Incorrect Component Placement
One of the most common mistakes in PCB Assembly is incorrect component placement. This can happen due to human error, incorrect markings on the PCB, or using the wrong component altogether. Incorrect component placement can lead to short circuits, open circuits, and other issues that can cause PCB failure.
To avoid this mistake, it is essential to follow the PCB layout carefully and double-check each component before placing it on the board. Using automated pick-and-place machines can also help reduce the risk of human error.
Common examples of incorrect component placement:
Component | Correct Placement | Incorrect Placement |
---|---|---|
Resistor | Aligned with pads | Skewed or misaligned |
Capacitor | Polarity matches markings | Reversed polarity |
IC | Notch aligned with marking | Rotated or flipped |
Overheating Components
Another common mistake in PCB assembly is overheating components during the soldering process. Overheating can damage the components, causing them to fail prematurely or not function at all. This can happen due to using a soldering iron with too high a temperature, applying heat for too long, or using the wrong type of solder.
To avoid overheating components, it is important to use a soldering iron with adjustable temperature control and to follow the recommended temperature settings for each component. Using the correct type of solder and applying heat for the appropriate amount of time can also help prevent overheating.
Recommended soldering temperatures for common components:
Component | Temperature Range |
---|---|
Resistor | 300-350°C |
Capacitor | 250-300°C |
IC | 300-350°C |
Using the Wrong Solder
Using the wrong type of solder can also lead to PCB failure. Different types of solder have different melting points, flux content, and alloy composition, which can affect the quality and reliability of the solder joint. Using the wrong type of solder can result in weak or brittle joints that can crack or break over time.
To avoid this mistake, it is important to choose the right type of solder for the specific application and to follow the manufacturer’s recommendations. Lead-free solder is becoming increasingly popular due to environmental concerns, but it requires higher soldering temperatures and may not be suitable for all components.
Common types of solder and their characteristics:
Solder Type | Melting Point | Flux Content | Alloy Composition |
---|---|---|---|
Lead-based | 183°C | Rosin | 63% Sn, 37% Pb |
Lead-free | 217°C | Rosin | 96.5% Sn, 3% Ag, 0.5% Cu |
High-temp | 280°C | Rosin | 95% Sn, 5% Sb |
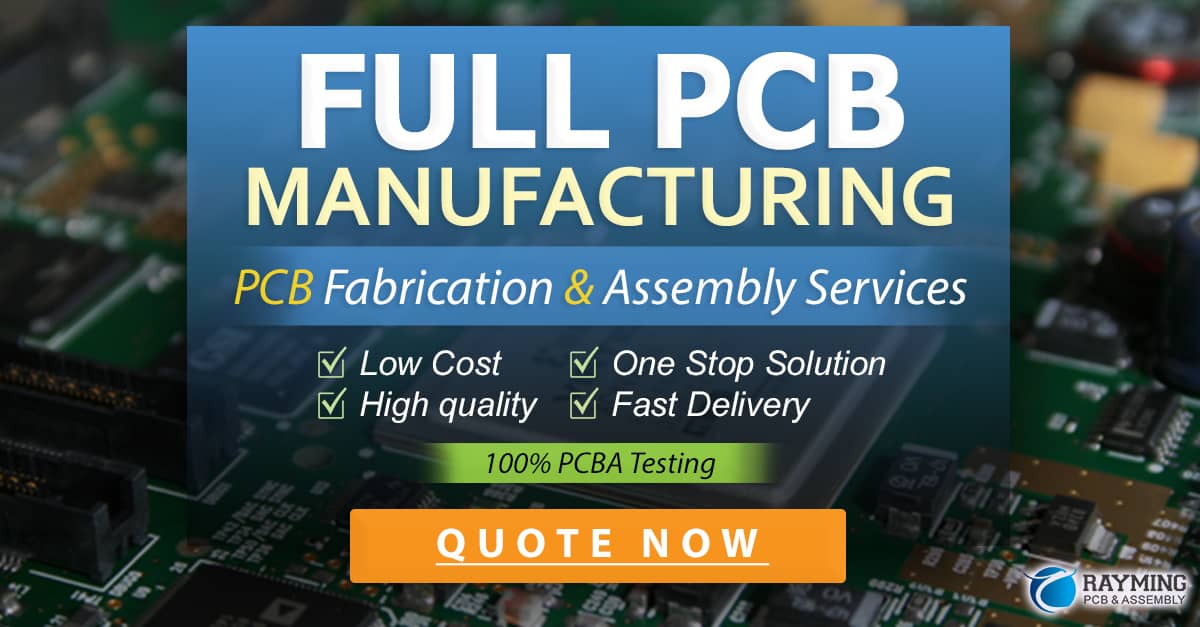
Insufficient Cleaning
Insufficient cleaning of the PCB after the soldering process can also lead to PCB failure. Flux residue, solder splashes, and other contaminants can cause corrosion, short circuits, and other issues that can affect the reliability and longevity of the PCB.
To avoid this mistake, it is important to clean the PCB thoroughly after the soldering process using the appropriate cleaning agents and methods. Isopropyl alcohol is a common cleaning agent, but other solvents may be necessary for more stubborn contaminants.
Recommended cleaning methods for PCBs:
Contaminant | Cleaning Method |
---|---|
Flux residue | Isopropyl alcohol |
Solder splashes | Solder wick or desoldering tool |
Grease or oil | Degreaser or ultrasonic cleaning |
Improper Handling and Storage
Improper handling and storage of PCBs can also lead to PCB failure. PCBs are sensitive to static electricity, moisture, and other environmental factors that can damage the components or the board itself. Mishandling PCBs during the assembly process or storing them in unsuitable conditions can result in warping, cracking, or other physical damage.
To avoid this mistake, it is important to handle PCBs with care, using appropriate static-dissipative equipment and techniques. PCBs should be stored in a dry, temperature-controlled environment, away from direct sunlight and other sources of heat or moisture.
Best practices for handling and storing PCBs:
- Use static-dissipative gloves, mats, and wrist straps when handling PCBs
- Store PCBs in anti-static bags or containers
- Keep PCBs away from sources of heat, moisture, and direct sunlight
- Handle PCBs by the edges to avoid touching the components or solder joints
- Use appropriate packaging materials when shipping or transporting PCBs
FAQ
-
What are the most common causes of PCB failure?
The most common causes of PCB failure include incorrect component placement, overheating components, using the wrong solder, insufficient cleaning, and improper handling and storage. -
How can I avoid incorrect component placement during PCB assembly?
To avoid incorrect component placement, follow the PCB layout carefully, double-check each component before placing it on the board, and consider using automated pick-and-place machines to reduce the risk of human error. -
What should I do if I accidentally overheat a component during soldering?
If you accidentally overheat a component during soldering, remove the heat source immediately and allow the component to cool down. If the component is damaged, it may need to be replaced. -
Can I use any type of solder for PCB assembly?
No, different types of solder have different characteristics that can affect the quality and reliability of the solder joint. Choose the right type of solder for the specific application and follow the manufacturer’s recommendations. -
How can I prevent damage to PCBs during handling and storage?
To prevent damage to PCBs during handling and storage, use appropriate static-dissipative equipment and techniques, store PCBs in a dry, temperature-controlled environment, and handle them by the edges to avoid touching the components or solder joints.
By avoiding these common mistakes and following best practices for PCB assembly, you can ensure the reliability, longevity, and performance of your PCBs. Whether you are a hobbyist or a professional, taking the time to do things right can save you time, money, and frustration in the long run.
0 Comments