What are Vias?
Vias are small holes drilled through a PCB to electrically connect different layers of the board. They allow signals and power to be routed between layers, enabling more complex and compact designs. There are several types of vias:
- Through-hole vias: These vias go through the entire thickness of the board.
- Blind vias: These vias start from an outer layer and end at an inner layer, without going through the entire board.
- Buried vias: These vias connect inner layers without reaching the outer layers of the board.
What is Via Plugging?
Via plugging is the process of filling the vias with a non-conductive material, such as epoxy or resin, to seal them and create a smooth surface on the PCB. This process is typically done after the vias have been plated with a conductive material, such as copper, to ensure electrical connectivity.
Advantages of Via Plugging
-
Improved Reliability: Plugged vias can enhance the reliability of a PCB by preventing contamination and moisture from entering the vias, which can cause short circuits or corrosion.
-
Better Mechanical Strength: Plugging vias can increase the mechanical strength of a PCB, particularly in areas subject to high stress or vibration. The filled vias act as reinforcements, reducing the risk of cracks or delamination.
-
Enhanced Thermal Management: In high-power applications, plugged vias can help dissipate heat more efficiently by providing a continuous thermal path between layers.
-
Reduced EMI: Plugged vias can minimize electromagnetic interference (EMI) by preventing the escape of high-frequency signals through the vias, which can act as antennas.
-
Improved Manufacturability: Plugging vias can simplify the manufacturing process by creating a smooth surface for subsequent operations, such as solder mask application or component placement.
Disadvantages of Via Plugging
-
Increased Cost: Via plugging adds an extra step to the PCB manufacturing process, which can increase production costs and lead times.
-
Potential for Defects: If not done properly, via plugging can introduce defects, such as voids or inconsistent fill, which can negatively impact the reliability and performance of the PCB.
-
Limited Repairability: Plugged vias can make repairs or modifications to the PCB more challenging, as the plugging material must be removed before any rework can be done.
-
Design Constraints: The presence of plugged vias may impose design constraints, such as minimum via sizes or spacing requirements, which can affect the overall layout and routing of the PCB.
Factors to Consider When Deciding to Plug Vias
-
Application Requirements: The decision to plug vias should be based on the specific requirements of the application, such as reliability, thermal management, or EMI suppression.
-
PCB Thickness: Thicker PCBs may benefit more from via plugging, as they are more susceptible to mechanical stress and thermal issues.
-
Layer Count: Multi-layer PCBs with a high number of layers may require via plugging to ensure reliable connections between layers and prevent signal integrity issues.
-
Manufacturing Capabilities: The availability and cost of via plugging services at your chosen PCB manufacturer should be considered when deciding whether to plug vias.
-
Budget and Timeline: Via plugging can add cost and time to the PCB manufacturing process, so it’s essential to weigh these factors against the potential benefits for your specific application.
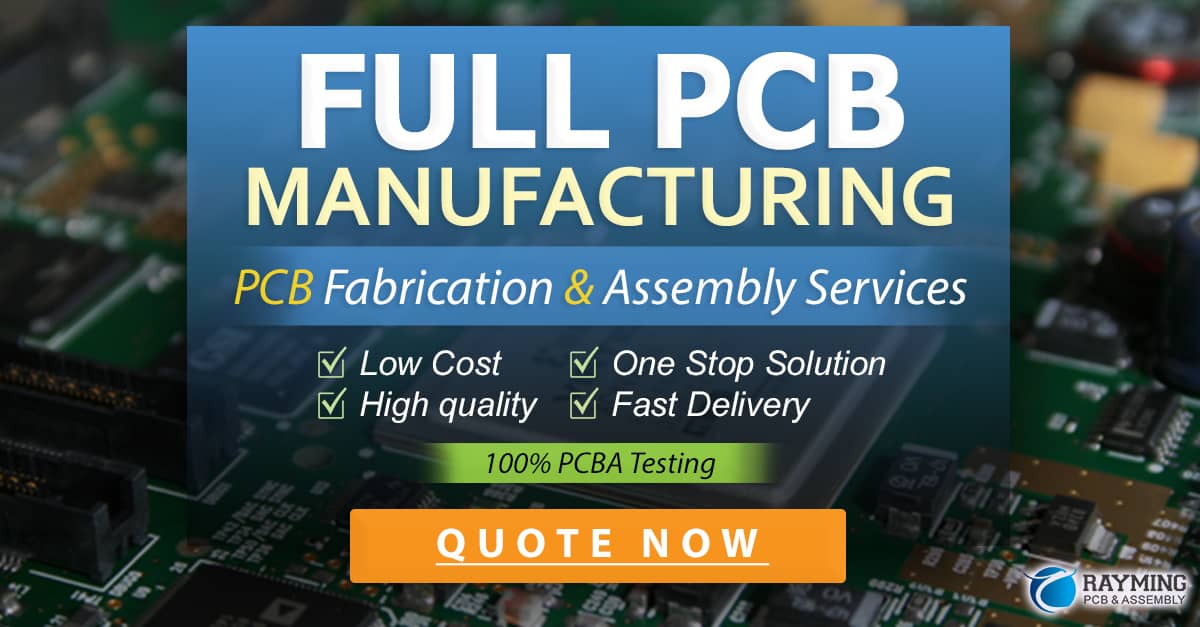
Via Plugging Techniques
There are several techniques used for via plugging, each with its own advantages and limitations:
Technique | Description | Advantages | Limitations |
---|---|---|---|
Epoxy Plugging | Vias are filled with a non-conductive epoxy resin. | – Cost-effective – Easy to apply – Good mechanical strength |
– Limited thermal conductivity – Potential for voids or inconsistent fill |
Conductive Epoxy Plugging | Vias are filled with a conductive epoxy resin. | – Improved thermal conductivity – Enhanced electrical connectivity |
– Higher cost than non-conductive epoxy – Potential for short circuits if not applied properly |
Copper Plugging | Vias are filled with copper through an electroplating process. | – Excellent thermal conductivity – Superior mechanical strength – Seamless integration with copper layers |
– Higher cost than epoxy plugging – Requires specialized equipment and processes |
Soldermask Plugging | Vias are filled with soldermask material during the soldermask application process. | – Cost-effective – Seamless integration with soldermask layer |
– Limited mechanical strength – Not suitable for high-reliability applications |
The choice of via plugging technique depends on the specific requirements of the application, such as thermal management, electrical performance, and cost constraints.
Via Plugging in High-Speed PCB Design
In high-speed PCB design, via plugging can play a crucial role in maintaining signal integrity and minimizing EMI. High-frequency signals can easily escape through unplugge vias, causing crosstalk, resonance, and other signal integrity issues.
Plugging vias in high-speed designs can help:
-
Reduce Stub Resonance: Unplugged vias can act as stubs, causing resonance and reflections that degrade signal quality. Plugging vias minimizes these effects by eliminating the stubs.
-
Minimize Crosstalk: Plugged vias can reduce crosstalk between adjacent signal traces by preventing the coupling of high-frequency signals through the vias.
-
Improve Impedance Control: Plugging vias can help maintain consistent impedance along signal traces by eliminating the impedance discontinuities caused by unplugged vias.
However, it’s essential to consider the potential impact of via plugging on the overall signal integrity and design complexity. In some cases, alternative techniques, such as back-drilling or optimized via placement, may be more suitable for high-speed designs.
Frequently Asked Questions (FAQ)
-
Q: Is via plugging always necessary?
A: No, via plugging is not always necessary. The decision to plug vias depends on the specific requirements of the application, such as reliability, thermal management, or EMI suppression. -
Q: Can via plugging improve the thermal management of a PCB?
A: Yes, plugging vias with a thermally conductive material, such as conductive epoxy or copper, can help dissipate heat more efficiently by providing a continuous thermal path between layers. -
Q: Does via plugging increase the cost of PCB manufacturing?
A: Yes, via plugging adds an extra step to the PCB manufacturing process, which can increase production costs and lead times. The cost increase depends on the chosen plugging technique and the number of vias to be plugged. -
Q: Can plugged vias be removed for rework or repairs?
A: Yes, plugged vias can be removed for rework or repairs, but the process can be challenging and time-consuming. The plugging material must be carefully removed without damaging the surrounding copper layers or components. -
Q: Are there any design constraints to consider when using plugged vias?
A: Yes, the presence of plugged vias may impose design constraints, such as minimum via sizes or spacing requirements, which can affect the overall layout and routing of the PCB. It’s essential to consult with your PCB manufacturer to ensure your design is compatible with their via plugging capabilities.
Conclusion
Via plugging is a technique used in PCB manufacturing to fill vias with a non-conductive or conductive material, offering several advantages, such as improved reliability, mechanical strength, thermal management, and reduced EMI. However, it also comes with disadvantages, such as increased cost, potential for defects, limited repairability, and design constraints.
The decision to plug vias should be based on a careful consideration of the specific requirements of the application, the PCB thickness and layer count, manufacturing capabilities, budget, and timeline. In high-speed PCB design, via plugging can be particularly beneficial for maintaining signal integrity and minimizing EMI, but alternative techniques may be more suitable in some cases.
Ultimately, the choice to plug vias or not depends on a balance between the potential benefits and the associated costs and constraints. By understanding the advantages, disadvantages, and factors to consider, engineers and designers can make informed decisions about via plugging in their PCB designs.
0 Comments