Introduction to ImSn PCB Finish
Immersion tin (ImSn) is a popular surface finish for printed circuit boards (PCBs) in the electronics industry. This chemical process deposits a thin, uniform layer of tin onto the copper pads and through-holes of a PCB, providing excellent solderability, flatness, and reliability. ImSn has gained widespread acceptance as a cost-effective and environmentally friendly alternative to other surface finishes, such as hot air solder leveling (HASL) and electroless nickel immersion gold (ENIG).
In this comprehensive article, we will explore the key aspects of ImSn PCB finish, including its properties, benefits, applications, and manufacturing process. We will also compare ImSn to other common surface finishes and discuss the factors to consider when selecting the most suitable finish for your PCB project.
Properties and Benefits of ImSn PCB Finish
Key Properties of ImSn
- Excellent solderability
- Flat and uniform surface
- Good electrical conductivity
- Compatibility with lead-free soldering processes
- Resistance to oxidation and corrosion
Benefits of Using ImSn PCB Finish
- Cost-effective compared to other surface finishes
- Environmentally friendly (no lead or hazardous chemicals)
- Suitable for fine-pitch components and high-density interconnects
- Improved shelf life and storage stability
- Easier visual inspection and quality control
Applications of ImSn PCB Finish
ImSn PCB finish is widely used in various electronics applications, including:
- Consumer electronics (smartphones, tablets, laptops)
- Automotive electronics (infotainment systems, sensors, control units)
- Industrial automation and control systems
- Medical devices and equipment
- Aerospace and defense electronics
- Internet of Things (IoT) devices
- Telecommunications equipment
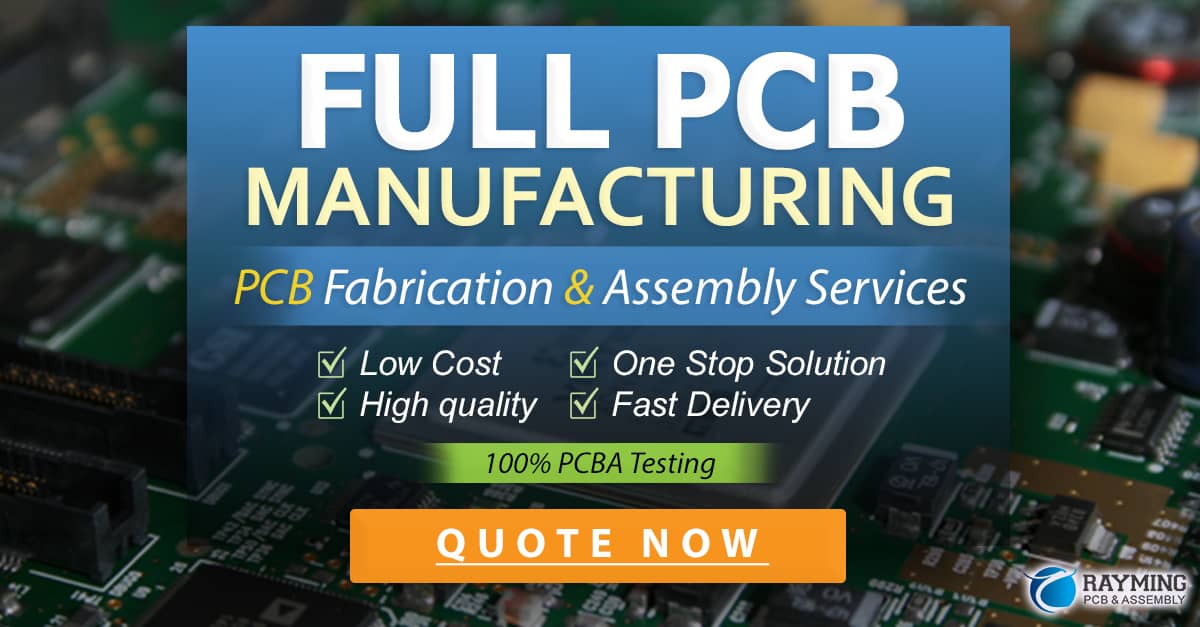
Manufacturing Process of ImSn PCB Finish
The ImSn PCB finishing process involves several steps to ensure a high-quality, uniform tin layer on the copper surfaces. Here’s an overview of the typical manufacturing process:
-
Pre-cleaning: The PCB is cleaned to remove any contaminants, such as dirt, grease, or oxides, from the copper surfaces. This step ensures proper adhesion of the tin layer.
-
Microetching: A mild etching solution is applied to the copper surfaces to create a micro-roughened surface, which enhances the bonding between the copper and the tin layer.
-
Acid dip: The PCB is dipped in a mild acid solution to remove any remaining oxides and activate the copper surfaces for the immersion tin process.
-
Immersion tin plating: The PCB is immersed in a tin solution, typically containing tin ions, thiourea, and other additives. The tin ions react with the copper surfaces, depositing a thin, uniform layer of tin through a chemical displacement reaction.
-
Rinsing: The PCB is thoroughly rinsed with deionized water to remove any excess tin solution and prevent staining or discoloration.
-
Drying: The PCB is dried using hot air or an oven to remove any residual moisture and ensure a clean, dry surface finish.
-
Inspection: The finished PCB undergoes visual inspection and quality control checks to ensure proper coverage, uniformity, and adherence to specifications.
The entire ImSn PCB finishing process is highly automated and carefully controlled to maintain consistency and quality across production batches.
Comparison of ImSn with Other PCB Surface Finishes
ImSn is one of several surface finishes available for PCBs, each with its own advantages and limitations. Let’s compare ImSn with two other popular surface finishes: HASL and ENIG.
Property | ImSn | HASL | ENIG |
---|---|---|---|
Solderability | Excellent | Good | Excellent |
Surface flatness | High | Low | High |
Shelf life | 12-18 months | 6-12 months | 12-18 months |
Cost | Low | Low | High |
Environmental impact | Low | High (lead content) | Moderate (gold and nickel) |
Fine-pitch compatibility | High | Low | High |
Reliability | Good | Moderate | Excellent |
As evident from the table, ImSn offers a balanced combination of good solderability, high surface flatness, and low cost compared to HASL and ENIG. It is also more environmentally friendly than HASL, which contains lead, and more cost-effective than ENIG, which uses expensive gold and nickel.
Factors to Consider When Choosing ImSn PCB Finish
When deciding whether ImSn is the right surface finish for your PCB project, consider the following factors:
-
Application requirements: Evaluate the specific needs of your application, such as solderability, surface flatness, and reliability, to determine if ImSn meets those requirements.
-
Cost considerations: Compare the cost of ImSn with other surface finishes, taking into account the volume of production and the overall budget of your project.
-
Environmental regulations: Ensure that ImSn complies with the environmental regulations and standards relevant to your industry and target markets, such as RoHS and REACH.
-
Manufacturing capabilities: Verify that your PCB manufacturer has the necessary equipment, expertise, and quality control processes to produce high-quality ImSn finishes consistently.
-
Compatibility with components: Check that the components and soldering processes used in your PCB Assembly are compatible with ImSn finish, especially for fine-pitch and high-density designs.
Frequently Asked Questions (FAQ)
-
Q: What is the typical thickness of an ImSn PCB finish?
A: The typical thickness of an ImSn PCB finish ranges from 0.8 to 1.2 microns (30 to 50 microinches). -
Q: How does ImSn compare to other PCB surface finishes in terms of cost?
A: ImSn is generally more cost-effective than ENIG and comparable to HASL, making it an attractive option for budget-conscious projects. -
Q: Is ImSn suitable for lead-free soldering processes?
A: Yes, ImSn is compatible with lead-free soldering processes and is often used in RoHS-compliant PCB assemblies. -
Q: What is the shelf life of ImSn PCB finish?
A: The shelf life of ImSn PCB finish is typically 12 to 18 months, depending on storage conditions and the quality of the finishing process. -
Q: Can ImSn be used for both rigid and flexible PCBs?
A: Yes, ImSn can be applied to both rigid and flexible PCBs, making it a versatile surface finish option for various applications.
Conclusion
Immersion tin (ImSn) is a highly regarded PCB surface finish that offers numerous benefits, including excellent solderability, high surface flatness, and cost-effectiveness. Its compatibility with lead-free soldering processes and environmental friendliness make it an attractive choice for a wide range of electronics applications, from consumer devices to industrial systems.
When considering ImSn for your PCB project, it is essential to evaluate your specific application requirements, cost constraints, and manufacturing capabilities to ensure that ImSn is the most suitable surface finish option. By understanding the properties, benefits, and limitations of ImSn, you can make an informed decision and achieve the best possible results for your PCB assembly.
As the electronics industry continues to evolve, with increasing demands for miniaturization, reliability, and sustainability, ImSn PCB finish is well-positioned to meet these challenges and remain a preferred choice among PCB manufacturers and designers alike.
0 Comments