What is PCB Panelization?
PCB panelization is the process of grouping multiple identical PCBs onto a single panel for fabrication. This process allows for the production of multiple PCBs in a single run, reducing manufacturing time and costs. The individual PCBs are separated from the panel after the fabrication process is complete, usually through a process called depaneling.
Benefits of PCB Panelization
There are several benefits to PCB panelization, including:
- Cost Reduction: By producing multiple PCBs on a single panel, the overall manufacturing cost per PCB is reduced.
- Increased Efficiency: Panelization allows for the simultaneous production of multiple PCBs, reducing the time required for fabrication.
- Improved Handling: Panels are easier to handle during the manufacturing process compared to individual PCBs, reducing the risk of damage.
- Consistent Quality: Panelization ensures that all PCBs on a panel are produced under the same conditions, resulting in consistent quality across the batch.
Types of PCB Panelization
There are two main types of PCB panelization: tab routing and v-scoring.
Tab Routing
Tab routing involves creating tabs that connect the individual PCBs to the panel frame. These tabs are cut away during the depaneling process to separate the individual boards. Tab routing is suitable for PCBs with simple shapes and less stringent requirements for edge quality.
V-Scoring
V-scoring involves creating V-shaped grooves along the edges of the individual PCBs. These grooves allow for easy separation of the boards from the panel, resulting in cleaner edges compared to tab routing. V-scoring is preferred for PCBs with complex shapes or those requiring better edge quality.
PCB Panelization Design Considerations
When designing a PCB panel, several factors must be considered to ensure optimal results:
-
Panel Size: The panel size should be chosen based on the dimensions of the individual PCBs and the manufacturing capabilities of the fabrication facility.
-
PCB orientation: The orientation of the individual PCBs on the panel should be optimized to maximize the number of boards per panel while minimizing waste.
-
Spacing: Adequate spacing between individual PCBs is necessary to ensure proper separation during depaneling and to avoid damage to the boards.
-
Fiducial Marks: Fiducial marks are used for alignment during the fabrication and assembly processes. They should be placed on the panel in accordance with the manufacturer’s guidelines.
-
Tooling Holes: Tooling holes are used to secure the panel during fabrication and assembly. Their placement and size should be determined based on the manufacturing equipment and processes.
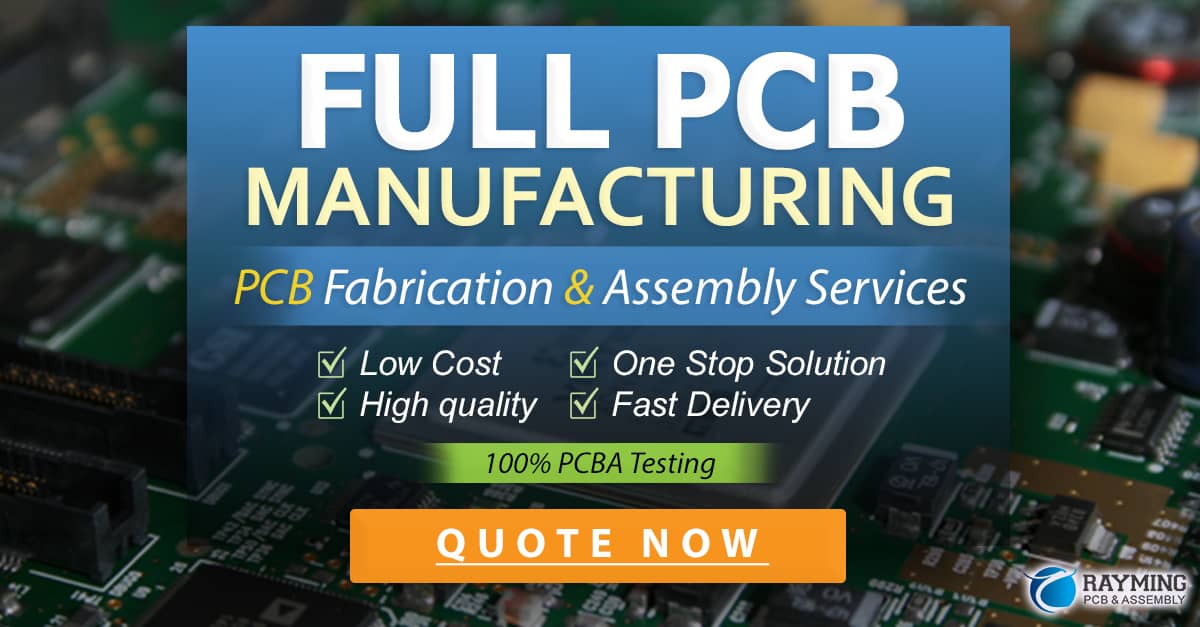
Screaming Circuits’ PCB Panelization Services
At Screaming Circuits, we offer comprehensive PCB panelization services to meet the unique needs of our customers. Our experienced team works closely with clients to develop panelization strategies that optimize manufacturing efficiency and product quality.
Panelization Design Assistance
Our PCB design experts can assist in creating panel layouts that maximize the number of boards per panel while ensuring proper spacing and alignment. We use advanced software tools to optimize panel designs and minimize waste.
Flexible Manufacturing Options
We offer both tab routing and v-scoring panelization options to accommodate a wide range of PCB designs and requirements. Our state-of-the-art manufacturing equipment ensures precise and consistent results.
Quick-Turn Prototyping
In addition to production-scale panelization, we also offer quick-turn Prototyping Services for PCB panels. This allows our customers to test and validate their panel designs before committing to full-scale production.
Quality Assurance
All of our PCB panels undergo rigorous quality inspections to ensure they meet the highest standards. We use automated optical inspection (AOI) and electrical testing to verify the integrity of each panel before shipping.
Frequently Asked Questions (FAQ)
-
What is the minimum number of PCBs required for panelization?
The minimum number of PCBs required for panelization varies depending on the size of the individual boards and the panel dimensions. Generally, panelization becomes cost-effective when producing 50 or more identical PCBs. -
Can different PCB designs be panelized together?
In most cases, it is not recommended to panelize different PCB designs together, as this can lead to issues with manufacturing and assembly. It is best to panelize identical PCBs to ensure consistent results. -
How does panelization affect the cost of PCB manufacturing?
Panelization can significantly reduce the cost of PCB manufacturing by allowing for the production of multiple boards in a single run. This reduces the time and resources required for fabrication, resulting in lower costs per PCB. -
What is the typical turnaround time for PCB panelization at Screaming Circuits?
The turnaround time for PCB panelization at Screaming Circuits depends on the complexity of the design and the manufacturing requirements. For quick-turn prototyping, we can typically deliver panels within 5-7 business days. Production-scale panelization turnaround times are determined on a case-by-case basis. -
Can Screaming Circuits handle the depaneling process?
Yes, Screaming Circuits offers depaneling services to separate the individual PCBs from the panel after fabrication. We use advanced equipment to ensure clean and precise separation, minimizing the risk of damage to the boards.
Conclusion
PCB panelization is a critical process in the manufacturing of printed circuit boards, offering numerous benefits including cost reduction, increased efficiency, and improved product quality. At Screaming Circuits, we have the expertise and capabilities to provide comprehensive PCB panelization services tailored to the unique needs of our customers.
By working with our experienced team, you can optimize your PCB panel designs, streamline your manufacturing process, and ensure the highest quality end products. Contact Screaming Circuits today to learn more about our PCB panelization services and how we can support your next project.
0 Comments