Introduction to Wave Soldering and PTH Components
Wave soldering is a widely used technique for soldering through-hole (PTH) components onto printed circuit boards (PCBs). This process involves passing the PCB over a molten solder wave, which creates a reliable electrical and mechanical connection between the components and the board. PTH components, such as resistors, capacitors, and connectors, have leads that pass through holes in the PCB and are soldered on the opposite side.
Advantages of Wave Soldering for PTH Components
Wave soldering offers several advantages for assembling PCBs with PTH components:
- High throughput: Wave soldering is a fast and efficient process, allowing for the soldering of multiple components simultaneously.
- Consistent quality: With proper process control, wave soldering ensures consistent solder joint quality across the entire PCB.
- Cost-effective: Wave soldering is an economical choice for high-volume production runs, as it minimizes manual labor and reduces the risk of errors.
The Wave Soldering Process
Preparing the PCB for Wave Soldering
Before the wave soldering process begins, the PCB must be properly prepared:
- PCB design: Ensure that the PCB is designed with appropriate hole sizes, pad sizes, and component spacing to accommodate wave soldering.
- Solder mask application: Apply a solder mask to the PCB to prevent solder bridging and protect the board from oxidation.
- Flux application: Apply flux to the bottom side of the PCB to remove oxidation, improve solder wettability, and enhance solder joint quality.
The Wave Soldering Machine
A typical wave soldering machine consists of the following components:
- Conveyor system: Transports the PCB through the various stages of the wave soldering process.
- Fluxer: Applies flux to the bottom side of the PCB.
- Preheater: Gradually heats the PCB to activate the flux and minimize thermal shock during soldering.
- Solder pot: Contains the molten solder, which is pumped to create the solder wave.
- Solder wave: The molten solder is forced upward through a nozzle to create a standing wave that contacts the bottom side of the PCB.
- Cooling zone: Allows the soldered PCB to cool gradually, preventing thermal stress and ensuring proper solder joint formation.
Wave Soldering Process Parameters
To achieve optimal results, several process parameters must be carefully controlled:
- Solder temperature: Typically between 240°C and 260°C (464°F to 500°F), depending on the solder alloy used.
- Conveyor speed: Determines the dwell time of the PCB in contact with the solder wave, typically ranging from 0.5 to 2 meters per minute (1.6 to 6.6 feet per minute).
- Preheat temperature: Usually between 100°C and 150°C (212°F to 302°F), depending on the PCB and component characteristics.
- Solder wave height: Typically 1/2 to 2/3 of the PCB thickness to ensure proper solder penetration and minimize bridging.
Solder Alloys for Wave Soldering
The most common solder alloys used in wave soldering are tin-lead (SnPb) and lead-free alloys, such as tin-silver-copper (SAC).
Tin-Lead Solder Alloys
Traditionally, tin-lead solder alloys, such as Sn63Pb37 (63% tin, 37% lead), were widely used in wave soldering due to their low melting point, good wetting properties, and reliable performance. However, due to environmental and health concerns, the use of lead in electronics has been restricted by various regulations, such as the European Union’s Restriction of Hazardous Substances (RoHS) directive.
Lead-Free Solder Alloys
Lead-free solder alloys, such as SAC305 (96.5% tin, 3% silver, 0.5% copper), have become the standard for wave soldering in RoHS-compliant manufacturing. These alloys have higher melting points compared to tin-lead alloys, requiring adjustments to the wave soldering process parameters.
Solder Alloy | Composition | Melting Point | Common Applications |
---|---|---|---|
Sn63Pb37 | 63% Sn, 37% Pb | 183°C (361°F) | Non-RoHS compliant electronics |
SAC305 | 96.5% Sn, 3% Ag, 0.5% Cu | 217-220°C (423-428°F) | RoHS-compliant electronics |
SN100C | 99.3% Sn, 0.7% Cu, 0.05% Ni | 227°C (441°F) | RoHS-compliant electronics |
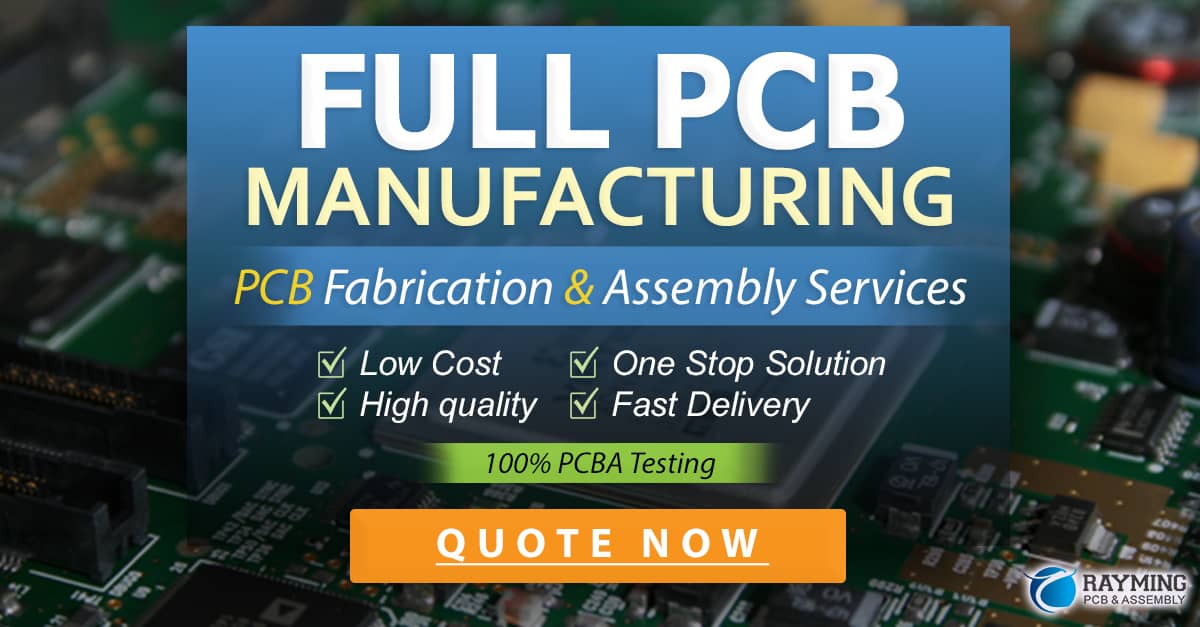
Defects in Wave Soldered PTH Components
Despite the advantages of wave soldering, several defects can occur during the process:
- Solder bridges: Unwanted solder connections between adjacent pads or pins, often caused by excessive solder, incorrect wave height, or poor PCB design.
- Insufficient solder: Incomplete solder joints resulting from inadequate solder penetration, low solder temperature, or poor wetting.
- Solder balls: Small spheres of solder that adhere to the PCB or components, often caused by excessive flux or turbulent solder flow.
- Tombstoning: When a component stands on one end due to uneven heating or surface tension, causing one lead to lift off the pad.
To minimize these defects, it is essential to optimize the wave soldering process parameters, maintain proper PCB design, and ensure consistent material quality.
Inspection and Quality Control
After the wave soldering process, it is crucial to inspect the soldered PCBs to ensure the quality of the solder joints and identify any defects.
Visual Inspection
Visual inspection is the first line of defense in detecting soldering defects. Trained operators use magnification and lighting to examine the solder joints for visible defects, such as bridges, insufficients, and solder balls.
Automated Optical Inspection (AOI)
AOI systems use high-resolution cameras and advanced image processing algorithms to detect and classify solder joint defects automatically. These systems can quickly inspect large numbers of PCBs and provide consistent, objective results.
X-Ray Inspection
For more complex PCBs with hidden or obscured solder joints, X-ray inspection may be necessary. X-ray systems allow for the visualization of solder joints through the components and PCB, enabling the detection of internal defects, such as voids or cracks.
Troubleshooting Wave Soldering Issues
When encountering wave soldering issues, a systematic approach to troubleshooting can help identify the root cause and implement corrective actions.
- Identify the defect: Clearly define the type and location of the defect, such as bridges, insufficients, or solder balls.
- Analyze the process parameters: Review the wave soldering machine settings, including solder temperature, conveyor speed, preheat temperature, and wave height.
- Check the materials: Ensure that the solder alloy, flux, and PCB materials are of the correct specification and quality.
- Examine the PCB design: Verify that the PCB design adheres to wave soldering guidelines, including hole sizes, pad sizes, and component spacing.
- Implement corrective actions: Based on the findings, make necessary adjustments to the process parameters, materials, or PCB design to resolve the issue.
- Monitor and document: Continuously monitor the wave soldering process and document any changes or improvements for future reference.
Frequently Asked Questions (FAQ)
-
Q: What is the difference between wave soldering and reflow soldering?
A: Wave soldering is used for soldering PTH components, where the leads pass through holes in the PCB. Reflow soldering, on the other hand, is used for surface mount (SMT) components, where the components are placed on pads on the surface of the PCB and soldered using a reflow oven. -
Q: Can wave soldering be used for SMT components?
A: While wave soldering is primarily used for PTH components, it can be used for some SMT components with proper fixturing and process control. However, reflow soldering is generally preferred for SMT components due to its superior control and reliability. -
Q: What is the purpose of applying flux in wave soldering?
A: Flux serves several purposes in wave soldering: it removes oxidation from the metal surfaces, improves solder wettability, and enhances solder joint quality by promoting even solder flow and reducing defects. -
Q: How can I minimize solder bridging in wave soldering?
A: To minimize solder bridging, ensure proper PCB design with adequate spacing between pads and pins, maintain the correct solder wave height, and optimize the conveyor speed to control the dwell time in the solder wave. Additionally, using a nitrogen atmosphere can help reduce bridging by limiting solder oxidation. -
Q: What are the environmental and health concerns associated with lead-based solder alloys?
A: Lead is a toxic substance that can cause serious health issues if ingested or inhaled. When lead-based solder alloys are used in electronics, there is a risk of lead leaching into the environment during the product’s lifecycle, especially during disposal. To address these concerns, many countries have implemented regulations, such as the RoHS directive, to restrict the use of lead in electronics manufacturing.
Conclusion
Wave soldering is a critical process in the assembly of PCBs with PTH components, offering high throughput, consistent quality, and cost-effectiveness. By understanding the principles of wave soldering, optimizing process parameters, and implementing proper inspection and troubleshooting techniques, manufacturers can achieve reliable and high-quality solder joints. As environmental and health concerns drive the transition to lead-free solder alloys, it is essential for manufacturers to adapt their processes and materials accordingly to ensure compliance and maintain product performance.
0 Comments