Introduction to Fine Pitch PCB
In the world of electronic manufacturing, printed circuit boards (PCBs) play a crucial role in connecting and supporting various components. As technology advances and devices become more compact, the demand for high-density PCB designs with fine pitch components has increased significantly. Fine pitch PCB Assembly refers to the process of mounting and soldering components with a pitch (distance between the centers of two adjacent pins) of less than 0.5mm.
What is a Fine Pitch PCB?
A fine pitch PCB is a type of printed circuit board that features components with a pitch of less than 0.5mm. These components, such as ball grid array (BGA) packages, quad flat no-lead (QFN) packages, and chip-scale packages (CSP), allow for higher component density and improved performance in a smaller footprint.
Advantages of Fine Pitch PCB Assembly
Fine pitch PCB assembly offers several advantages over traditional PCB designs:
- Increased component density: Fine pitch components allow for more functionality to be packed into a smaller space, enabling the creation of more compact devices.
- Improved performance: The shorter distances between components in fine pitch PCB designs lead to reduced signal propagation delays and improved overall system performance.
- Cost-effective: By utilizing smaller components and PCB sizes, fine pitch PCB assembly can lead to cost savings in terms of material usage and manufacturing processes.
Challenges in Fine Pitch PCB Assembly
While fine pitch PCB assembly offers numerous benefits, it also presents several challenges that must be addressed to ensure successful manufacturing and reliable performance.
Soldering Difficulties
One of the primary challenges in fine pitch PCB assembly is the soldering process. The small size and close proximity of the pins make it difficult to achieve reliable solder joints without causing bridging or other defects. To overcome this challenge, specialized soldering techniques, such as Pin-in-Paste (PIP) and no-clean flux, are often employed.
Thermal Management
Fine pitch components generate more heat per unit area compared to their larger counterparts. This increased heat density can lead to thermal management issues, which can affect the performance and reliability of the PCB. To mitigate these issues, proper thermal design techniques, such as the use of thermal vias and heat sinks, must be implemented.
Handling and Placement
The small size of fine pitch components makes them more susceptible to damage during handling and placement. Specialized equipment, such as high-precision pick-and-place machines and vision systems, is required to ensure accurate and reliable component placement.
Fine Pitch PCB Design Considerations
To ensure successful fine pitch PCB assembly, several design considerations must be taken into account.
Component Selection
When designing a fine pitch PCB, it is essential to carefully select components that are compatible with the desired pitch and package type. Designers should also consider the thermal characteristics and power requirements of the components to ensure proper functionality and reliability.
Pad and Trace Design
The pad and trace design for fine pitch components must be optimized to ensure proper solder joint formation and signal integrity. This includes the use of appropriate pad sizes, solder mask openings, and trace widths and spacings.
Stencil Design
The stencil design plays a critical role in the successful application of solder paste to fine pitch pads. The stencil aperture size and shape must be carefully designed to ensure the proper volume and distribution of solder paste.
Pitch (mm) | Pad Width (mm) | Pad Length (mm) | Solder Mask Opening (mm) |
---|---|---|---|
0.4 | 0.2 | 0.3 | 0.3 |
0.3 | 0.15 | 0.25 | 0.25 |
0.2 | 0.1 | 0.2 | 0.2 |
Table 1: Recommended pad and solder mask opening sizes for various fine pitch components.
Design for Manufacturing (DFM)
To ensure the manufacturability of fine pitch PCB designs, it is essential to adhere to DFM guidelines. This includes the use of appropriate design rules, such as minimum trace widths and spacings, as well as the incorporation of testability features, such as test points and boundary scan.
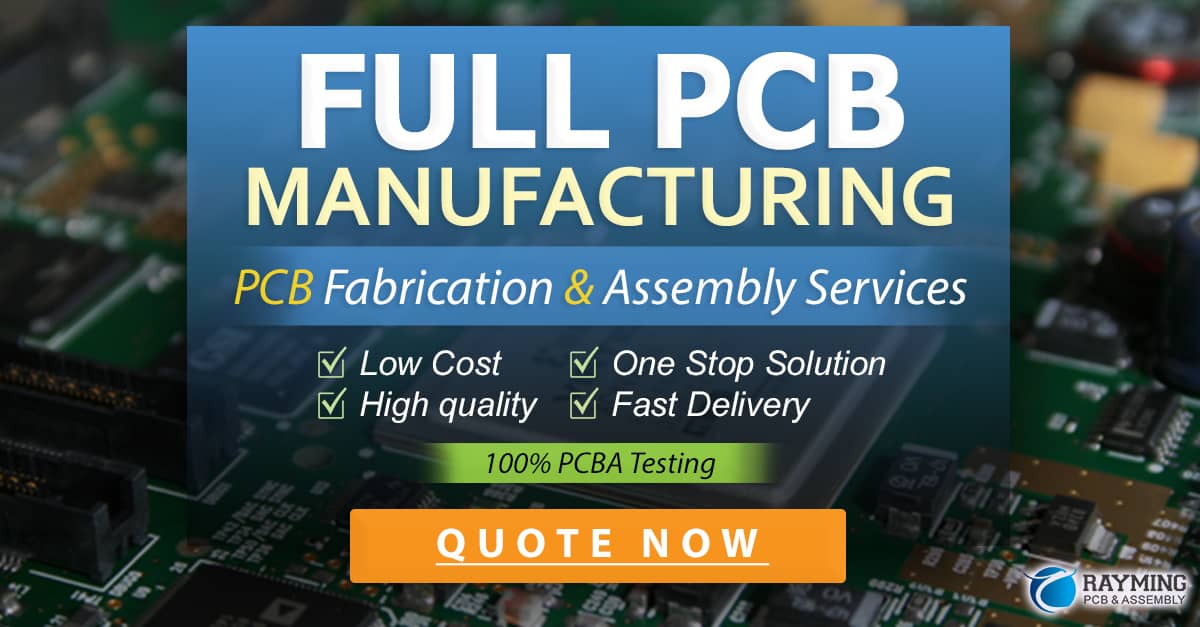
Fine Pitch PCB Assembly Process
The fine pitch PCB assembly process involves several key steps to ensure the successful mounting and soldering of components.
Solder Paste Printing
The first step in fine pitch PCB assembly is the application of solder paste to the pads using a stencil. The stencil is aligned with the PCB, and solder paste is applied using a squeegee or automated printing machine. The stencil design and printing process parameters must be carefully controlled to ensure the proper volume and distribution of solder paste.
Component Placement
Once the solder paste has been applied, the fine pitch components are placed on the PCB using high-precision pick-and-place machines. These machines use vision systems to ensure accurate alignment and placement of the components. The placement process must be carefully monitored to prevent component shifting or tombstoning.
Reflow Soldering
After component placement, the PCB undergoes reflow soldering, where the board is heated to a specific temperature profile to melt the solder paste and form reliable solder joints. The reflow profile must be carefully controlled to ensure proper solder joint formation and to prevent component damage due to excessive heat exposure.
Inspection and Testing
Following the reflow soldering process, the PCB undergoes visual inspection and automated optical inspection (AOI) to detect any soldering defects or component placement issues. Additionally, functional testing and boundary scan testing may be performed to ensure the proper operation of the assembled PCB.
Frequently Asked Questions (FAQ)
- What is the minimum pitch that can be achieved with fine pitch PCB assembly?
-
The minimum pitch achievable with fine pitch PCB assembly depends on various factors, such as the component package type, PCB manufacturing capabilities, and assembly process employed. Currently, pitches as small as 0.2mm can be achieved with advanced manufacturing techniques and specialized equipment.
-
What are some common defects encountered in fine pitch PCB assembly?
-
Some common defects encountered in fine pitch PCB assembly include solder bridging, insufficient solder, component misalignment, tombstoning, and solder balling. These defects can be caused by issues in the design, stencil printing, component placement, or reflow soldering processes.
-
How can solder bridging be prevented in fine pitch PCB assembly?
-
Solder bridging can be prevented by ensuring proper stencil design, controlling solder paste volume and distribution, optimizing reflow profiles, and using no-clean flux to reduce the surface tension of the molten solder. Additionally, the use of solder masks and selective soldering techniques can help minimize the risk of bridging.
-
What type of inspection methods are used for fine pitch PCB assembly?
-
Visual inspection, automated optical inspection (AOI), and X-ray inspection are commonly used methods for inspecting fine pitch PCB assemblies. AOI systems use high-resolution cameras and advanced algorithms to detect soldering defects and component placement issues, while X-ray inspection allows for the examination of solder joints beneath components.
-
How can thermal management be improved in fine pitch PCB designs?
- Thermal management in fine pitch PCB designs can be improved by incorporating thermal vias to conduct heat away from components, using high-thermal-conductivity PCB materials, and implementing heat sinks or other cooling solutions. Additionally, proper component placement and the use of thermal interface materials can help dissipate heat more effectively.
Conclusion
Fine pitch PCB assembly is a critical process in the manufacturing of high-density, high-performance electronic devices. By understanding the challenges and design considerations associated with fine pitch PCB assembly, engineers and manufacturers can ensure the successful production of reliable and cost-effective PCBs.
Through careful component selection, optimized pad and trace design, and adherence to DFM guidelines, designers can create fine pitch PCB layouts that are both manufacturable and functional. The use of advanced soldering techniques, high-precision placement equipment, and thorough inspection and testing procedures further ensures the quality and reliability of the assembled PCBs.
As technology continues to advance and the demand for smaller, more powerful devices grows, the importance of fine pitch PCB assembly will only continue to increase. By staying up-to-date with the latest design and manufacturing techniques, electronics manufacturers can remain competitive and meet the ever-evolving needs of their customers.
0 Comments