What is an 8-Layer PCB?
An 8-layer PCB is a printed circuit board that consists of eight conductive layers laminated together with insulating material. These layers are strategically stacked and interconnected using vias, allowing for complex routing and improved signal integrity. The increased number of layers enables designers to create high-density layouts with enhanced functionality and performance.
Structure of an 8-Layer PCB
A typical 8-layer PCB structure consists of the following layers:
- Top Layer (Layer 1)
- Ground Plane (Layer 2)
- Signal Layer (Layer 3)
- Signal Layer (Layer 4)
- Power Plane (Layer 5)
- Signal Layer (Layer 6)
- Signal Layer (Layer 7)
- Bottom Layer (Layer 8)
The arrangement of these layers may vary depending on the specific design requirements and the manufacturer’s preferences.
Benefits of Using 8-Layer PCBs
Increased Density and Miniaturization
One of the primary advantages of using 8-layer PCBs is the ability to incorporate a higher density of components and traces within a smaller footprint. With the additional layers, designers can route signals more efficiently, reducing the overall size of the board. This miniaturization is particularly beneficial for applications where space is limited, such as smartphones, wearable devices, and aerospace systems.
Improved Signal Integrity
Signal integrity is a critical concern in high-speed and high-frequency applications. 8-layer PCBs offer improved signal integrity by providing dedicated layers for power and ground planes. These planes help to reduce electromagnetic interference (EMI) and crosstalk, ensuring cleaner and more stable signals. Additionally, the increased number of layers allows for better control over impedance matching and reduces signal reflections.
Enhanced Thermal Management
As electronic devices become more powerful, thermal management becomes a significant challenge. 8-layer PCBs can help alleviate this issue by incorporating dedicated layers for heat dissipation. These layers, often referred to as thermal planes, spread the heat generated by components evenly across the board, preventing hot spots and improving overall thermal performance.
Increased Reliability
The multi-layer structure of 8-layer PCBs contributes to their increased reliability. By distributing the power and ground planes throughout the board, the risk of voltage drops and ground loops is minimized. Furthermore, the use of blind and buried vias in 8-layer PCBs reduces the number of drill holes, enhancing the board’s mechanical strength and durability.
Applications of 8-Layer PCBs
8-layer PCBs find applications in various industries and products that require high-density layouts, improved signal integrity, and enhanced performance. Some common applications include:
- Telecommunications equipment
- Networking devices
- High-performance computing systems
- Medical devices
- Aerospace and defense systems
- Automotive electronics
- Industrial control systems
- Consumer electronics
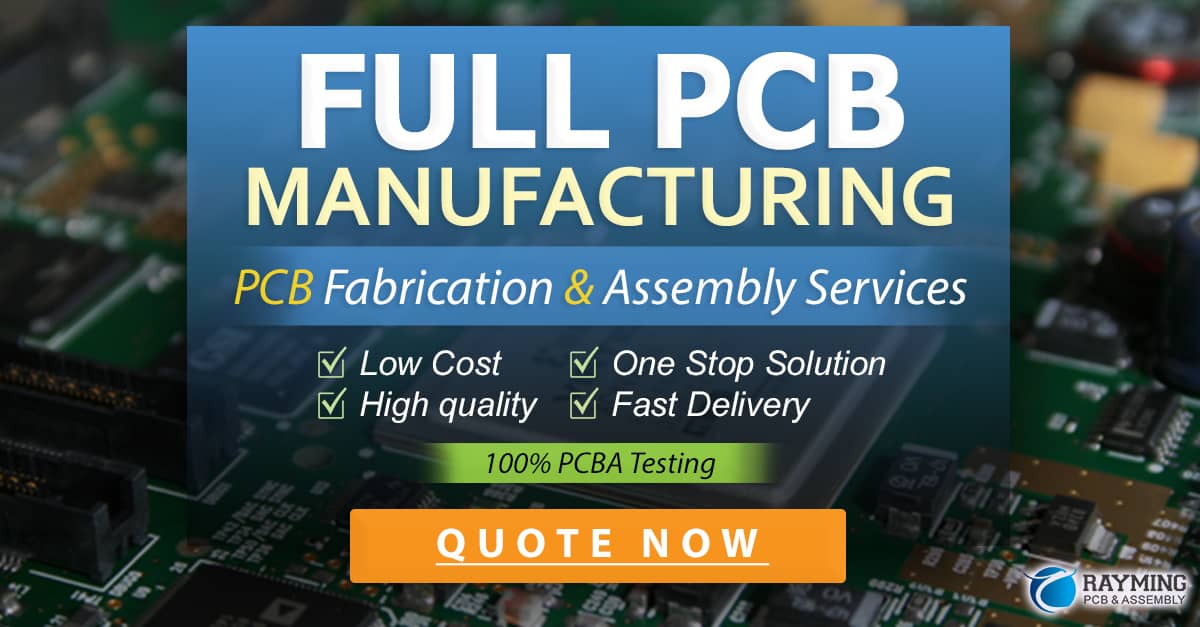
Designing 8-Layer PCBs
Designing an 8-layer PCB requires careful consideration of various factors to ensure optimal performance and manufacturability. Here are some key aspects to keep in mind:
Layer Stackup
The layer stackup refers to the arrangement of conductive and insulating layers in the PCB. When designing an 8-layer PCB, it is essential to determine the appropriate layer stackup based on the signal requirements, power distribution, and EMI considerations. Consult with your PCB manufacturer to determine the best layer stackup for your specific application.
Signal Integrity
To maintain signal integrity in an 8-layer PCB, designers must consider factors such as trace width, spacing, and impedance control. It is crucial to follow the manufacturer’s design guidelines and use simulation tools to analyze and optimize signal paths. Proper grounding and shielding techniques should also be employed to minimize crosstalk and EMI.
Power Distribution
Efficient power distribution is critical in 8-layer PCBs to ensure stable and reliable operation. Designers should strategically place power and ground planes to minimize voltage drops and provide a low-impedance return path for signals. The use of Decoupling capacitors and proper power plane segmentation can help mitigate noise and improve power integrity.
Thermal Management
Thermal management is an important consideration in 8-layer PCB design. Designers should identify high-power components and place them strategically to minimize thermal interactions. The use of thermal vias and dedicated thermal planes can help dissipate heat effectively. Thermal simulation tools can be used to analyze and optimize the thermal performance of the board.
Design for Manufacturability (DFM)
Designing an 8-layer PCB with manufacturability in mind is crucial to ensure a smooth and cost-effective production process. Designers should adhere to the manufacturer’s design rules, such as minimum trace width, spacing, and hole sizes. It is also important to consider the capabilities and limitations of the chosen manufacturing process, such as via formation and layer registration tolerances.
Choosing the Right 8-Layer PCB Manufacturer
Selecting the right 8-layer PCB manufacturer is crucial to ensure the quality, reliability, and timely delivery of your boards. Here are some factors to consider when choosing a manufacturer:
Experience and Expertise
Look for a manufacturer with a proven track record in producing 8-layer PCBs. They should have experience in handling complex designs and be familiar with the latest manufacturing technologies and processes. Ask for references and review their portfolio to assess their expertise.
Manufacturing Capabilities
Ensure that the manufacturer has the necessary equipment and capabilities to produce 8-layer PCBs. This includes advanced lamination processes, high-precision drilling and plating, and automated optical inspection (AOI) systems. Inquire about their minimum feature sizes, layer registration accuracy, and quality control measures.
Certifications and Standards
Choose a manufacturer that adheres to industry standards and holds relevant certifications, such as ISO 9001, IATF 16949, and UL. These certifications demonstrate their commitment to quality and reliability. Additionally, ensure that the manufacturer complies with environmental regulations, such as RoHS and REACH.
Lead Time and Pricing
Consider the manufacturer’s lead time and pricing structure. While cost is an important factor, it should not be the sole determining factor. Ensure that the manufacturer can deliver high-quality boards within your required timeframe. Request quotes from multiple manufacturers and compare their pricing, lead times, and value-added services.
Customer Support and Communication
Effective communication and responsive customer support are essential when working with an 8-layer PCB manufacturer. Look for a manufacturer that provides clear and timely communication, technical support, and design assistance. They should be willing to collaborate with you throughout the project and address any concerns or issues promptly.
Frequently Asked Questions (FAQs)
-
What is the typical turnaround time for 8-layer PCB manufacturing?
The turnaround time for 8-layer PCB manufacturing varies depending on the complexity of the design, the manufacturer’s workload, and the chosen manufacturing process. Typically, it can range from 7 to 14 days, but expedited services may be available for faster delivery. -
How much does an 8-layer PCB cost compared to a 4-layer PCB?
The cost of an 8-layer PCB is generally higher than that of a 4-layer PCB due to the increased complexity and material requirements. The exact cost difference depends on factors such as board size, quantity, and the manufacturer’s pricing structure. On average, an 8-layer PCB can cost 1.5 to 2 times more than a 4-layer PCB. -
Can 8-layer PCBs be manufactured with blind and buried vias?
Yes, 8-layer PCBs can be manufactured with blind and buried vias. Blind vias connect an outer layer to an inner layer, while buried vias connect two or more inner layers without reaching the outer layers. These types of vias offer increased routing flexibility and help reduce the overall board size. -
What are the common challenges faced during 8-layer PCB manufacturing?
Some common challenges in 8-layer PCB manufacturing include maintaining precise layer registration, ensuring proper via formation, and managing signal integrity. The increased number of layers also requires careful lamination and pressing processes to prevent delamination and warpage. Manufacturers must have robust quality control measures in place to mitigate these challenges. -
How can I ensure the reliability and longevity of my 8-layer PCBs?
To ensure the reliability and longevity of your 8-layer PCBs, follow best design practices, such as proper signal routing, power distribution, and thermal management. Choose a reputable manufacturer with a proven track record of producing high-quality boards. Additionally, consider incorporating features like conformal coating, underfill, and strain relief to enhance the board’s durability and protection against environmental factors.
Conclusion
8-layer PCBs offer numerous benefits, including increased density, improved signal integrity, enhanced thermal management, and increased reliability. They find applications in various industries where high-performance and complex designs are required. When designing 8-layer PCBs, careful consideration must be given to layer stackup, signal integrity, power distribution, thermal management, and manufacturability.
Choosing the right 8-layer PCB manufacturer is crucial to ensure the success of your project. Look for a manufacturer with experience, expertise, and the necessary manufacturing capabilities. Consider factors such as certifications, lead time, pricing, and customer support when making your decision.
By understanding the intricacies of 8-layer PCB manufacturing and partnering with a reliable manufacturer, you can unlock the full potential of your electronic designs and bring your innovative ideas to life.
0 Comments