform rigorous testing and quality control. Additionally, consider the operating environment and use appropriate protection measures, such as jacketing and sealing.
-
What are the common challenges in cable and wire harness assembly design, and how can I overcome them?
- Common challenges include space constraints, weight reduction, electrical performance, and environmental factors. To overcome these challenges, use 3D modeling and simulation tools for optimizing the design, select appropriate materials and components, implement best practices for manufacturing and assembly, and collaborate closely with experienced suppliers and engineers.
Conclusion
Selecting the right cable and wire harness assembly is essential for ensuring the optimal performance, reliability, and cost-effectiveness of your final product. By considering factors such as application requirements, material selection, electrical and mechanical performance, connector selection, standards and certifications, manufacturing process, and cost and supplier selection, you can make an informed decision and enhance the overall quality of your product.
Remember to follow best practices in cable and wire harness assembly design, such as conducting thorough application analysis, using appropriate wire gauges and insulation materials, minimizing connectors and splices, ensuring proper strain relief and bend radius, implementing shielding and grounding techniques, and performing rigorous testing and quality control.
By partnering with experienced suppliers and engineers and staying up-to-date with the latest industry trends and technologies, you can overcome common challenges and create a high-performance cable and wire harness assembly that meets your specific application requirements.
0 Comments