Introduction
Getting PCB Quotes online can be a daunting task, especially if you’re not familiar with the process. With so many manufacturers and options available, it’s easy to get overwhelmed and make mistakes that can cost you time and money. In this article, we’ll explore 11 common minefields to avoid when getting PCB quotes online, so you can get the best possible price and quality for your project.
1. Not Providing Enough Information
Why Providing Detailed Information is Crucial
When requesting PCB quotes online, it’s essential to provide as much information as possible about your project. This includes the number of layers, board size, material, thickness, copper weight, surface finish, and any special requirements. Without this information, manufacturers may not be able to provide accurate quotes, leading to delays and potential misunderstandings.
What Information Should You Provide?
To ensure you receive accurate PCB quotes, provide the following information:
Information | Description |
---|---|
Number of Layers | Specify the number of layers your PCB requires (e.g., 2, 4, 6, etc.) |
Board Size | Provide the dimensions of your PCB (length x width) |
Material | Specify the material for your PCB (e.g., FR-4, Rogers, etc.) |
Thickness | Indicate the thickness of your PCB (e.g., 0.8mm, 1.6mm, etc.) |
Copper Weight | Specify the copper weight for your PCB (e.g., 1oz, 2oz, etc.) |
Surface Finish | Choose the surface finish for your PCB (e.g., HASL, ENIG, etc.) |
Special Requirements | Mention any special requirements (e.g., impedance control, blind/buried vias, etc.) |
By providing this information upfront, you can help manufacturers provide more accurate quotes and avoid potential issues down the line.
2. Not Checking Manufacturer Capabilities
Why Checking Manufacturer Capabilities is Important
Not all PCB Manufacturers have the same capabilities. Some may specialize in certain types of PCBs, while others may have limitations on the materials or features they can accommodate. Before requesting quotes, it’s crucial to research manufacturers and ensure they can meet your project’s specific requirements.
How to Check Manufacturer Capabilities
To check a manufacturer’s capabilities, follow these steps:
- Visit the manufacturer’s website and look for information about their capabilities, such as the types of PCBs they produce, materials they work with, and any certifications they hold.
- Contact the manufacturer directly and ask about their experience with projects similar to yours.
- Request references or case studies from the manufacturer to see examples of their work.
By verifying manufacturer capabilities upfront, you can avoid wasting time on quotes from manufacturers who cannot meet your project’s needs.
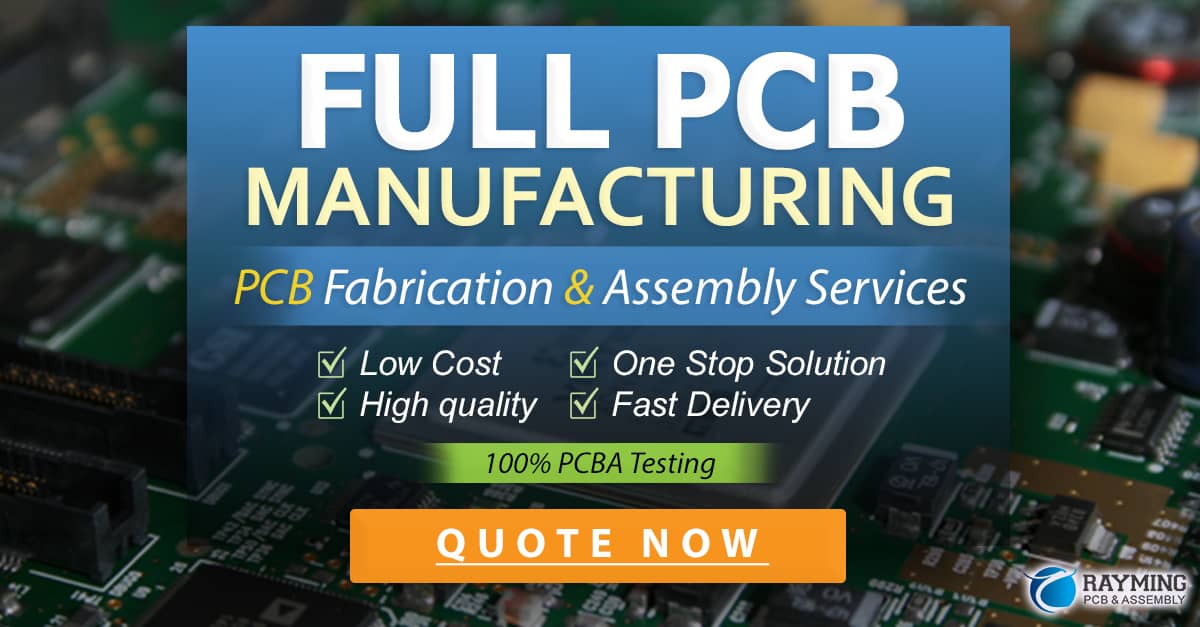
3. Not Considering Lead Times
The Importance of Lead Times
Lead times can vary significantly between manufacturers, depending on factors such as their production capacity, workload, and supply chain. When getting PCB quotes online, it’s essential to consider lead times to ensure your project stays on schedule.
How to Inquire About Lead Times
To inquire about lead times, follow these steps:
- When requesting quotes, ask manufacturers to provide estimated lead times for your project.
- If lead times are not specified in the quote, follow up with the manufacturer to clarify.
- Consider prioritizing manufacturers who can meet your project’s timeline, even if their prices are slightly higher.
By factoring in lead times during the quoting process, you can avoid delays and ensure your project stays on track.
4. Not Comparing Apples to Apples
The Importance of Consistent Specifications
When comparing PCB quotes from different manufacturers, it’s crucial to ensure that you’re comparing apples to apples. This means providing each manufacturer with the same specifications and requirements for your project. If specifications vary between quotes, it can be difficult to make an accurate comparison and choose the best option.
How to Ensure Consistent Specifications
To ensure consistent specifications when requesting PCB quotes, follow these steps:
- Create a detailed specification document that outlines all the requirements for your project, including the information mentioned in the “Not Providing Enough Information” section.
- Provide this specification document to each manufacturer when requesting quotes.
- If a manufacturer suggests changes or alterations to your specifications, make sure to update the specification document and provide the revised version to all manufacturers for requoting.
By maintaining consistent specifications across all quotes, you can make more accurate comparisons and choose the best manufacturer for your project.
5. Not Considering Quality and Reliability
The Importance of Quality and Reliability
While price is an important factor when choosing a PCB manufacturer, it shouldn’t be the only consideration. Quality and reliability are equally important, as they can impact the performance and longevity of your end product. Choosing a manufacturer based solely on price may lead to subpar PCBs that fail prematurely or cause other issues.
How to Evaluate Quality and Reliability
To evaluate a manufacturer’s quality and reliability, consider the following factors:
- Certifications: Look for manufacturers with relevant certifications, such as ISO 9001, UL, or IPC.
- Testing and Inspection: Ask about the manufacturer’s testing and inspection processes to ensure they meet industry standards.
- Warranty and Support: Consider manufacturers that offer warranties and responsive customer support.
- References and Reviews: Research the manufacturer’s reputation by reading reviews and asking for references from previous clients.
By prioritizing quality and reliability alongside price, you can ensure that you receive PCBs that meet your project’s requirements and perform well in the long run.
6. Not Accounting for Shipping Costs
The Impact of Shipping Costs on Total Price
When getting PCB quotes online, it’s easy to focus solely on the unit price of the PCBs themselves. However, shipping costs can significantly impact the total cost of your project, especially if you require expedited shipping or are ordering from an international manufacturer.
How to Account for Shipping Costs
To account for shipping costs when evaluating PCB quotes, follow these steps:
- Ask manufacturers to provide shipping costs upfront, along with their unit prices.
- Consider the location of the manufacturer and the shipping methods available, as these can impact both cost and lead times.
- If shipping costs are not provided in the quote, follow up with the manufacturer to request this information.
- Factor in shipping costs when comparing quotes to ensure you’re getting the best overall value for your project.
By accounting for shipping costs during the quoting process, you can avoid unexpected expenses and make more informed decisions about which manufacturer to choose.
7. Not Considering Minimum Order Quantities (MOQs)
What are MOQs and Why Do They Matter?
Minimum Order Quantities (MOQs) refer to the minimum number of PCBs a manufacturer requires you to order. MOQs can vary between manufacturers and may impact your project’s budget and timeline. If you require a small number of PCBs, you may find that some manufacturers have MOQs that exceed your needs, forcing you to order more than necessary or look for alternative suppliers.
How to Navigate MOQs
To navigate MOQs when getting PCB quotes online, consider the following:
- When requesting quotes, provide the exact quantity of PCBs you require, even if it’s below the manufacturer’s MOQ.
- If a manufacturer’s MOQ is higher than your needs, ask if they can accommodate a smaller order or if they have any alternative options, such as combining your order with others.
- Consider the long-term needs of your project. If you anticipate needing additional PCBs in the future, ordering a larger quantity upfront may be more cost-effective in the long run.
- If a manufacturer’s MOQ is too high for your needs, look for alternative suppliers who can accommodate smaller orders.
By considering MOQs during the quoting process, you can ensure that you’re able to order the quantity of PCBs you need without exceeding your budget or ending up with excess inventory.
8. Not Asking About Design Support
The Value of Design Support
Depending on your level of expertise and the complexity of your project, you may require design support from your PCB manufacturer. This can include assistance with layout, component selection, or even prototyping. Not all manufacturers offer the same level of design support, so it’s important to inquire about these services when getting quotes.
How to Inquire About Design Support
To inquire about design support when getting PCB quotes online, follow these steps:
- When requesting quotes, ask manufacturers about their design support services and capabilities.
- Provide details about your project’s complexity and any specific areas where you may require assistance.
- If design support is offered, ask about the associated costs and how they will be incorporated into your quote.
- Consider the value of design support in relation to your own expertise and resources. In some cases, paying for design support may be more cost-effective than trying to handle everything in-house.
By asking about design support during the quoting process, you can ensure that you have access to the resources and expertise needed to bring your project to fruition.
9. Not Considering Intellectual Property (IP) Protection
The Importance of IP Protection
When working with a PCB manufacturer, it’s crucial to consider the protection of your intellectual property (IP). This includes your design files, schematics, and any proprietary information related to your project. Not all manufacturers have the same level of IP protection, and failing to address this issue could put your company’s valuable assets at risk.
How to Evaluate IP Protection
To evaluate a manufacturer’s IP protection measures, consider the following:
- Non-Disclosure Agreements (NDAs): Ask if the manufacturer is willing to sign an NDA to protect your sensitive information.
- IP Policies: Inquire about the manufacturer’s internal policies and procedures for protecting client IP.
- Employee Training: Ask about the manufacturer’s employee training programs related to IP protection and confidentiality.
- Physical and Digital Security: Consider the manufacturer’s physical and digital security measures, such as access controls and data encryption.
By prioritizing IP protection when getting PCB quotes online, you can safeguard your company’s valuable assets and maintain a competitive edge in your industry.
10. Not Asking for References or Samples
The Value of References and Samples
When evaluating PCB manufacturers, it’s important to ask for references and samples of their work. References can provide valuable insights into a manufacturer’s reliability, communication, and overall performance. Samples, on the other hand, allow you to assess the quality and workmanship of a manufacturer’s PCBs firsthand.
How to Request References and Samples
To request references and samples when getting PCB quotes online, follow these steps:
- When requesting quotes, ask manufacturers if they can provide references from previous clients with similar projects.
- If references are provided, follow up with them to ask about their experience working with the manufacturer.
- Ask manufacturers if they can provide samples of their work, either from previous projects or a small sample run of your own design.
- If samples are provided, carefully inspect them for quality, consistency, and adherence to your specifications.
By requesting references and samples during the quoting process, you can gain a more comprehensive understanding of a manufacturer’s capabilities and make a more informed decision about which one to choose for your project.
11. Not Establishing Clear Communication Channels
The Importance of Clear Communication
Clear communication is essential when working with a PCB manufacturer, especially if your project is complex or requires ongoing support. Establishing clear communication channels from the outset can help prevent misunderstandings, delays, and other issues that can derail your project.
How to Establish Clear Communication Channels
To establish clear communication channels when getting PCB quotes online, consider the following:
- Point of Contact: Ask manufacturers to provide a dedicated point of contact for your project, such as an account manager or project engineer.
- Communication Methods: Clarify the preferred methods of communication, such as email, phone, or video conferencing, and establish expectations for response times.
- Project Updates: Discuss how often you expect to receive project updates and what information should be included in these updates.
- Escalation Procedures: Establish a clear escalation process for addressing any issues or concerns that may arise during the project.
By establishing clear communication channels from the outset, you can foster a more collaborative and effective working relationship with your chosen PCB manufacturer.
FAQ
1. How can I ensure that I’m getting the best price when getting PCB quotes online?
To ensure you’re getting the best price when getting PCB quotes online, provide detailed specifications to multiple manufacturers, compare quotes carefully, and consider factors such as lead times, shipping costs, and minimum order quantities. Don’t focus solely on price, but also consider quality, reliability, and the overall value provided by each manufacturer.
2. What should I do if a manufacturer’s minimum order quantity (MOQ) is higher than my needs?
If a manufacturer’s MOQ is higher than your needs, you can ask if they can accommodate a smaller order or if they have any alternative options, such as combining your order with others. If the manufacturer is unable to accommodate your needs, look for alternative suppliers who can work with smaller order quantities.
3. How important is design support when choosing a PCB manufacturer?
The importance of design support depends on your level of expertise and the complexity of your project. If you have limited experience with PCB design or if your project is particularly complex, choosing a manufacturer that offers robust design support can be invaluable. However, if you have in-house design capabilities or a simple project, design support may be less critical.
4. What steps can I take to protect my intellectual property when working with a PCB manufacturer?
To protect your intellectual property when working with a PCB manufacturer, consider requesting a non-disclosure agreement (NDA), inquiring about the manufacturer’s IP policies and procedures, and evaluating their physical and digital security measures. By taking these steps, you can safeguard your company’s valuable assets and maintain a competitive edge in your industry.
5. How can I assess the quality and reliability of a PCB manufacturer?
To assess the quality and reliability of a PCB manufacturer, look for relevant certifications (such as ISO 9001, UL, or IPC), inquire about their testing and inspection processes, and consider their warranty and support offerings. Additionally, research the manufacturer’s reputation by reading reviews and asking for references from previous clients. By evaluating these factors, you can gain a more comprehensive understanding of a manufacturer’s capabilities and make an informed decision about which one to choose for your project.
Conclusion
Getting PCB quotes online can be a complex and time-consuming process, but by avoiding these 11 common minefields, you can streamline the process and ensure that you get the best possible price and quality for your project. Remember to provide detailed specifications, check manufacturer capabilities, consider lead times and shipping costs, and prioritize quality and reliability alongside price. Additionally, don’t forget to inquire about design support, IP protection, and clear communication channels to foster a successful working relationship with your chosen manufacturer. By following these guidelines and doing your due diligence, you can navigate the world of online PCB quotes with confidence and bring your project to life.
0 Comments