Introduction
Printed circuit boards (PCBs) are essential components in nearly all modern electronic devices. As technology continues to advance at a rapid pace, PCB Manufacturing Trends are constantly evolving to keep up with the demands of the industry. Staying informed about these trends can help you save time and energy when designing and manufacturing PCBs.
In this article, we will explore the latest PCB manufacturing trends, including advanced materials, miniaturization, 3D printing, and more. We will also discuss how these trends can help streamline your PCB design and manufacturing process, ultimately saving you time and energy.
Advanced Materials in PCB Manufacturing
One of the most significant trends in PCB manufacturing is the use of advanced materials. These materials offer improved performance, reliability, and durability compared to traditional PCB materials. Some of the most popular advanced materials used in PCB manufacturing include:
High-Frequency Materials
High-frequency PCB materials are designed to support high-speed data transmission and minimize signal loss. These materials typically have a low dielectric constant and low loss tangent, which allows for faster signal propagation and reduced signal attenuation. Some common high-frequency materials include:
- Rogers RO4000 series
- Isola IS680
- Taconic RF-35
Flexible PCB Materials
Flexible PCBs are becoming increasingly popular due to their ability to conform to various shapes and sizes. These PCBs are made using flexible substrates, such as polyimide or polyester, which can be bent, folded, or rolled without damaging the circuit. Flexible PCBs are commonly used in wearable devices, medical equipment, and aerospace applications.
Thermal Management Materials
As electronic devices become more powerful and compact, thermal management becomes a critical concern. PCB materials with high thermal conductivity can help dissipate heat more effectively, preventing component failure and extending the lifespan of the device. Some thermal management materials used in PCB manufacturing include:
- Aluminum core PCBs
- Copper core PCBs
- Ceramic substrate PCBs
Material | Thermal Conductivity (W/mK) |
---|---|
FR-4 | 0.3 |
Aluminum | 205 |
Copper | 385 |
Ceramic | 20-30 |
Miniaturization and High-Density Interconnect (HDI) PCBs
Another significant trend in PCB manufacturing is miniaturization. As electronic devices become smaller and more compact, PCBs must also shrink in size while maintaining or improving functionality. High-Density Interconnect (HDI) PCBs are designed to accommodate this need for miniaturization.
What are HDI PCBs?
HDI PCBs are characterized by their high wiring density, fine line width and spacing, and small via sizes. These features allow for more components to be placed on a smaller PCB surface area, enabling the creation of compact, high-performance electronic devices.
Benefits of HDI PCBs
- Reduced PCB size and weight
- Improved signal integrity
- Higher component density
- Enhanced thermal management
- Lower power consumption
HDI PCB Design Considerations
Designing HDI PCBs requires careful consideration of several factors, including:
- Via types and sizes
- Line width and spacing
- Pad sizes and shapes
- Layer stackup
- Signal integrity analysis
HDI PCB Feature | Typical Dimensions |
---|---|
Line width/spacing | 50-100 µm |
Via diameter | 50-200 µm |
Via pad diameter | 100-400 µm |
Layer count | 6-24 |
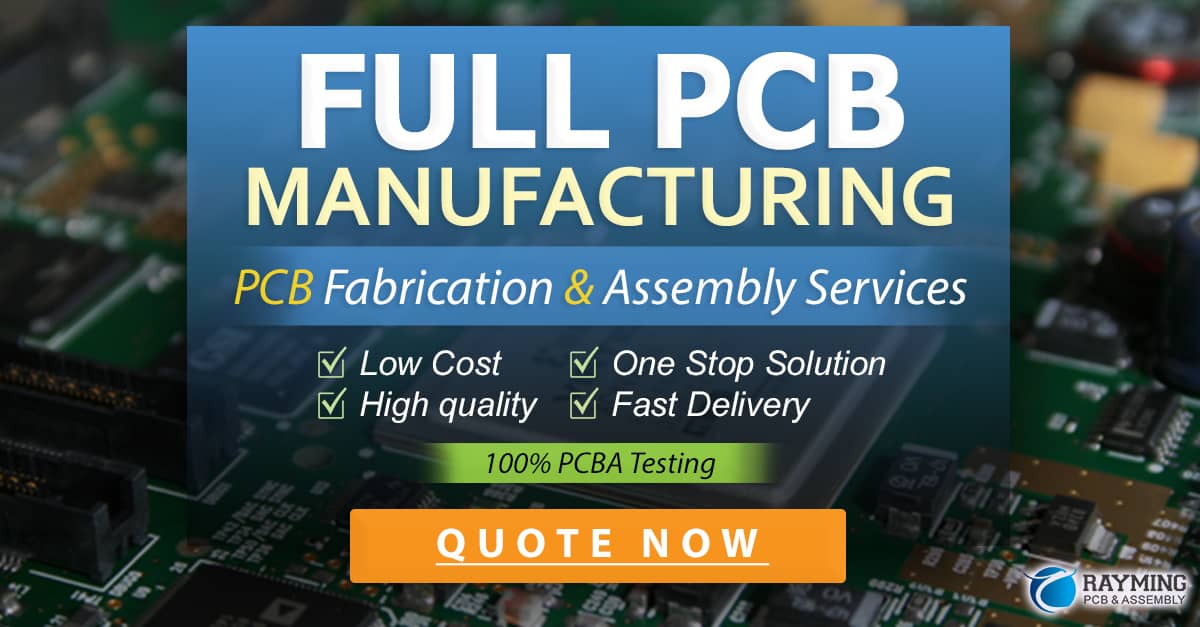
3D Printing in PCB Manufacturing
3D printing, also known as additive manufacturing, is a rapidly growing trend in PCB manufacturing. This technology allows for the creation of complex, three-dimensional PCB structures that would be difficult or impossible to achieve with traditional manufacturing methods.
Advantages of 3D Printing in PCB Manufacturing
- Rapid prototyping and shorter lead times
- Increased design flexibility
- Reduced waste and material consumption
- Ability to create complex, non-planar structures
- Cost-effective for low-volume production
3D Printing Technologies for PCBs
Several 3D printing technologies are used in PCB manufacturing, including:
- Fused Deposition Modeling (FDM)
- Stereolithography (SLA)
- Selective Laser Sintering (SLS)
- Inkjet Printing
Each technology has its own advantages and limitations, and the choice of technology depends on the specific requirements of the PCB design.
Automation and Industry 4.0 in PCB Manufacturing
Automation and Industry 4.0 technologies are transforming the PCB manufacturing landscape. These technologies aim to improve efficiency, reduce costs, and enhance product quality through the integration of smart machines, real-time data analytics, and cloud computing.
Benefits of Automation in PCB Manufacturing
- Increased productivity and throughput
- Reduced labor costs
- Improved product quality and consistency
- Real-time process monitoring and control
- Predictive maintenance and reduced downtime
Industry 4.0 Technologies in PCB Manufacturing
Industry 4.0 technologies leverage the power of data, connectivity, and automation to create intelligent, self-optimizing manufacturing systems. Some of the key Industry 4.0 technologies used in PCB manufacturing include:
- Industrial Internet of Things (IIoT)
- Big Data analytics
- Machine learning and artificial intelligence
- Cloud computing
- Cybersecurity
Technology | Application in PCB Manufacturing |
---|---|
IIoT | Real-time process monitoring and control |
Big Data analytics | Predictive maintenance and quality control |
Machine learning | Automated optical inspection (AOI) |
Cloud computing | Collaborative design and remote access |
Cybersecurity | Protecting sensitive data and intellectual property |
Environmental Sustainability in PCB Manufacturing
As environmental concerns continue to grow, PCB manufacturers are increasingly focusing on sustainable practices and eco-friendly materials. This trend not only helps protect the environment but also enables companies to comply with stringent regulations and meet customer demands for greener products.
Eco-Friendly PCB Materials
Some eco-friendly PCB materials include:
- Halogen-free laminates
- Lead-free solders
- Biodegradable substrate materials
- Recycled copper foils
These materials help reduce the environmental impact of PCB manufacturing by minimizing the use of hazardous substances and promoting recyclability.
Sustainable Manufacturing Practices
PCB manufacturers can adopt several sustainable practices to reduce their environmental footprint, such as:
- Implementing energy-efficient equipment and processes
- Optimizing resource consumption and waste reduction
- Recycling and reusing materials whenever possible
- Adopting green chemistry principles
- Obtaining environmental certifications (e.g., ISO 14001, EMAS)
Frequently Asked Questions (FAQ)
1. What are the benefits of using advanced materials in PCB manufacturing?
Advanced materials offer several benefits, including improved performance, reliability, and durability. High-frequency materials enable faster signal propagation and reduced signal loss, while flexible materials allow for the creation of PCBs that can conform to various shapes and sizes. Thermal management materials help dissipate heat more effectively, preventing component failure and extending device lifespan.
2. How do HDI PCBs enable miniaturization in electronic devices?
HDI PCBs feature high wiring density, fine line width and spacing, and small via sizes, allowing for more components to be placed on a smaller PCB surface area. This enables the creation of compact, high-performance electronic devices while maintaining or improving functionality.
3. What are the advantages of using 3D printing in PCB manufacturing?
3D printing offers several advantages in PCB manufacturing, including rapid prototyping, increased design flexibility, reduced waste and material consumption, and the ability to create complex, non-planar structures. It is also cost-effective for low-volume production.
4. How does automation benefit PCB manufacturing?
Automation in PCB manufacturing leads to increased productivity and throughput, reduced labor costs, improved product quality and consistency, real-time process monitoring and control, and predictive maintenance, which reduces downtime.
5. Why is environmental sustainability important in PCB manufacturing?
Environmental sustainability is crucial in PCB manufacturing as it helps protect the environment, enables compliance with stringent regulations, and meets customer demands for greener products. By adopting eco-friendly materials and sustainable manufacturing practices, PCB manufacturers can reduce their environmental impact and contribute to a more sustainable future.
Conclusion
Keeping up with the latest technology and PCB manufacturing trends is essential for saving time and energy in the design and production process. Advanced materials, miniaturization, 3D printing, automation, and environmental sustainability are just a few of the trends shaping the industry today.
By understanding and incorporating these trends into your PCB design and manufacturing workflow, you can create high-performance, reliable, and sustainable electronic devices while streamlining your processes and reducing costs. Staying informed and adaptable in the face of ever-evolving technology and manufacturing trends will help you remain competitive and successful in the dynamic world of PCB manufacturing.
0 Comments