Introduction to CEM-3 PCB
CEM-3 (Composite Epoxy Material-3) is a high-quality, flame-retardant printed circuit board (PCB) substrate material that is widely used in the electronics industry. It is known for its excellent mechanical and electrical properties, making it an ideal choice for a wide range of applications, including consumer electronics, industrial control systems, and telecommunications equipment.
Composition and Properties of CEM-3
CEM-3 is a composite material that consists of a woven fiberglass cloth impregnated with an epoxy resin system. The fiberglass cloth provides mechanical strength and dimensional stability, while the epoxy resin system offers excellent electrical insulation and chemical resistance. CEM-3 is classified as a FR-4 (Flame Retardant-4) material, which means it has superior flame-retardant properties compared to other PCB substrate materials.
Some of the key properties of CEM-3 include:
- High mechanical strength and stiffness
- Excellent electrical insulation
- Good thermal stability
- Superior flame retardancy
- Resistance to moisture and chemicals
- Ease of fabrication and processing
Advantages of Using CEM-3 PCBs
CEM-3 PCBs offer several advantages over other types of PCB substrate materials, such as:
-
Cost-effectiveness: CEM-3 is a cost-effective alternative to high-end PCB materials like polyimide and Teflon, making it an attractive option for budget-conscious projects.
-
Reliability: The superior mechanical and electrical properties of CEM-3 ensure that the PCBs are reliable and durable, even in harsh operating conditions.
-
Versatility: CEM-3 PCBs can be used in a wide range of applications, from consumer electronics to industrial control systems, making them a versatile choice for PCB manufacturers.
-
Ease of processing: CEM-3 is easy to fabricate and process, which reduces manufacturing time and costs.
CEM-3 PCB Manufacturing Process
The manufacturing process for CEM-3 PCBs involves several steps, each of which is critical to ensuring the quality and reliability of the final product.
Step 1: Design and Artwork Creation
The first step in the CEM-3 PCB manufacturing process is to create the PCB design and artwork. This involves using specialized PCB design software to layout the circuit schematic and generate the necessary artwork files (Gerber files) for manufacturing.
Step 2: Material Selection and Preparation
Once the design is finalized, the next step is to select the appropriate CEM-3 material based on the specific requirements of the project (e.g., thickness, copper weight). The CEM-3 material is then cut to size and cleaned to remove any contaminants.
Step 3: Drilling and Hole Plating
The CEM-3 board is then drilled according to the design specifications to create the necessary holes for component placement and interconnections. After drilling, the holes are plated with copper to ensure electrical conductivity.
Step 4: Patterning and Etching
The copper-clad CEM-3 board is then patterned using a photoresist and exposed to UV light through a photomask containing the PCB artwork. The exposed areas of the photoresist are then developed and removed, leaving behind a protective layer in the shape of the desired circuit pattern. The exposed copper is then etched away using a chemical solution, leaving only the desired copper traces on the board.
Step 5: Solder Mask Application and Silkscreening
A solder mask is then applied to the PCB to protect the copper traces from oxidation and prevent solder bridging during assembly. The solder mask is typically green in color but can be customized based on the project requirements. After the solder mask application, silkscreening is performed to add component labels, logos, and other markings to the PCB.
Step 6: Surface Finish and Final Inspection
The final step in the CEM-3 PCB manufacturing process is to apply a surface finish to the exposed copper areas to prevent oxidation and enhance solderability. Common surface finishes include Hot Air Solder Leveling (HASL), Electroless Nickel Immersion Gold (ENIG), and Immersion Silver (IAg). After the surface finish application, the PCBs undergo a final inspection to ensure they meet the required quality standards before being packaged and shipped to the customer.
Choosing the Right CEM-3 PCB Manufacturer
Selecting the right CEM-3 PCB manufacturer is crucial to ensuring the success of your project. Here are some factors to consider when choosing a CEM-3 PCB manufacturer:
1. Experience and Expertise
Look for a manufacturer with extensive experience in producing CEM-3 PCBs and a proven track record of delivering high-quality products. The manufacturer should have expertise in various PCB manufacturing processes and be able to provide guidance and support throughout the project.
2. Quality Control and Certifications
Ensure that the manufacturer has a robust quality control system in place and holds relevant industry certifications such as ISO 9001, UL, and IPC. These certifications demonstrate the manufacturer’s commitment to quality and adherence to industry standards.
3. Manufacturing Capabilities and Capacity
Consider the manufacturer’s manufacturing capabilities, including their equipment, technology, and production capacity. Ensure that they can handle your specific project requirements, such as PCB complexity, layer count, and volume.
4. Lead Time and Pricing
Evaluate the manufacturer’s lead time and pricing to ensure they align with your project timeline and budget. Keep in mind that while price is an important factor, it should not be the sole determining factor in your decision, as quality and reliability are equally important.
5. Customer Service and Support
Choose a manufacturer that provides excellent customer service and support throughout the project. They should be responsive to your inquiries, provide regular updates on project progress, and be willing to work with you to address any issues that may arise.
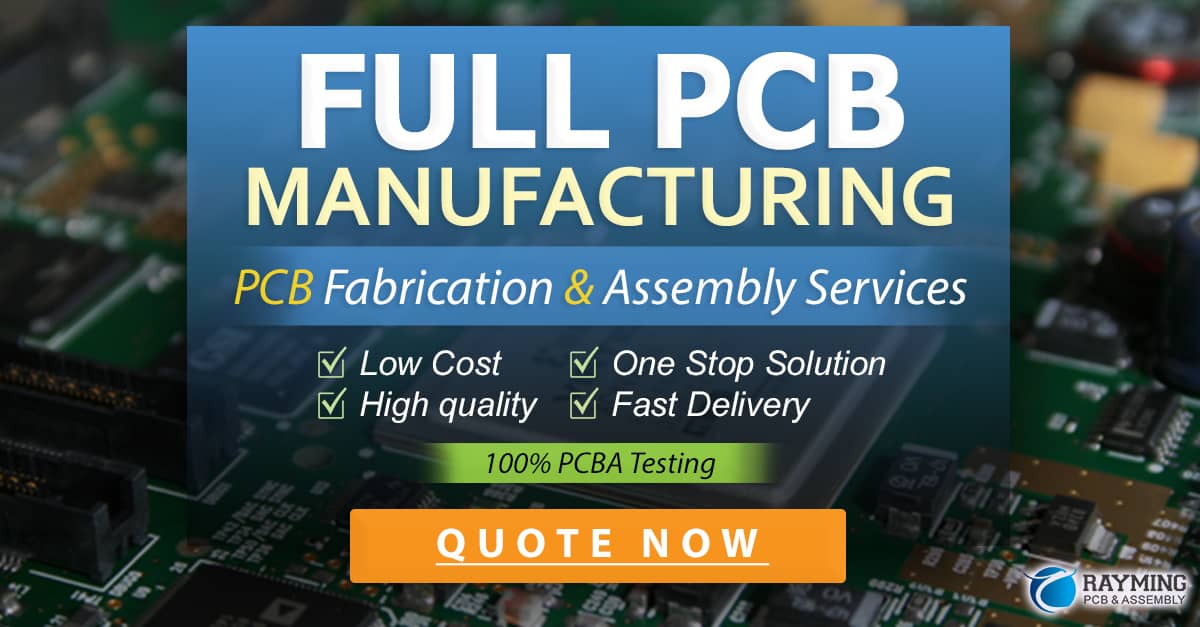
Applications of CEM-3 PCBs
CEM-3 PCBs are used in a wide range of applications across various industries. Some common applications include:
- Consumer Electronics:
- Smartphones and tablets
- Laptops and computers
- Gaming consoles
-
Wearable devices
-
Industrial Control Systems:
- Automation and process control equipment
- Motor drives and power supplies
-
Sensors and data acquisition systems
-
Telecommunications:
- Routers and switches
- Modems and gateways
-
Wireless communication devices
-
Automotive Electronics:
- Infotainment systems
- Engine control units (ECUs)
-
Advanced driver assistance systems (ADAS)
-
Medical Devices:
- Patient monitoring systems
- Diagnostic equipment
- Wearable medical devices
Comparison of CEM-3 with Other PCB Materials
CEM-3 is one of several PCB substrate materials available in the market. Here’s a comparison of CEM-3 with other common PCB materials:
Material | Composition | Advantages | Disadvantages |
---|---|---|---|
FR-4 | Woven fiberglass cloth with epoxy resin | Low cost, good mechanical and electrical properties | Limited high-frequency performance, higher moisture absorption |
CEM-1 | Cotton paper and epoxy resin | Lower cost than CEM-3, suitable for low-end applications | Inferior mechanical and electrical properties compared to CEM-3 |
CEM-2 | Cotton paper and epoxy resin with fiberglass | Better mechanical properties than CEM-1 | Higher cost than CEM-1, lower performance than CEM-3 |
Polyimide | Polyimide film with copper cladding | Excellent high-temperature and high-frequency performance | High cost, more difficult to process than CEM-3 |
Teflon | PTFE (polytetrafluoroethylene) with ceramic | Superior high-frequency and low-loss performance | Very high cost, challenging to process |
Frequently Asked Questions (FAQ)
1. What is the difference between CEM-3 and FR-4 PCBs?
CEM-3 and FR-4 are both flame-retardant PCB substrate materials that use woven fiberglass cloth impregnated with epoxy resin. However, CEM-3 has a higher glass transition temperature (Tg) and better thermal stability compared to FR-4. CEM-3 is also slightly more expensive than FR-4.
2. Can CEM-3 PCBs be used for high-frequency applications?
While CEM-3 PCBs are suitable for many general-purpose applications, they may not be the best choice for high-frequency applications due to their higher dielectric constant and loss tangent compared to specialized materials like Teflon and ceramics. However, for moderately high-frequency applications, CEM-3 can still provide satisfactory performance at a lower cost.
3. What surface finishes are available for CEM-3 PCBs?
Common surface finishes for CEM-3 PCBs include Hot Air Solder Leveling (HASL), Electroless Nickel Immersion Gold (ENIG), Immersion Silver (IAg), and Organic Solderability Preservative (OSP). The choice of surface finish depends on factors such as solderability requirements, shelf life, and cost.
4. How do I specify the right CEM-3 material for my project?
When specifying CEM-3 material for your project, consider factors such as the required thickness, copper weight, and any special requirements like controlled impedance or halogen-free properties. Consult with your PCB manufacturer to determine the most suitable CEM-3 material for your specific application.
5. What certifications should I look for when choosing a CEM-3 PCB manufacturer?
When selecting a CEM-3 PCB manufacturer, look for certifications such as ISO 9001 (quality management), UL (safety), and IPC (industry standards for PCB manufacturing). These certifications indicate that the manufacturer adheres to strict quality control processes and industry best practices.
Conclusion
CEM-3 PCBs are a reliable and cost-effective choice for a wide range of electronic applications. With their excellent mechanical, electrical, and thermal properties, CEM-3 PCBs offer a balance of performance and affordability. When selecting a CEM-3 PCB manufacturer, consider factors such as experience, quality control, manufacturing capabilities, and customer support to ensure the success of your project. By understanding the properties, manufacturing process, and applications of CEM-3 PCBs, you can make informed decisions and create high-quality electronic products that meet your specific requirements.
0 Comments