Introduction to FastPCBManufacturing”>FastPCBManufacturing
In today’s fast-paced electronic industry, the demand for quick and efficient PCB manufacturing has never been higher. Printed Circuit Boards (PCBs) are the backbone of almost every electronic device, from smartphones to medical equipment. As such, manufacturers are constantly looking for ways to optimize their PCB production processes to meet the ever-growing demand while maintaining high quality standards. This article will discuss seven crucial factors that contribute to fast PCB manufacturing.
H2: 1. Design Optimization for FastPCBManufacturing
One of the most critical factors in fast PCB manufacturing is design optimization. A well-designed PCB can significantly reduce production time and minimize the risk of errors. Here are some key considerations for optimizing your PCB design:
H3: 1.1 Keep the Design Simple
A simple PCB design is easier to manufacture and less prone to errors. Avoid unnecessary complexity, such as excessive layering or dense component placement, whenever possible.
H3: 1.2 Use Standard Components
Using standard components can greatly speed up the manufacturing process. Custom or rare components may require additional sourcing time, which can delay production.
H3: 1.3 Adhere to Design Rules
Ensure that your PCB design adheres to the manufacturer’s design rules, such as minimum trace width, clearance, and hole size. Violating these rules can lead to production delays or even redesigns.
Design Rule | Minimum Value |
---|---|
Trace Width | 0.006 inches |
Clearance | 0.008 inches |
Hole Size | 0.020 inches |
Table 1: Example of PCB design rules
H2: 2. Material Selection for FastPCBManufacturing
The choice of materials can significantly impact the speed of PCB manufacturing. Consider the following factors when selecting materials:
H3: 2.1 Substrate Material
The most common substrate materials for PCBs are FR-4, Rogers, and Polyimide. FR-4 is the most widely used and cost-effective option, making it a good choice for fast manufacturing.
H3: 2.2 Copper Thickness
Thinner copper layers can be etched more quickly, reducing production time. However, ensure that the copper thickness is sufficient for your application’s current-carrying requirements.
H3: 2.3 Solder Mask and Silkscreen
Choose a solder mask and silkscreen that are compatible with your chosen substrate material and can be applied quickly and efficiently.
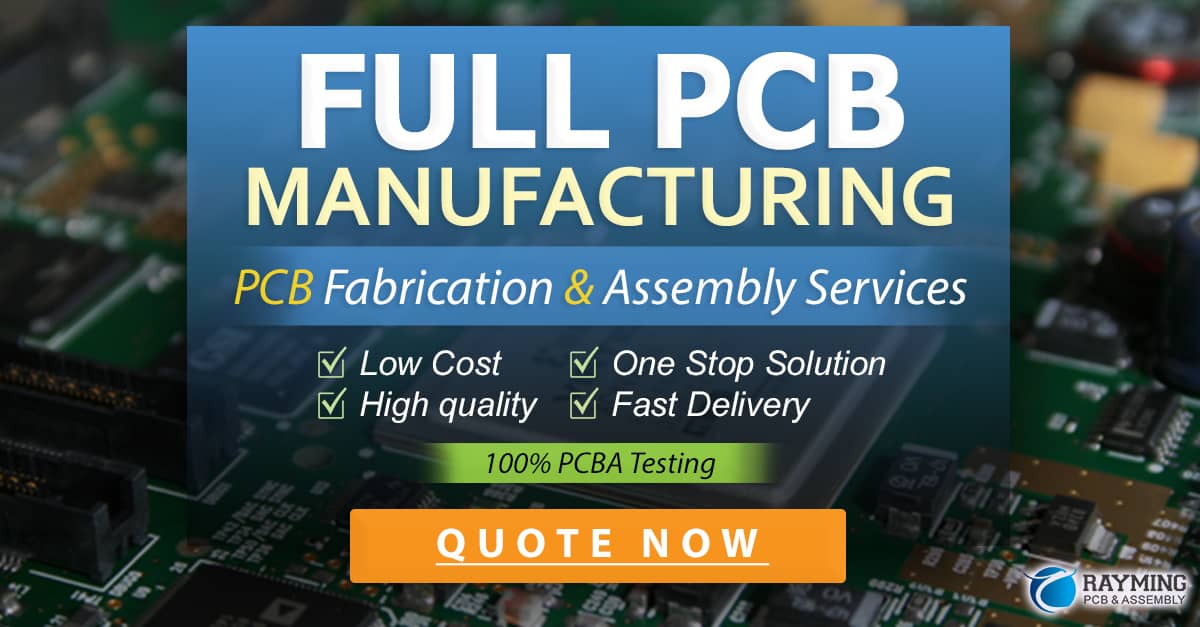
H2: 3. Panelization for FastPCBManufacturing
Panelization is the process of grouping multiple PCB designs onto a single panel for production. Effective panelization can significantly increase manufacturing speed and reduce costs. Consider the following:
H3: 3.1 Panel Size
Choose a panel size that maximizes the number of PCBs per panel while ensuring sufficient spacing for tooling and handling.
H3: 3.2 Tooling Holes and Fiducials
Include tooling holes and fiducials in your panel design to facilitate accurate alignment and processing during manufacturing.
H3: 3.3 Breakaway Tabs
Use breakaway tabs to securely hold the individual PCBs in place during manufacturing and allow for easy separation after production.
H2: 4. Automation and Equipment for FastPCBManufacturing
Investing in advanced automation and equipment can greatly accelerate PCB manufacturing. Some key technologies include:
H3: 4.1 Computer Numerical Control (CNC) Machines
CNC machines enable precise and rapid drilling, routing, and milling of PCBs, reducing manual labor and increasing consistency.
H3: 4.2 Automated Optical Inspection (AOI)
AOI systems use high-resolution cameras and advanced algorithms to quickly detect and identify defects in PCBs, ensuring quality control without slowing down production.
H3: 4.3 Surface Mount Technology (SMT) Lines
SMT lines automate the placement and soldering of surface-mount components, significantly reducing assembly time compared to manual methods.
H2: 5. Lean Manufacturing Principles for FastPCBManufacturing
Implementing lean manufacturing principles can streamline your PCB production process and reduce waste. Some key practices include:
H3: 5.1 Just-in-Time (JIT) Inventory Management
JIT inventory management ensures that materials and components are available when needed, without excess stock that can slow down production and increase costs.
H3: 5.2 Continuous Improvement (Kaizen)
Encourage a culture of continuous improvement, where employees are empowered to identify and implement process enhancements that can speed up manufacturing.
H3: 5.3 Value Stream Mapping
Use value stream mapping to visualize your entire PCB manufacturing process, identify bottlenecks, and eliminate non-value-added activities.
H2: 6. Supply Chain Optimization for FastPCBManufacturing
An efficient and reliable supply chain is crucial for fast PCB manufacturing. Consider the following strategies:
H3: 6.1 Supplier Consolidation
Consolidate your supplier base to a few key strategic partners who can provide high-quality materials and components with short lead times.
H3: 6.2 Vendor-Managed Inventory (VMI)
Implement VMI programs with your suppliers, where they maintain an agreed-upon inventory of critical components at your facility, reducing procurement time.
H3: 6.3 Logistics and Shipping
Optimize your logistics and shipping processes to ensure that materials and finished products are transported quickly and efficiently.
H2: 7. Collaboration and Communication for FastPCBManufacturing
Effective collaboration and communication among all stakeholders are essential for fast PCB manufacturing. Consider the following:
H3: 7.1 Design for Manufacturing (DFM) Feedback
Encourage open communication between your design team and the manufacturing team to ensure that designs are optimized for manufacturability from the outset.
H3: 7.2 Cross-Functional Teams
Create cross-functional teams that include representatives from design, manufacturing, quality control, and supply chain to foster collaboration and quickly resolve any issues that may arise.
H3: 7.3 Clear Documentation and Instructions
Maintain clear and comprehensive documentation, including bill of materials (BOM), assembly instructions, and quality control specifications, to ensure that all team members have the information they need to work efficiently.
Frequently Asked Questions (FAQ)
-
Q: What is the most important factor in fast PCB manufacturing?
A: Design optimization is arguably the most important factor, as a well-designed PCB can significantly reduce production time and minimize the risk of errors. -
Q: How can I ensure that my PCB design is optimized for fast manufacturing?
A: Keep your design simple, use standard components, and adhere to the manufacturer’s design rules to optimize your PCB design for fast manufacturing. -
Q: What materials should I choose for fast PCB manufacturing?
A: FR-4 is the most widely used and cost-effective substrate material, making it a good choice for fast manufacturing. Thinner copper layers can also help reduce production time. -
Q: How can automation and advanced equipment speed up PCB manufacturing?
A: Technologies like CNC machines, AOI systems, and SMT lines can significantly reduce manual labor, increase consistency, and accelerate PCB manufacturing. -
Q: What role does collaboration play in fast PCB manufacturing?
A: Effective collaboration and communication among design, manufacturing, quality control, and supply chain teams are essential for fostering a smooth and efficient PCB production process.
Conclusion
Fast PCB manufacturing is a critical aspect of staying competitive in today’s electronic industry. By focusing on these seven key factors – design optimization, material selection, panelization, automation and equipment, lean manufacturing principles, supply chain optimization, and collaboration – you can significantly accelerate your PCB production process while maintaining high quality standards. Implementing these strategies will help you meet the growing demand for quick turnaround times and stay ahead of the competition.
0 Comments