Introduction to PCB and 94V 0 Circuit Boards
Printed Circuit Boards (PCBs) are the backbone of modern electronics. They are used in almost every electronic device, from smartphones and laptops to industrial machinery and medical equipment. PCBs are designed to mechanically support and electrically connect electronic components using conductive pathways, traces, or signal traces etched from copper sheets laminated onto a non-conductive substrate.
One important aspect of PCBs is their flammability rating. The 94V 0 rating is a common standard for PCBs used in consumer electronics and other applications where fire safety is a concern. In this article, we’ll dive deep into the world of 94V 0 circuit boards, exploring what they are, how they’re made, and why they’re so important in the electronics industry.
What is the UL 94 Standard?
The UL 94 standard is a safety standard developed by Underwriters Laboratories (UL), an independent global safety certification company. The standard sets requirements for the flammability of plastic materials used in devices and appliances. It consists of several tests that measure a material’s ability to withstand exposure to a flame or high-temperature source.
The UL 94 standard includes several ratings, each with specific requirements:
Rating | Description |
---|---|
94HB | Slow burning on a horizontal specimen; burning rate < 76 mm/min for thickness < 3 mm or burning stops before 100 mm |
94V-2 | Burning stops within 30 seconds on a vertical specimen; drips of flaming particles allowed |
94V-1 | Burning stops within 30 seconds on a vertical specimen; no drips allowed |
94V-0 | Burning stops within 10 seconds on a vertical specimen; no drips allowed |
94-5VA | Burning stops within 60 seconds on a vertical specimen; no drips allowed; plaque specimens may develop a hole |
94-5VB | Burning stops within 60 seconds on a vertical specimen; no drips allowed; plaque specimens may not develop a hole |
The 94V 0 rating is one of the most stringent ratings, requiring that the material self-extinguish within 10 seconds and not produce any flaming drips.
What Makes a 94V 0 Circuit Board Special?
A 94V 0 circuit board is made from materials that have been tested and certified to meet the UL 94V-0 flammability rating. This means that the PCB substrate and any other materials used in the board’s construction have been designed to resist ignition and quickly self-extinguish if exposed to a flame.
The main benefits of using a 94V 0 circuit board include:
-
Enhanced safety: The flame-resistant properties of 94V 0 PCBs help prevent the spread of fire in electronic devices, reducing the risk of harm to users and property damage.
-
Compliance with regulations: Many industries, such as aerospace, automotive, and medical, have strict regulations regarding the fire safety of electronic components. Using 94V 0 PCBs ensures compliance with these regulations.
-
Improved reliability: The high-quality materials used in 94V 0 PCBs not only provide fire resistance but also contribute to the overall reliability and durability of the board.
Common Materials Used in 94V 0 PCBs
Several materials can be used to manufacture 94V 0 PCBs, each with its own unique properties and advantages. Some of the most common materials include:
-
FR-4: FR-4 is a glass-reinforced epoxy laminate and is the most widely used material for PCBs. It offers excellent electrical insulation, mechanical strength, and thermal stability. FR-4 is available in various grades, with some specifically designed to meet the UL 94V-0 rating.
-
Polyimide: Polyimide is a high-performance polymer known for its exceptional heat resistance, mechanical strength, and dimensional stability. It is often used in applications that require exposure to high temperatures or harsh environments.
-
CEM-1: CEM-1 is a composite material made from woven glass fabric and epoxy resin. It offers good electrical properties and mechanical strength at a lower cost compared to FR-4.
-
PTFE (Teflon): PTFE is a fluoropolymer with excellent dielectric properties, low friction, and high temperature resistance. It is often used in high-frequency applications, such as RF and microwave circuits.
Manufacturing Process of 94V 0 PCBs
The manufacturing process for 94V 0 PCBs is similar to that of other PCBs, with a few additional steps to ensure the board meets the required flammability rating. The general steps involved in the manufacturing process are:
-
Design and Layout: The PCB design is created using specialized software, taking into account the required components, connections, and any special requirements, such as controlled impedance or high voltage clearance.
-
Material Selection: The appropriate 94V 0 rated materials are selected based on the specific application and design requirements.
-
Lamination: The selected materials are laminated together under high pressure and temperature to form a solid board.
-
Drilling: Holes are drilled through the board to accommodate through-hole components and vias.
-
Plating: Copper is plated onto the board and inside the drilled holes to create conductive pathways.
-
Etching: The unwanted copper is removed using a chemical etching process, leaving only the desired conductive traces.
-
Solder Mask Application: A protective solder mask is applied to the board to insulate the copper traces and prevent short circuits.
-
Silkscreen: A silkscreen layer is added to the board to provide labels, logos, and other markings.
-
Surface Finish: A surface finish, such as HASL (Hot Air Solder Leveling), ENIG (Electroless Nickel Immersion Gold), or OSP (Organic Solderability Preservative), is applied to protect the exposed copper and improve solderability.
-
Testing: The completed board undergoes various tests, including electrical continuity, insulation resistance, and flammability testing, to ensure it meets the required specifications and standards.
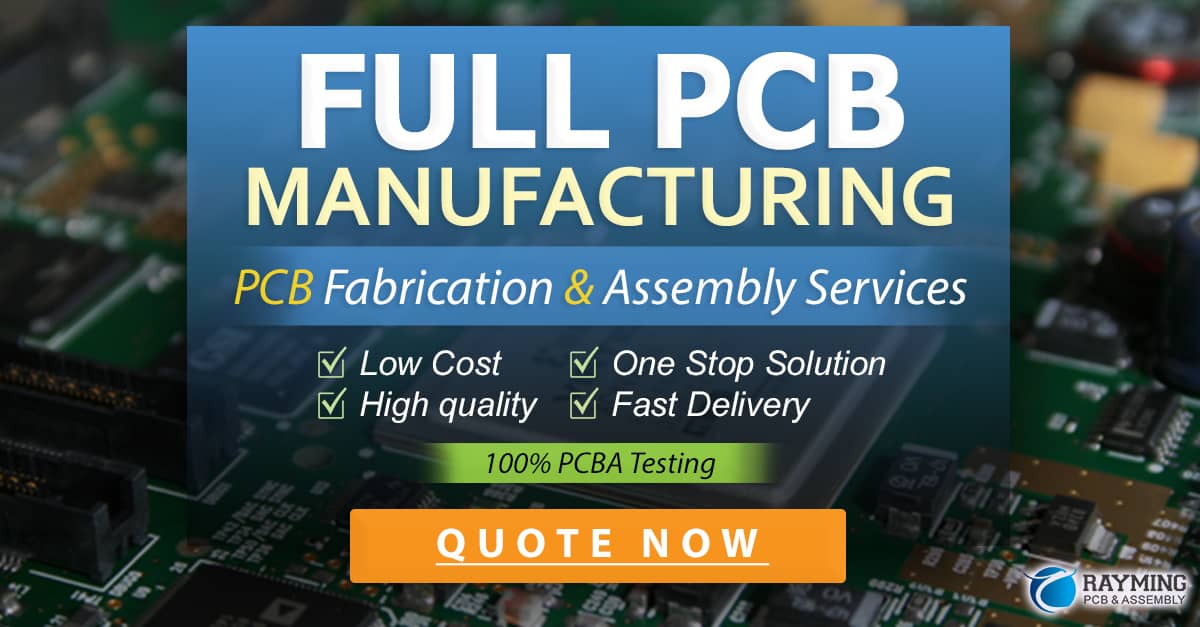
Applications of 94V 0 PCBs
94V 0 PCBs are used in a wide range of applications where fire safety is a critical concern. Some of the most common applications include:
-
Consumer Electronics: Many consumer electronic devices, such as televisions, computers, and home appliances, use 94V 0 PCBs to reduce the risk of fire and ensure compliance with safety regulations.
-
Automotive Electronics: The automotive industry heavily relies on 94V 0 PCBs for various electronic systems, such as engine control units, infotainment systems, and advanced driver assistance systems (ADAS).
-
Medical Devices: Medical equipment, such as patient monitors, imaging systems, and surgical instruments, often require 94V 0 PCBs to ensure patient safety and meet strict regulatory requirements.
-
Aerospace and Defense: The aerospace and defense industries use 94V 0 PCBs in a variety of applications, including avionics, communication systems, and weaponry, where reliability and fire safety are paramount.
-
Industrial Control Systems: Industrial control systems, such as programmable logic controllers (PLCs) and human-machine interfaces (HMIs), often use 94V 0 PCBs to ensure reliable operation in harsh environments.
Advantages of Using 94V 0 PCBs
Using 94V 0 PCBs offers several advantages over non-rated or lower-rated PCBs:
-
Enhanced Safety: The primary advantage of 94V 0 PCBs is their enhanced fire safety. The flame-resistant properties of these boards help prevent the spread of fire in electronic devices, reducing the risk of harm to users and property damage.
-
Regulatory Compliance: Many industries have strict regulations regarding the fire safety of electronic components. Using 94V 0 PCBs ensures compliance with these regulations, avoiding potential fines or legal issues.
-
Improved Reliability: The high-quality materials used in 94V 0 PCBs not only provide fire resistance but also contribute to the overall reliability and durability of the board. This improved reliability can lead to reduced maintenance costs and longer product life spans.
-
Versatility: 94V 0 PCBs can be manufactured using a variety of materials and processes, allowing designers to choose the best option for their specific application. This versatility enables the use of 94V 0 PCBs in a wide range of industries and applications.
-
Peace of Mind: By using 94V 0 PCBs, manufacturers and consumers can have peace of mind knowing that their electronic devices are built with safety in mind, reducing the risk of fire-related incidents.
Challenges and Considerations
While 94V 0 PCBs offer numerous benefits, there are some challenges and considerations to keep in mind:
-
Higher Cost: The materials and additional testing required for 94V 0 PCBs can result in higher production costs compared to non-rated or lower-rated PCBs. However, the added safety and reliability benefits often justify the increased cost.
-
Design Constraints: The use of flame-resistant materials may impose certain design constraints, such as minimum hole sizes or trace widths. Designers must take these constraints into account when creating the PCB layout.
-
Material Availability: Some specialized 94V 0 rated materials may have limited availability or longer lead times, which can impact production schedules. It’s essential to plan accordingly and work closely with PCB Manufacturers to ensure timely delivery.
-
Environmental Concerns: Some flame-retardant materials used in 94V 0 PCBs may have environmental concerns, such as the use of halogenated compounds. Designers and manufacturers should stay informed about evolving environmental regulations and consider using eco-friendly alternatives when possible.
Future Trends in 94V 0 PCBs
As technology advances and new materials are developed, the future of 94V 0 PCBs looks promising. Some of the trends and developments to watch include:
-
Eco-Friendly Materials: There is a growing demand for eco-friendly flame-retardant materials that minimize the use of harmful substances. Researchers are developing new compounds and resins that provide excellent fire resistance while reducing environmental impact.
-
Advanced Manufacturing Techniques: Advancements in PCB manufacturing, such as 3D printing and embedded components, are enabling the creation of more complex and compact 94V 0 PCBs. These techniques can help reduce costs and improve performance in certain applications.
-
High-Speed and High-Frequency Applications: As electronic devices continue to push the boundaries of speed and frequency, there will be an increasing need for 94V 0 PCBs that can handle these demands. New materials and manufacturing processes are being developed to address these challenges.
-
Increased Adoption in Emerging Industries: As new industries, such as renewable energy, electric vehicles, and the Internet of Things (IoT), continue to grow, the demand for 94V 0 PCBs is expected to rise. These industries often require high levels of safety and reliability, making 94V 0 PCBs an essential component in their electronic systems.
FAQ
-
What is the difference between UL 94V-0 and UL 94V-1?
UL 94V-0 and UL 94V-1 are both flammability ratings for plastic materials, but they have different requirements. UL 94V-0 requires that the material self-extinguish within 10 seconds and not produce any flaming drips, while UL 94V-1 allows up to 30 seconds for self-extinguishing and permits flaming drips. -
Can 94V 0 PCBs be used in high-temperature applications?
Yes, some 94V 0 PCBs are designed for high-temperature applications. Materials like polyimide and PTFE offer excellent heat resistance and can withstand temperatures up to 260°C or higher. However, it’s essential to choose the appropriate material and work closely with your PCB manufacturer to ensure the board meets your specific requirements. -
Are 94V 0 PCBs more expensive than non-rated PCBs?
Yes, 94V 0 PCBs are generally more expensive than non-rated PCBs due to the higher cost of flame-resistant materials and the additional testing required to ensure compliance with the UL 94V-0 standard. However, the added safety and reliability benefits often justify the increased cost, especially in applications where fire safety is a critical concern. -
Can 94V 0 PCBs be manufactured using lead-free processes?
Yes, 94V 0 PCBs can be manufactured using lead-free processes. Many PCB manufacturers offer lead-free options that comply with RoHS (Restriction of Hazardous Substances) regulations while still meeting the UL 94V-0 flammability rating. Lead-free processes typically involve using alternative solder alloys and surface finishes that do not contain lead. -
How can I ensure that my PCB design is compatible with 94V 0 materials?
To ensure your PCB design is compatible with 94V 0 materials, consider the following: - Choose a material that meets the UL 94V-0 rating and is suitable for your application’s requirements (e.g., temperature range, dielectric properties, and mechanical strength).
- Work closely with your PCB manufacturer to understand any design constraints imposed by the chosen material, such as minimum hole sizes or trace widths.
- Follow best practices for PCB design, including proper spacing between components, adequate copper weight, and appropriate solder mask and silkscreen specifications.
- Consider engaging a PCB design specialist or using design for manufacturing (DFM) services to review your design and ensure compatibility with 94V 0 materials and manufacturing processes.
Conclusion
94V 0 circuit boards are an essential component in many electronic devices, offering enhanced fire safety, regulatory compliance, and improved reliability. By using materials that meet the stringent UL 94V-0 flammability rating, these PCBs help reduce the risk of fire-related incidents and ensure the safety of users and property.
As technology continues to advance and new industries emerge, the demand for 94V 0 PCBs is expected to grow. Designers and manufacturers must stay informed about the latest materials, manufacturing processes, and regulatory requirements to ensure their products meet the highest safety and performance standards.
By understanding the importance of 94V 0 PCBs and the challenges and considerations involved in their design and manufacture, electronics professionals can make informed decisions and create safer, more reliable products for a wide range of applications.
0 Comments