Introduction to PCB Simulation
PCB (Printed Circuit Board) simulation is a crucial step in the design and manufacturing process of electronic devices. It allows engineers to test and optimize the performance of their PCB Designs before physically manufacturing them. PCB simulation can be divided into two main categories: pre-layout simulation and post-layout simulation. In this article, we will explore the differences between these two types of PCB simulation and their importance in the PCB design process.
What is Pre-Layout PCB Simulation?
Pre-layout PCB simulation is performed before the actual PCB Layout is created. It involves simulating the schematic design of the PCB to ensure that the circuit functions as intended. Pre-layout simulation focuses on the electrical behavior of the circuit, including component values, connectivity, and signal integrity.
Benefits of Pre-Layout PCB Simulation
- Early Detection of Design Flaws: Pre-layout simulation helps identify design issues early in the development cycle, reducing the need for costly redesigns later on.
- Optimization of Circuit Performance: By simulating the circuit before layout, engineers can optimize component values and circuit topology to achieve the desired performance.
- Time and Cost Savings: Identifying and fixing design issues during the pre-layout stage saves time and money compared to discovering problems after the PCB has been manufactured.
What is Post-Layout PCB Simulation?
Post-layout PCB simulation is performed after the PCB layout has been created. It takes into account the physical characteristics of the PCB, such as trace widths, lengths, and spacing, as well as the placement of components. Post-layout simulation provides a more accurate representation of the PCB’s behavior, including parasitic effects and electromagnetic interactions.
Benefits of Post-Layout PCB Simulation
- Verification of Signal Integrity: Post-layout simulation allows engineers to analyze the impact of PCB layout on signal integrity, including crosstalk, reflections, and power integrity.
- Electromagnetic Compatibility (EMC) Analysis: Post-layout simulation can be used to assess the PCB’s electromagnetic compatibility, ensuring that it meets regulatory requirements and does not interfere with other electronic devices.
- Thermal Analysis: Post-layout simulation can also include thermal analysis to ensure that the PCB operates within safe temperature ranges and dissipates heat effectively.
Differences Between Pre-Layout and Post-Layout PCB Simulation
Now that we have a basic understanding of pre-layout and post-layout PCB simulation, let’s dive into the key differences between the two.
Timing of Simulation
The primary difference between pre-layout and post-layout simulation is the stage at which they are performed in the PCB design process.
Simulation Type | Timing |
---|---|
Pre-Layout | Before PCB layout, during schematic design |
Post-Layout | After PCB layout, before manufacturing |
Level of Detail
Pre-layout and post-layout simulations differ in the level of detail they consider.
Simulation Type | Level of Detail |
---|---|
Pre-Layout | Focuses on electrical behavior, component values, and connectivity |
Post-Layout | Includes physical characteristics, parasitic effects, and electromagnetic interactions |
Accuracy of Results
The accuracy of simulation results varies between pre-layout and post-layout simulations.
Simulation Type | Accuracy |
---|---|
Pre-Layout | Provides a general idea of circuit performance, but does not account for physical layout effects |
Post-Layout | Offers a more accurate representation of the PCB’s behavior, considering layout-dependent factors |
Simulation Tools
Different tools are used for pre-layout and post-layout PCB simulations.
Simulation Type | Common Tools |
---|---|
Pre-Layout | SPICE simulators (e.g., LTspice, PSpice), Multisim, Cadence OrCAD |
Post-Layout | Ansys SIwave, Cadence Sigrity, Mentor Graphics HyperLynx |
PCB Simulation Workflow
To better understand the role of pre-layout and post-layout simulations in the PCB design process, let’s look at a typical PCB simulation workflow.
-
Schematic Design: The PCB design process begins with creating a schematic diagram of the circuit. This includes selecting components, defining their values, and specifying the connectivity between them.
-
Pre-Layout Simulation: Once the schematic is complete, pre-layout simulation is performed to verify the circuit’s functionality and performance. This step helps identify any design issues early on and allows for optimization of component values and circuit topology.
-
PCB Layout: After the pre-layout simulation is satisfactory, the PCB layout is created. This involves placing components on the board, routing traces, and defining the physical dimensions of the PCB.
-
Post-Layout Simulation: With the PCB layout complete, post-layout simulation is performed to analyze the impact of the physical layout on the circuit’s behavior. This step includes signal integrity analysis, EMC analysis, and thermal analysis.
-
Design Refinement: Based on the results of the post-layout simulation, the PCB design may need to be refined to address any issues discovered. This may involve adjusting component placement, modifying trace routing, or adding shielding or filtering components.
-
Manufacturing: Once the post-layout simulation results are satisfactory, the PCB design is ready for manufacturing. The design files are sent to a PCB Fabrication house for production.
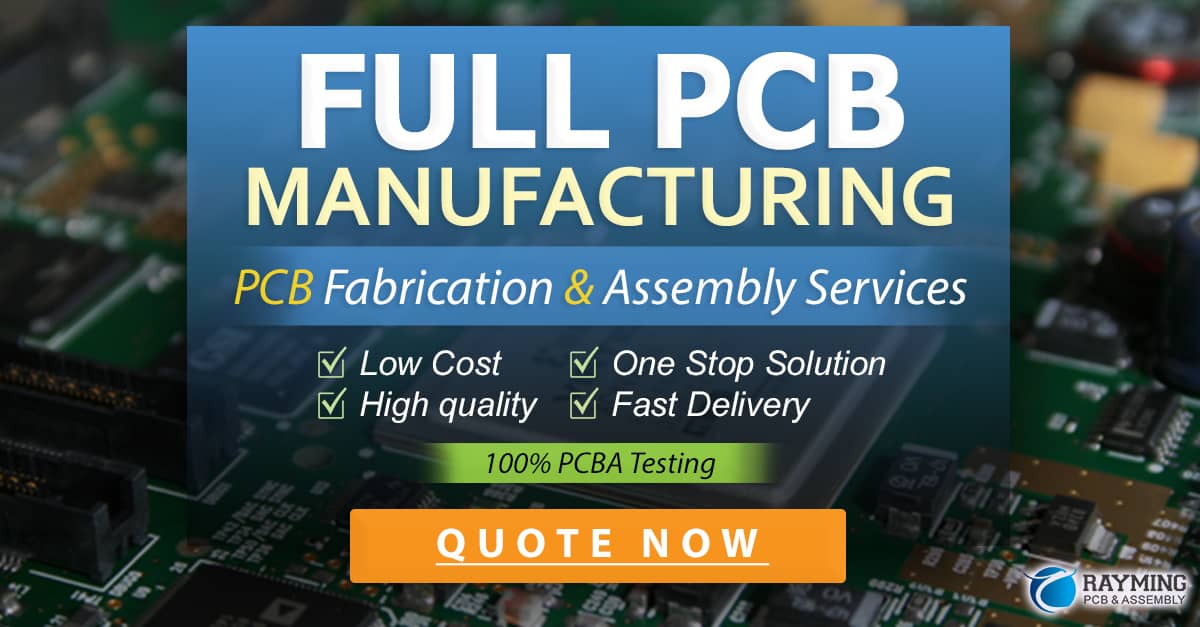
Best Practices for PCB Simulation
To ensure accurate and reliable PCB simulations, consider the following best practices:
-
Use Accurate Models: Ensure that the component models used in simulations are accurate and up-to-date. This includes using manufacturer-provided SPICE models when available.
-
Define Simulation Goals: Clearly define the goals of each simulation, such as verifying functionality, analyzing signal integrity, or assessing EMC performance. This helps focus the simulation efforts and ensures that the necessary analyses are performed.
-
Validate Simulation Results: Compare simulation results with measurements from physical prototypes to validate the accuracy of the simulations. This helps refine the simulation models and increases confidence in future simulations.
-
Collaborate with PCB Layout Designers: Maintain open communication between circuit designers and PCB layout designers throughout the design process. This ensures that the layout considers the circuit’s requirements and that any layout-related issues are addressed promptly.
-
Document Simulation Results: Maintain detailed documentation of simulation results, including the simulation setup, input parameters, and output waveforms. This helps with troubleshooting and provides a reference for future designs.
FAQs
-
Q: Can pre-layout simulation completely replace post-layout simulation?
A: No, pre-layout simulation cannot replace post-layout simulation. While pre-layout simulation is essential for verifying the circuit’s functionality and performance, it does not account for the physical layout effects that can impact the PCB’s behavior. Post-layout simulation is necessary to ensure that the PCB will function as intended after manufacturing. -
Q: What are the most common issues discovered during post-layout PCB simulation?
A: Some of the most common issues discovered during post-layout PCB simulation include signal integrity problems (such as crosstalk, reflections, and ground bounce), power integrity issues (such as voltage drops and power supply noise), and electromagnetic compatibility (EMC) concerns (such as radiated emissions and susceptibility to external interference). -
Q: How long does PCB simulation typically take?
A: The duration of PCB simulation depends on the complexity of the design, the level of detail required, and the computing resources available. Simple pre-layout simulations may take a few minutes, while complex post-layout simulations can take several hours or even days. It is essential to allocate sufficient time for simulation to ensure thorough analysis and optimization of the PCB design. -
Q: Are there any limitations to PCB simulation?
A: While PCB simulation is a powerful tool for analyzing and optimizing PCB designs, it does have some limitations. Simulations are based on models and assumptions, which may not perfectly represent real-world conditions. Additionally, some complex phenomena, such as non-linear effects or high-frequency behavior, may be challenging to simulate accurately. It is essential to validate simulation results with physical measurements to ensure the reliability of the simulations. -
Q: Can PCB simulation be used for high-speed digital designs?
A: Yes, PCB simulation is particularly important for high-speed digital designs. As signal speeds increase, the impact of physical layout effects on signal integrity becomes more significant. Post-layout simulation is crucial for analyzing and mitigating issues such as signal reflections, crosstalk, and power supply noise in high-speed digital designs. Specialized simulation tools and techniques, such as multi-gigabit serial link analysis and power integrity analysis, are often employed for high-speed Digital PCB simulations.
Conclusion
PCB simulation is a vital step in the design and manufacturing process of electronic devices. Pre-layout and post-layout simulations play different but equally important roles in ensuring the functionality, performance, and reliability of PCBs.
Pre-layout simulation focuses on verifying the circuit’s electrical behavior and optimizing component values and topology. It helps identify design issues early in the development cycle, saving time and cost.
Post-layout simulation, on the other hand, takes into account the physical characteristics of the PCB layout, including parasitic effects and electromagnetic interactions. It provides a more accurate representation of the PCB’s behavior and is essential for analyzing signal integrity, EMC, and thermal performance.
By understanding the differences between pre-layout and post-layout PCB simulations and following best practices for simulation, engineers can create robust and reliable PCB designs that meet the desired performance requirements. Investing time and effort in thorough PCB simulations can ultimately lead to faster time-to-market, reduced development costs, and improved product quality.
0 Comments