Understanding the Effects of Moisture on PCBs
Moisture can have several detrimental effects on PCBs:
-
Corrosion: When exposed to moisture, the metal components on a PCB can corrode, leading to reduced conductivity and potential short circuits.
-
Delamination: Moisture can cause the layers of a PCB to separate, resulting in delamination and compromised structural integrity.
-
Electromigration: High humidity levels can accelerate electromigration, causing the movement of metal ions and potentially leading to open circuits.
-
Fungal Growth: In extreme cases, moisture can promote the growth of fungi on PCBs, causing further damage and reliability issues.
Factors Affecting PCB Moisture Exposure in Outdoor Environments
Several factors can influence the level of moisture exposure for PCBs in outdoor environments:
-
Humidity: High humidity levels increase the likelihood of moisture-related issues.
-
Temperature Fluctuations: Rapid changes in temperature can lead to condensation on PCBs.
-
Precipitation: Rain, snow, and other forms of precipitation can directly expose PCBs to moisture.
-
Enclosure Design: Poorly designed enclosures may allow moisture to enter and accumulate around PCBs.
Best Practices for PCB Moisture Protection
To minimize the risk of moisture-related issues, consider the following best practices:
Conformal Coating
Applying a conformal coating to PCBs can provide a barrier against moisture. Common coating materials include:
- Acrylic
- Silicone
- Polyurethane
- Epoxy
Coating Material | Advantages | Disadvantages |
---|---|---|
Acrylic | Easy to apply, low cost | Limited chemical and abrasion resistance |
Silicone | Excellent flexibility, wide temperature range | Difficult to repair, can trap contaminants |
Polyurethane | Good chemical and abrasion resistance | Requires special application equipment |
Epoxy | High strength, good chemical resistance | Brittle, difficult to remove |
Enclosure Design
Proper enclosure design is crucial for protecting PCBs from moisture. Consider the following:
-
IP Rating: Choose an enclosure with an appropriate Ingress Protection (IP) rating for the intended environment.
-
Gaskets and Seals: Use gaskets and seals to prevent moisture from entering the enclosure.
-
Drainage: Include drainage holes or channels to allow any accumulated moisture to escape.
-
Ventilation: Incorporate ventilation features to prevent the buildup of humid air inside the enclosure.
Component Selection
Select components that are rated for the expected environmental conditions:
-
Moisture Sensitivity Level (MSL): Choose components with an appropriate MSL rating for the anticipated humidity levels.
-
Protective Finishes: Opt for components with protective finishes, such as gold plating or conformal coating.
-
Hermetic Sealing: For critical applications, consider using hermetically sealed components.
PCB Design Considerations
Incorporate moisture-resistant features into the PCB design:
-
Solder Mask: Use a high-quality solder mask to protect the copper traces from moisture.
-
Solderable Finishes: Choose solderable finishes, such as Electroless Nickel Immersion Gold (ENIG) or Immersion Silver, that offer good corrosion resistance.
-
Increased Spacing: Provide adequate spacing between components and traces to minimize the risk of short circuits caused by moisture.
-
Avoid Moisture Traps: Design the PCB layout to avoid creating moisture traps, such as deep vias or narrow channels.
Storage and Handling
Proper storage and handling practices can help prevent moisture-related issues:
-
Moisture-Barrier Bags: Store PCBs in moisture-barrier bags with desiccants when not in use.
-
Humidity Control: Maintain a controlled-humidity environment for storage and assembly areas.
-
Baking: If PCBs have absorbed moisture, bake them according to the manufacturer’s recommendations before assembly.
-
Handling Precautions: Use gloves when handling PCBs to avoid contamination and moisture transfer from skin.
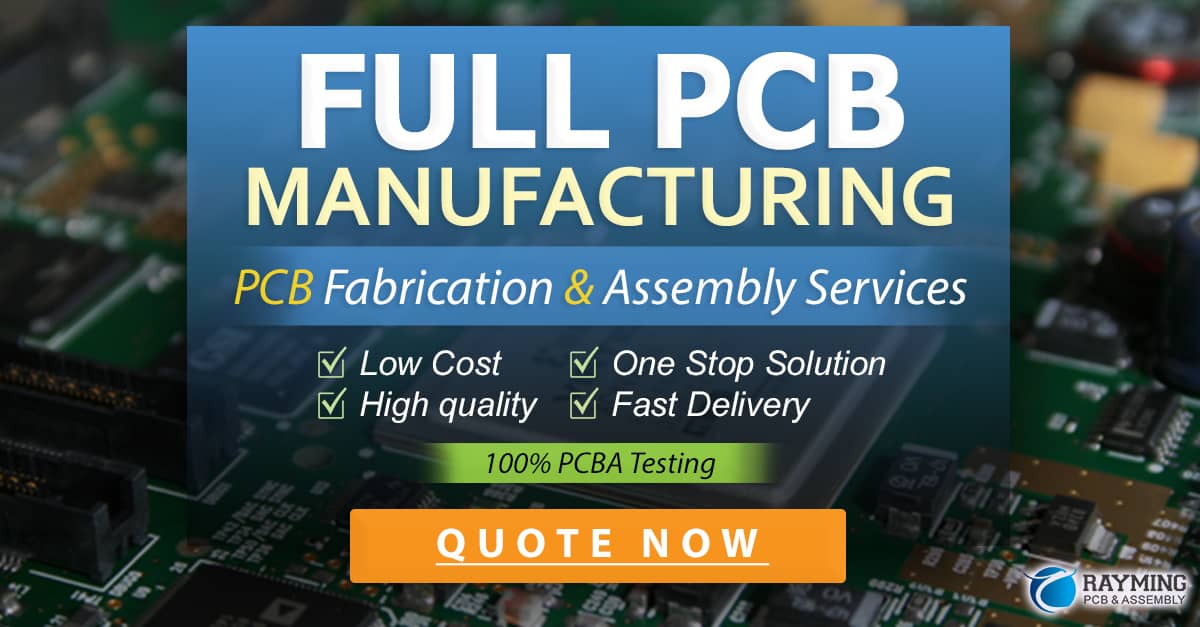
Monitoring and Maintenance
Regular monitoring and maintenance can help identify and address moisture-related issues before they cause significant damage:
-
Visual Inspection: Periodically inspect PCBs for signs of corrosion, delamination, or other moisture-related damage.
-
Humidity Monitoring: Use humidity sensors to monitor the humidity levels inside enclosures and storage areas.
-
Cleaning: If necessary, clean PCBs using appropriate methods, such as isopropyl alcohol or specialized cleaning solutions.
-
Reapplication of Conformal Coating: If the conformal coating becomes damaged, reapply it to maintain moisture protection.
Frequently Asked Questions (FAQ)
-
What is the best conformal coating for outdoor environments?
The best conformal coating for outdoor environments depends on the specific requirements of the application. Silicone and polyurethane coatings offer good protection against moisture and have a wide operating temperature range. However, silicone can be difficult to repair, while polyurethane requires specialized application equipment. Epoxy coatings provide high strength and chemical resistance but are brittle and difficult to remove. Ultimately, the choice of coating should be based on factors such as the expected environmental conditions, the desired level of protection, and the ease of application and maintenance. -
How can I tell if a PCB has been damaged by moisture?
Signs of moisture damage on a PCB include corrosion on metal components, delamination of the PCB layers, and the presence of fungal growth. Corrosion appears as a green or white powdery substance on the surface of the metal components. Delamination can be identified by the separation of the PCB layers, often visible at the edges of the board. Fungal growth appears as a fuzzy or slimy substance on the surface of the PCB. If any of these signs are observed, the PCB should be inspected more closely and, if necessary, cleaned or repaired. -
Can moisture-damaged PCBs be repaired?
In some cases, moisture-damaged PCBs can be repaired, depending on the extent and type of damage. Minor corrosion can be cleaned using isopropyl alcohol or specialized cleaning solutions. If the conformal coating has been damaged, it can be reapplied after cleaning the affected area. However, if the damage is severe, such as extensive corrosion or delamination, the PCB may need to be replaced entirely. It is essential to address moisture damage promptly to prevent further deterioration of the PCB. -
How often should I inspect PCBs in outdoor environments?
The frequency of PCB inspections in outdoor environments depends on the specific application and the harshness of the environment. In general, it is recommended to inspect PCBs at least once every six months to identify any signs of moisture damage or other issues. However, if the environment is particularly harsh, with high humidity levels or frequent temperature fluctuations, more frequent inspections may be necessary. Regularly monitoring humidity levels inside enclosures can also help determine the appropriate inspection frequency. -
Can I use silica gel packets to protect PCBs from moisture?
Silica gel packets can be used to absorb moisture and help protect PCBs during storage. However, they are not a substitute for proper PCB design, conformal coating, and enclosure design. Silica gel packets should be used in conjunction with moisture-barrier bags when storing PCBs. It is important to note that silica gel packets have a limited capacity for moisture absorption and should be replaced periodically to maintain their effectiveness. Additionally, silica gel packets should not be relied upon for long-term moisture protection in outdoor environments.
Conclusion
Protecting PCBs from moisture in outdoor environments is essential to ensure the reliability and longevity of electronic devices. By implementing best practices such as conformal coating, proper enclosure design, component selection, and PCB design considerations, the risk of moisture-related issues can be significantly reduced. Regular monitoring and maintenance, including visual inspections and humidity monitoring, can help identify and address any problems before they cause significant damage. By following these guidelines, designers and manufacturers can create PCBs that can withstand the challenges of outdoor environments and provide reliable performance for years to come.
0 Comments