Improper Solder Paste Application
One of the most frequent problems in LED PCB Assembly is applying the solder paste improperly. If too much or too little solder paste is used, or if it is not applied evenly, it can lead to issues like bridging, tombstoning, or insufficient solder joints.
Some common causes of improper solder paste application include:
Cause | Description |
---|---|
Stencil misalignment | The solder paste stencil is not aligned correctly with the PCB pads |
Incorrect stencil thickness | Using a stencil that is too thick or thin for the specific component and pad sizes |
Poor paste release | The solder paste does not release cleanly from the stencil apertures |
Inadequate paste viscosity | The solder paste has an incorrect viscosity for the application method |
To ensure proper solder paste application, consider these solutions:
- Use a high-quality stencil that is precision cut for your specific LED PCB design
- Verify the stencil alignment before beginning the solder paste application
- Select an appropriate stencil thickness based on the pad and component sizes
- Optimize the solder paste properties like viscosity and bead size for your process
- Regularly clean and maintain the stencil and solder paste dispenser
- Implement solder paste inspection (SPI) to detect any defects early
LED Component Shifting
Another common issue is shifting or misalignment of the LED components during the pick-and-place or reflow process. Even small amounts of component movement can cause illumination issues in the final product.
LED component shifting often happens due to:
Cause | Description |
---|---|
Vibration | Excessive vibration during the pick-and-place causes components to move |
Improper placement force | Using too much force during component placement disturbs their positioning |
Unbalanced LED orientation | Rectangular LEDs placed off-center are prone to shifting |
Insufficient solder paste | Not enough solder paste fails to hold the component securely |
To mitigate LED component shifting, try these solutions:
- Minimize vibration in the pick-and-place machine through dampening and calibration
- Adjust the placement force and speed settings for the delicate LED components
- Ensure LEDs are centered properly on their pads during placement
- Use an adequate amount of solder paste to anchor the components
- Consider using an adhesive underfill material for additional LED stability
- Inspect placement accuracy with AOI (automated optical inspection) before reflow
Incorrect LED Polarity
Since LEDs are polarized components, they must be placed in the correct orientation to function properly. Placing LEDs with incorrect polarity is a common mistake that causes them to not illuminate.
Typical reasons for LED polarity errors include:
Cause | Description |
---|---|
Similar LED appearance | LEDs with symmetrical packages can be placed backwards |
Unclear polarity marking | Hard to see or inconsistent polarity indicators on the LED |
Polarity not checked | Neglecting to verify LED orientation during inspection |
Improper pick-and-place setup | Machine placing components with wrong polarity |
To avoid LED polarity problems, consider these tips:
- Select LED packages with clear and prominent polarity markings
- Verify the polarity of the LEDs during incoming inspection
- Ensure the pick-and-place machine is set up to recognize LED polarity
- Visually check LED orientation after placement, before reflow soldering
- Perform illuminated testing after assembly to catch any polarity errors
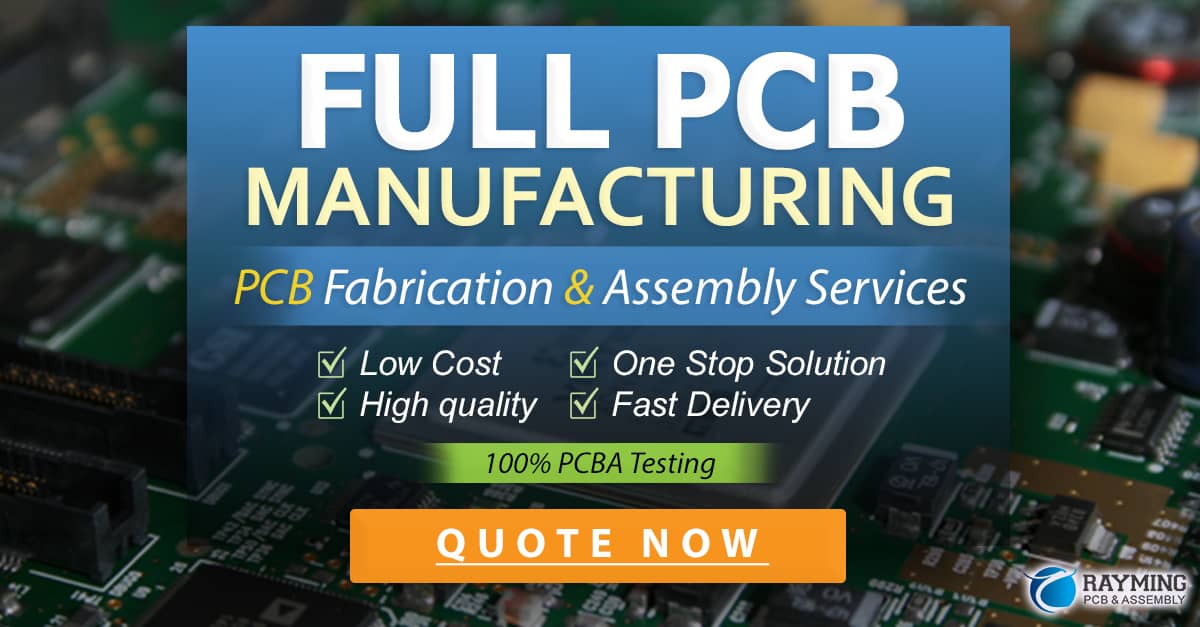
Thermal Damage to LEDs
LEDs are sensitive to high temperatures, so thermal damage is a concern during the soldering process. Overheating the LEDs can degrade their performance, shorten their lifespan, or cause immediate failure.
Common causes of LED thermal damage are:
Cause | Description |
---|---|
Excessive soldering temperature | Applying more heat than the LED is rated to withstand |
Prolonged heat exposure | Leaving the LED exposed to high soldering temperatures for too long |
Insufficient heat sinking | Not using proper thermal management techniques during soldering |
To prevent overheating LEDs, follow these guidelines:
- Know the maximum soldering temperature specified in the LED datasheet
- Minimize the exposure time to high temperatures during soldering
- Use a reflow oven profile tailored for the heat sensitivity of the LEDs
- Attach LEDs to a heat spreading metal core PCB or heat sink substrate
- Optimize the thermal path from the LED thermal pad to the PCB
- Consider using lower temperature solder alloys for LED attachment
Poor Optical Performance
The ultimate goal of LED PCB assembly is to create a product with optimal illumination properties. However, various defects can degrade the optical performance, resulting in uneven illumination, color inconsistency, or low light output.
Factors that commonly impact LED optical performance include:
Factor | Description |
---|---|
Incorrect LED binning | Noticeable variations in color or brightness between LEDs |
Obstructed light emission | Components or solder residue blocking part of the LED lens |
Suboptimal PCB layout | LED placement and trace routing causing inconsistent current |
Diffuser/optics issues | Poor integration of secondary optics reducing efficiency |
To optimize the optical performance of your LED PCB assembly:
- Source LEDs from reputable suppliers with tightly controlled binning
- Verify binning conformity through incoming inspection and testing
- Design the PCB layout to deliver even current to all LEDs
- Ensure no obstructions are present in the LED optical path
- Simulate the optical performance using ray tracing software tools
- Incorporate high efficiency PCB materials and thermal substrates
- Properly integrate secondary optics and diffusers for beam shaping
Electrostatic Discharge (ESD) Damage
Many types of LED components are highly sensitive to electrostatic discharge. ESD events can happen at various points in the LED PCB assembly process, potentially damaging the LEDs and reducing yield.
Typical ESD risk areas include:
Process Step | ESD Risk |
---|---|
Component handling | Human contact, unprotected workstations |
PCB loading/unloading | Contact with machines, conveyors, racks |
Soldering operations | Charged soldering tools, ungrounded equipment |
Testing and inspection | Contact with test probes, fixtures, instruments |
To protect LEDs from ESD damage, implement a robust ESD control program:
- Establish ESD safe workstations with grounded mats and wrist straps
- Use ESD safe storage and transport materials for PCBs and components
- Properly ground all equipment and machinery used in the process
- Ionize the air to neutralize any static buildup in the assembly area
- Conduct ESD training for all personnel handling the PCBs or components
- Continuously monitor the ESD control measures using static field meters
Inadequate Quality Control
Comprehensive quality control is essential for identifying and rectifying defects in LED PCB assembly. Inadequate inspection and testing can allow subpar products to slip through, leading to field failures and returns.
Quality control oversights often stem from:
Cause | Description |
---|---|
Skipping inspection steps | Not performing needed checks after key process steps |
Improper AOI programming | Automated inspection not set up to catch certain flaws |
Insufficient testing | Only doing basic functional tests, not parametric or stress tests |
Lack of traceability | No tracking of materials, processes, and test results by serial number |
To ensure robust quality control for your LED PCB assemblies:
- Define and document a full inspection and test plan for production
- Incorporate automated inspection like AOI, SPI, and X-ray where suitable
- Regularly validate and update the inspection machine programming
- Perform both functional and parametric testing on the final assembly
- Conduct accelerated life and stress tests to verify long-term reliability
- Implement a defect tracking system for continuous process improvement
- Maintain full traceability of materials, processes, and test results
By being aware of these common LED PCB assembly issues and taking proactive steps to mitigate them, you can improve your manufacturing yield, product quality, and customer satisfaction. Partnering with an experienced LED PCB assembly provider can also help you navigate these challenges successfully.
FAQ
What is the most common defect in LED PCB assembly?
One of the most frequent issues is improper solder paste application, which can lead to bridging, tombstoning, or poor solder joints. Implementing solder paste inspection (SPI) helps catch these defects early.
How can I ensure the LEDs are placed with the correct polarity?
To avoid LED polarity errors, choose LED packages with clear polarity markings, verify orientation during inspection, set up machines properly, and check illumination after assembly.
What causes LEDs to have inconsistent brightness or color?
Inconsistent LED optical performance often stems from incorrect binning, obstructed light emission, suboptimal current distribution, or secondary optic issues. Careful supplier selection, PCB layout, and optical design help minimize variations.
How can I prevent ESD from damaging LEDs during the assembly process?
Protecting LEDs from ESD requires a comprehensive control program including grounded workstations, ESD safe handling materials, air ionization, personnel training, and continuous monitoring.
What testing should I perform to validate the quality of the LED PCB assemblies?
A thorough quality control plan for LED PCBs should include automated optical inspection (AOI), functional testing, parametric verification, stress testing, and accelerated life testing to ensure long-term reliability. Full traceability of the process and materials is also important.
0 Comments