Introduction
When it comes to assembling printed circuit boards (PCBs), there are two primary methods used in the industry: wave soldering and reflow soldering. Both techniques have their advantages and disadvantages, and the choice between them depends on various factors such as the type of components, board complexity, production volume, and cost. In this article, we will dive deep into the differences between wave soldering and reflow soldering, their applications, and help you determine which method is best suited for your PCB Assembly needs.
What is Wave Soldering?
Wave soldering is a process that involves passing a PCB over a molten solder wave to create electrical connections between the components and the board. The process begins with applying flux to the bottom side of the PCB to clean and prepare the surface for soldering. The board is then placed on a conveyor belt that moves it over a preheating zone to activate the flux and prevent thermal shock to the components.
As the PCB moves further along the conveyor, it passes over a molten solder wave. The solder wave is created by pumping molten solder through a nozzle, forming a standing wave that contacts the bottom of the PCB. The solder adheres to the exposed metal surfaces, creating a strong electrical and mechanical bond between the components and the board.
Advantages of Wave Soldering
-
Suitable for through-hole components: Wave soldering is ideal for soldering through-hole components, which have long leads that extend through the holes in the PCB.
-
High throughput: Wave soldering is a fast process that can handle high-volume production runs, making it suitable for large-scale manufacturing.
-
Cost-effective: Wave soldering is generally less expensive than reflow soldering, especially for high-volume production.
-
Flexibility: Wave soldering allows for the soldering of mixed technology boards, which contain both through-hole and surface mount components.
Disadvantages of Wave Soldering
-
Limited component compatibility: Wave soldering is not suitable for certain types of surface mount components, such as fine-pitch devices or those with heat-sensitive packaging.
-
Potential for defects: Wave soldering can lead to defects such as bridging (unintended connections between adjacent pins), solder skips (missing solder on some pins), and solder balls (small spheres of solder that adhere to the board).
-
Board design constraints: The PCB layout must be designed with wave soldering in mind, ensuring adequate clearance between components and proper hole sizing.
What is Reflow Soldering?
Reflow soldering is a process that involves applying solder paste to the PCB, placing the surface mount components onto the solder paste, and then heating the entire assembly in a reflow oven to melt the solder and create a strong bond between the components and the board.
The process begins with the application of solder paste to the PCB using a stencil or screen printing method. The solder paste is a mixture of tiny solder particles suspended in a flux medium. Once the solder paste is applied, the surface mount components are placed onto the board using a pick-and-place machine or by hand.
The populated PCB is then placed in a reflow oven, which heats the board in a controlled manner following a specific temperature profile. The temperature profile typically consists of four stages: preheat, thermal soak, reflow, and cooling. During the reflow stage, the solder paste melts and forms a strong bond between the components and the PCB pads.
Advantages of Reflow Soldering
-
Suitable for surface mount components: Reflow soldering is the preferred method for soldering surface mount components, which have small leads or terminations that sit directly on the PCB pads.
-
High precision: Reflow soldering allows for the accurate placement and soldering of fine-pitch components, ensuring a high degree of precision and reliability.
-
Automated process: Reflow soldering is a highly automated process, which reduces the risk of human error and ensures consistent quality across production runs.
-
Reduced thermal stress: The controlled heating profile in reflow soldering minimizes thermal stress on the components and the PCB, reducing the risk of damage.
Disadvantages of Reflow Soldering
-
Higher initial investment: Reflow soldering requires specialized equipment such as stencil printers, pick-and-place machines, and reflow ovens, which can be more expensive than wave soldering equipment.
-
Limited compatibility with through-hole components: Reflow soldering is primarily used for surface mount components and is not well-suited for soldering through-hole components.
-
Solder paste shelf life: Solder paste has a limited shelf life and must be stored and handled properly to maintain its quality and performance.
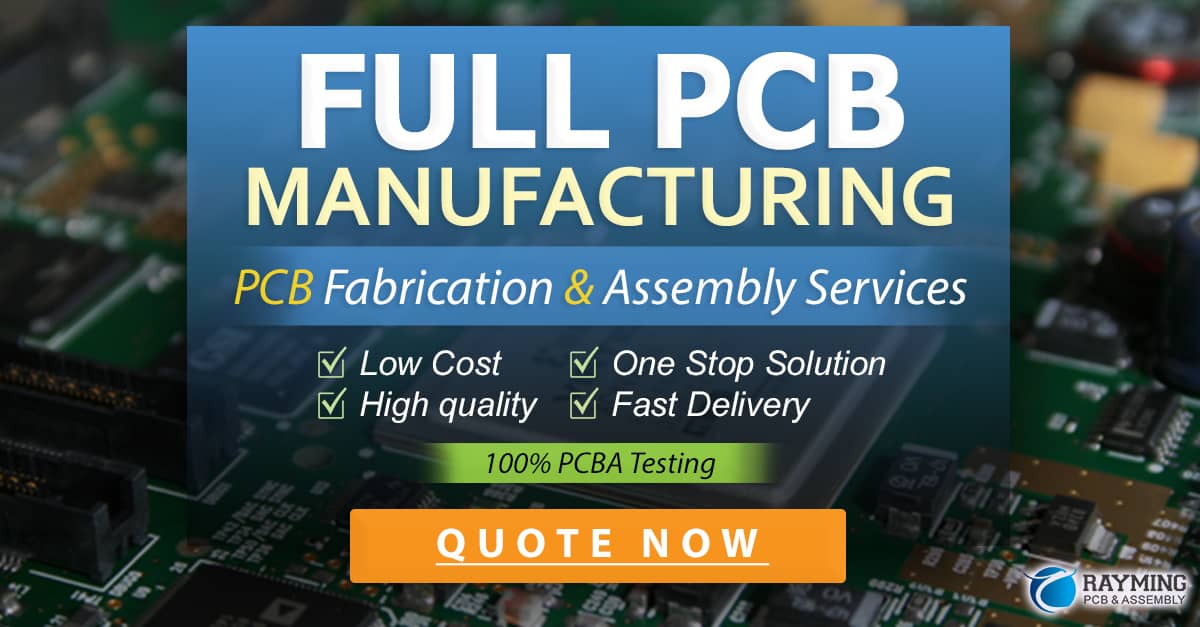
Comparing Wave Soldering and Reflow Soldering
Factor | Wave Soldering | Reflow Soldering |
---|---|---|
Component Compatibility | Through-hole and some surface mount | Surface mount |
Production Volume | High | Medium to High |
Precision | Moderate | High |
Cost | Lower | Higher |
Defects | Bridging, solder skips, solder balls | Fewer defects |
Board Design Constraints | Clearance and hole sizing | Minimal constraints |
Thermal Stress | Higher | Lower |
Choosing the Right Soldering Method
When deciding between wave soldering and reflow soldering for your PCB assembly, consider the following factors:
-
Component types: If your PCB primarily uses through-hole components, wave soldering is the better choice. If your board mainly consists of surface mount components, reflow soldering is the preferred method.
-
Production volume: For high-volume production runs, wave soldering may be more cost-effective. However, if your production volumes are medium to high and you require high precision, reflow soldering may be the better option.
-
Board complexity: Reflow soldering is better suited for complex boards with fine-pitch components and tight spacing. Wave soldering may be more appropriate for simpler board designs with larger components.
-
Budget: Wave soldering generally has a lower initial investment cost compared to reflow soldering. However, consider the long-term costs, including defect rates and rework, when making your decision.
FAQ
-
Q: Can wave soldering and reflow soldering be used together on the same PCB?
A: Yes, it is possible to use both wave soldering and reflow soldering on the same PCB in a process called mixed technology assembly. In this case, the surface mount components are typically reflowed first, followed by wave soldering of the through-hole components. -
Q: What is selective soldering, and how does it differ from wave soldering?
A: Selective soldering is a process that uses a localized solder wave or mini-wave to solder specific areas or components on a PCB. It differs from traditional wave soldering in that it targets only the desired areas, minimizing the risk of bridging or other defects on nearby components. -
Q: Can reflow soldering be used for double-sided PCBs?
A: Yes, reflow soldering can be used for double-sided PCBs. In this case, the process is called double-sided reflow soldering. The PCB is first reflowed on one side, then flipped over, and reflowed on the other side. Special fixtures or adhesives may be used to hold the components in place during the second reflow process. -
Q: What is the role of flux in wave soldering and reflow soldering?
A: Flux is a chemical agent that is used in both wave soldering and reflow soldering to clean and prepare the metal surfaces for soldering. It removes oxides and contaminants from the PCB pads and component leads, promoting better solder wetting and a stronger bond. -
Q: Are there any environmental concerns associated with wave soldering and reflow soldering?
A: Both wave soldering and reflow soldering processes can have environmental impacts if not managed properly. The use of lead-based solder, which is now restricted in many countries, can be a concern. Additionally, the flux used in these processes can generate fumes and waste that must be properly ventilated and disposed of in accordance with local regulations.
Conclusion
Wave soldering and reflow soldering are both essential methods for PCB assembly, each with its own strengths and weaknesses. Wave soldering is best suited for through-hole components and high-volume production, while reflow soldering is ideal for surface mount components and high-precision assembly.
When choosing between these two methods, consider factors such as component types, production volume, board complexity, and budget. In some cases, a combination of both methods, known as mixed technology assembly, may be the best approach.
By understanding the differences between wave soldering and reflow soldering and carefully evaluating your specific PCB assembly needs, you can select the most appropriate soldering method to ensure the highest quality, reliability, and cost-effectiveness for your project.
0 Comments