What is Electronics Manufacturing?
Electronics manufacturing is the process of designing, developing, testing, and producing electronic components, devices, and equipment. It encompasses a wide range of products, from simple components like resistors and capacitors to complex systems such as computers, smartphones, and industrial control equipment.
The electronics manufacturing industry has grown significantly over the past few decades, driven by advances in technology, increasing demand for electronic products, and the globalization of supply chains. Today, electronics manufacturing is a multi-trillion dollar industry that plays a crucial role in the global economy.
Key Aspects of Electronics Manufacturing
-
Design and Development: The first step in electronics manufacturing is the design and development of the product. This involves creating schematics, selecting components, and designing the layout of the printed circuit board (PCB).
-
Component Procurement: Once the design is finalized, the next step is to procure the necessary components. This involves sourcing components from suppliers, negotiating prices, and ensuring that the components meet the required specifications.
-
PCB Fabrication: The PCB is the backbone of any electronic device. PCB fabrication involves creating the board, drilling holes, and applying the necessary coatings and finishes.
-
Component Assembly: After the PCB is fabricated, the next step is to assemble the components onto the board. This can be done manually or using automated equipment, depending on the complexity of the product and the volume of production.
-
Testing and Quality Control: Once the product is assembled, it must undergo rigorous testing to ensure that it meets the required specifications and functions as intended. This involves various types of testing, such as functional testing, environmental testing, and reliability testing.
-
Packaging and Shipping: After the product has passed all the necessary tests, it is packaged and shipped to the customer. Packaging must be designed to protect the product during transportation and storage.
The Evolution of Electronics Manufacturing
Electronics manufacturing has come a long way since the invention of the first electronic devices in the early 20th century. The industry has undergone significant changes over the years, driven by advances in technology and changes in consumer demand.
The Early Days of Electronics Manufacturing
In the early days of electronics manufacturing, most products were simple devices like radios and televisions. These products were manufactured using manual assembly techniques, with workers soldering components onto PCBs by hand.
As electronic devices became more complex in the 1960s and 1970s, manufacturers began to adopt automated assembly techniques. This involved using machines to place components onto PCBs, which increased the speed and accuracy of the assembly process.
The Rise of Contract Manufacturing
In the 1980s and 1990s, the electronics manufacturing industry underwent a significant shift with the rise of contract manufacturing. Companies began to outsource the production of their electronic products to specialized manufacturers, known as Electronic Manufacturing services (EMS) providers.
EMS providers offered a range of services, from design and development to component procurement, PCB fabrication, and final assembly. By outsourcing production to EMS providers, companies could reduce costs, improve efficiency, and focus on their core competencies.
The Impact of Globalization
The rise of contract manufacturing coincided with the globalization of the electronics industry. As trade barriers fell and transportation costs decreased, companies began to shift production to low-cost countries in Asia, particularly China.
China quickly became the world’s largest producer of electronic products, thanks to its low labor costs, well-developed supply chain, and favorable government policies. Today, China accounts for over half of global electronics production.
However, rising labor costs and increasing trade tensions have led some companies to diversify their supply chains and shift production to other countries, such as Vietnam, India, and Mexico.
Key Technologies in Electronics Manufacturing
Electronics manufacturing relies on a range of advanced technologies to design, develop, and produce electronic products. Here are some of the key technologies used in electronics manufacturing:
Computer-Aided Design (CAD) Software
CAD software is used to design electronic products, from simple components to complex systems. CAD tools allow engineers to create detailed 3D models of products, simulate their performance, and optimize their design for manufacturing.
Some of the most popular CAD tools used in electronics manufacturing include Autodesk Eagle, Altium Designer, and KiCad.
3D Printing
3D printing is increasingly being used in electronics manufacturing to create prototypes, tooling, and even final products. 3D printing allows manufacturers to quickly and cheaply create complex geometries that would be difficult or impossible to produce using traditional manufacturing methods.
Some of the most popular 3D printing technologies used in electronics manufacturing include fused deposition modeling (FDM), stereolithography (SLA), and selective laser sintering (SLS).
Surface-Mount Technology (SMT)
SMT is a method of assembling electronic components onto PCBs using automated equipment. SMT allows for the placement of smaller components at higher densities than traditional through-hole assembly techniques.
SMT equipment includes pick-and-place machines, reflow ovens, and inspection systems. These machines are highly automated and can place thousands of components per hour with high accuracy and repeatability.
Automated Optical Inspection (AOI)
AOI is a technology used to inspect PCBs and other electronic components for defects and quality issues. AOI systems use high-resolution cameras and advanced image processing algorithms to detect issues such as missing components, solder defects, and incorrect component placement.
AOI systems can inspect PCBs at high speeds and with high accuracy, reducing the need for manual inspection and improving quality control.
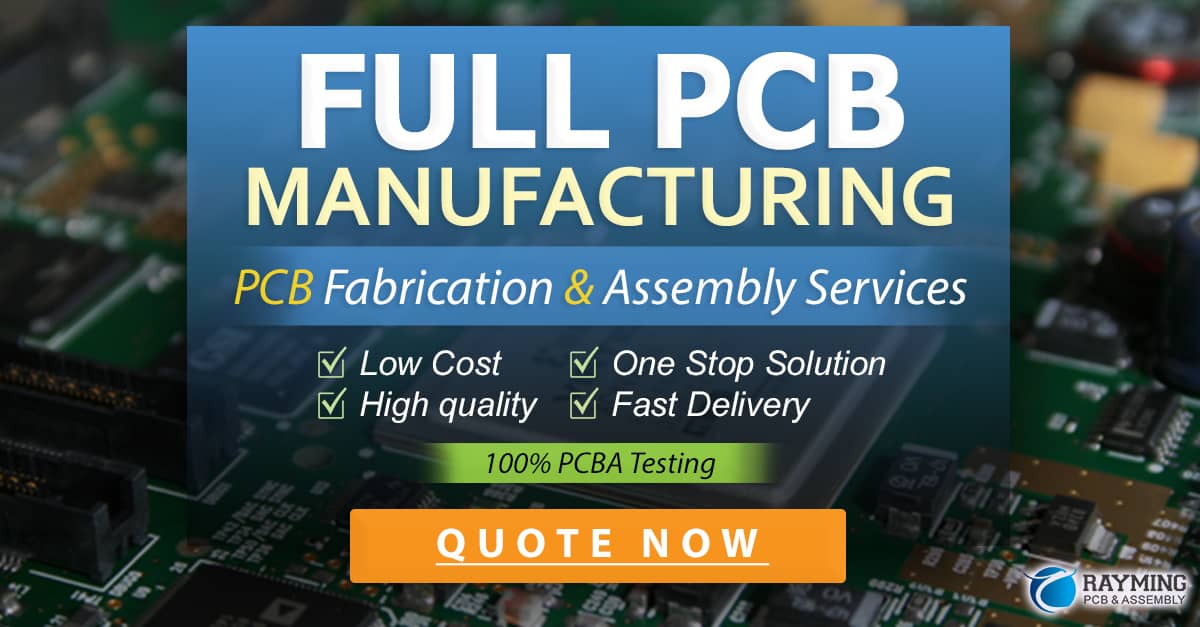
Challenges and Opportunities in Electronics Manufacturing
Despite its growth and success, the electronics manufacturing industry faces a number of challenges and opportunities. Here are some of the key challenges and opportunities facing the industry today:
Supply Chain Disruptions
The COVID-19 pandemic has highlighted the vulnerability of global supply chains to disruptions. Electronics manufacturers have faced challenges in sourcing components and materials, as well as disruptions to transportation and logistics.
To mitigate these risks, many manufacturers are looking to diversify their supply chains and build more resilient networks. This may involve sourcing components from multiple suppliers, building inventory buffers, and investing in digital tools to improve supply chain visibility and agility.
Sustainability and Environmental Responsibility
Electronics manufacturing has a significant environmental impact, from the extraction of raw materials to the disposal of electronic waste. Consumers and regulators are increasingly demanding that manufacturers take steps to reduce their environmental footprint and promote sustainability.
This has led to a growing focus on eco-design, which involves designing products with sustainability in mind from the outset. Manufacturers are also investing in recycling and takeback programs to reduce electronic waste and promote a circular economy.
Skilled Labor Shortages
The electronics manufacturing industry relies on a skilled workforce, from engineers and technicians to assembly line workers. However, many manufacturers are facing shortages of skilled labor, particularly in advanced manufacturing roles.
To address this challenge, manufacturers are investing in training and development programs to upskill their existing workforce and attract new talent to the industry. Some are also partnering with educational institutions to develop curricula and programs that align with industry needs.
Cybersecurity Risks
As electronic devices become more connected and networked, they are increasingly vulnerable to cyber threats. Manufacturers must ensure that their products are secure and can withstand attacks from hackers and other malicious actors.
This requires a focus on security-by-design, which involves building security into products from the ground up. Manufacturers must also ensure that their own systems and networks are secure, and that they have robust incident response plans in place in case of a breach.
Frequently Asked Questions (FAQ)
- What is the difference between through-hole and surface-mount assembly?
Through-hole assembly involves inserting component leads through holes drilled in the PCB and soldering them in place. Surface-mount assembly involves placing components directly onto the surface of the PCB and soldering them in place. Surface-mount assembly allows for smaller components and higher component densities than through-hole assembly.
- What is the role of testing in electronics manufacturing?
Testing is a critical part of electronics manufacturing, as it ensures that products meet the required specifications and function as intended. Testing can involve a range of methods, from visual inspection to automated testing using specialized equipment. Testing helps to identify defects and quality issues early in the manufacturing process, reducing the risk of product failures and recalls.
- What is the future of electronics manufacturing?
The future of electronics manufacturing is likely to be shaped by a number of trends, including the increasing demand for connected and smart devices, the growing focus on sustainability and eco-design, and the adoption of advanced technologies such as 3D printing and robotics. Manufacturers will need to be agile and adaptable to stay competitive in a rapidly changing industry.
- What are some of the key skills needed for a career in electronics manufacturing?
A career in electronics manufacturing requires a range of skills, including technical knowledge of electronic components and systems, experience with CAD software and other design tools, and familiarity with manufacturing processes and quality control methods. Soft skills such as communication, problem-solving, and teamwork are also important for success in the industry.
- How has the COVID-19 pandemic impacted the electronics manufacturing industry?
The COVID-19 pandemic has had a significant impact on the electronics manufacturing industry, disrupting supply chains, reducing demand for certain products, and forcing manufacturers to adapt to new ways of working. However, the pandemic has also accelerated certain trends, such as the adoption of digital technologies and the shift towards remote work. Manufacturers that are able to adapt and innovate in response to these challenges will be well-positioned for success in the post-pandemic world.
Conclusion
Electronics manufacturing is a complex and constantly evolving industry that plays a crucial role in the global economy. From simple components to complex systems, electronic products are essential to modern life, and the demand for these products is only expected to grow in the coming years.
To stay competitive in this dynamic industry, manufacturers must be willing to embrace new technologies, adapt to changing market conditions, and prioritize sustainability and social responsibility. By investing in their people, processes, and products, electronics manufacturers can build a strong foundation for long-term success and contribute to a more sustainable and connected world.
0 Comments