What is PCB Warpage?
PCB warpage refers to the undesirable bending, twisting or distortion of a printed circuit board (PCB) from its intended flat shape. Warpage can occur during various stages of the PCB assembly process, such as during reflow soldering, hot air solder leveling (HASL), or even storage. Excessive warpage can lead to issues like poor component placement, solder joint defects, and reduced reliability of the final product.
Causes of PCB Warpage
There are several factors that can contribute to PCB warpage during the assembly process:
1. Thermal Stress
One of the primary causes of PCB warpage is thermal stress. During the reflow soldering process, PCBs are exposed to high temperatures (typically around 230-260°C) to melt the solder and form electrical connections between components and the board. However, this thermal exposure can cause the PCB substrate to expand and contract unevenly, leading to warpage.
The severity of thermal stress-induced warpage depends on factors such as:
– The coefficient of thermal expansion (CTE) mismatch between the PCB substrate, copper layers, and components
– The thickness and layout of the copper traces
– The placement and density of components on the board
2. Moisture Absorption
PCBs can absorb moisture from the environment during storage or handling. If a moisture-laden PCB is subjected to high temperatures during reflow soldering, the rapid evaporation of the absorbed moisture can cause localized swelling and warpage.
The risk of moisture-induced warpage is higher for PCBs with:
– Hygroscopic substrates (e.g., FR-4)
– Thicker boards
– Higher layer counts
– Denser component placement
3. Mechanical Stress
Mechanical stress can also contribute to PCB warpage. This can occur due to:
– Improper handling or storage of PCBs
– Uneven clamping force during the assembly process
– Misalignment of the PCB in the assembly fixtures
– Unbalanced copper distribution in the PCB stackup
4. Design-Related Issues
Certain PCB design choices can make the board more susceptible to warpage:
– Asymmetric copper distribution between layers
– Large, unsupported copper planes
– High aspect ratio (length-to-width) of the board
– Insufficient thickness of the PCB substrate
Prevention Measures for PCB Warpage
To minimize the risk of PCB warpage during the assembly process, consider the following prevention measures:
1. Design Optimization
- Balance copper distribution across layers to minimize CTE mismatches
- Use symmetric stackups whenever possible
- Avoid large, unsupported copper planes
- Optimize component placement to distribute thermal stress evenly
- Consider using lower-CTE substrates for high-reliability applications
2. Moisture Management
- Store PCBs in moisture-barrier bags with desiccants
- Bake PCBs before assembly to remove absorbed moisture
- Maintain proper humidity control in the storage and assembly environment
3. Process Control
- Use appropriate reflow soldering profiles with controlled ramp rates and peak temperatures
- Ensure proper alignment and clamping of PCBs in assembly fixtures
- Implement suitable cooling methods to minimize thermal shock after reflow
- Monitor and control the HASL process parameters to minimize thermal stress
4. Material Selection
- Choose PCB substrates with lower CTE and higher glass transition temperature (Tg)
- Use low-stress soldermask and conformal coatings
- Select components with matched CTE to the PCB substrate
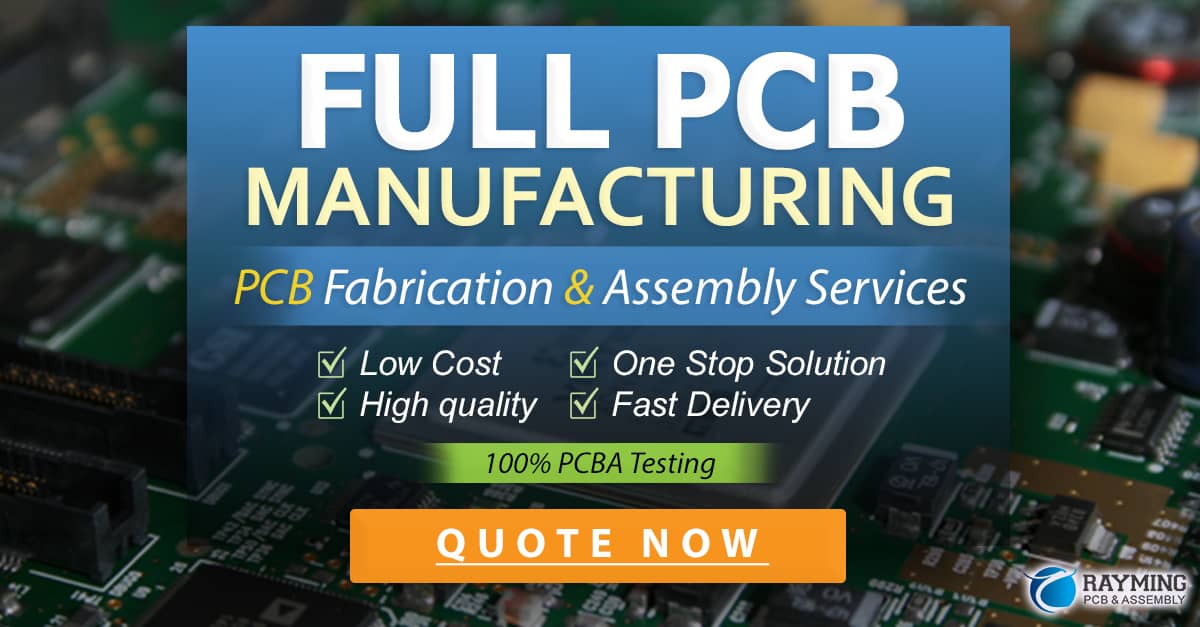
Warpage Measurement and Inspection
To ensure that PCBs meet the required flatness specifications, it is essential to measure and inspect for warpage at various stages of the assembly process. Some common methods include:
Method | Description | Advantages | Limitations |
---|---|---|---|
Shadow Moiré | Projects a grid pattern onto the PCB surface to detect warpage | Non-contact, fast, suitable for large-area measurement | Limited accuracy, sensitive to surface finish |
Laser Scanning | Uses a laser sensor to scan the PCB surface and create a 3D map | High accuracy, suitable for complex geometries | Slower than shadow moiré, higher cost |
Coordinate Measuring Machine (CMM) | Measures the PCB surface using a probe to create a 3D map | High accuracy, suitable for specific points of interest | Slow, contact-based, higher cost |
Regular warpage measurement and inspection can help identify issues early in the assembly process, allowing for timely corrective actions and process improvements.
Frequently Asked Questions (FAQ)
1. What is the acceptable level of PCB warpage?
The acceptable level of PCB warpage depends on the specific application and the component types used. Generally, the industry standard for maximum allowable warpage is 0.75% of the diagonal length of the PCB. However, some high-precision applications may require tighter flatness tolerances.
2. Can PCB warpage be corrected after assembly?
In most cases, PCB warpage cannot be easily corrected after assembly without risking damage to the components or solder joints. Prevention through proper design, material selection, and process control is the best approach.
3. How does the PCB thickness affect warpage?
Thicker PCBs are generally less susceptible to warpage due to their increased rigidity. However, thicker boards may be more prone to moisture-induced warpage if not properly stored and handled.
4. What is the impact of PCB warpage on solder joint reliability?
PCB warpage can lead to uneven solder joint formation, resulting in weak or open connections. This can reduce the reliability and longevity of the assembled product, especially under thermal cycling or mechanical stress conditions.
5. How can PCB warpage be prevented during the HASL process?
To minimize warpage during the HASL process, ensure that the PCB is properly supported and clamped to prevent bending. Control the immersion time and temperature to minimize thermal shock, and allow for gradual cooling after the process. Additionally, consider using a lead-free HASL process, which typically operates at lower temperatures compared to leaded HASL.
0 Comments