What is PCB Ultraviolet Laser Technology?
PCB ultraviolet laser technology involves using UV lasers to drill micro vias, cut circuits, and mark printed circuit boards (PCBs). UV lasers emit light in the ultraviolet range of the electromagnetic spectrum, with wavelengths typically between 355-375 nanometers.
The short wavelength of UV light allows for high-precision micromachining of PCBs with minimal heat-affected zones. This “cold” laser processing enables drilling and cutting of PCBs without damaging sensitive components.
Advantages of UV Lasers for PCBs
Compared to conventional mechanical drilling and CO2 or fiber lasers, UV lasers offer several advantages for PCB manufacturing:
Aspect | UV Laser | Mechanical Drilling | CO2/Fiber Laser |
---|---|---|---|
Hole Size | 5-200 μm | >200 μm | 50-500 μm |
Drilling Speed | High | Low | Medium |
Heat Damage | Minimal | None | High |
Flexibility | High | Low | Medium |
UV lasers can drill much smaller holes than mechanical bits, at a faster speed than CO2 lasers, with minimal collateral heat damage to the circuit board. The focused beam allows for complex patterns and rapid adaptation to design changes.
PCB UV Laser Drilling
One of the primary applications of ultraviolet lasers in PCB manufacturing is drilling micro vias and through holes. UV lasers can create high Aspect Ratio holes with diameters as small as 5-10 microns and depths up to 50x the diameter.
UV Laser Drilling Process
The UV laser drilling process involves:
- Focusing the UV laser beam onto the PCB surface
- Pulsing the laser to ablate the dielectric material
- Moving the beam or workpiece to create the desired hole pattern
- Cleaning debris from the holes using suction or washing
Key parameters in UV laser drilling include:
- Wavelength (355/375 nm)
- Pulse duration (nanoseconds)
- Pulse repetition rate (kHz)
- Pulse energy (microjoules)
- Beam spot size (microns)
- Number of pulses per hole
By optimizing these parameters for each material and thickness, UV lasers can produce precise, clean, high-density holes for vias and component interconnects.
Benefits of UV Laser Drilling
UV laser drilled micro vias enable high density interconnect (HDI) PCB designs with benefits such as:
- Smaller form factors
- Lighter weight
- Higher component density
- Shorter signal paths
- Improved electrical performance
UV laser drilling also allows stacked and staggered vias further increasing circuit density compared to through hole designs.
PCB UV Laser Cutting
Another major use of ultraviolet lasers in PCB manufacturing is cutting out circuit patterns, drilling large holes, and singulating boards.
UV Laser Cutting Process
UV laser cutting of PCBs uses similar setups and techniques as UV drilling but with higher power and deeper cuts. The focused UV beam follows a 2D tool path to cut through the copper and substrate.
Factors affecting UV laser cutting of PCBs include:
- Material type and thickness
- Beam power and spot size
- Cutting speed and overlap
- Number of passes
Proper settings can minimize heat effects and produce a clean, burr-free cut edge. Assist gas, such as compressed air or nitrogen, helps remove ablated material.
Advantages of UV PCB Cutting
UV laser cutting provides advantages over mechanical methods like routing or punching:
- No tool wear or breakage
- Easier adaption to design changes
- Smaller features and curves
- Less material waste
- Burr-free and clean cut edges
UV lasers are ideal for quick-turn prototyping and complex PCB geometries not feasible with standard routing bits or dies.
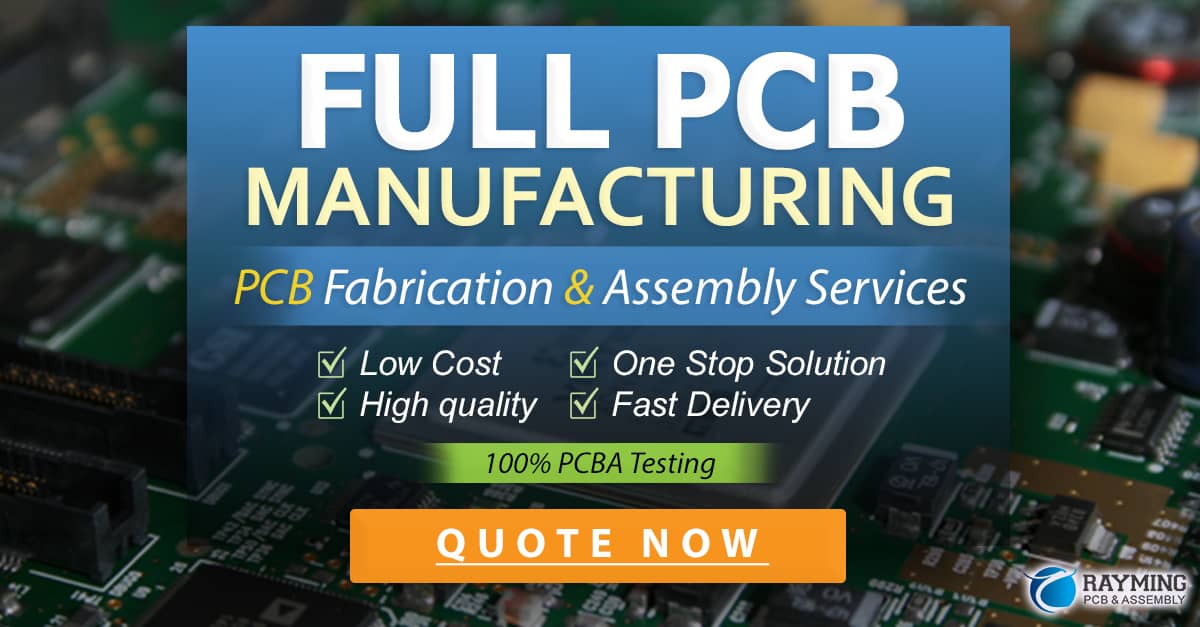
PCB UV Laser Marking
Ultraviolet lasers also find use marking PCBs for identification, traceability and information purposes. UV laser marking creates high contrast, permanent markings for:
- Barcodes and QR codes
- Serial numbers
- Logos and graphics
- Electrical parameters
- Standards compliance
UV laser marking works by selectively altering the surface through:
- Engraving/ablation
- Annealing/color change
- Foaming
The short wavelength and control of UV lasers allows crisp marking of detailed graphics without damage.
Considerations for PCB UV Laser Processing
When utilizing ultraviolet lasers for PCB manufacturing some important considerations include:
Material Compatibility
Not all PCB materials interact the same with UV light. Some substances absorb UV better enabling efficient drilling/cutting, while others may reflect or transmit the light. Fillers like fiberglass can affect the laser process.
Common PCB materials suitable for UV laser processing include:
- FR-4
- Polyimides
- PTFE
- Ceramics
- Flexible films
Testing is recommended to determine optimal laser parameters for each unique material combination.
Laser Safety
UV laser light can pose risks to eyes and skin. Even though UV is mostly invisible, the high intensity can cause photokeratitis (arc eye) or burns.
UV laser systems require proper shielding, interlocks, and personal protective equipment (PPE) like:
- Laser safety glasses
- Gloves
- Clothing
Fumes from laser processing may contain hazardous compounds requiring ventilation. Always follow laser safety protocols.
Capital Investment
Industrial UV laser systems for PCBs have higher upfront costs compared to conventional equipment like CNC machines. Justifying a UV laser purchase requires sufficient production volume of high-value parts.
Typical pricing for a UV laser PCB drilling/cutting system ranges from $100k to over $1M depending on performance. Maintenance and consumables add to the total cost of ownership.
Future of UV Lasers in PCB Manufacturing
Ultraviolet lasers continue expanding their roles and capabilities in PCB Production. Trends and developments to watch include:
Shorter Wavelengths
Researchers are exploring UV lasers with even shorter wavelengths, such as 266 nm (fourth harmonic) or 213 nm (fifth harmonic). These systems could enable finer features but face challenges in cost and optics.
Faster Pulse Rates
Newer UV lasers offer pulse rates approaching 1 MHz or higher. Such speeds allow faster drilling and cutting to keep up with shrinking PCB features.
Larger Panel Sizes
UV lasers with more powerful beams and bigger scan fields can accommodate the trend towards larger PCB Panel Sizes, such as 25×30 inches or greater. This boosts production efficiency.
Integration and Automation
UV laser systems are becoming more integrated with other PCB processes like direct imaging and inspection. Automation improves quality and throughput.
Frequently Asked Questions (FAQ)
What is the main advantage of using a UV laser for PCB drilling?
UV lasers can drill much smaller micro vias with diameters down to 5 microns compared to mechanical drills limited to around 200 microns. This enables higher density interconnects.
How fast can UV lasers drill holes in PCBs?
The drilling speed depends on the number and size of holes, but modern UV laser systems can drill over 1000 holes per second. A typical 18×24 inch PCB may have 20,000 holes drilled in under a minute.
Are there any downsides to UV laser cutting of PCBs?
One potential issue is heat damage to sensitive areas adjacent to the cut path. This can be minimized through parameter optimization and assist gas. UV lasers also cannot easily cut thick metal layers over 1 mm.
What type of UV laser is best for PCB processing?
Many systems use frequency-tripled Nd:YAG or Nd:YVO4 lasers at 355 nm, though some use 375 nm diode-pumped solid-state (DPSS) lasers. Excimer gas lasers are less common. Newer options include UV fiber lasers and direct diode lasers.
How much does a UV laser system for PCBs cost?
Prices vary widely based on performance specs, but entry-level systems start around $100,000 while high-end production lines can exceed $1 million. This is more than mechanical equipment but enables capabilities essential for advanced HDI and flexible circuits.
0 Comments