Introduction to Mixed Model Assembly
Mixed Model Assembly (MMA) is a manufacturing strategy that enables the production of multiple product variants on a single assembly line. This approach has gained significant traction in recent years as industries strive to meet the growing demand for customized and diverse product offerings. By leveraging the flexibility and adaptability of MMA, companies can efficiently produce a wide range of products while optimizing resource utilization and minimizing costs.
Key Benefits of Mixed Model Assembly
- Increased product variety
- Improved responsiveness to customer demands
- Optimized resource utilization
- Reduced inventory costs
- Enhanced manufacturing flexibility
The Evolution of Mixed Model Assembly
Traditional Assembly Lines
Traditionally, assembly lines were designed to produce large volumes of a single product variant. This approach, known as the dedicated assembly line, was highly efficient for mass production but lacked the flexibility to accommodate product variations. As consumer preferences shifted towards personalized and diverse products, the limitations of dedicated assembly lines became apparent.
The Emergence of Mixed Model Assembly
To address the challenges posed by changing market demands, manufacturers began exploring alternative production strategies. Mixed Model Assembly emerged as a viable solution, allowing companies to produce multiple product variants on a single assembly line. By incorporating flexible equipment, cross-trained workers, and intelligent scheduling systems, MMA enables seamless transitions between different product models.
Implementing Mixed Model Assembly
Planning and Preparation
Before implementing MMA, thorough planning and preparation are essential. This involves conducting a detailed analysis of product variations, demand forecasts, and production constraints. Based on this information, manufacturers can design an assembly line layout that accommodates the required product mix and ensures smooth material flow.
Equipment and Technology
To support the flexibility required for MMA, manufacturers must invest in adaptable equipment and advanced technology. This includes:
- Flexible manufacturing systems (FMS)
- Modular workstations
- Automated guided vehicles (AGVs)
- Robotics and automation
These technologies enable quick changeovers between product variants and optimize material handling processes.
Workforce Training and Development
Successful implementation of MMA relies heavily on a skilled and versatile workforce. Employees must be cross-trained to handle multiple tasks and adapt to different product requirements. Investing in comprehensive training programs and fostering a culture of continuous learning is crucial for achieving the flexibility and efficiency demanded by MMA.
Scheduling and Sequencing
Effective scheduling and sequencing are critical components of MMA. Manufacturers must develop intelligent scheduling algorithms that consider factors such as:
- Product mix and demand
- Production constraints
- Material availability
- Workforce skills and availability
By optimizing the production sequence, manufacturers can minimize changeover times, reduce inventory levels, and improve overall efficiency.
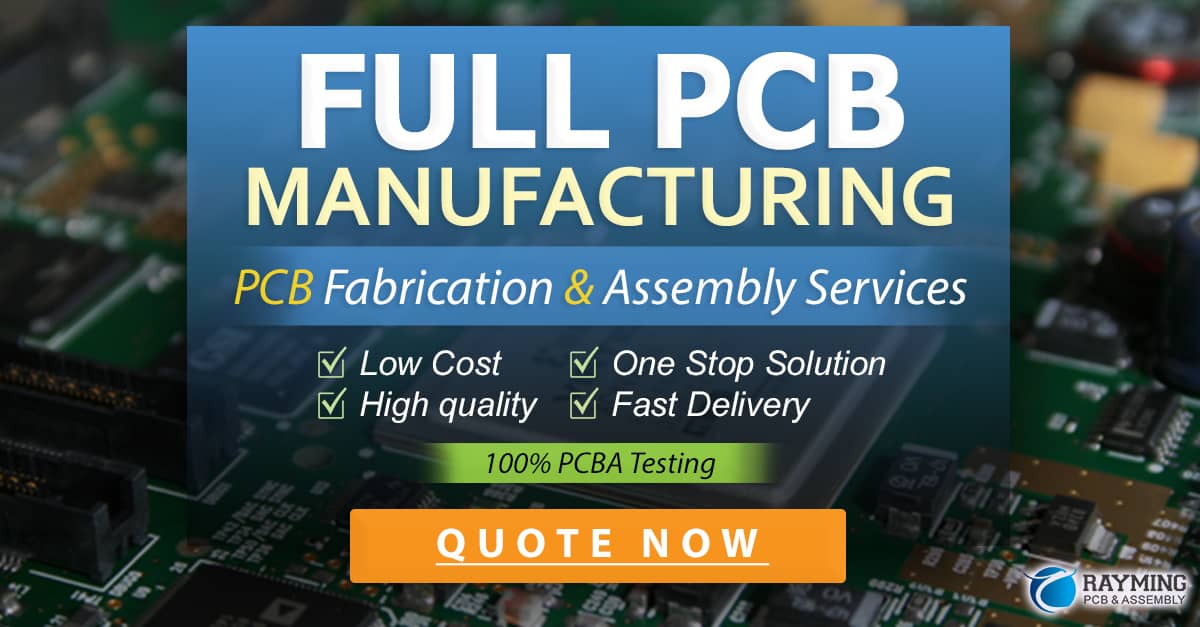
Challenges and Opportunities in Mixed Model Assembly
Balancing Efficiency and Flexibility
One of the primary challenges in MMA is striking the right balance between efficiency and flexibility. While MMA enables the production of multiple product variants, it can also introduce complexity and potentially impact overall productivity. Manufacturers must carefully assess the trade-offs and implement strategies to minimize the impact on efficiency.
Managing Supply Chain Complexity
MMA often requires a more diverse and complex supply chain to support the production of multiple product variants. Manufacturers must establish strong partnerships with suppliers, ensuring timely delivery of components and materials. Effective supply chain management, including inventory optimization and just-in-time delivery, is essential for the success of MMA.
Continuous Improvement and Innovation
To remain competitive in a rapidly evolving market, manufacturers must embrace a culture of continuous improvement and innovation. This involves regularly reviewing and optimizing MMA processes, identifying bottlenecks, and implementing data-driven solutions. By leveraging advanced analytics and Industry 4.0 technologies, manufacturers can gain valuable insights into production performance and drive ongoing improvements.
Real-World Applications of Mixed Model Assembly
Automotive Industry
The automotive industry has been at the forefront of adopting MMA. With the increasing demand for customized vehicles and the need to respond quickly to market trends, automotive manufacturers have successfully implemented MMA to produce a wide range of car models on a single assembly line. This has enabled them to offer customers a greater variety of options while maintaining production efficiency.
Consumer Electronics
The consumer electronics industry is another sector that has benefited from MMA. With the rapid pace of technological advancements and the constant introduction of new features and designs, electronics manufacturers must be able to quickly adapt their production lines. MMA allows them to produce multiple product variants, such as smartphones, tablets, and laptops, on the same assembly line, reducing time-to-market and meeting diverse customer demands.
Aerospace and Defense
In the aerospace and defense industry, MMA has proven valuable for producing complex and customized products. With strict quality requirements and the need for high precision, aerospace manufacturers leverage MMA to efficiently produce aircraft components and systems while accommodating specific customer specifications. This flexibility enables them to meet the unique needs of both commercial and military applications.
The Future of Mixed Model Assembly
Integration with Industry 4.0
As Industry 4.0 technologies continue to advance, the potential for MMA will only grow. The integration of Industrial Internet of Things (IIoT), artificial intelligence (AI), and advanced robotics will further enhance the flexibility and efficiency of MMA. These technologies will enable real-time monitoring, predictive maintenance, and autonomous decision-making, optimizing production processes and reducing downtime.
Enhancing Sustainability
MMA can play a significant role in promoting sustainable manufacturing practices. By reducing inventory levels and minimizing waste, MMA contributes to more efficient resource utilization. Additionally, the flexibility of MMA allows manufacturers to quickly adapt to changing market demands, reducing the risk of obsolescence and overproduction. As sustainability becomes an increasingly important consideration for businesses and consumers alike, MMA will be a key enabler of eco-friendly manufacturing.
Collaborating with Customers
The future of MMA lies in closer collaboration with customers. By involving customers in the product design and configuration process, manufacturers can gather valuable insights and tailor their offerings to specific needs. This collaboration can be facilitated through digital platforms, such as online product configurators and virtual reality simulations, allowing customers to visualize and customize their products before production begins. This level of customer engagement not only enhances satisfaction but also streamlines the MMA process by ensuring that products meet exact requirements.
Frequently Asked Questions (FAQ)
-
What is Mixed Model Assembly?
Mixed Model Assembly (MMA) is a manufacturing strategy that enables the production of multiple product variants on a single assembly line. It allows manufacturers to efficiently produce a wide range of products while optimizing resource utilization and minimizing costs. -
What are the benefits of Mixed Model Assembly?
The key benefits of MMA include increased product variety, improved responsiveness to customer demands, optimized resource utilization, reduced inventory costs, and enhanced manufacturing flexibility. -
How does Mixed Model Assembly differ from traditional assembly lines?
Traditional assembly lines are designed to produce large volumes of a single product variant, while MMA allows for the production of multiple product variants on a single assembly line. MMA incorporates flexible equipment, cross-trained workers, and intelligent scheduling systems to enable seamless transitions between different product models. -
What industries commonly use Mixed Model Assembly?
MMA is commonly used in industries such as automotive, consumer electronics, aerospace and defense, where there is a high demand for product customization and variety. These industries benefit from the flexibility and efficiency offered by MMA. -
What role does technology play in Mixed Model Assembly?
Advanced technologies such as flexible manufacturing systems (FMS), modular workstations, automated guided vehicles (AGVs), robotics, and automation are crucial for the successful implementation of MMA. These technologies enable quick changeovers between product variants and optimize material handling processes, enhancing the overall efficiency and flexibility of the assembly line.
Conclusion
Mixed Model Assembly has emerged as a powerful strategy for manufacturers to meet the growing industrial demand for customized and diverse products. By enabling the production of multiple product variants on a single assembly line, MMA offers increased flexibility, improved responsiveness, and optimized resource utilization. The successful implementation of MMA requires careful planning, investment in adaptable equipment and technology, and a skilled and versatile workforce.
As industries continue to evolve and customer expectations rise, the importance of MMA will only grow. The integration of Industry 4.0 technologies, the focus on sustainability, and closer collaboration with customers will shape the future of MMA. By embracing these advancements and continuously improving their processes, manufacturers can unlock the full potential of Mixed Model Assembly and remain competitive in an ever-changing market.
0 Comments