What is Solder Wicking?
Solder wicking, also known as capillary action, is a phenomenon that occurs when molten solder is drawn up into the small spaces between connector leads or component pins during the soldering process. This effect is caused by the surface tension of the liquid solder and the attractive forces between the solder and the metal surfaces it comes in contact with.
The Science Behind Solder Wicking
The primary force responsible for solder wicking is capillary action. Capillary action is the ability of a liquid to flow in narrow spaces without the assistance of, or even in opposition to, external forces like gravity. This occurs because of the intermolecular forces between the liquid and the surrounding solid surfaces.
In the case of solder wicking, the molten solder is attracted to the metal surfaces of the connector leads or component pins. The small gaps between these surfaces act as capillaries, drawing the solder upwards. The extent of solder wicking depends on several factors, including:
- The surface tension of the molten solder
- The wettability of the metal surfaces
- The size of the gaps between the surfaces
- The temperature of the solder and the surrounding environment
Benefits of Solder Wicking
When controlled properly, solder wicking can be beneficial in electronic assembly. Some of the advantages include:
-
Improved mechanical strength: Solder wicking helps to create a stronger mechanical bond between the connector leads and the solder. This is because the solder fills the gaps between the surfaces, creating a larger contact area and a more robust connection.
-
Better electrical conductivity: As the solder wicks up the connector leads, it creates a continuous electrical path. This can help to reduce resistance and improve the overall conductivity of the connection.
-
Increased reliability: A well-formed solder joint with proper wicking can be more reliable than one without. The increased mechanical strength and improved electrical conductivity contribute to a connection that is less likely to fail over time.
Challenges Associated with Solder Wicking
While solder wicking can be beneficial, it can also present some challenges in electronic assembly. Some of the potential issues include:
-
Excess solder buildup: If too much solder is applied or if the solder is allowed to wick too far up the connector leads, it can result in excess solder buildup. This can create a risk of short circuits or other electrical issues.
-
Difficulty in controlling the amount of wicking: Controlling the exact amount of solder wicking can be challenging. Factors such as the temperature of the soldering iron, the amount of solder applied, and the duration of the soldering process can all affect the extent of wicking.
-
Aesthetic concerns: In some cases, visible solder wicking may be considered aesthetically undesirable. This is particularly true in consumer electronics where the appearance of the product is important.
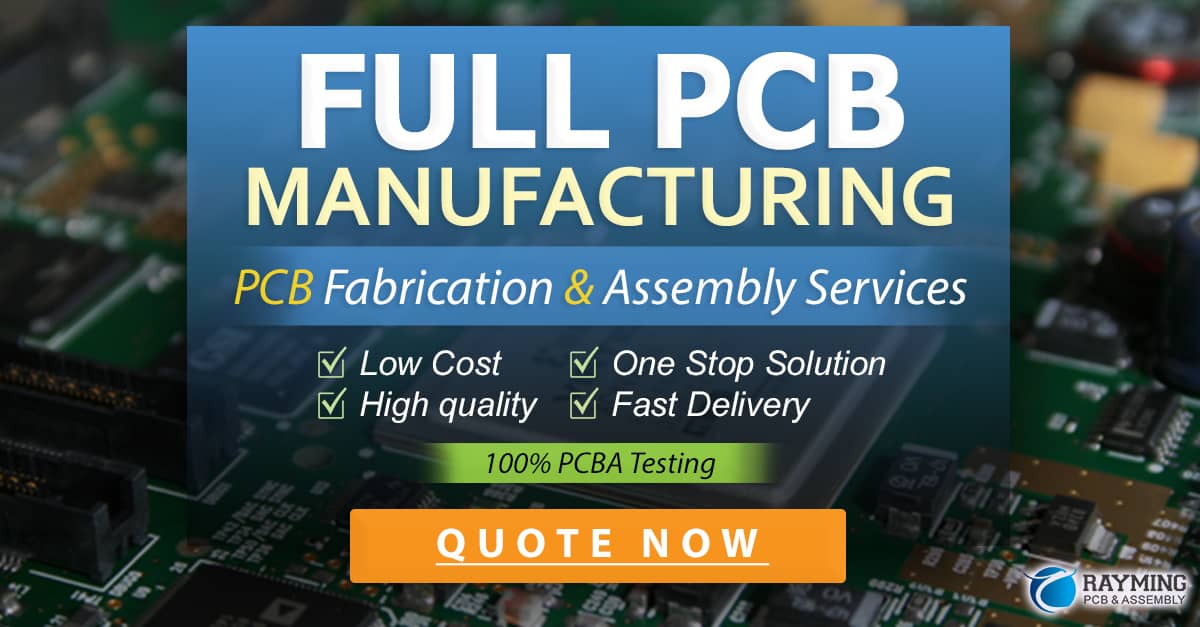
Techniques for Controlling Solder Wicking
There are several techniques that can be used to control solder wicking and mitigate the potential challenges:
-
Proper soldering technique: Using the correct soldering technique is essential for controlling solder wicking. This includes applying the right amount of solder, using the appropriate soldering iron temperature, and maintaining the right duration of contact between the iron and the joint.
-
Use of solder masks: Solder masks are coatings that are applied to the PCB to prevent solder from adhering to certain areas. By strategically applying solder masks, you can limit the areas where solder wicking can occur.
-
Selection of appropriate solder and flux: The type of solder and flux used can also affect solder wicking. Some solder alloys and flux formulations are designed to minimize wicking, while others may promote it. Selecting the right materials for the job can help to control wicking.
-
Design considerations: The design of the PCB and the components can also play a role in controlling solder wicking. For example, using connectors with longer lead lengths can provide more space for solder to wick without causing problems. Similarly, ensuring adequate spacing between leads can help to prevent short circuits caused by excess wicking.
Technique | Description | Advantages | Disadvantages |
---|---|---|---|
Proper soldering technique | Using correct amount of solder, temperature, and duration | Helps to control wicking without additional steps | Requires skill and experience |
Use of solder masks | Coatings applied to PCB to prevent solder adhesion in certain areas | Can effectively limit areas of wicking | Adds an additional step to the PCB manufacturing process |
Selection of appropriate solder and flux | Choosing solder alloys and flux formulations that minimize wicking | Can reduce wicking without changes to the process | May require experimentation to find the right materials |
Design considerations | Designing PCB and components to accommodate wicking | Can prevent problems without changing the soldering process | May not always be feasible due to other design constraints |
FAQ
-
Q: Is solder wicking always a problem?
A: No, solder wicking is not always a problem. In fact, when controlled properly, it can be beneficial by improving the mechanical strength and electrical conductivity of the solder joint. However, excessive or uncontrolled wicking can lead to issues like short circuits or aesthetic concerns. -
Q: How does the choice of solder affect wicking?
A: The composition of the solder alloy can affect its surface tension and wetting properties, which in turn influence its tendency to wick. Some solder alloys are formulated to minimize wicking, while others may promote it. The flux used with the solder can also play a role, as some flux formulations are designed to enhance or restrict wicking. -
Q: Can solder wicking be completely eliminated?
A: While it may not be possible to completely eliminate solder wicking, it can be effectively controlled and minimized. Using proper soldering techniques, solder masks, appropriate solder and flux selection, and design considerations can all help to manage wicking and prevent it from causing problems in the final assembly. -
Q: What role does temperature play in solder wicking?
A: Temperature plays a significant role in solder wicking. At higher temperatures, the solder becomes more fluid and its surface tension decreases, which can promote wicking. Conversely, at lower temperatures, the solder is less fluid and may not wick as readily. Controlling the temperature of the soldering iron and the duration of contact can help to manage the extent of wicking. -
Q: Are there any industry standards related to solder wicking?
A: While there are no specific industry standards that directly address solder wicking, there are standards related to soldering and PCB assembly that can influence wicking. For example, IPC standards like IPC-A-610 and IPC J-STD-001 provide guidelines for acceptable solder joint formation, which can include considerations for solder wicking. Additionally, standards for PCB design, such as IPC-2221, can include recommendations for pad sizes and spacing that can impact wicking.
Conclusion
Solder wicking is a complex phenomenon that can have both positive and negative impacts on electronic assemblies. By understanding the science behind wicking and the factors that influence it, engineers and technicians can take steps to control and manage its effects. Through the use of proper soldering techniques, solder masks, appropriate materials selection, and design considerations, solder wicking can be harnessed to create stronger, more reliable solder joints while minimizing the risk of defects or failures.
As the electronics industry continues to evolve, with ever-increasing demands for miniaturization and performance, the importance of understanding and controlling solder wicking will only continue to grow. By staying informed about the latest techniques and best practices, professionals in the field can ensure that their assemblies are built to the highest standards of quality and reliability.
0 Comments