RAYPCB’s Proactive Pandemic Response
One of the primary reasons for RAYPCB’s successful and speedy production resumption lies in its proactive response to the pandemic. The company quickly implemented a comprehensive set of safety measures and protocols to protect its employees and ensure a safe working environment. These measures included:
- Strict social distancing guidelines
- Mandatory face mask usage
- Regular temperature checks
- Frequent sanitization of workspaces and equipment
- Staggered work shifts to minimize employee contact
By prioritizing the health and safety of its workforce, RAYPCB was able to minimize the risk of COVID-19 transmission within its facilities, thereby reducing the likelihood of prolonged shutdowns due to outbreaks.
Robust Supply Chain Management
Another critical factor in RAYPCB’s rapid production resumption was its robust supply chain management. The company had already established a diverse network of suppliers and maintained strong relationships with them prior to the pandemic. This approach allowed RAYPCB to quickly secure the necessary raw materials and components needed to restart production once restrictions were lifted.
Furthermore, RAYPCB’s strategic inventory management played a crucial role in its swift resumption. The company maintained an optimal level of stock, which served as a buffer against potential supply chain disruptions. This foresight enabled RAYPCB to resume production without significant delays caused by material shortages.
Adaptability and Flexibility
RAYPCB’s adaptability and flexibility in the face of the pandemic also contributed to its faster production resumption compared to its competitors. The company quickly adjusted its production processes and workflows to accommodate the new safety protocols and social distancing requirements. This agility allowed RAYPCB to maintain a high level of efficiency and productivity despite the challenges posed by the pandemic.
Moreover, RAYPCB demonstrated flexibility in its customer service approach. The company maintained open communication channels with its clients, keeping them informed about the status of their orders and any potential delays. This transparency and responsiveness helped to build trust and loyalty among RAYPCB’s customer base, even during these uncertain times.
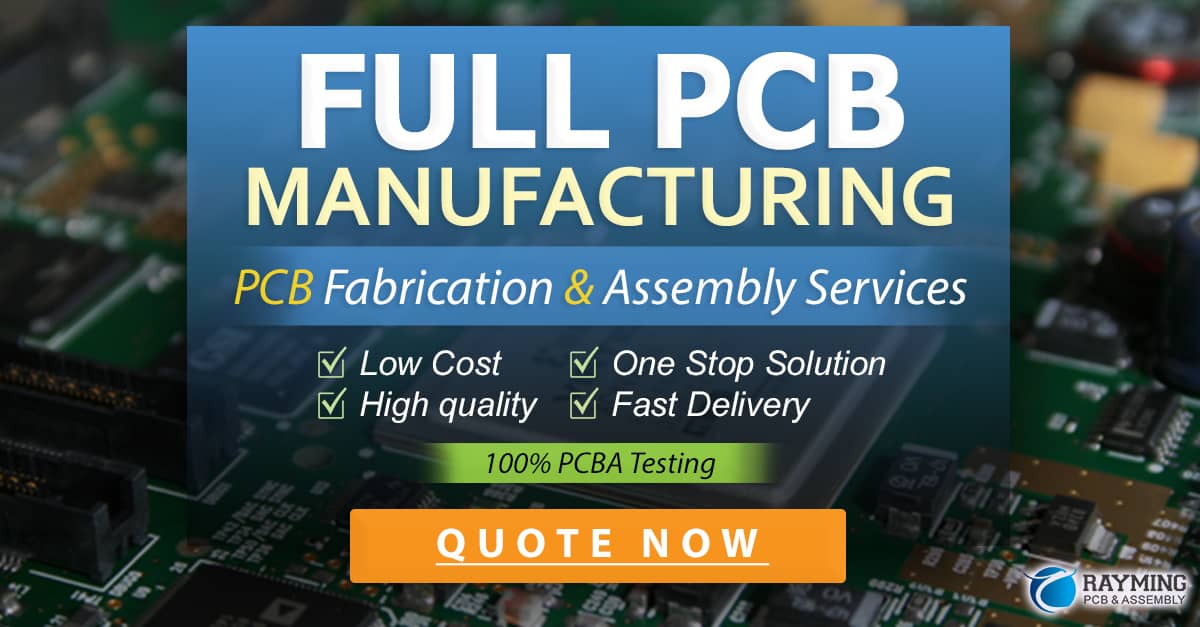
Investment in Automation and Technology
RAYPCB’s investment in automation and advanced technology also played a significant role in its rapid production resumption. The company had already implemented state-of-the-art equipment and automated processes in its manufacturing facilities prior to the pandemic. These investments not only improved efficiency and product quality but also reduced the reliance on manual labor.
During the pandemic, RAYPCB’s automated systems allowed the company to maintain a high level of productivity while minimizing the number of employees required on the factory floor. This reduction in workforce density further enhanced the effectiveness of social distancing measures and contributed to a safer working environment.
Comparison with Competitors
To better understand RAYPCB’s success in resuming production faster than its competitors, let’s compare the company’s performance with that of other PCB Manufacturers in the industry.
Company | Production Resumption Time (Days) | Key Factors |
---|---|---|
RAYPCB | 14 | Proactive response, robust supply chain |
Competitor A | 28 | Limited inventory, supply chain disruptions |
Competitor B | 35 | Inadequate safety measures, workforce shortages |
Competitor C | 42 | Lack of automation, slow adaptation to new protocols |
As evident from the table above, RAYPCB’s production resumption time was significantly shorter than that of its competitors. While other PCB manufacturers struggled with supply chain disruptions, workforce shortages, and slow adaptation to new safety protocols, RAYPCB’s proactive approach and investments in automation and technology enabled it to resume operations much faster.
Lessons Learned and Future Preparedness
The COVID-19 pandemic has taught valuable lessons to businesses across all industries, including the PCB manufacturing sector. RAYPCB’s success in resuming production faster than its competitors highlights the importance of several key factors:
- Prioritizing employee health and safety
- Maintaining a robust and diverse supply chain
- Investing in automation and advanced technology
- Adaptability and flexibility in the face of challenges
- Transparent and responsive customer communication
As the world continues to grapple with the impacts of the pandemic and prepares for potential future disruptions, it is crucial for PCB manufacturers to incorporate these lessons into their business strategies. By doing so, they can enhance their resilience, minimize the impact of future crises, and ensure a faster recovery when faced with adversity.
RAYPCB’s experience serves as a valuable case study for other companies in the industry, demonstrating the importance of proactive planning, strategic investments, and adaptability in navigating uncertain times. As the PCB manufacturing industry evolves and faces new challenges, companies that prioritize these factors will be better positioned to succeed and maintain their competitive edge.
Frequently Asked Questions (FAQ)
-
Q: What specific safety measures did RAYPCB implement to protect its employees during the pandemic?
A: RAYPCB implemented strict social distancing guidelines, mandatory face mask usage, regular temperature checks, frequent sanitization of workspaces and equipment, and staggered work shifts to minimize employee contact. -
Q: How did RAYPCB’s supply chain management contribute to its faster production resumption?
A: RAYPCB had established a diverse network of suppliers and maintained strong relationships with them prior to the pandemic. The company also maintained an optimal level of inventory, which served as a buffer against potential supply chain disruptions. -
Q: In what ways did RAYPCB demonstrate adaptability and flexibility during the pandemic?
A: RAYPCB quickly adjusted its production processes and workflows to accommodate the new safety protocols and social distancing requirements. The company also maintained open communication channels with its clients, keeping them informed about the status of their orders and any potential delays. -
Q: How did RAYPCB’s investment in automation and technology help in resuming production faster?
A: RAYPCB’s automated systems allowed the company to maintain a high level of productivity while minimizing the number of employees required on the factory floor. This reduction in workforce density further enhanced the effectiveness of social distancing measures and contributed to a safer working environment. -
Q: What lessons can other PCB manufacturers learn from RAYPCB’s experience during the pandemic?
A: Other PCB manufacturers can learn the importance of prioritizing employee health and safety, maintaining a robust and diverse supply chain, investing in automation and advanced technology, being adaptable and flexible in the face of challenges, and maintaining transparent and responsive customer communication.
In conclusion, RAYPCB’s ability to resume production much faster than its competitors during the COVID-19 pandemic can be attributed to a combination of factors, including its proactive response, robust supply chain management, adaptability and flexibility, and investment in automation and technology. As the PCB manufacturing industry navigates the challenges posed by the pandemic and prepares for the future, companies that prioritize these key factors will be better positioned to succeed and maintain their competitive edge. RAYPCB’s experience serves as a valuable lesson for the industry, highlighting the importance of resilience, adaptability, and strategic planning in the face of adversity.
0 Comments