Key Characteristics of 6 Layer PCB Boards
Increased Circuit Complexity
One of the main advantages of using a 6 layer PCB is the ability to design more complex circuits. With six conductive layers available, designers have more routing options and can incorporate a greater number of components and connections within a smaller area. This is particularly beneficial for advanced electronics such as smartphones, medical devices, aerospace systems, and high-performance computing hardware.
Improved Signal Integrity
6 layer PCBs offer improved signal integrity compared to boards with fewer layers. By strategically arranging signal traces on different layers and utilizing proper grounding and shielding techniques, designers can minimize crosstalk, electromagnetic interference (EMI), and signal distortion. This ensures that the signals remain clean and stable, which is critical for high-speed digital circuits and sensitive analog signals.
Enhanced Thermal Management
Another advantage of 6 layer PCBs is enhanced thermal management. With multiple layers, designers can create dedicated power and ground planes that provide low-impedance paths for current flow. This helps to distribute heat more evenly across the board, reducing hot spots and improving overall thermal performance. Additionally, the increased surface area of the copper layers allows for better heat dissipation, which is crucial for high-power components and devices operating in harsh environments.
Miniaturization and Space Savings
6 layer PCBs enable greater miniaturization and space savings compared to boards with fewer layers. By utilizing the additional routing space provided by the extra layers, designers can reduce the overall size of the PCB while still accommodating a large number of components. This is particularly important for portable devices, wearables, and other applications where space is at a premium.
Layer Stack-up and Construction
A typical 6 layer PCB Stack-up consists of the following layers:
- Top Layer (Signal)
- Ground Plane
- Inner Layer 1 (Signal)
- Inner Layer 2 (Signal)
- Power Plane
- Bottom Layer (Signal)
The signal layers are used for routing traces and placing components, while the ground and power planes provide stable reference voltages and distribute power efficiently throughout the board. The insulating material between the layers is typically made of FR-4, a glass-reinforced epoxy laminate that offers good mechanical and electrical properties.
Here’s a visual representation of a 6 layer PCB stack-up:
Layer | Type |
---|---|
Top | Signal |
Plane 1 | Ground |
Inner 1 | Signal |
Inner 2 | Signal |
Plane 2 | Power |
Bottom | Signal |
Design Considerations for 6 Layer PCBs
Signal Integrity and EMI Control
When designing a 6 layer PCB, it’s essential to follow best practices for signal integrity and EMI control. This includes:
- Proper trace routing and spacing to minimize crosstalk and interference
- Appropriate use of ground and power planes for shielding and noise reduction
- Impedance matching and termination techniques to maintain signal quality
- Careful placement of high-speed components and sensitive analog circuits
Designers should also consider the use of electromagnetic compatibility (EMC) simulation tools to analyze and optimize the board’s performance in terms of signal integrity and EMI.
Thermal Management and Power Distribution
Effective thermal management and power distribution are critical for 6 layer PCBs, especially those with high-power components or operating in harsh environments. Designers should consider the following:
- Proper sizing and placement of power and ground planes to minimize voltage drops and ensure even current distribution
- Adequate copper thickness and width for high-current traces to prevent excessive heating
- Use of thermal vias and heat sinks to dissipate heat from hot spots
- Incorporation of thermal management features such as phase change materials or active cooling solutions
Manufacturing and Assembly Considerations
6 layer PCBs require more advanced manufacturing and assembly processes compared to simpler boards. Designers should work closely with their PCB fabrication and assembly partners to ensure that the board meets all manufacturing requirements and tolerances. This includes:
- Specifying appropriate materials, copper weights, and finish options
- Defining clear and accurate design rules and constraints
- Providing comprehensive documentation, including Gerber files, drill files, and assembly drawings
- Conducting thorough design reviews and prototyping to identify and resolve any issues before mass production
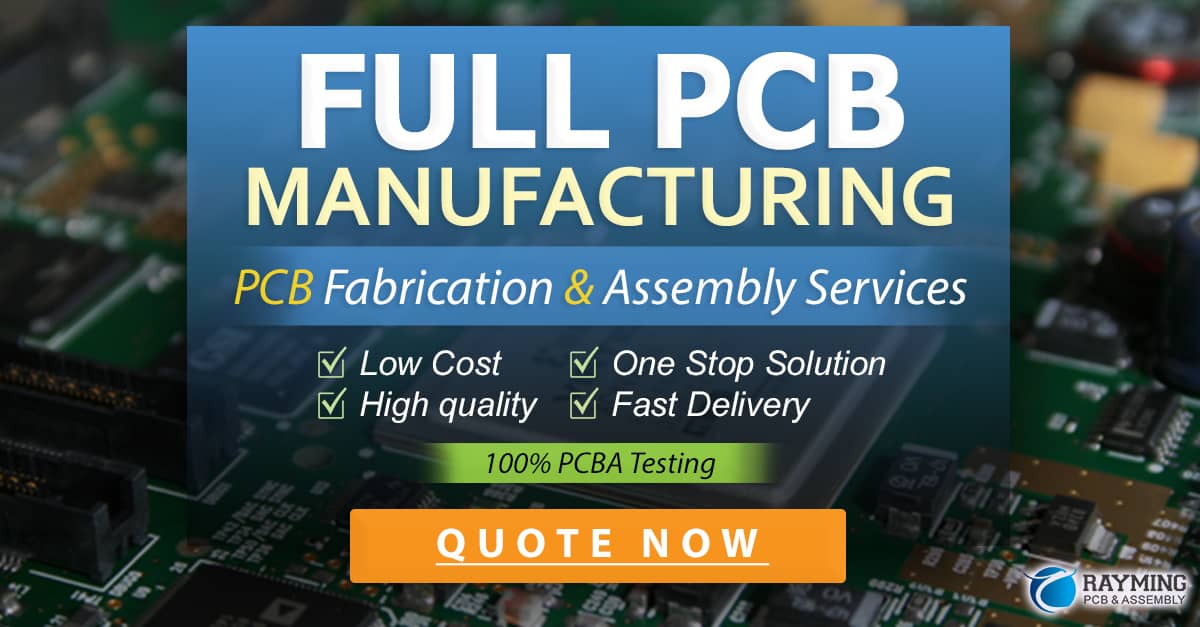
Applications of 6 Layer PCBs
6 layer PCBs are used in a wide range of advanced electronics applications, including:
- Smartphones and tablets
- Wearable devices
- Medical equipment
- Automotive electronics
- Aerospace and defense systems
- High-performance computing hardware
- Industrial automation and control systems
- Telecommunications infrastructure
In each of these applications, 6 layer PCBs provide the necessary complexity, reliability, and performance to meet the demanding requirements of modern electronics.
Frequently Asked Questions (FAQ)
1. What is the difference between a 4 layer and 6 layer PCB?
A 4 layer PCB has four conductive layers (two signal layers and two plane layers), while a 6 layer PCB has six conductive layers (four signal layers and two plane layers). The additional layers in a 6 layer PCB allow for more complex routing, better signal integrity, and improved thermal management compared to a 4 layer PCB.
2. Are 6 layer PCBs more expensive than 4 layer PCBs?
Yes, 6 layer PCBs are generally more expensive than 4 layer PCBs due to the increased complexity of manufacturing and the additional materials required. However, the higher cost is often justified by the improved performance and functionality offered by 6 layer PCBs in advanced electronics applications.
3. Can 6 layer PCBs be used for high-frequency applications?
Yes, 6 layer PCBs are well-suited for high-frequency applications such as RF and microwave circuits. The additional layers allow for better control of signal integrity, impedance matching, and EMI, which are critical for maintaining signal quality and minimizing losses at high frequencies.
4. How do I choose the right layer stack-up for my 6 layer PCB?
The choice of layer stack-up for a 6 layer PCB depends on the specific requirements of your application, such as signal integrity, power distribution, and EMI control. Factors to consider include the types of signals (digital, analog, or mixed-signal), the operating frequencies, the power requirements, and the environmental conditions. It’s best to consult with experienced PCB designers or your fabrication partner to determine the optimal stack-up for your project.
5. What are some best practices for designing 6 layer PCBs?
Some best practices for designing 6 layer PCBs include:
- Following proper signal integrity and EMI control guidelines
- Using appropriate grounding and shielding techniques
- Optimizing power distribution and thermal management
- Adhering to manufacturing and assembly requirements and tolerances
- Conducting thorough design reviews and prototyping before mass production
By following these best practices, you can ensure that your 6 layer PCB design is robust, reliable, and performs optimally in your target application.
Conclusion
6 layer PCBs are an essential component in many advanced electronics applications, offering increased circuit complexity, improved signal integrity, enhanced thermal management, and greater miniaturization compared to simpler PCBs. By understanding the key characteristics, design considerations, and best practices associated with 6 layer PCBs, engineers and designers can create high-performance, reliable, and cost-effective solutions for a wide range of industries and applications.
0 Comments