What is a PCB antipad?
A PCB antipad, also known as a thermal relief pad or thermal spoke, is a design technique used in printed circuit boards (PCBs) to improve solderability and reduce thermal stress on plated through-holes (PTHs). An antipad is essentially a clearance area around a PTH where the copper plane or pour is removed, leaving only thin traces or “spokes” connecting the PTH to the surrounding copper.
The primary purpose of an antipad is to limit the amount of heat transferred from the PTH to the surrounding copper during the soldering process. Without an antipad, the large copper area around the PTH would act as a heat sink, drawing heat away from the PTH and making it difficult for the solder to melt and form a proper joint. By reducing the copper area connected to the PTH, the antipad allows the hole to reach the required temperature for soldering more easily.
Advantages of Using PCB Antipads
- Improved solderability: Antipads help PTHs reach the necessary temperature for proper soldering, resulting in better solder joint formation and reliability.
- Reduced thermal stress: By limiting the heat transfer from the PTH to the surrounding copper, antipads minimize the thermal stress on the PCB and components during soldering.
- Enhanced manufacturing yield: The use of antipads can lead to fewer soldering defects and improved overall manufacturing yield.
- Better solder joint inspection: Antipads make it easier to visually inspect solder joints, as the clearance area around the PTH allows for a clearer view of the solder fillet.
Disadvantages of Using PCB Antipads
- Reduced thermal conductivity: While antipads improve solderability, they also reduce the thermal conductivity between the PTH and the surrounding copper. This can be a concern for components that generate significant heat and rely on the copper plane for heat dissipation.
- Increased impedance: The reduced copper area around the PTH can lead to higher impedance, which may impact high-frequency signal integrity.
- Potential for signal integrity issues: In some cases, the thin traces connecting the PTH to the surrounding copper can act as antennas, leading to unwanted signal radiation or coupling.
Designing PCB Antipads
When designing PCB antipads, there are several factors to consider, including the antipad shape, size, and the number of spokes connecting the PTH to the surrounding copper.
Antipad Shape
Antipads can be designed in various shapes, with the most common being circular and square. The choice of shape depends on the specific requirements of the design and the manufacturing capabilities of the PCB fabricator.
Shape | Advantages | Disadvantages |
---|---|---|
Circular | – Easier to manufacture – More common in PCB design software |
– May not provide optimal thermal relief in all directions |
Square | – Provides equal thermal relief in all directions | – More difficult to manufacture – Less common in PCB design software |
Antipad Size
The size of the antipad is another important consideration. A larger antipad provides better thermal relief but also reduces the copper area available for heat dissipation and can impact signal integrity. On the other hand, a smaller antipad may not provide sufficient thermal relief, leading to soldering difficulties.
As a general rule, the antipad diameter should be at least 1.5 times the diameter of the PTH. However, the optimal size may vary depending on the specific design requirements and the PCB Fabrication process.
Antipad Size | Advantages | Disadvantages |
---|---|---|
Larger | – Provides better thermal relief – Improves solderability |
– Reduces copper area for heat dissipation – May impact signal integrity |
Smaller | – Maintains more copper area for heat dissipation – Less impact on signal integrity |
– May not provide sufficient thermal relief – Can lead to soldering difficulties |
Number of Spokes
The number of spokes connecting the PTH to the surrounding copper is another design consideration. More spokes provide a better electrical and thermal connection between the PTH and the copper plane but can also make the PCB more difficult to manufacture. Fewer spokes, on the other hand, may not provide a sufficient connection, leading to signal integrity or thermal management issues.
A common approach is to use four spokes, arranged in a cross pattern around the PTH. This provides a good balance between electrical and thermal connection and manufacturability. However, the optimal number of spokes may vary depending on the specific design requirements and the PCB fabrication process.
Number of Spokes | Advantages | Disadvantages |
---|---|---|
More | – Provides better electrical and thermal connection – Improves signal integrity |
– Can make the PCB more difficult to manufacture – May not be necessary for all designs |
Fewer | – Easier to manufacture – Sufficient for many designs |
– May not provide a sufficient connection – Can lead to signal integrity or thermal management issues |
When to Use PCB Antipads
PCB antipads are typically used in the following situations:
- PTHs for through-hole components: Antipads are commonly used for PTHs that accommodate through-hole components, such as connectors, switches, and some types of capacitors and resistors.
- Vias in thermal relief pads: Antipads can be used for vias located within thermal relief pads, which are larger copper areas designed to dissipate heat from surface-mounted components.
- High-current PTHs: Antipads can be beneficial for PTHs carrying high currents, as they help reduce thermal stress and improve solderability.
- Multi-layer PCBs: In multi-layer PCBs, antipads can be used to provide thermal relief for PTHs that pass through multiple copper layers.
However, antipads may not be necessary or desirable in all situations. For example:
- PTHs for non-critical components: Antipads may not be needed for PTHs accommodating non-critical components or those that do not generate significant heat.
- Low-current PTHs: Antipads may not provide significant benefits for PTHs carrying low currents, as the thermal stress and solderability challenges are less pronounced.
- High-frequency designs: In some high-frequency designs, the use of antipads may lead to signal integrity issues due to the reduced copper area and potential for unwanted radiation or coupling.
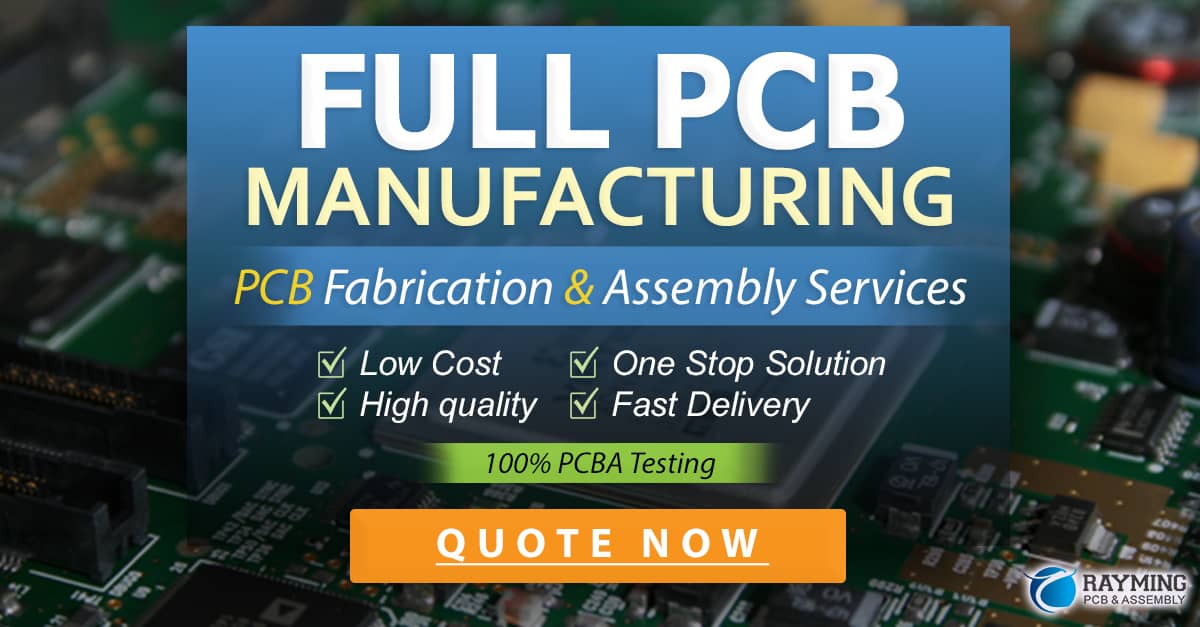
PCB Antipad Design Guidelines
When incorporating antipads into your PCB design, consider the following guidelines:
- Consult with your PCB fabricator: Discuss your antipad requirements with your PCB fabricator to ensure that they can accommodate your design and provide guidance on the optimal antipad shape, size, and spoke configuration for your specific application.
- Balance thermal relief and signal integrity: Strike a balance between providing adequate thermal relief and maintaining signal integrity. This may involve adjusting the antipad size, shape, and spoke configuration to optimize performance.
- Consider the impact on thermal management: While antipads improve solderability, they can also reduce the thermal conductivity between the PTH and the surrounding copper. Ensure that your design accounts for this and provides sufficient thermal management for components that generate significant heat.
- Evaluate the need for antipads on a case-by-case basis: Not all PTHs require antipads. Evaluate the need for antipads based on the specific requirements of your design, including the types of components, current levels, and thermal management needs.
- Use appropriate antipad settings in your PCB design software: Most PCB design software packages offer settings for configuring antipads. Ensure that you use appropriate settings based on your design requirements and the guidelines provided by your PCB fabricator.
Frequently Asked Questions (FAQ)
- What is the difference between an antipad and a thermal relief pad?
-
An antipad and a thermal relief pad are essentially the same things. Both terms refer to the clearance area around a PTH where the copper plane or pour is removed, leaving only thin traces or “spokes” connecting the PTH to the surrounding copper. The purpose of both is to improve solderability and reduce thermal stress during the soldering process.
-
Can antipads be used for surface-mounted components?
-
Antipads are primarily used for PTHs, which are typically associated with through-hole components. However, antipads can be used for vias located within thermal relief pads, which are larger copper areas designed to dissipate heat from surface-mounted components.
-
How do I determine the appropriate antipad size for my design?
-
As a general rule, the antipad diameter should be at least 1.5 times the diameter of the PTH. However, the optimal size may vary depending on the specific design requirements and the PCB fabrication process. It is best to consult with your PCB fabricator to determine the appropriate antipad size for your design.
-
Can antipads cause signal integrity issues in high-frequency designs?
-
In some high-frequency designs, the use of antipads may lead to signal integrity issues due to the reduced copper area and potential for unwanted radiation or coupling. It is important to carefully evaluate the need for antipads in high-frequency designs and consider alternative techniques for improving solderability and thermal management if necessary.
-
Are there any industry standards or guidelines for designing PCB antipads?
- While there are no universally accepted industry standards for designing PCB antipads, many PCB Fabricators and design software packages provide guidelines and recommendations based on best practices and experience. It is important to consult with your PCB fabricator and refer to the guidelines provided by your PCB design software to ensure that your antipad design is appropriate for your specific application.
In conclusion, PCB antipads are a valuable design technique for improving solderability and reducing thermal stress in PTHs. By carefully considering the antipad shape, size, and spoke configuration, and balancing thermal relief with signal integrity and thermal management requirements, designers can create more reliable and manufacturable PCBs. However, it is important to evaluate the need for antipads on a case-by-case basis and consult with PCB fabricators to ensure optimal results.
0 Comments