Understanding Functional Testing in PCB Assembly
Functional testing is a crucial step in the PCB-Assembly-process-techniques-and-best-practices/”>PCB assembly process that ensures the proper operation of the assembled printed circuit board. This type of testing verifies that the PCB performs according to its intended design and meets the specified requirements. Functional testing is typically performed after the PCB has undergone other tests, such as visual inspection and in-circuit testing (ICT).
The Importance of Functional Testing
Functional testing is essential for several reasons:
-
Verifying the PCB’s functionality: It ensures that the assembLED PCB functions as intended, meeting all the design specifications and requirements.
-
Identifying defects: Functional testing helps detect any defects or issues that may have been missed during previous testing stages.
-
Ensuring product quality: By performing functional testing, manufacturers can guarantee that the PCBs delivered to customers are of high quality and will perform reliably in their intended applications.
-
Reducing costs: Identifying and fixing defects early in the production process through functional testing can save significant costs associated with product recalls or field failures.
Types of Functional Testing
There are several types of functional testing that can be performed on PCBs, depending on the specific requirements and applications. Some common types include:
-
Power-on testing: This test verifies that the PCB powers on correctly and that all the components receive the proper voltage levels.
-
Boundary scan testing: This test uses JTAG (Joint Test Action Group) technology to test the connectivity and functionality of the components on the PCB.
-
Functional test fixtures: Custom-designed test fixtures are used to simulate the PCB’s intended operating environment and test its functionality under various conditions.
-
Burn-in testing: This test involves subjecting the PCB to elevated temperatures and voltages for an extended period to identify any early failures or weaknesses.
The Functional Testing Process
The functional testing process typically involves the following steps:
1. Test Planning and Development
The first step in functional testing is to develop a comprehensive test plan based on the PCB’s design specifications and requirements. This plan should outline the specific tests to be performed, the test conditions, and the expected results. Test engineers work closely with the design team to create test cases that cover all the essential functions of the PCB.
2. Test Fixture Design and Fabrication
Once the test plan is finalized, the next step is to design and fabricate the test fixtures. These fixtures are custom-designed to interface with the PCB and provide the necessary electrical connections and mechanical support during testing. The test fixtures should be designed to simulate the PCB’s intended operating environment as closely as possible.
3. Test Execution
With the test plan and fixtures in place, the actual testing can begin. The PCB is connected to the test fixture, and the various test cases are executed according to the plan. The test results are recorded and compared against the expected outcomes to identify any discrepancies or issues.
4. Debugging and Failure Analysis
If any failures or issues are identified during testing, the next step is to perform debugging and failure analysis. This involves investigating the root cause of the failure and determining the appropriate corrective action. The debugging process may involve using various tools and techniques, such as oscilloscopes, logic analyzers, and thermal imaging cameras.
5. Retesting and Validation
After the necessary corrections have been made, the PCB undergoes retesting to ensure that the issues have been resolved and that the board now meets all the functional requirements. This process may be repeated until the PCB passes all the test cases successfully.
Test Equipment and Tools
Functional testing requires specialized equipment and tools to perform the various tests efficiently and accurately. Some common test equipment and tools used in functional testing include:
-
Oscilloscopes: Used to measure and analyze electrical signals on the PCB.
-
Logic analyzers: Used to capture and display digital signals and bus transactions.
-
Multimeters: Used to measure voltage, current, and resistance on the PCB.
-
Power supplies: Used to provide the necessary power to the PCB during testing.
-
Function generators: Used to generate various test signals and waveforms.
-
Thermal imaging cameras: Used to identify hot spots or thermal issues on the PCB.
-
Boundary scan tools: Used to perform boundary scan testing using JTAG technology.
Test Equipment | Purpose |
---|---|
Oscilloscope | Measure and analyze electrical signals |
Logic Analyzer | Capture and display digital signals and bus transactions |
Multimeter | Measure voltage, current, and resistance |
Power Supply | Provide necessary power to the PCB |
Function Generator | Generate various test signals and waveforms |
Thermal Imaging Camera | Identify hot spots or thermal issues |
Boundary Scan Tools | Perform boundary scan testing using JTAG technology |
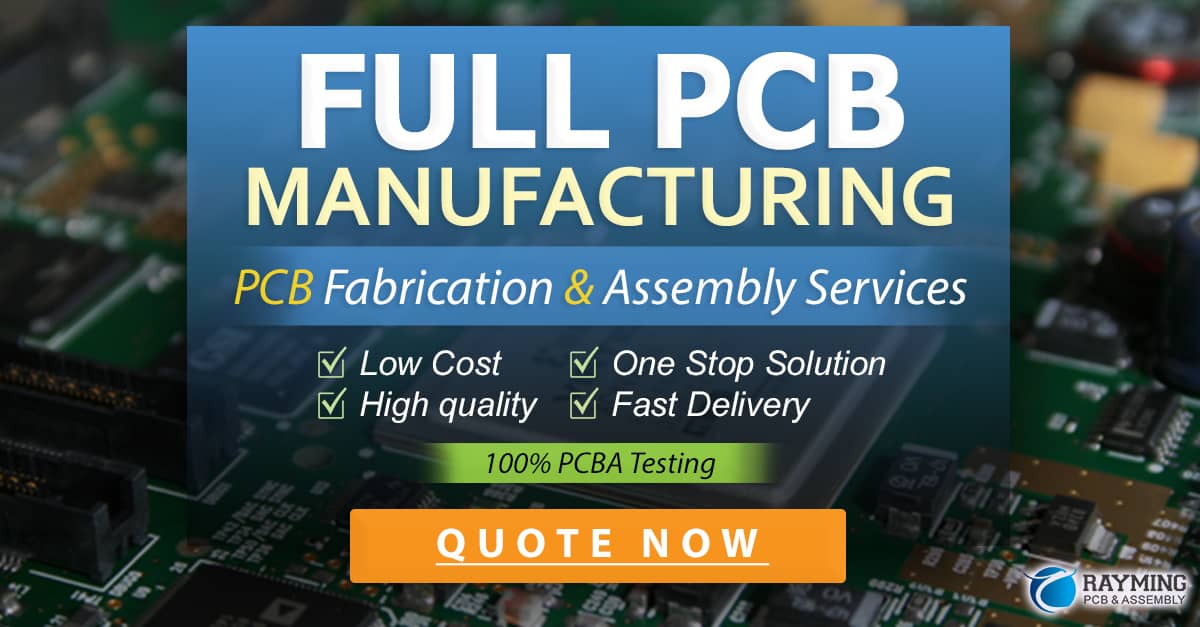
Benefits of Automated Functional Testing
While functional testing can be performed manually, many manufacturers opt for automated functional testing to improve efficiency and accuracy. Automated functional testing offers several benefits, including:
-
Increased test coverage: Automated testing allows for more comprehensive test coverage, as it can execute a large number of test cases in a short amount of time.
-
Improved accuracy: Automated testing eliminates human error and ensures consistent and reliable test results.
-
Faster testing: Automated testing can be performed much faster than manual testing, reducing the overall testing time and increasing productivity.
-
Cost savings: By reducing testing time and improving accuracy, automated functional testing can lead to significant cost savings in the long run.
Challenges in Functional Testing
Despite its importance, functional testing can present several challenges, such as:
-
Complexity: As PCBs become more complex and feature-rich, creating comprehensive test plans and fixtures can be challenging and time-consuming.
-
Compatibility issues: Ensuring compatibility between the test equipment and the PCB can be difficult, especially when dealing with high-speed or high-frequency designs.
-
Debugging difficulties: Identifying the root cause of failures during functional testing can be challenging, particularly when dealing with intermittent or non-reproducible issues.
-
Cost considerations: Implementing a robust functional testing process can be expensive, requiring significant investments in test equipment, fixtures, and skilled personnel.
Best Practices for Effective Functional Testing
To ensure the effectiveness of functional testing, manufacturers should follow these best practices:
-
Collaborate closely with the design team to develop comprehensive test plans and cases.
-
Invest in high-quality test equipment and tools to ensure accurate and reliable results.
-
Use automated testing wherever possible to improve efficiency and coverage.
-
Regularly review and update test plans and fixtures to keep pace with design changes and new requirements.
-
Provide adequate training and resources to test engineers to ensure they have the necessary skills and knowledge.
Frequently Asked Questions (FAQ)
-
What is the difference between functional testing and in-circuit testing (ICT)?
Functional testing verifies the overall functionality of the assembled PCB, while in-circuit testing focuses on testing individual components and their connections on the board. -
Is functional testing mandatory for all PCBs?
While functional testing is highly recommended for all PCBs, the extent and type of testing may vary depending on the specific application and industry requirements. Some industries, such as aerospace and medical devices, have strict regulatory requirements that mandate comprehensive functional testing. -
Can functional testing be performed without custom test fixtures?
While it is possible to perform some basic functional tests without custom fixtures, using purpose-built test fixtures is essential for comprehensive and reliable testing. Custom fixtures ensure proper connections and provide the necessary mechanical support during testing. -
How long does functional testing typically take?
The duration of functional testing can vary widely depending on the complexity of the PCB, the number of test cases, and the type of testing performed. Simple boards may take a few minutes to test, while more complex boards can take several hours or even days. -
What should be done if a PCB fails functional testing?
If a PCB fails functional testing, the first step is to perform debugging and failure analysis to identify the root cause of the failure. Once the issue has been identified, the necessary corrective actions should be taken, such as reworking the PCB or updating the design. The PCB should then be retested to ensure that the issue has been resolved and that it now meets all the functional requirements.
Conclusion
Functional testing is a vital step in the PCB assembly process, ensuring that the assembled board performs as intended and meets all the specified requirements. By verifying the PCB’s functionality, identifying defects, and ensuring product quality, functional testing helps manufacturers deliver reliable and high-performing products to their customers.
To implement an effective functional testing process, manufacturers should collaborate closely with their design teams, invest in high-quality test equipment and tools, and follow best practices such as using automated testing and regularly reviewing and updating test plans and fixtures.
By understanding the importance of functional testing, the various types of tests involved, and the challenges and best practices associated with the process, manufacturers can optimize their PCB assembly operations and deliver products that meet the highest standards of quality and reliability.
0 Comments