Introduction to PCB Routing
Printed Circuit Board (PCB) routing is a crucial step in the design and manufacturing of electronic devices. It involves the placement and connection of electronic components on a PCB to ensure proper functionality, reliability, and performance. Effective PCB routing practices can help minimize signal integrity issues, reduce electromagnetic interference (EMI), and improve the overall quality of the final product.
In this article, we will discuss the top 10 best PCB routing practices that every designer should follow to achieve optimal results. By adhering to these guidelines, you can create PCBs that are efficient, reliable, and cost-effective.
1. Plan Your Layout
1.1 Create a Schematic
Before starting the PCB routing process, it is essential to create a detailed schematic of your circuit. A schematic is a graphical representation of the electronic components and their interconnections. It helps you visualize the logical flow of the circuit and identify potential issues early in the design process.
1.2 Define Component Placement
Once you have a schematic, the next step is to define the placement of components on the PCB. Consider factors such as component size, thermal requirements, and signal integrity when determining the optimal placement. Group related components together and minimize the distance between them to reduce signal delays and improve performance.
1.3 Consider Manufacturing Constraints
When planning your PCB layout, it is crucial to consider the manufacturing constraints imposed by your chosen fabrication process. These constraints may include minimum trace width, spacing requirements, and drill sizes. Consulting with your PCB manufacturer early in the design process can help you avoid potential manufacturing issues and ensure a smooth production process.
2. Use a Grid System
2.1 Benefits of Using a Grid
Using a grid system when routing your PCB can help you maintain consistency and alignment throughout the design. It allows you to snap traces and components to predefined grid points, making it easier to create a neat and organized layout. A grid system also helps you adhere to the manufacturing constraints and ensures that your design is compatible with the fabrication process.
2.2 Choosing the Right Grid Size
The grid size you choose depends on the complexity of your design and the manufacturing constraints. A smaller grid size allows for more precise placement and routing but may increase the design time and complexity. On the other hand, a larger grid size can simplify the routing process but may result in a less optimized layout. It is important to strike a balance between precision and efficiency when selecting your grid size.
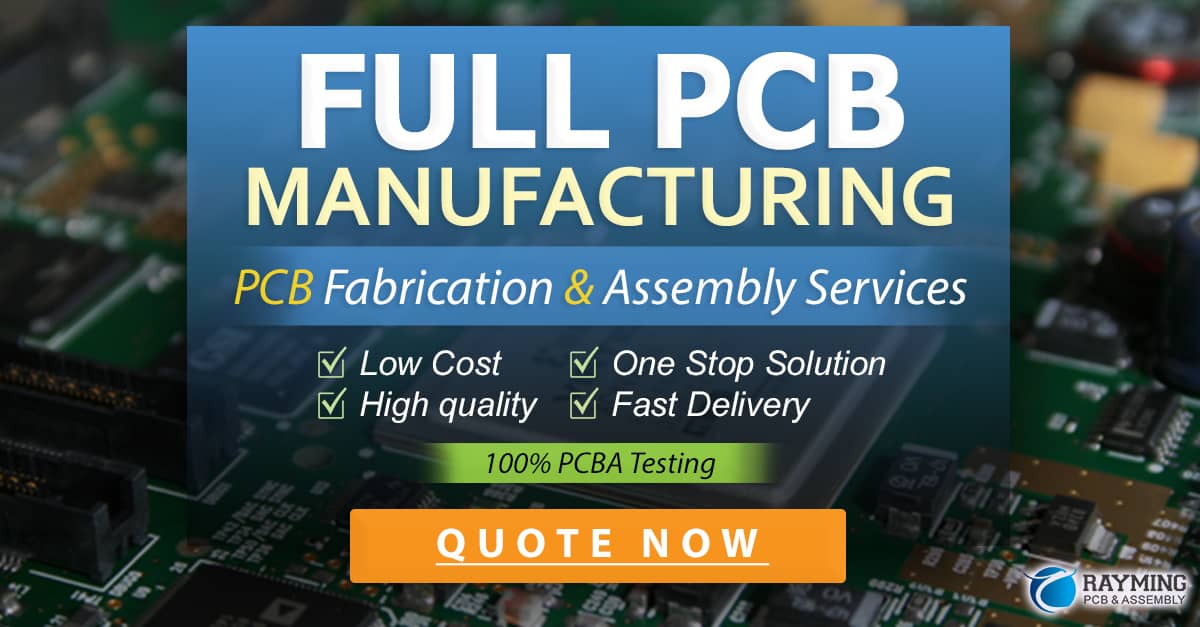
3. Route Power and Ground Planes
3.1 Importance of Power and Ground Planes
Power and ground planes play a crucial role in maintaining signal integrity and reducing EMI in PCBs. They provide a low-impedance path for power distribution and help minimize voltage drops across the board. By dedicating entire layers to power and ground, you can create a stable reference plane for your signals and reduce the risk of signal degradation.
3.2 Splitting Power and Ground Planes
In some cases, it may be necessary to split power and ground planes to accommodate different voltage levels or to isolate sensitive circuits. When splitting planes, it is important to maintain adequate spacing between the split regions to prevent signal coupling and crosstalk. Use appropriate stitching capacitors to provide a low-impedance path between the split planes and minimize voltage differences.
4. Follow Signal Integrity Guidelines
4.1 Minimize Trace Length
To maintain signal integrity, it is important to minimize the length of traces on your PCB. Longer traces are more susceptible to signal degradation, crosstalk, and EMI. When routing signals, take the shortest possible path between the source and destination components. If longer traces are unavoidable, consider using techniques such as signal conditioning or impedance matching to mitigate signal integrity issues.
4.2 Match Trace Impedance
Matching the impedance of traces is critical for high-speed signals and long traces. Impedance mismatches can cause signal reflections, leading to signal distortion and degradation. To match trace impedance, you need to consider factors such as trace width, thickness, and the dielectric constant of the PCB material. Use impedance calculators or simulation tools to determine the optimal trace geometry for your desired impedance.
4.3 Avoid Sharp Corners
Sharp corners in traces can cause signal reflections and create impedance discontinuities. When routing traces, use smooth curves or 45-degree angles instead of sharp 90-degree corners. This helps maintain a consistent impedance along the trace and reduces the risk of signal integrity issues.
5. Minimize Crosstalk
5.1 Understanding Crosstalk
Crosstalk occurs when signals from one trace interfere with signals on adjacent traces. It is caused by electromagnetic coupling between the traces and can lead to signal distortion and errors. Crosstalk is particularly problematic in high-speed designs where traces are closely spaced and signals have fast rise and fall times.
5.2 Techniques to Minimize Crosstalk
To minimize crosstalk, you can employ several techniques:
- Increase the spacing between traces: By increasing the distance between traces, you can reduce the electromagnetic coupling and minimize crosstalk.
- Use guard traces: Place grounded guard traces between sensitive signal traces to provide shielding and reduce crosstalk.
- Route signals on different layers: By routing signals on different layers of the PCB, you can reduce the coupling between traces and minimize crosstalk.
- Use differential signaling: Differential signaling techniques, such as LVDS or CML, can help cancel out the effects of crosstalk by using complementary signals.
6. Consider EMI and EMC
6.1 Understanding EMI and EMC
Electromagnetic Interference (EMI) refers to the unwanted electromagnetic energy that can interfere with the operation of electronic devices. Electromagnetic Compatibility (EMC) is the ability of a device to function properly in its electromagnetic environment without causing interference to other devices. When designing PCBs, it is important to consider both EMI and EMC to ensure the reliability and performance of your product.
6.2 Techniques to Reduce EMI
To reduce EMI in your PCB design, you can employ the following techniques:
- Use proper grounding techniques: Ensure that your PCB has a solid ground plane and use appropriate grounding techniques, such as star grounding or multi-point grounding, to minimize ground loops and reduce EMI.
- Implement shielding: Use shielding techniques, such as metal enclosures or shielding gaskets, to contain electromagnetic emissions and prevent interference with other devices.
- Filter power supplies: Use power supply filters to suppress high-frequency noise and prevent it from propagating throughout the PCB.
- Minimize current loops: Minimize the area of current loops by keeping signal traces and return paths close together. This reduces the magnetic field generated by the current loop and minimizes EMI.
7. Optimize Via Placement
7.1 Understanding Vias
Vias are conductive holes that allow signals to pass through different layers of a PCB. They are essential for connecting components and routing signals in multi-layer designs. However, vias can also introduce signal integrity issues, such as impedance discontinuities and reflections, if not used properly.
7.2 Best Practices for Via Placement
To optimize via placement and minimize signal integrity issues, follow these best practices:
- Minimize the number of vias: Use the minimum number of vias necessary to route your signals. Each via introduces a small amount of inductance and capacitance, which can affect signal integrity.
- Place vias near the source: Place vias as close as possible to the source component to minimize the trace length and reduce signal reflections.
- Use appropriate via sizes: Choose via sizes that are appropriate for your signal frequencies and current requirements. Larger vias have lower inductance and resistance but may consume more board space.
- Avoid vias in high-speed signals: If possible, avoid placing vias in high-speed signal paths. If vias are necessary, use techniques such as via stitching or back-drilling to minimize the stub length and reduce reflections.
8. Route Differential Pairs
8.1 Understanding Differential Signaling
Differential signaling is a technique where two complementary signals are transmitted over a pair of traces. The signals are equal in magnitude but opposite in polarity, allowing them to cancel out common-mode noise and reduce EMI. Differential signaling is commonly used in high-speed interfaces, such as USB, PCIe, and HDMI.
8.2 Routing Differential Pairs
When routing differential pairs, it is important to maintain the signal integrity and minimize any imbalances between the two traces. Follow these guidelines for effective differential pair routing:
- Match trace lengths: Ensure that the lengths of the two traces in a differential pair are closely matched. Any length mismatch can introduce skew and degrade the signal quality.
- Maintain consistent spacing: Keep the spacing between the traces in a differential pair consistent throughout the route. Variations in spacing can cause impedance mismatches and signal reflections.
- Avoid sharp bends: Use smooth curves or 45-degree angles when routing differential pairs to maintain a consistent impedance and minimize signal distortion.
- Consider coupling: Differential pairs require a certain amount of coupling between the traces to maintain signal integrity. Use appropriate trace spacing and geometry to achieve the desired coupling level.
9. Implement Thermal Management
9.1 Importance of Thermal Management
Thermal management is crucial in PCB design to ensure the reliable operation and longevity of electronic components. Overheating can lead to performance degradation, reduced reliability, and even component failure. Proper thermal management techniques help dissipate heat effectively and maintain the temperature of components within their specified operating ranges.
9.2 Thermal Management Techniques
To implement effective thermal management in your PCB design, consider the following techniques:
- Use thermal vias: Place thermal vias near power-dissipating components to provide a low-resistance path for heat transfer to the PCB’s ground plane or dedicated thermal layers.
- Incorporate heatsinks: Attach heatsinks to components that generate significant heat to increase the surface area for heat dissipation and improve cooling efficiency.
- Optimize component placement: Place temperature-sensitive components away from heat-generating components to minimize thermal interactions and ensure adequate cooling.
- Use thermal interface materials: Apply thermal interface materials, such as thermal pads or thermal adhesives, between components and heatsinks to enhance heat transfer and reduce thermal resistance.
10. Perform Design Review and Verification
10.1 Importance of Design Review
Before finalizing your PCB design, it is essential to perform a thorough design review and verification process. This step helps identify potential issues, such as signal integrity problems, manufacturing constraints, or thermal concerns, and allows you to make necessary corrections before sending the design for fabrication.
10.2 Design Review Checklist
When conducting a design review, use the following checklist as a guide:
- Schematic review: Verify that the schematic accurately represents the intended circuit and that all components and connections are correct.
- Layout review: Check the PCB layout for proper component placement, routing, and adherence to design rules and manufacturing constraints.
- Signal integrity analysis: Perform signal integrity simulations to ensure that critical signals meet the required timing and quality parameters.
- Thermal analysis: Conduct thermal simulations to verify that the PCB and components operate within their specified temperature ranges.
- Manufacturing review: Consult with your PCB manufacturer to ensure that your design meets their fabrication capabilities and requirements.
Frequently Asked Questions (FAQ)
1. What is the importance of using a grid system in PCB routing?
Using a grid system in PCB routing helps maintain consistency and alignment throughout the design. It allows you to snap traces and components to predefined grid points, making it easier to create a neat and organized layout. A grid system also helps you adhere to manufacturing constraints and ensures compatibility with the fabrication process.
2. How can I minimize crosstalk in my PCB design?
To minimize crosstalk in your PCB design, you can employ techniques such as increasing the spacing between traces, using guard traces, routing signals on different layers, and implementing differential signaling. These techniques help reduce electromagnetic coupling between traces and minimize the effects of crosstalk.
3. What are the benefits of using power and ground planes in PCB routing?
Power and ground planes provide a low-impedance path for power distribution and help minimize voltage drops across the PCB. They create a stable reference plane for signals and reduce the risk of signal degradation. By dedicating entire layers to power and ground, you can improve signal integrity and reduce EMI in your PCB design.
4. How can I optimize via placement in my PCB layout?
To optimize via placement, minimize the number of vias used, place vias near the source component, choose appropriate via sizes, and avoid placing vias in high-speed signal paths. If vias are necessary in high-speed signals, use techniques such as via stitching or back-drilling to minimize stub lengths and reduce reflections.
5. Why is thermal management important in PCB design?
Thermal management is crucial in PCB design to ensure the reliable operation and longevity of electronic components. Overheating can lead to performance degradation, reduced reliability, and even component failure. Proper thermal management techniques, such as using thermal vias, heatsinks, and optimizing component placement, help dissipate heat effectively and maintain the temperature of components within their specified operating ranges.
Conclusion
Effective PCB routing practices are essential for creating reliable, high-performance electronic devices. By following the top 10 best practices discussed in this article, you can improve signal integrity, reduce EMI, and optimize your PCB design for manufacturing and reliability.
Remember to plan your layout carefully, use a grid system, route power and ground planes, follow signal integrity guidelines, minimize crosstalk, consider EMI and EMC, optimize via placement, route differential pairs, implement thermal management, and perform thorough design reviews and verification.
By adhering to these guidelines and continuously refining your PCB routing skills, you can create PCBs that meet the highest standards of quality and functionality.
0 Comments