What is a 4 Layer PCB?
A 4 layer PCB, or printed circuit board, is a type of circuit board that consists of four conductive copper layers laminated together with insulating material. These layers are typically labeled as follows:
- Top Layer (Layer 1)
- Ground Plane (Layer 2)
- Power Plane (Layer 3)
- Bottom Layer (Layer 4)
The top and bottom layers are used for placing components and routing signals, while the inner layers (ground and power planes) provide a stable reference for the signals and help reduce electromagnetic interference (EMI).
Advantages of 4 Layer PCBs
Improved Signal Integrity
One of the main advantages of using a 4 layer PCB is improved signal integrity. By dedicating entire layers to ground and power planes, the PCB can provide a low-impedance path for return currents, minimizing the loop area and reducing EMI. This is especially important for high-speed designs and sensitive analog circuits.
Reduced Crosstalk
Another benefit of 4 layer PCBs is reduced crosstalk between signals. The ground and power planes act as shields between the top and bottom layers, reducing the coupling between adjacent traces. This helps maintain signal integrity and prevents unwanted interference.
Better Power Distribution
The dedicated power plane in a 4 layer PCB provides a low-impedance path for distributing power to components. This helps reduce voltage drops and ensures that all components receive a stable and clean power supply. The power plane also acts as a large Decoupling capacitor, helping to reduce power supply noise.
Increased Routing Density
With four layers available for routing, designers have more flexibility to route complex designs with high component density. The additional layers allow for more efficient use of board space, enabling smaller form factors and reduced manufacturing costs.
Designing 4 Layer PCBs
Layer Stackup
When designing a 4 layer PCB, it’s essential to consider the layer stackup carefully. A typical stackup might look like this:
Layer | Material | Thickness (mm) |
---|---|---|
Top | Copper | 0.035 |
Dielectric | FR-4 | 0.2 |
Ground | Copper | 0.035 |
Dielectric | FR-4 | 0.7 |
Power | Copper | 0.035 |
Dielectric | FR-4 | 0.2 |
Bottom | Copper | 0.035 |
The thickness of the dielectric layers can be adjusted based on the desired impedance of the traces and the required board thickness.
Trace Width and Spacing
When routing traces on a 4 layer PCB, it’s important to consider the trace width and spacing to ensure signal integrity and manufacturability. The trace width should be chosen based on the required current carrying capacity and the desired impedance. Wider traces have lower impedance and can carry more current, but they also take up more space.
Trace spacing should be sufficient to prevent unwanted coupling between adjacent traces. The spacing requirements depend on factors such as the signal rise time, dielectric constant of the PCB material, and the maximum allowable crosstalk.
Via Design
Vias are used to connect traces between layers in a 4 layer PCB. When designing vias, it’s important to consider the via size, drill size, and pad size. Smaller vias allow for higher routing density but are more expensive to manufacture. Larger vias are easier to manufacture but take up more space.
It’s also important to consider the placement of vias to minimize the impact on signal integrity. Vias should be placed as close as possible to the components they connect to reduce the loop area and minimize inductance.
Ground and Power Planes
The ground and power planes in a 4 layer PCB should be designed to provide a low-impedance path for return currents and power distribution. The planes should be as continuous as possible, with minimal splits or cuts. If cuts are necessary, they should be kept as small as possible and placed away from sensitive signals.
It’s also important to consider the placement of decoupling capacitors on the power plane. Decoupling capacitors should be placed as close as possible to the components they are decoupling to minimize the loop area and provide effective noise reduction.
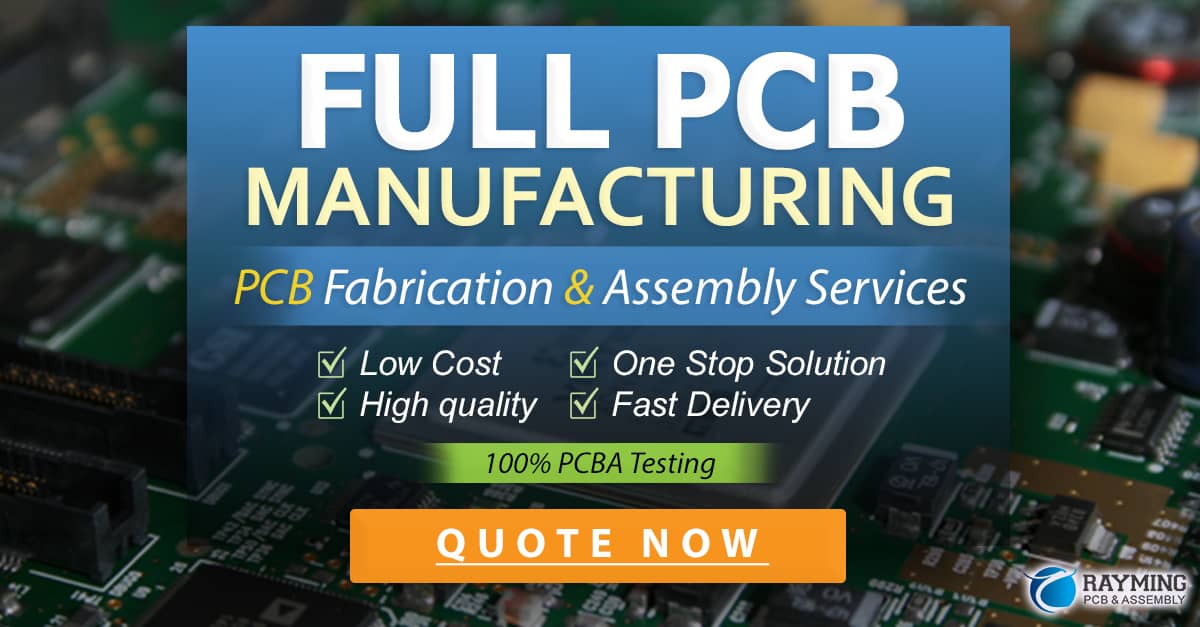
Manufacturing 4 Layer PCBs
Material Selection
When manufacturing 4 layer PCBs, the choice of material is critical. The most common material used for 4 layer PCBs is FR-4, a glass-reinforced epoxy laminate. FR-4 has good mechanical and electrical properties and is relatively inexpensive.
For high-speed designs or designs with strict impedance requirements, other materials such as Rogers or Isola may be used. These materials have lower dielectric constants and lower loss tangents, which can help reduce signal attenuation and improve signal integrity.
Lamination Process
The lamination process is critical to ensuring the quality and reliability of a 4 layer PCB. During lamination, the four layers are pressed together under high temperature and pressure to form a single board. The temperature and pressure must be carefully controlled to ensure proper bonding between the layers and to prevent defects such as delamination or warping.
Drilling and Plating
After lamination, the PCB is drilled to create holes for vias and component leads. The holes are then plated with copper to provide electrical connectivity between layers. The plating process must be carefully controlled to ensure uniform coverage and to prevent defects such as voids or thin spots.
Solder Mask and Silkscreen
The final steps in manufacturing a 4 layer PCB are applying solder mask and silkscreen. Solder mask is a protective coating that covers the copper traces and prevents accidental short circuits during assembly. Silkscreen is used to add text and graphics to the PCB for identification and assembly purposes.
Frequently Asked Questions
Q1: When should I use a 4 layer PCB instead of a 2 layer PCB?
A1: 4 layer PCBs are typically used for designs with high component density, high-speed signals, or strict impedance requirements. If your design has a lot of components, requires controlled impedance, or has signals with fast rise times, a 4 layer PCB may be necessary to ensure signal integrity and manufacturability.
Q2: How much more expensive is a 4 layer PCB compared to a 2 layer PCB?
A2: The cost of a 4 layer PCB is typically 2-3 times higher than a 2 layer PCB of the same size and quantity. The additional cost is due to the extra materials and processing steps required to manufacture a 4 layer board. However, the improved performance and reliability of a 4 layer PCB can often justify the added cost.
Q3: Can I mix signal and power traces on the same layer in a 4 layer PCB?
A3: It’s generally not recommended to mix signal and power traces on the same layer in a 4 layer PCB. The power traces can introduce noise and crosstalk into the signal traces, which can degrade signal integrity. It’s best to route power traces on the dedicated power plane and signal traces on the top and bottom layers.
Q4: How do I choose the right trace width and spacing for my 4 layer PCB design?
A4: The trace width and spacing should be chosen based on factors such as the required current carrying capacity, desired impedance, and maximum allowable crosstalk. There are many online calculators and tools available to help designers determine the appropriate trace width and spacing for their specific design requirements.
Q5: What are some common pitfalls to avoid when designing a 4 layer PCB?
A5: Some common pitfalls to avoid when designing a 4 layer PCB include:
- Failing to consider the layer stackup and material properties
- Not providing enough clearance between traces and vias
- Mixing signal and power traces on the same layer
- Not properly designing the ground and power planes
- Failing to consider the impact of vias on signal integrity
- Not properly specifying the required impedance and tolerances
By carefully considering these factors and following best practices for PCB design, designers can ensure the success of their 4 layer PCB projects.
Conclusion
Designing and manufacturing 4 layer PCBs requires careful consideration of many factors, from the layer stackup and material properties to the trace width and spacing and via design. By understanding the advantages and challenges of 4 layer PCBs and following best practices for design and manufacturing, designers can create high-quality, reliable circuit boards for even the most demanding applications. Whether you’re designing a complex high-speed digital system or a sensitive analog circuit, a well-designed 4 layer PCB can provide the performance and reliability you need for success.
0 Comments