What is PCB Conformal Coating?
PCB conformal coating is a thin, protective layer applied to the surface of a PCB, conforming to its contours and components. The coating is typically a polymeric material that is applied through various methods, such as spraying, dipping, or brushing. The primary purpose of conformal coating is to protect the PCB from environmental factors that can cause damage or deterioration over time.
Types of Conformal Coatings
There are several types of conformal coatings available, each with its own unique properties and advantages. The most common types include:
- Acrylic
- Silicone
- Polyurethane
- Epoxy
- Parylene
The choice of conformal coating depends on the specific requirements of the PCB, such as the operating environment, temperature range, and required level of protection.
Why is PCB Conformal Coating Thickness Important?
The thickness of the conformal coating is a critical factor in determining its effectiveness in protecting the PCB. A coating that is too thin may not provide adequate protection against environmental hazards, while a coating that is too thick can lead to other issues, such as increased weight, reduced flexibility, and altered electrical properties.
The ideal thickness of a conformal coating depends on several factors, which we will discuss in detail in the following sections.
Factor 1: Environmental Conditions
The environmental conditions in which the PCB will operate play a significant role in determining the ideal conformal coating thickness. Harsh environments, such as those with high humidity, corrosive chemicals, or extreme temperatures, may require a thicker coating to provide adequate protection.
Environment | Recommended Thickness |
---|---|
Mild | 25-50 µm |
Moderate | 50-75 µm |
Harsh | 75-100 µm |
It is essential to assess the specific environmental conditions the PCB will be exposed to and select a coating thickness that provides sufficient protection without compromising other aspects of the PCB’s performance.
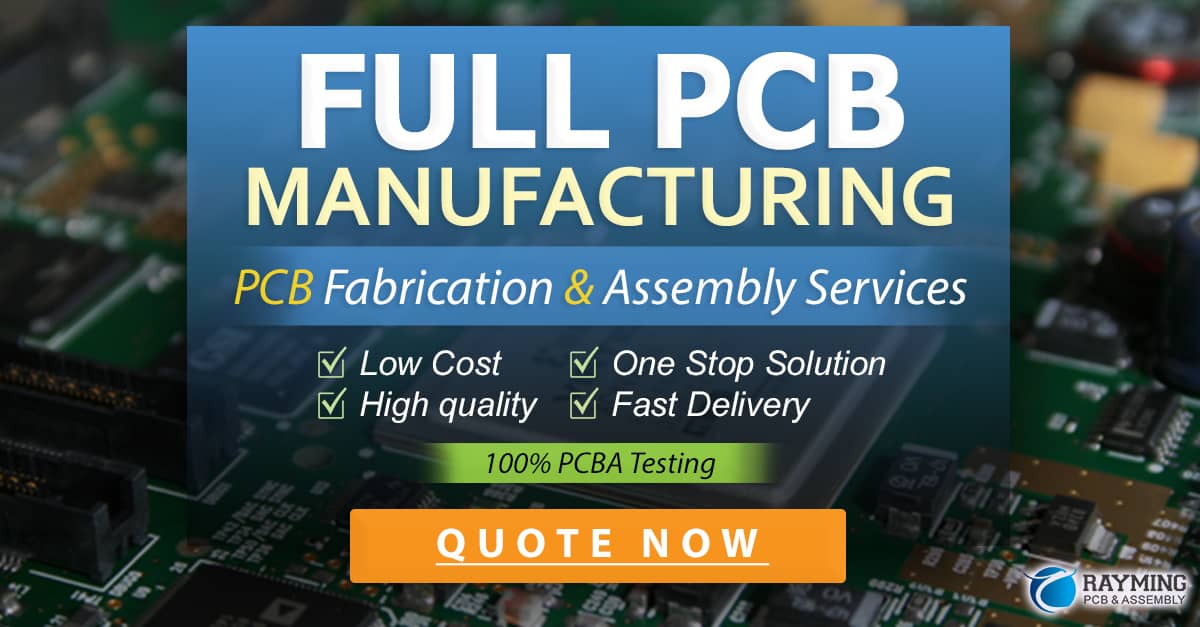
Factor 2: Coating Material Properties
The properties of the chosen conformal coating material also influence the ideal thickness. Different coating materials have varying levels of viscosity, cure time, and surface tension, which can affect the achievable thickness and uniformity of the coating.
For example, acrylic coatings typically have a lower viscosity and can be applied in thinner layers compared to epoxy coatings, which have a higher viscosity and may require thicker layers to achieve the desired level of protection.
Coating Material | Typical Thickness Range |
---|---|
Acrylic | 25-75 µm |
Silicone | 50-200 µm |
Polyurethane | 25-250 µm |
Epoxy | 25-100 µm |
Parylene | 0.1-50 µm |
It is crucial to consult the manufacturer’s guidelines and technical data sheets when selecting the appropriate coating material and thickness for a specific application.
Factor 3: Application Method
The method used to apply the conformal coating can also affect the achievable thickness and uniformity of the coating. The three most common application methods are:
- Spraying
- Dipping
- Brushing
Spraying
Spraying is a popular method for applying conformal coatings, as it allows for precise control over the coating thickness and can be automated for high-volume production. The thickness of the coating can be adjusted by varying the spray parameters, such as the nozzle size, air pressure, and distance from the PCB.
Dipping
Dipping involves immersing the PCB in a tank of liquid conformal coating material. This method is suitable for coating complex geometries and large quantities of PCBs. The thickness of the coating can be controlled by adjusting the immersion time and the viscosity of the coating material.
Brushing
Brushing is a manual application method that is suitable for small-scale production or touch-up work. The thickness of the coating depends on the skill of the operator and the viscosity of the coating material.
Application Method | Typical Thickness Range |
---|---|
Spraying | 25-250 µm |
Dipping | 25-100 µm |
Brushing | 25-100 µm |
The choice of application method depends on factors such as the PCB geometry, required coating thickness, and production volume.
Factor 4: PCB Geometry and Component Placement
The geometry of the PCB and the placement of its components can affect the ideal conformal coating thickness. PCBs with closely spaced components or intricate geometries may require a thinner coating to ensure proper coverage without bridging between components.
On the other hand, PCBs with larger components or greater spacing between components may allow for a thicker coating to provide enhanced protection.
It is essential to consider the specific geometry and component placement of the PCB when determining the appropriate coating thickness to ensure adequate protection without compromising the functionality of the PCB.
Factor 5: Curing Process
The curing process is an essential step in the application of conformal coatings, as it allows the coating to achieve its final properties and form a stable protective layer. The curing process can affect the final thickness of the coating, as well as its adhesion, hardness, and other physical properties.
Different coating materials have varying curing requirements, such as temperature, humidity, and curing time. For example, some coatings may require elevated temperatures to cure, while others may cure at room temperature.
Coating Material | Typical Curing Conditions |
---|---|
Acrylic | Room temperature, 24-48 hours |
Silicone | Room temperature, 24-72 hours |
Polyurethane | Room temperature, 24-48 hours |
Epoxy | Elevated temperature, 1-2 hours |
Parylene | Vacuum deposition, no curing required |
It is crucial to follow the manufacturer’s guidelines for curing the selected conformal coating to ensure optimal performance and protection.
Factor 6: Electrical Properties
The electrical properties of the PCB, such as its impedance and capacitance, can be affected by the thickness of the conformal coating. A thicker coating may increase the capacitance between traces and components, which can alter the electrical performance of the PCB.
In high-frequency applications, such as radio frequency (RF) or microwave circuits, the thickness of the conformal coating must be carefully controlled to minimize its impact on the electrical properties of the PCB.
It is essential to consider the electrical requirements of the PCB when selecting the appropriate coating thickness and material to ensure optimal performance.
Factor 7: Cost and Production Efficiency
The cost and production efficiency of applying conformal coatings are also important factors to consider when determining the ideal coating thickness. Thicker coatings may require more material and longer processing times, which can increase production costs.
On the other hand, thinner coatings may be more cost-effective but may not provide the desired level of protection for the PCB.
It is essential to strike a balance between the required level of protection and the cost and production efficiency of applying the conformal coating. This can be achieved by optimizing the coating thickness based on the specific requirements of the PCB and the production process.
FAQ
Q1: How do I choose the right conformal coating material for my PCB?
A1: The choice of conformal coating material depends on factors such as the operating environment, required level of protection, and compatibility with the PCB materials and components. Consult the manufacturer’s guidelines and technical data sheets to select the most suitable coating material for your specific application.
Q2: Can I apply multiple layers of conformal coating to increase the thickness?
A2: Yes, it is possible to apply multiple layers of conformal coating to achieve the desired thickness. However, it is essential to allow sufficient curing time between layers and to ensure that the total thickness does not exceed the recommended range for the selected coating material.
Q3: How can I measure the thickness of the applied conformal coating?
A3: There are several methods for measuring the thickness of conformal coatings, including:
1. Wet film thickness gauges
2. Dry film thickness gauges
3. Optical microscopy
4. Cross-sectional analysis
The choice of measurement method depends on factors such as the coating material, the stage of the coating process, and the required level of accuracy.
Q4: Can I rework a PCB with conformal coating?
A4: Yes, it is possible to rework a PCB with conformal coating, but it requires special techniques and tools to remove the coating without damaging the PCB or its components. Common methods for removing conformal coatings include:
1. Mechanical abrasion
2. Chemical solvents
3. Thermal removal
It is essential to follow the manufacturer’s guidelines and industry best practices when reworking a PCB with conformal coating to ensure the integrity of the PCB and its components.
Q5: How often should I inspect the conformal coating on my PCBs?
A5: The frequency of inspecting the conformal coating on your PCBs depends on factors such as the operating environment, the criticality of the application, and the expected service life of the PCB. In general, it is recommended to inspect the conformal coating:
1. After initial application and curing
2. Periodically during the service life of the PCB
3. After exposure to extreme environmental conditions
4. Before and after any rework or repair operations
Regular inspections can help identify any defects or degradation in the conformal coating and allow for timely maintenance or repair to ensure the continued protection of the PCB.
Conclusion
The ideal thickness of PCB conformal coating is a critical factor in ensuring the optimal protection and performance of the PCB. The seven important factors that influence the ideal coating thickness are:
- Environmental conditions
- Coating material properties
- Application method
- PCB geometry and component placement
- Curing process
- Electrical properties
- Cost and production efficiency
By carefully considering these factors and selecting the appropriate coating material, thickness, and application method, you can ensure that your PCBs are adequately protected against environmental hazards while maintaining optimal performance and cost-effectiveness.
0 Comments