Introduction
Printed circuit boards (PCBs) are essential components in a wide range of electronic devices, including medical equipment. Medical PCBs play a critical role in ensuring the reliability, safety, and performance of medical devices that are used to diagnose, treat, and monitor patients. Medical PCB Manufacturers specialize in producing high-quality, custom-designed PCBs that meet the stringent requirements of the medical industry.
In this article, we will explore the role of medical PCB manufacturers, the challenges they face, and the factors to consider when selecting the best manufacturer for your medical device project.
What Are Medical PCBs?
Medical PCBs are specialized printed circuit boards designed to meet the unique requirements of medical devices. These PCBs are used in a variety of medical applications, including:
- Diagnostic equipment (e.g., MRI machines, CT scanners, X-ray machines)
- Monitoring devices (e.g., heart rate monitors, blood pressure monitors, EEG machines)
- Treatment devices (e.g., pacemakers, defibrillators, insulin pumps)
- Laboratory equipment (e.g., centrifuges, microscopes, analytical instruments)
Medical PCBs must be designed and manufactured to the highest standards to ensure patient safety, device reliability, and compliance with regulatory requirements. Some of the key characteristics of medical PCBs include:
- High reliability and durability
- Resistance to harsh environments (e.g., chemicals, moisture, temperature extremes)
- Electromagnetic compatibility (EMC) and electromagnetic interference (EMI) shielding
- Miniaturization and high-density packaging
- Biocompatibility (for implantable devices)
- Compliance with industry standards and regulations (e.g., ISO 13485, IEC 60601-1)
The Role of Medical PCB Manufacturers
Medical PCB manufacturers play a crucial role in the development and production of medical devices. They work closely with medical device companies to design, prototype, and manufacture custom PCBs that meet the specific requirements of each application.
The key responsibilities of medical PCB manufacturers include:
1. PCB Design and Engineering
Medical PCB manufacturers have experienced PCB designers and engineers who work with medical device companies to create custom PCB layouts and schematics. They use advanced design tools and techniques to optimize PCB performance, reliability, and manufacturability.
2. Prototyping and Testing
Once the PCB design is finalized, medical PCB manufacturers create prototypes for testing and validation. They use state-of-the-art equipment and processes to fabricate and assemble Prototype PCBs, which are then subjected to rigorous testing to ensure they meet the required specifications and standards.
3. PCB Fabrication and Assembly
Medical PCB manufacturers have specialized facilities and equipment for high-volume PCB fabrication and assembly. They use advanced manufacturing techniques, such as multi-layer PCBs, HDI (high-density interconnect) PCBs, and flexible PCBs, to produce high-quality, reliable PCBs for medical devices.
4. Quality Control and Inspection
Medical PCB manufacturers have stringent quality control and inspection processes in place to ensure that every PCB meets the required specifications and standards. They use automated inspection systems, such as AOI (automated optical inspection) and X-ray inspection, to detect and correct any defects or issues during the manufacturing process.
5. Regulatory Compliance
Medical PCB manufacturers must comply with various industry standards and regulations, such as ISO 13485 (quality management system for medical devices), IEC 60601-1 (safety and essential performance of medical electrical equipment), and FDA regulations. They must maintain proper documentation, traceability, and quality control records to demonstrate compliance with these standards.
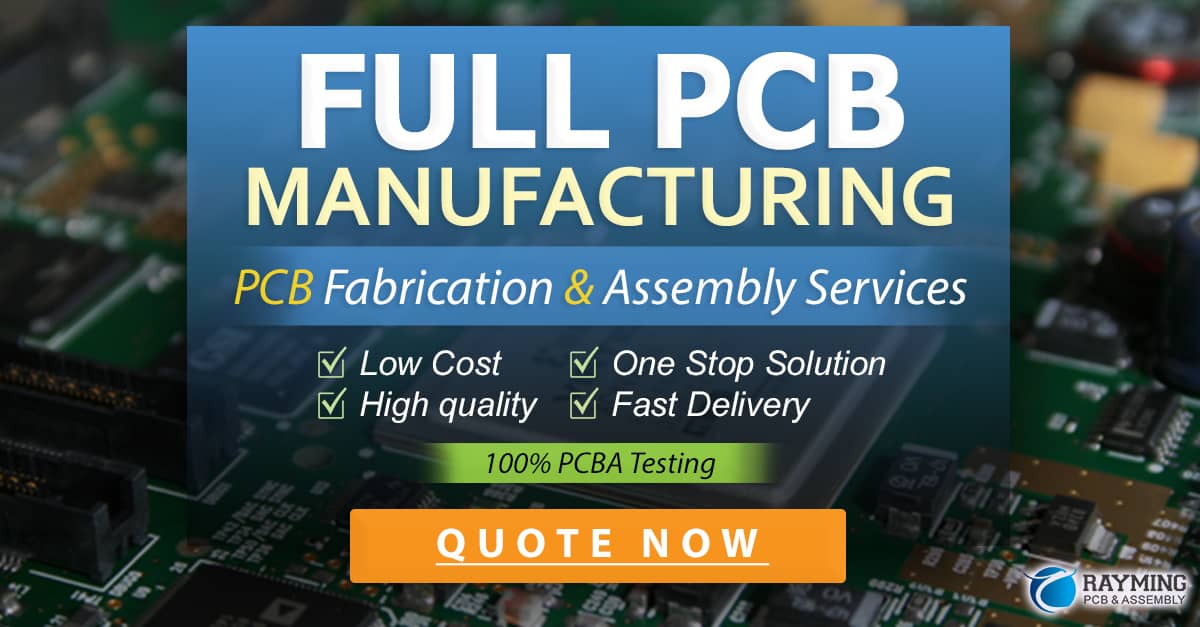
Challenges Faced by Medical PCB Manufacturers
Medical PCB manufacturers face several challenges in designing and producing PCBs for medical devices:
1. Stringent Regulatory Requirements
Medical devices are subject to strict regulatory requirements to ensure patient safety and device effectiveness. Medical PCB manufacturers must comply with various standards and regulations, such as ISO 13485, IEC 60601-1, and FDA regulations. Compliance with these requirements involves significant documentation, testing, and quality control processes, which can be time-consuming and costly.
2. Complexity and Miniaturization
Medical devices are becoming increasingly complex and miniaturized, requiring PCBs with high-density interconnects, fine-pitch components, and multi-layer structures. Designing and manufacturing these complex PCBs requires advanced tools, techniques, and expertise, which can be challenging for some manufacturers.
3. Reliability and Durability
Medical PCBs must be highly reliable and durable, as they are often used in critical life-support devices and harsh environments. Manufacturers must use high-quality materials, advanced manufacturing processes, and rigorous testing to ensure that PCBs can withstand the required operating conditions and have a long service life.
4. Cost Pressure
Medical device companies face increasing pressure to reduce costs while maintaining high quality and regulatory compliance. Medical PCB manufacturers must find ways to optimize their processes, reduce waste, and improve efficiency to remain competitive and meet their customers’ cost expectations.
Factors to Consider When Selecting a Medical PCB Manufacturer
Choosing the right medical PCB manufacturer is critical to the success of your medical device project. Here are some key factors to consider when selecting a manufacturer:
1. Experience and Expertise
Look for a manufacturer with extensive experience and expertise in designing and producing PCBs for medical devices. They should have a proven track record of working with medical device companies and be familiar with the relevant industry standards and regulations.
2. Quality Management System
Ensure that the manufacturer has a robust quality management system in place, such as ISO 13485 certification. This demonstrates their commitment to quality and their ability to consistently produce PCBs that meet the required specifications and standards.
3. Manufacturing Capabilities
Consider the manufacturer’s manufacturing capabilities, including their ability to produce complex, high-density PCBs, their capacity for high-volume production, and their use of advanced manufacturing techniques and equipment.
4. Testing and Inspection
Verify that the manufacturer has comprehensive testing and inspection processes in place, including automated optical inspection (AOI), X-ray inspection, and functional testing. This ensures that PCBs are thoroughly checked for defects and meet the required quality standards.
5. Customer Support and Communication
Choose a manufacturer that provides excellent customer support and communication throughout the entire project lifecycle. They should be responsive to your needs, provide regular updates on project status, and be willing to work closely with your team to resolve any issues that arise.
6. Cost and Lead Time
Consider the manufacturer’s pricing and lead times for PCB Prototyping and production. While cost is an important factor, it should not be the sole deciding factor. Look for a manufacturer that offers competitive pricing while maintaining high quality and reliability.
Factor | Importance |
---|---|
Experience and Expertise | High |
Quality Management System | High |
Manufacturing Capabilities | High |
Testing and Inspection | High |
Customer Support and Communication | Medium |
Cost and Lead Time | Medium |
FAQ
1. What certifications should a medical PCB manufacturer have?
A medical PCB manufacturer should have ISO 13485 certification, which is a quality management system specifically for medical devices. They may also have other certifications, such as ISO 9001 (general quality management) and IPC (Association Connecting Electronics Industries) certifications for PCB manufacturing.
2. How long does it typically take to prototype and produce medical PCBs?
The lead time for prototyping and producing medical PCBs can vary depending on the complexity of the design, the manufacturer’s capacity, and the specific requirements of the project. Typically, prototyping can take several weeks, while production lead times can range from a few weeks to several months.
3. What is the typical cost range for medical PCBs?
The cost of medical PCBs can vary widely depending on factors such as the complexity of the design, the materials used, the production volume, and the manufacturer’s pricing structure. In general, medical PCBs tend to be more expensive than standard PCBs due to the higher quality and reliability requirements. The cost can range from a few dollars per board for simple designs to hundreds of dollars per board for complex, high-density designs.
4. How can I ensure that my medical PCB design is manufacturable?
To ensure that your medical PCB design is manufacturable, it’s important to work closely with your chosen PCB manufacturer from the early stages of the design process. They can provide guidance on design for manufacturability (DFM) principles, such as component selection, layout optimization, and testability. They can also conduct design reviews and provide feedback on potential manufacturability issues before the design is finalized.
5. What should I do if I encounter quality issues with my medical PCBs?
If you encounter quality issues with your medical PCBs, the first step is to contact your PCB manufacturer and inform them of the problem. They should have a formal process for handling quality issues and customer complaints, which may include a root cause analysis, corrective action, and preventive action (CAPA) process. Work closely with the manufacturer to identify the cause of the issue and develop a plan to resolve it and prevent future occurrences.
Conclusion
Medical PCB manufacturers play a critical role in the development and production of medical devices, ensuring that PCBs meet the stringent quality, reliability, and regulatory requirements of the medical industry. When selecting a medical PCB manufacturer, it’s important to consider factors such as experience, quality management, manufacturing capabilities, testing and inspection, customer support, and cost.
By partnering with the right medical PCB manufacturer and working closely with them throughout the design and production process, medical device companies can ensure that their PCBs are of the highest quality and reliability, ultimately contributing to the safety and effectiveness of their medical devices.
0 Comments