Introduction to Medical PCB Assembly
Medical PCB assembly is a highly specialized field that requires strict adherence to industry standards and regulations. Printed Circuit Boards (PCBs) used in medical devices must be designed, manufactured, and assembled with the utmost care and precision to ensure patient safety and device reliability. In this article, we will explore the intricacies of medical PCB assembly and prototyping, including the unique challenges, requirements, and best practices involved in creating high-quality medical electronics.
Key Considerations for Medical PCB Assembly
When it comes to medical PCB assembly, several key factors must be taken into account:
-
Regulatory Compliance: Medical devices are subject to strict regulatory requirements, such as those set forth by the FDA (Food and Drug Administration) in the United States and the European Union’s Medical Device Regulation (MDR). PCB assembly must adhere to these regulations to ensure patient safety and device effectiveness.
-
Quality Control: Medical PCBs require rigorous quality control measures throughout the assembly process. This includes thorough testing, inspection, and documentation to ensure that each board meets the required specifications and performs reliably.
-
Cleanliness and Contamination Control: Medical PCBs must be assembled in a clean environment to prevent contamination that could compromise device performance or patient safety. This often requires the use of specialized equipment, such as cleanrooms and ESD (Electrostatic Discharge) protection measures.
-
Materials Selection: The choice of materials used in medical PCB assembly is crucial. Components and materials must be biocompatible, resistant to harsh sterilization processes, and able to withstand the rigors of long-term use in medical environments.
Medical PCB Design Considerations
Designing a medical PCB requires careful consideration of various factors to ensure optimal performance, reliability, and patient safety. Some key design considerations include:
Component Selection
When selecting components for a medical PCB, designers must choose parts that are reliable, durable, and able to withstand the harsh conditions often encountered in medical environments. This may include exposure to chemicals, sterilization processes, and extreme temperatures. Components should also be selected based on their ability to meet the specific performance requirements of the medical device in question.
Layout and Routing
The layout and routing of a medical PCB play a critical role in its overall performance and reliability. Designers must carefully consider factors such as signal integrity, power distribution, and thermal management when creating the board layout. In addition, special attention must be paid to minimizing electromagnetic interference (EMI) and ensuring proper grounding to prevent electrical noise from interfering with device functionality.
Shielding and Protection
Medical PCBs often require additional shielding and protection measures to ensure reliable operation in harsh environments. This may include the use of conformal coatings, potting compounds, or specialized enclosures to protect the board from moisture, dust, and other contaminants. Designers must also consider the need for ESD protection to prevent damage from static discharge events.
Medical PCB Prototyping Process
Prototyping is an essential step in the development of any medical device, allowing designers and engineers to test and refine their designs before moving into full-scale production. The medical PCB prototyping process typically involves the following steps:
-
Design Validation: The first step in the prototyping process is to validate the PCB design to ensure that it meets all functional and regulatory requirements. This may involve computer-aided design (CAD) simulations, as well as physical testing of individual components and sub-assemblies.
-
Prototype Fabrication: Once the design has been validated, the next step is to fabricate one or more prototype boards. This typically involves using specialized PCB manufacturing equipment and techniques to create a small number of boards for testing and evaluation.
-
Assembly and Testing: After the prototype boards have been fabricated, they must be assembled and tested to ensure proper functionality. This may involve manual or automated assembly processes, depending on the complexity of the board and the number of prototypes required. Testing may include functional testing, environmental testing, and other specialized tests to validate the board’s performance under various conditions.
-
Design Refinement: Based on the results of the prototype testing, designers may need to make changes or refinements to the PCB design to improve performance, reliability, or manufacturability. This may involve multiple iterations of the prototyping process until the desired results are achieved.
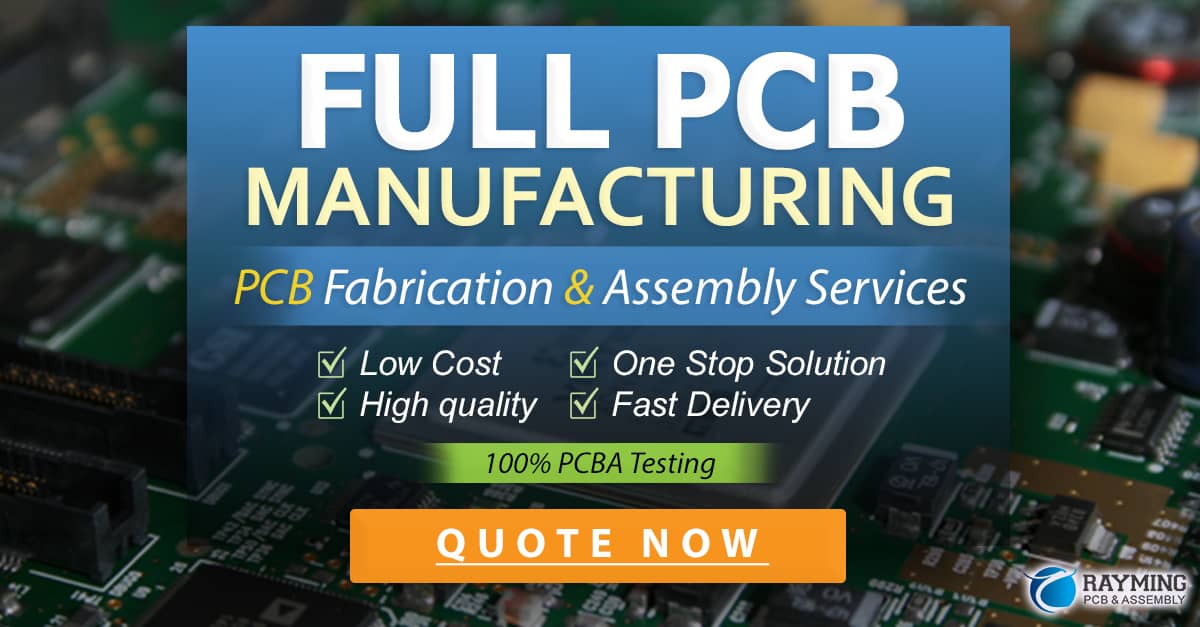
Medical PCB Assembly Best Practices
To ensure the highest quality and reliability in medical PCB assembly, it is important to follow best practices throughout the design, prototyping, and production processes. Some key best practices include:
Collaboration and Communication
Effective collaboration and communication between all stakeholders involved in the medical PCB assembly process is essential. This includes designers, engineers, manufacturers, and regulatory experts. By working closely together and maintaining open lines of communication, teams can identify and address potential issues early in the process, reducing the risk of delays or quality problems down the line.
Robust Documentation
Maintaining accurate and up-to-date documentation is critical in medical PCB assembly. This includes design files, bill of materials (BOM), assembly instructions, and quality control records. By maintaining a comprehensive documentation system, teams can ensure that all stakeholders have access to the information they need to make informed decisions and maintain traceability throughout the product lifecycle.
Continuous Improvement
Medical PCB assembly is an ongoing process that requires continuous improvement to keep pace with advances in technology and changes in regulatory requirements. By regularly reviewing and updating their processes, procedures, and equipment, medical device manufacturers can ensure that they are always producing the highest quality products and meeting the evolving needs of patients and healthcare providers.
Challenges in Medical PCB Assembly
Despite the many best practices and quality control measures in place, medical PCB assembly still presents several unique challenges that manufacturers must be prepared to address. Some of the most significant challenges include:
Regulatory Compliance
Keeping up with the ever-changing landscape of regulatory requirements can be a major challenge for medical device manufacturers. From the FDA in the United States to the MDR in Europe, manufacturers must navigate a complex web of regulations and standards to ensure that their products are compliant and safe for use. This requires ongoing investment in training, auditing, and quality management systems to stay ahead of the curve.
Supply Chain Management
Managing the supply chain for medical PCB assembly can be a complex and time-consuming process. Manufacturers must ensure that they have a reliable and consistent supply of high-quality components and materials, while also managing inventory levels and lead times to meet production schedules. This requires close collaboration with suppliers and a robust system for tracking and managing inventory and orders.
Skilled Workforce
Medical PCB assembly requires a highly skilled and specialized workforce, including designers, engineers, technicians, and quality control personnel. Finding and retaining top talent in this field can be a challenge, particularly in regions with high competition for skilled labor. Manufacturers must invest in training and development programs to build and maintain a strong workforce, while also offering competitive compensation and benefits to attract and retain top talent.
Conclusion
Medical PCB assembly and prototyping is a complex and challenging field that requires a deep understanding of the unique requirements and challenges involved. From regulatory compliance and quality control to materials selection and design considerations, there are many factors that must be carefully managed to ensure the highest level of quality and reliability in medical devices.
By following best practices, investing in continuous improvement, and staying up to date with the latest technologies and regulations, medical device manufacturers can overcome these challenges and deliver products that improve patient outcomes and advance the field of healthcare. As the demand for innovative and high-quality medical devices continues to grow, the importance of medical PCB assembly and prototyping will only continue to increase in the years to come.
FAQs
-
Q: What is the difference between medical PCB assembly and regular PCB assembly?
A: Medical PCB assembly requires additional considerations and requirements compared to regular PCB assembly. These include stricter quality control measures, the use of biocompatible materials, and adherence to regulatory standards such as those set by the FDA and MDR. -
Q: How long does the medical PCB prototyping process typically take?
A: The length of the medical PCB prototyping process can vary depending on the complexity of the design and the number of iterations required. On average, the process can take anywhere from a few weeks to several months, depending on the specific requirements of the project. -
Q: What are some of the most common materials used in medical PCB assembly?
A: Some of the most common materials used in medical PCB assembly include FR-4, polyimide, and ceramic substrates. These materials are chosen for their biocompatibility, durability, and ability to withstand harsh sterilization processes and environmental conditions. -
Q: How can medical device manufacturers ensure compliance with regulatory requirements?
A: To ensure compliance with regulatory requirements, medical device manufacturers must implement robust quality management systems, conduct regular audits and inspections, and maintain detailed documentation throughout the product lifecycle. They must also stay up to date with the latest regulatory changes and guidelines and work closely with regulatory agencies to ensure that their products meet all necessary standards. -
Q: What are some of the key trends and innovations in medical PCB assembly?
A: Some of the key trends and innovations in medical PCB assembly include the use of advanced materials such as flexible and stretchable substrates, the integration of wireless connectivity and sensing capabilities, and the development of miniaturized and implantable devices. Additionally, there is growing interest in the use of additive manufacturing techniques such as 3D printing for medical PCB fabrication and assembly.
0 Comments