Yes, printed circuit boards (PCBs) are manufactured in the United States at domestic facilities operated by both large global electronics producers and smaller specialized American fabricators. However, the majority of PCB production has shifted overseas over recent decades.
Roughly 2-4% of global PCB output currently originates from U.S. based production according to industry estimates. Domestic capacity remains robust in certain military, aerospace, medical and other high reliability board segments yet faces stiff cost competition abroad for high volume commercial goods.
Nevertheless, hundreds of American companies still supply PCBs to electronics firms across varied end markets. Their domestic production, engineering support and supply chain logistics offer differentiated value securing continued viability against foreign rivals.
History of Printed Circuit Board Manufacturing in USA
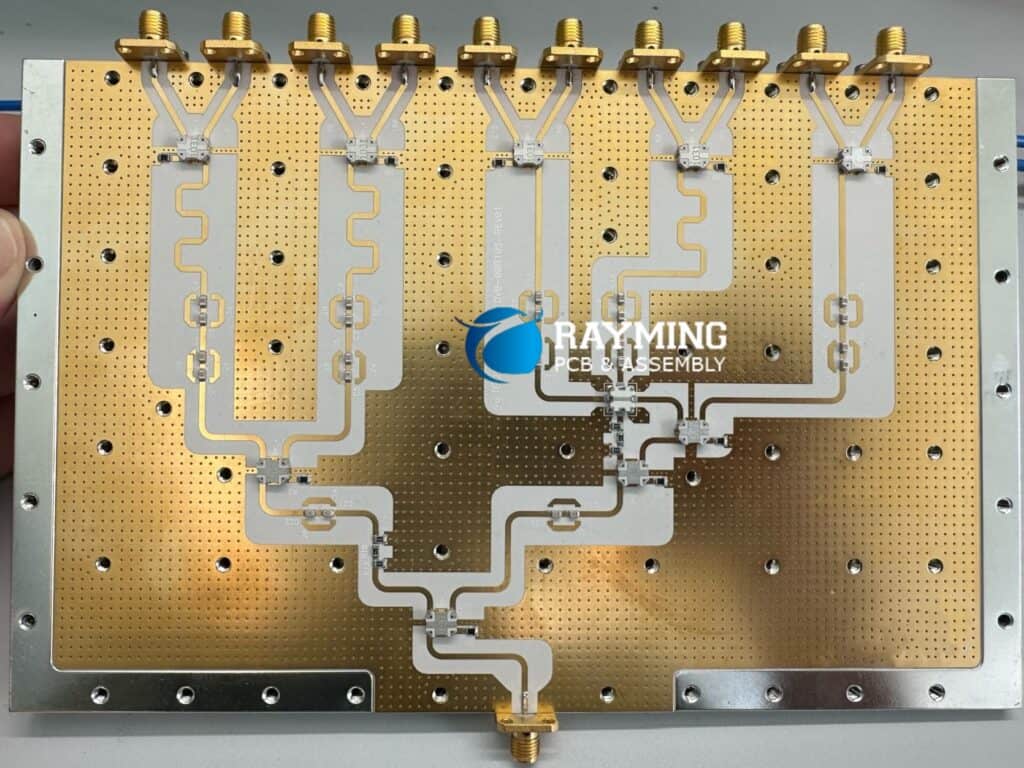
The American PCB industry pioneered much of the early development in printed circuit board technology establishing U.S. as leader in PCB manufacturing during the 20th century.
Origins
Printed circuits themselves were first invented in the United States in 1903 by Albert Hanson although commercialization awaited mid-century. The 1952 launch of a mechanized production process at Square D marked arrival of volume PCB fabrication stateside.
**Rapid Growth Phase **
During the 1960s-80s, newly founded PCB shops proliferated across America thanks rising electronics demand from appliance, computer, automotive and assembly industries. Aerospace applications also drove much innovation as the industry matured.
Globalization Pressures
From 1970s onwards however, smaller U.S. PCB manufacturers began facing existential cost pressures as labor wages climbed against fierce global competition from Asian and European rivals. Offshoring initially focused on high volume commodity work.
Current Landscape
Presently American PCB makers target higher complexity, lower volume batches along with quick-turn prototype builds leveraging agility and engineering expertise to fulfill demanding domestic customers across life-saving, mission-critical sectors.
Though ceding market share abroad, American PCB makers continue serving key strategic needs in the global electronics ecosystem.
U.S. PCB Production Capacity and Statistics
The United States retains meaningful production capacity supporting customers across niche and broad applications:
- 100+ domestic PCB manufacturers still actively operate per industry tallies
- Their 150+ facilities span 20+ states delivering regional access
- Estimated $3 billion in annual domestic PCB production value
- Capability for boards ranging from single-sided to advanced HDI multilayer
- Annual American PCB shipments approach 100 million square feet
- Run sizes spanning prototypes to tens of thousands of boards
- Quick-turn orders in as little as 24 hours
- Serving OEMs across defense, aerospace, medical, industrial, auto/transportation, computing etc.
Though a fraction of the estimated $70 billion global PCB output, American providers meaningfully compete based on speed, engineering collaboration and supply chain security.
Reasons Why Companies Still Source USA Made Printed Circuit Boards
Procuring boards from domestic PCB manufacturers offers OEMs key advantages:
ITAR Regulatory Compliance
Many defense and aerospace OEMs must adhere to International Traffic in Arms Regulations (ITAR) concerning export controls for sensitive technologies. This restricts offshoring PCB production which could expose protected intellectual property required on custom boards. Domestic PCB partners mitigate this risk.
Intellectual Property Protection
For innovators across technology sectors seeking maximum patent protection and trade secret control of unique board fabrication techniques or embedded technologies, relying on trusted local supply chain partners ensures greater oversight compared to foreign providers.
Zero Defects Requirements
High reliability sectors like medical and transportation stipulate near-perfect quality in PCB production – often exceeding 99%+ yield rates given product integrity risks. U.S. manufacturers provide precision process controls reaching these totals.
Controlled Supply Chains
Government and highly regulated industries require full component traceability and supply chain transparency spanning approved specialty chemicals like resists or laminates through auditable waste disposal. Domestic board makers simplify compliance.
Geopolitical Conflict Hedges
Regionalized American production offers a manufacturing alternative insulating OEMs from trade wars or acts of war abroad which could cut-off foreign PCB supply flows.
Prototype Agility
Quick-turn engineering engagements to refine iterative prototypes benefit from direct designer-fabricator collaborations feasible with American PCB companies operating in similar time zones.
While cost remains a consideration, these strategic reasons justify maintaining domestic American PCB production.
Key American PCB Companies
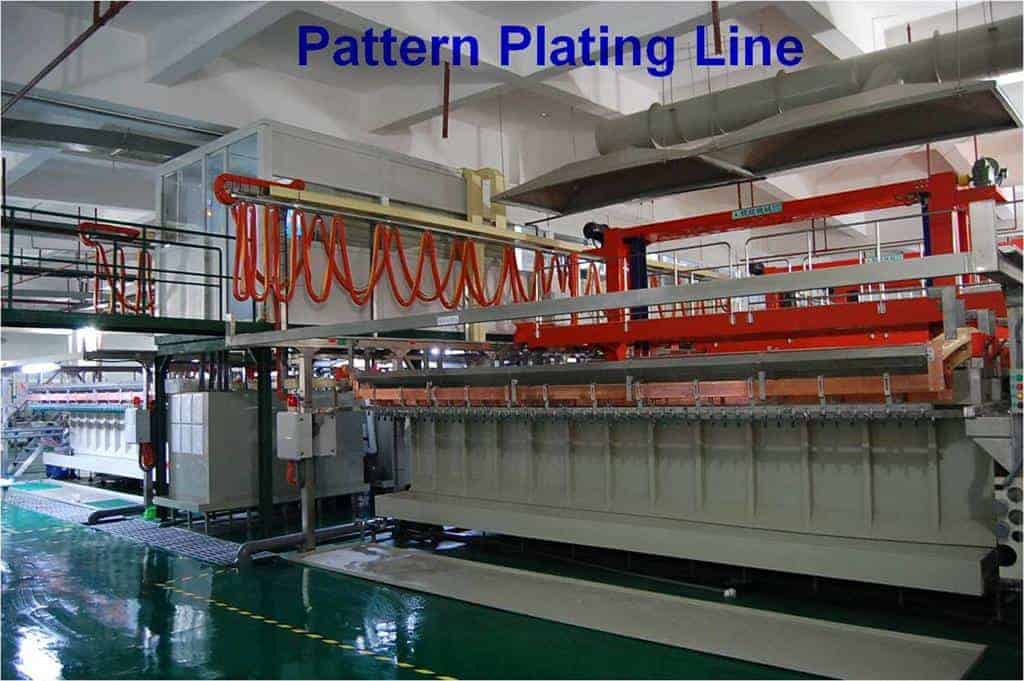
The landscape of American PCB manufacturing ranges from small specialty job shops to billion dollar printed circuit board enterprises:
Tier 3 Job Shops
Hundreds of small operations with ~$1-5 million in annual sales tend to focus on prototype engineering support, limited production run testing vehicles, and fast delivery of small volume boards for local customers.
Tier 2 Regional Manufacturers
Larger companies like Lenthor, EAG, Bettadynamics, Sunstone, Advanced Circuits, Pulse Electronics and others generate $10-100 million in annual PCB sales leveraging higher-end domestic capabilities to serve broad customer bases across diverse verticals.
Tier 1 Multinationals
Major publicly listed PCB conglomerates like TTM Technologies, Sanmina and smaller rivals manufacture defense grade circuits domestically while reserving offshore production for commercial commodity volumes price-sensitive sectors. Their U.S. facilities support customer volumes too demanding for smaller shops yet below mass production economics abroad.
Collectively domestic PCB fabricators provide scaled manufacturing aligned to priorities beyond solely cost minimization per board.
American PCB Industry Challenges
Despite advantages, multiple factors introduce struggles for U.S. PCB production sustainability:
Pricing Pressures
Larger offshore factories across Asia, able operate at slimmer margins given lower local wages, exert pricing pressure on American PCB companies struggling to compete purely on cost.
Talent Shortages
Aging engineering workforces at domestic manufacturers combine with declines in vocational trades training to drive fears of skill gaps jeopardizing quality and innovation going forward.
Raw Materials Costs
PCB substrate materials like resins and glass fabrics face supply constraints as overseas capacity dominates key steps in early stage chemical processing and weaving. Shipping finished materials stateside adds costs.
Geographic Imbalances
Many smaller U.S. PCB factories remain clustered on the coasts nearer end customers. However, inland expansion could boost production volumes by accessing lower cost regions while supporting domestic high-tech growth.
Consolidation
Smaller U.S. board shops struggle generating enough critical mass vital for large equipment investments as product mix complexity increases. This sparks ongoing mergers and acquisitions activity.
Surmounting the challenges to maintain strategic American PCB production involves proactive partnerships between policymakers, academia and commercial sector leaders.
American PCB Industry Outlook
Domestic American PCB providers remain well positioned for long term resilience – targeting more value-added niches insulated from pure cost based competition:
High Density Interconnect (HDI)
As miniaturization demands drive stacked microvia boards with thin dielectrics below 0.008”, American companies aim to lead cutting-edge production unmatched abroad.
Quick-Turn Prototypes
Rapid concept iterations with engineers benefit from direct design-fabrication interactions feasible between local contract manufacturers and customers – accelerating innovation.
Defense and Aerospace
Where certified supply chains and intellectual property control matches strict tolerances, domestic PCB shops thrive thanks to prioritization beyond solely unit economics.
Automation Investments
From inkjet solder masking to smart factory data utilization, American companies actively fund productivity enhancing modernizations compensating for higher regional wages.
Strategic Niches
Specialization in niche applications like medical monitors, satellite payloads, wireless infrastructure etc. cultivates deep expertise cementing customer loyalties across generations.
Rather than chasing race-to-the-bottom commodity board manufacturing, the domestic American PCB industry sharpens specialization on higher value segments leveraging agility and engineering partnership – ensuring locally sustained strategic capacity.
Key Trends Shaping Future American PCB Manufacturing
Several emerging developments bear monitoring as indicators of evolutions in domestic American PCB fabrication and associated supply chains:
Reshoring Incentives
In response to concerns over electronics dependency on Asia, new federal and state level manufacturing partnerships aim to spur domestic growth through subsidies, tax credits and small business grants.
Innovation Hubs
Academic engineering research around next-generation PCB materials and processing could seed regional cluster development if promising technologies reach commercialization at American incubators nearby affiliated universities.
** unpredictability Automation**
As machine learning models guide automated optical inspection and new optimization algorithms direct additive equipment installations, heightened efficiencies combat labor cost gaps at American factories.
Sustainability Priorities
Emphasis on environmental metrics guides materials science and chemistry innovations in domestic PCB manufacturing aligned with growing corporate ESG initiative demands from OEMs.
Supply Chain Security
Geopolitics and trade volatility incentivize regionalized redundancy for key strategic American industry supply continuity, secured via partnerships with local PCB fabricators.
Ongoing American PCB manufacturing retention relies on cultivating differentiating capabilities warranting premiums, policymaker collaboration to nurture innovation, and supply chain resilience efforts.
Examples of Innovative American PCB Companies
Notable disruptive domestic PCB manufacturers driving American industry advancements include:
Ascentech
Specializes in embedded electronics integrations allowing customers late stage customization of commercial assemblies for defense systems, optimizing inventory costs.
Saline Lectronics
Its “Super Speed” service reflows solder paste PCB in under 60 seconds, expediting prototyping iterations by hours compared to traditional SMT machinery.
Tempo Automation
Leverages software built atop ML/AI-based platforms encompassing design-rule checking through automated optical inspection able to adapt across small to medium scale volumes.
American Semiconductor
Seeks reinventing semiconductor fabrication via modular equipment and process innovations enabling affordable domestic 200mm wafer production at old plants.
Rogers Corporation
Develops cutting edge high frequency and power integrity materials research used globally in next-generation wireless and radar PCB designs, maintaining American leadership.
By pursuing capabilities differentiation, such innovators secure value-added market roles ensuring ongoing domestic PCB survivability.
Notable American Electronics Companies Relying on Domestic PCBs
Major American electronics brands across aerospace, telecom, medical, defense, transportation and other sectors proudly maintain production partnerships with domestic PCB manufacturers:
BAE Systems Dependence on export control compliance and intellectual property confidentiality drives utilization of secure American PCB fabs for sensitive defense electronics.
John Deere Mission-critical agricultural equipment avoids offshore supply chain risks or geo-political conflicts that could hamper harvests by sourcing boards locally.
Keysight Technologies
Cutting edge R&D oscilloscopes, microwave radio and cell network analyzers demand tightly integrated engineering support feasible with American PCB partners.
Medtronic Life-dependent medical devices necessitate flawless quality only ensured via direct process oversight at closely located American PCB shops.
Garmin Airline cockpits to outdoor GPS systems require extreme reliability, prioritizing American PCB maker relations able to meet stringent standards.
Rather than abandon domestic PCB infrastructure, such prominent brands selectively leverage American manufacturing for securing product advantages and supply chain resilience.
Frequently Asked Questions
How do American PCB manufacturers stay cost competitive?
Domestic PCB shops offset higher regional wages through tactics like:
- Specialization in complex boards bearing price premiums
- Investments raising automation and machine utilization
- Value engineering optimizing designs for efficient production
- Selective adoption of HDI and advanced packaging raising functionality per area
- Leveraging quick-turn and engineering support services
- Prioritizing quality for yielding higher first-pass ratios
- Taking equity stakes in startups eventual requiring scaled domestic production
What key American PCB industry trade groups exist?
Major U.S. printed circuit board industry associations include:
- IPC – Association Connecting Electronics Industries
- TPCA – Taiwan Printed Circuit Association
- JPCA – Japan Electronics Packaging and Circuits Association
These groups lobby governments, organize North American trade shows, publish industry research, and help members adopt technology or business best practices.
Are military printed circuit boards manufactured in the USA?
Yes, stringent U.S. defense electronics requirements covering integrity, ITAR regulatory compliance and intellectual property confidentiality means military systems primes commonly require American PCB production partners. Vital weapons and platform sellers serving Pentagon needs like Raytheon, Lockheed Martin, Northrop Grumman and General Dynamics all utilize secure domestic PCB supply chains. Similarly strict aviation electronics needs mean aerospace OEMs like Boeing, Honeywell and Garmin availability leverage American PCB makers heavily.
0 Comments