Introduction to Silk Screen Printing for PCBs
Silk screen printing, also known as screen printing or serigraphy, is a versatile printing technique that has been widely used in various industries for decades. In the realm of printed circuit board (PCB) manufacturing, silk screen printing plays a crucial role in applying non-conductive ink onto the surface of the PCB. This process is commonly referred to as “silk screening” or “legend printing” in the PCB industry.
The primary purpose of silk screen printing on PCBs is to provide clear and durable markings, such as component identifiers, logos, and text, which aid in the assembly, testing, and maintenance of electronic devices. The silk screen layer serves as a visual guide for engineers, technicians, and end-users, making it easier to identify and work with the various components on the PCB.
The Silk Screen Printing Process
Silk screen printing involves the use of a fine mesh screen, typically made of polyester or stainless steel, which is stretched tightly over a frame. The desired design, such as component identifiers or logos, is created on the screen using a photosensitive emulsion or a stencil. The areas of the screen that are not part of the design are blocked out, allowing ink to pass through only in the desired areas.
To print on a PCB, the screen is placed over the board, and ink is applied to the top of the screen. A squeegee is then used to push the ink through the open areas of the screen, transferring the design onto the surface of the PCB. The ink is then cured, typically using UV light or heat, to ensure a strong bond and long-lasting durability.
Advantages of Silk Screen Printing for PCBs
Silk screen printing offers several advantages for PCB manufacturing:
-
Durability: Silk screened markings are highly durable and resistant to wear, abrasion, and chemicals, ensuring long-lasting legibility.
-
Precision: The silk screen process allows for precise and detailed printing, enabling the creation of intricate designs and small text.
-
Versatility: Silk screening can be used on a wide range of PCB Materials, including FR-4, ceramic, and metal-core substrates.
-
Cost-effectiveness: For medium to large production runs, silk screen printing is a cost-effective method for applying markings to PCBs.
Silk Screen Ink Types and Properties
The choice of ink is crucial for achieving high-quality, durable markings on PCBs. Several types of ink are commonly used in silk screen printing for PCBs, each with its own unique properties and advantages.
Epoxy-Based Inks
Epoxy-based inks are among the most popular choices for silk screening PCBs due to their excellent durability and resistance properties. These inks are composed of a two-part system, consisting of a resin and a hardener, which react chemically to form a strong, cross-linked polymer when cured. Epoxy-based inks offer several advantages:
- High resistance to chemicals, solvents, and abrasion
- Excellent adhesion to various PCB Substrates
- Wide operating temperature range
- Long shelf life and pot life
However, epoxy-based inks typically require a longer curing time compared to other ink types and may be more expensive.
UV-Curable Inks
UV-curable inks are another popular option for silk screening PCBs. These inks are formulated to cure rapidly when exposed to ultraviolet (UV) light, allowing for faster production times and improved efficiency. UV-curable inks provide several benefits:
- Fast curing time, often within seconds
- Good resistance to chemicals and abrasion
- Excellent print definition and edge sharpness
- Lower energy consumption during the curing process
One drawback of UV-curable inks is that they may not be as durable as epoxy-based inks in extreme environmental conditions.
Comparison of Ink Properties
Property | Epoxy-Based Inks | UV-Curable Inks |
---|---|---|
Durability | Excellent | Good |
Chemical Resistance | High | Good |
Abrasion Resistance | High | Good |
Adhesion | Excellent | Good |
Curing Time | Longer (minutes to hours) | Fast (seconds) |
Cost | Higher | Moderate |
The choice between epoxy-based and UV-curable inks depends on the specific requirements of the PCB application, such as the desired durability, production speed, and cost considerations.
Silk Screen Mesh and Stencil Considerations
The quality and precision of the silk screen printing process depend heavily on the selection of the appropriate mesh and stencil materials. The mesh and stencil work together to define the design that will be printed on the PCB surface.
Mesh Material and Count
Silk screen meshes are typically made from polyester or stainless steel, with polyester being the more common choice for PCB Applications. The mesh is characterized by its thread diameter and the number of threads per inch (TPI) or threads per centimeter (TPC). A higher mesh count indicates a finer mesh, which allows for more detailed prints and better ink control.
Common mesh counts for PCB silk screening range from 80 to 400 TPI (32 to 158 TPC). The choice of mesh count depends on factors such as the desired print resolution, ink viscosity, and substrate surface.
Mesh Count (TPI) | Mesh Count (TPC) | Typical Applications |
---|---|---|
80-100 | 32-40 | Large, bold text and graphics |
120-160 | 47-63 | General-purpose printing |
180-250 | 71-99 | Fine details and small text |
280-400 | 110-158 | Very fine details and high-resolution printing |
Stencil Materials and Techniques
Stencils are used to define the design that will be printed on the PCB surface. There are several stencil materials and techniques available for silk screen printing:
-
Photoemulsion: A light-sensitive emulsion is applied to the mesh and exposed to UV light through a film positive of the desired design. The unexposed areas are then washed away, leaving a stencil of the design on the mesh.
-
Capillary Film: A pre-sensitized, self-adhesive film is applied to the mesh and exposed to UV light through a film positive. The unexposed areas are washed away, creating a stencil.
-
Direct Emulsion: A light-sensitive emulsion is applied directly to the mesh and exposed to UV light through a film positive. The unexposed areas are washed away, forming a stencil.
-
Laser-Cut Stencils: A stencil is created by laser-cutting the desired design into a thin, durable material such as mylar or metal. This method offers high precision and is suitable for intricate designs.
The choice of stencil material and technique depends on factors such as the desired print quality, durability, and production efficiency.
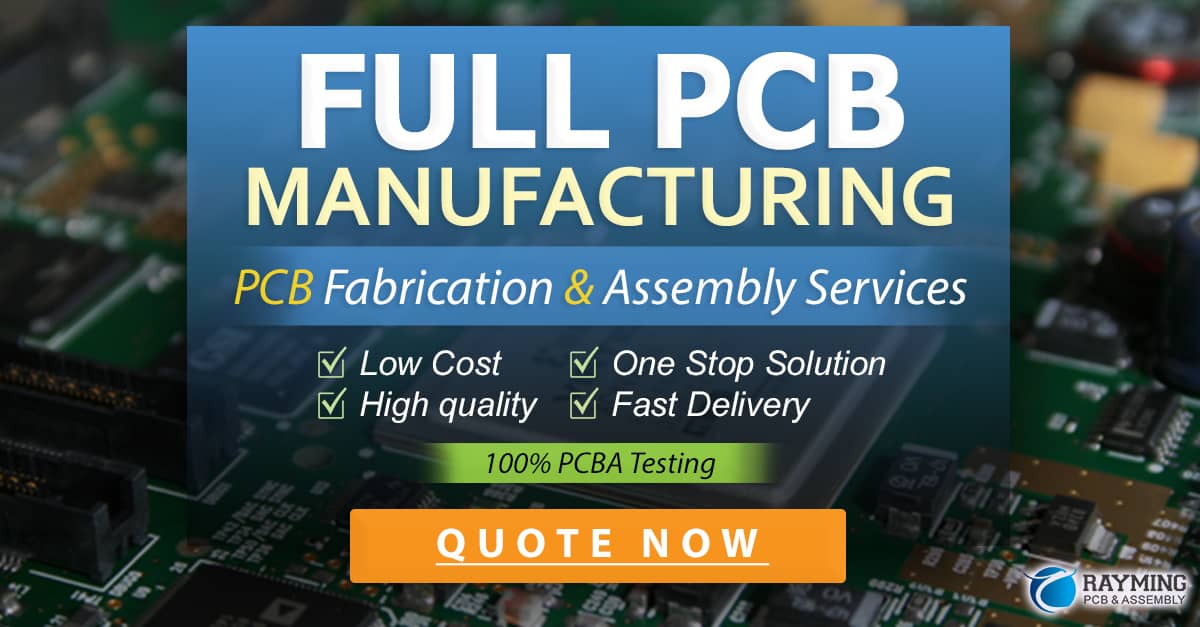
Silk Screen Printing Process Optimization
To achieve the best results in silk screen printing for PCBs, it is essential to optimize various aspects of the printing process. This includes ink preparation, screen setup, printing parameters, and curing conditions.
Ink Preparation and Handling
Proper ink preparation and handling are crucial for achieving consistent print quality and preventing issues such as clogging or premature curing. Some key considerations include:
-
Mixing: Thoroughly mix the ink components (resin and hardener for epoxy-based inks) according to the manufacturer’s instructions, ensuring a homogeneous mixture.
-
Viscosity Control: Maintain the ink viscosity within the recommended range for optimal print quality. Use compatible thinners or retarders to adjust the viscosity as needed.
-
Storage: Store inks in a cool, dry place, away from direct sunlight and heat sources. Follow the manufacturer’s guidelines for storage temperature and shelf life.
Screen Setup and Alignment
Accurate screen setup and alignment are essential for achieving precise and consistent prints on PCBs. Key factors to consider include:
-
Screen Tension: Maintain proper screen tension to ensure a smooth and even ink deposit. Regularly check and adjust the tension as needed.
-
Alignment: Use alignment tools, such as pin registration systems or optical alignment devices, to ensure precise alignment between the screen and the PCB.
-
Off-Contact Distance: Maintain a consistent off-contact distance between the screen and the PCB surface to prevent smudging and ensure clear prints.
Printing Parameters
Optimizing printing parameters helps to achieve the desired print quality and consistency. Important parameters to consider include:
-
Squeegee Pressure: Apply appropriate squeegee pressure to ensure even ink coverage and prevent bleed-through or incomplete prints.
-
Squeegee Angle: Maintain a consistent squeegee angle (typically 45-60 degrees) to promote even ink deposit and prevent screen damage.
-
Print Speed: Adjust the print speed to achieve the desired ink flow and coverage. Faster speeds may be suitable for larger areas, while slower speeds are better for fine details.
Curing Conditions
Proper curing is essential for achieving strong adhesion and durability of the silk screened markings on PCBs. Optimize the curing conditions based on the ink type and manufacturer’s recommendations:
-
UV-Curable Inks: Ensure sufficient UV exposure (intensity and duration) for complete curing. Follow the ink manufacturer’s guidelines for the optimal UV wavelength and energy output.
-
Epoxy-Based Inks: Maintain the recommended curing temperature and duration for complete cross-linking of the resin and hardener. Avoid excessive temperatures that may cause discoloration or damage to the PCB.
Regular monitoring and adjustment of these printing process parameters help to maintain consistent print quality and minimize defects, ensuring the production of high-quality silk screened PCBs.
Quality Control and Inspection
Implementing a robust quality control and inspection process is essential for ensuring the consistency and reliability of silk screened PCBs. This involves visual inspection, measurement, and testing to detect and correct any defects or deviations from the specified requirements.
Visual Inspection
Visual inspection is the first line of defense in identifying silk screen printing defects. Trained operators visually examine the printed PCBs for issues such as:
-
Incomplete or missing prints: Check for areas where the ink failed to transfer or was not fully deposited.
-
Blurred or smudged prints: Look for signs of ink spreading, bleed-through, or poor edge definition.
-
Color consistency: Verify that the ink color matches the specified requirements and is consistent across the batch.
-
Alignment: Ensure that the printed markings are correctly aligned with the PCB features and components.
Visual inspection can be performed manually or using automated optical inspection (AOI) systems for higher throughput and consistency.
Measurement and Dimensional Checks
Measuring and verifying the dimensions of the silk screened markings is crucial for ensuring compliance with the design specifications. This can be done using various tools and techniques, such as:
-
Optical Measurement: Use optical microscopes or vision systems to measure the dimensions of the printed features, such as line widths, spacing, and character sizes.
-
Coordinate Measuring Machines (CMMs): Employ CMMs to accurately measure the position and dimensions of the printed markings relative to the PCB features.
-
Gauge Pins or Calipers: Utilize gauge pins or calipers to physically measure the dimensions of the printed features and verify conformance to the specified tolerances.
Adhesion and Durability Testing
Testing the adhesion and durability of the silk screened markings is essential for ensuring their long-term performance and reliability. Common test methods include:
-
Tape Test: Apply a standard adhesive tape to the printed surface and rapidly remove it at a specified angle. Inspect the tape and the PCB surface for any ink removal or damage.
-
Abrasion Test: Subject the printed PCB to a controlled abrasive force, such as a rubbing action with a specified material, to evaluate the resistance of the markings to wear and abrasion.
-
Chemical Resistance Test: Expose the silk screened PCB to various chemicals, such as solvents, cleaning agents, or fluxes, to assess the resistance of the markings to chemical attack.
-
Environmental Testing: Evaluate the performance of the silk screened markings under different environmental conditions, such as high temperature, humidity, or thermal cycling, to ensure their stability and durability.
By implementing a comprehensive quality control and inspection process, manufacturers can identify and address silk screen printing issues early in the production process, reducing the risk of defective products reaching the end-users.
Frequently Asked Questions (FAQ)
-
Q: What is the purpose of silk screen printing on PCBs?
A: Silk screen printing on PCBs is used to apply non-conductive ink markings, such as component identifiers, logos, and text, to aid in the assembly, testing, and maintenance of electronic devices. -
Q: What are the most common types of ink used for silk screening PCBs?
A: The two most common types of ink used for silk screening PCBs are epoxy-based inks and UV-curable inks. Epoxy-based inks offer excellent durability and resistance properties, while UV-curable inks provide faster curing times and good print definition. -
Q: How does the mesh count affect the silk screen printing process?
A: The mesh count, measured in threads per inch (TPI) or threads per centimeter (TPC), determines the print resolution and ink control. Higher mesh counts allow for finer details and better ink control, while lower mesh counts are suitable for larger, bold prints. -
Q: What are the key factors to consider when optimizing the silk screen printing process for PCBs?
A: Key factors to consider when optimizing the silk screen printing process include ink preparation and handling, screen setup and alignment, printing parameters (such as squeegee pressure, angle, and speed), and curing conditions (UV exposure or temperature and duration for epoxy-based inks). -
Q: What quality control measures are typically employed for silk screened PCBs?
A: Quality control measures for silk screened PCBs include visual inspection (manual or automated) to identify defects, measurement and dimensional checks to verify conformance to specifications, and adhesion and durability testing to ensure the long-term performance of the printed markings.
Conclusion
Silk screen printing plays a vital role in the production of high-quality, reliable PCBs by providing clear and durable markings that facilitate assembly, testing, and maintenance. By understanding the various aspects of the silk screen printing process, such as ink selection, mesh and stencil considerations, process optimization, and quality control, manufacturers can ensure the consistent production of silk screened PCBs that meet the required specifications and performance standards.
As the electronics industry continues to evolve, with increasing demands for miniaturization and higher functionality, the importance of precise and reliable silk screen printing on PCBs will only continue to grow. By staying up-to-date with the latest developments in silk screen technology, materials, and processes, PCB Manufacturers can remain competitive and deliver products that meet the ever-changing needs of their customers.
0 Comments