Introduction to PCB Wiring
Printed Circuit Board (PCB) wiring is the process of connecting various electronic components on a PCB using conductive traces, pads, and other features. Proper PCB wiring is essential for ensuring the functionality, reliability, and durability of electronic devices. In this article, we will discuss the tips and essentials for PCB wiring, covering topics such as wire selection, wire routing, soldering techniques, and testing methods.
Importance of PCB Wiring
PCB wiring plays a crucial role in the performance and longevity of electronic devices. Here are some reasons why PCB wiring is important:
-
Signal Integrity: Proper PCB wiring ensures that electrical signals are transmitted efficiently and accurately between components, minimizing signal loss, noise, and interference.
-
Reliability: Well-executed PCB wiring reduces the risk of short circuits, open circuits, and other wiring-related issues that can lead to device failure or malfunction.
-
Durability: Robust PCB wiring techniques, such as using appropriate wire gauges and secure connections, contribute to the overall durability of the electronic device, making it resistant to physical stresses and environmental factors.
-
Manufacturability: Efficient PCB wiring layouts and techniques facilitate the manufacturing process, reducing production time and costs while improving the overall quality of the end product.
Wire Selection for PCB Wiring
Choosing the right wires for PCB wiring is essential for ensuring optimal performance and reliability. Here are some factors to consider when selecting wires:
Wire Gauge
The wire gauge refers to the thickness of the wire’s conductive core. Thicker wires (lower gauge numbers) have lower resistance and can carry more current, while thinner wires (higher gauge numbers) are more suitable for low-current applications. Common wire gauges used in PCB wiring include:
Wire Gauge | Diameter (mm) | Current Rating (A) |
---|---|---|
22 AWG | 0.64 | 7 |
24 AWG | 0.51 | 5 |
26 AWG | 0.40 | 3.5 |
28 AWG | 0.32 | 2.5 |
Insulation Material
The insulation material surrounding the conductive core provides electrical isolation and protection. Common insulation materials include:
- PVC (Polyvinyl Chloride): Affordable and widely used, but less resistant to high temperatures.
- Teflon (PTFE): Excellent heat resistance and chemical stability, but more expensive.
- Silicone: Flexible, heat-resistant, and suitable for high-temperature applications.
Stranded vs. Solid Core
Wires can have either stranded or solid conductive cores:
- Stranded wires consist of multiple thin conductive strands twisted together, providing flexibility and resistance to vibration.
- Solid core wires have a single, solid conductive core and are less flexible but offer better electrical conductivity.
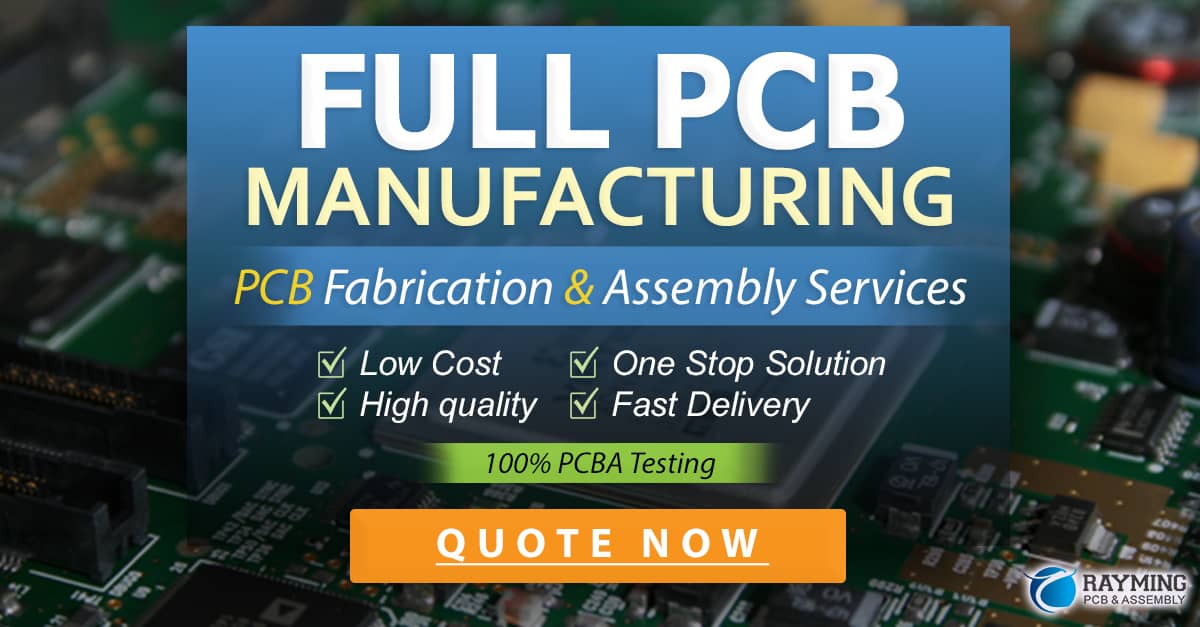
Wire Routing Techniques
Proper wire routing is crucial for maintaining signal integrity, reducing crosstalk, and minimizing electromagnetic interference (EMI). Here are some wire routing techniques to follow:
Keep Wires Short
Minimize the length of wires whenever possible to reduce resistance, signal loss, and noise pickup. Shorter wires also contribute to better signal integrity and lower EMI.
Avoid Right-Angle Turns
Right-angle turns in wire routing can cause signal reflections and increase EMI. Instead, use 45-degree angles or curved traces to smooth out the wire paths.
Maintain Adequate Spacing
Ensure sufficient spacing between wires to minimize crosstalk and reduce the risk of short circuits. The spacing depends on factors such as wire gauge, signal frequency, and voltage levels.
Use Ground Planes
Incorporate ground planes in the PCB design to provide a low-impedance return path for signals and shield against EMI. Ground planes also help maintain signal integrity and reduce crosstalk.
Route Sensitive Signals Carefully
Pay special attention to routing sensitive signals, such as high-speed signals, analog signals, and power lines. Keep them away from potential sources of interference, such as digital circuits or switching power supplies.
Soldering Techniques
Soldering is the process of joining wires and components to the PCB using a conductive metal alloy called solder. Proper soldering techniques ensure strong and reliable connections. Here are some tips for soldering:
Choose the Right Solder
Use solder with the appropriate melting temperature and composition for your specific application. Common solder types include:
- Lead-based solder (e.g., 63/37 tin-lead): Lower melting point and easier to work with, but less environmentally friendly.
- Lead-free solder (e.g., SAC305): Higher melting point and more environmentally friendly, but requires more precise temperature control.
Use Flux
Apply flux to the soldering area to remove oxidation, improve solder flow, and promote a stronger bond between the wire and the PCB pad. Flux can be applied separately or as part of the solder wire (flux-cored solder).
Control Soldering Temperature
Use a temperature-controlled soldering iron with the appropriate tip size for the job. The ideal soldering temperature depends on the solder type and the components being soldered. Typically, temperatures between 300°C and 400°C are used.
Create a Good Solder Joint
A good solder joint should be shiny, smooth, and concave in shape. It should completely cover the wire and the PCB pad, forming a strong mechanical and electrical connection. Avoid cold solder joints, which appear dull and lumpy, as they can lead to poor connections and reliability issues.
Testing and Inspection
After completing the PCB wiring, it is essential to test and inspect the connections to ensure proper functionality and reliability. Here are some testing and inspection methods:
Visual Inspection
Perform a visual inspection of the PCB wiring using a magnifying glass or microscope. Look for any signs of poor soldering, such as cold solder joints, excessive solder, or bridged connections.
Continuity Testing
Use a multimeter to test the continuity between the wires and the PCB pads. Ensure that there are no open circuits or short circuits in the wiring.
Insulation Resistance Testing
Measure the insulation resistance between wires and between wires and ground using a high-voltage insulation tester (megohmmeter). This test helps detect any insulation defects or leakage currents.
Functional Testing
Perform functional tests on the assembled PCB to verify that all components and circuits are working as intended. This may involve applying power, testing inputs and outputs, and measuring signal levels.
Frequently Asked Questions (FAQ)
1. What is the difference between through-hole and surface-mount PCB wiring?
Through-hole PCB wiring involves inserting component leads through drilled holes in the PCB and soldering them on the opposite side. Surface-mount PCB wiring, on the other hand, involves soldering components directly onto the surface of the PCB without using drilled holes. Surface-mount wiring allows for smaller components and higher component density, while through-hole wiring offers stronger mechanical connections.
2. Can I mix different wire gauges in the same PCB?
While it is possible to use different wire gauges in the same PCB, it is generally recommended to use consistent wire gauges for similar signal types or power requirements. Mixing wire gauges can lead to uneven current distribution, signal integrity issues, and difficulties in soldering and wire management.
3. How do I choose the right soldering iron tip size?
The soldering iron tip size should match the size of the components and wires being soldered. For smaller components and fine-pitch soldering, use a smaller tip (e.g., 0.5mm to 1mm). For larger components and wires, use a larger tip (e.g., 2mm to 3mm). Using the appropriate tip size ensures efficient heat transfer and precise soldering control.
4. What is the purpose of using a conformal coating on PCBs?
Conformal coating is a protective layer applied to PCBs to shield them from environmental factors such as moisture, dust, and chemical contaminants. It helps improve the durability and reliability of the PCB by preventing corrosion, leakage currents, and short circuits caused by environmental exposure.
5. How can I prevent electrostatic discharge (ESD) damage during PCB wiring?
To prevent ESD damage, follow these tips:
– Use an ESD-safe workstation with grounded mats and wrist straps.
– Wear ESD-protective clothing and footwear.
– Handle components and PCBs by their edges, avoiding direct contact with pins or pads.
– Store components and PCBs in ESD-safe packaging when not in use.
– Use ESD-safe soldering irons and tools.
Conclusion
PCB wiring is a critical aspect of electronic device design and manufacturing. By following the tips and essentials discussed in this article, you can ensure that your PCB wiring is reliable, durable, and performs optimally. Remember to choose the right wires, follow proper routing techniques, use appropriate soldering methods, and thoroughly test and inspect your work. With these best practices in mind, you can create high-quality PCBs that meet the demands of your electronic projects.
0 Comments